If you use a bike and sit on your saddle then you will know as a rider how important it is to have the right saddle and how it is fundamental to your ride. Saddle production is concentrated in a few places in the world. One of those production centres is Velo enterprises in Taichung, Taiwan. We visited the factory to discover the latest production methods and how saddles are made.
The Factory
The Saddle Factory is located on the coast near Taichung, in the middle of a town, with more than 1500 people working at the factory of which half of the people live in dormitories nearby.
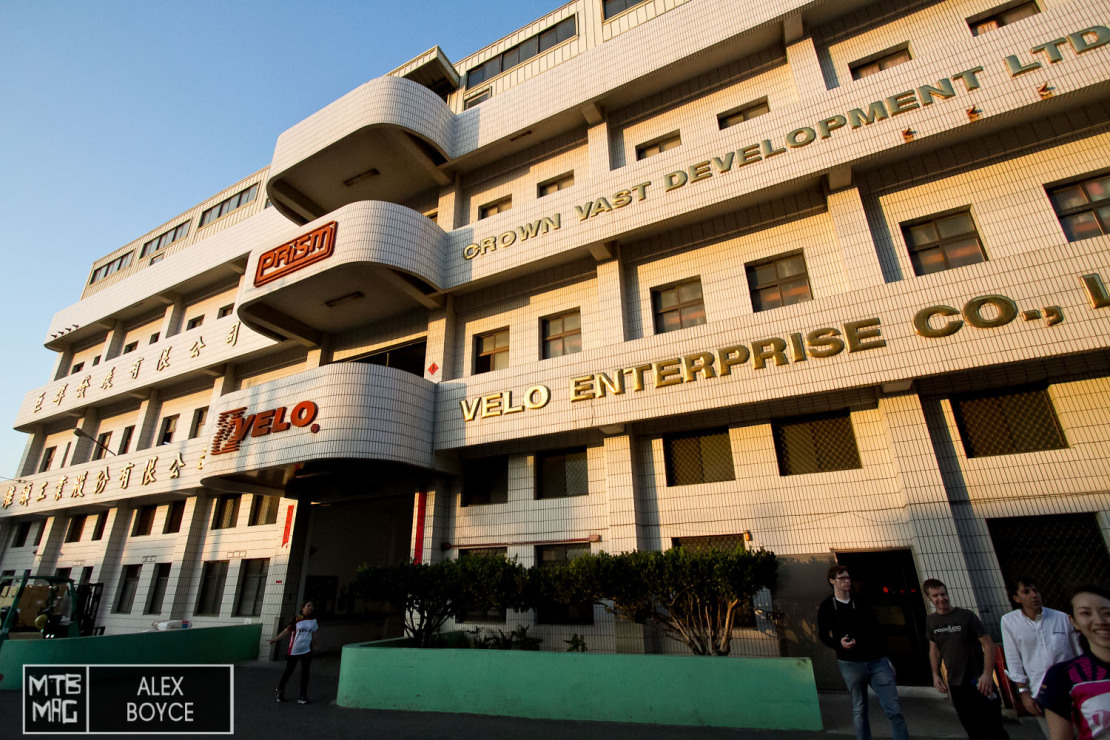
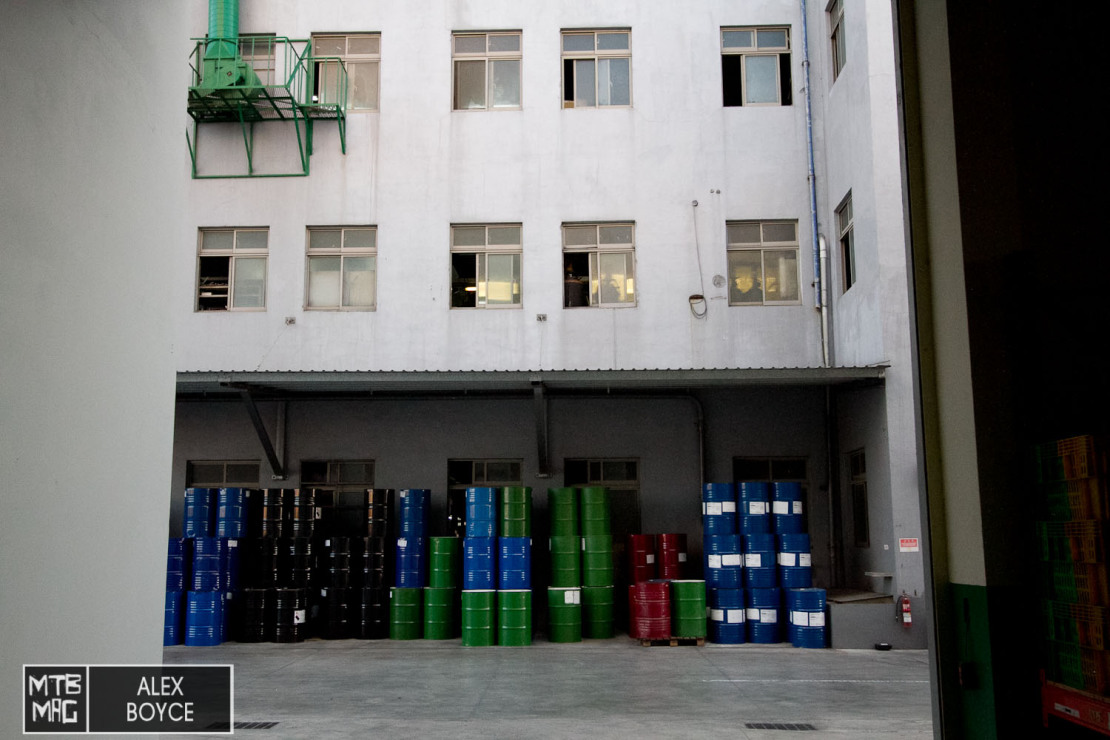
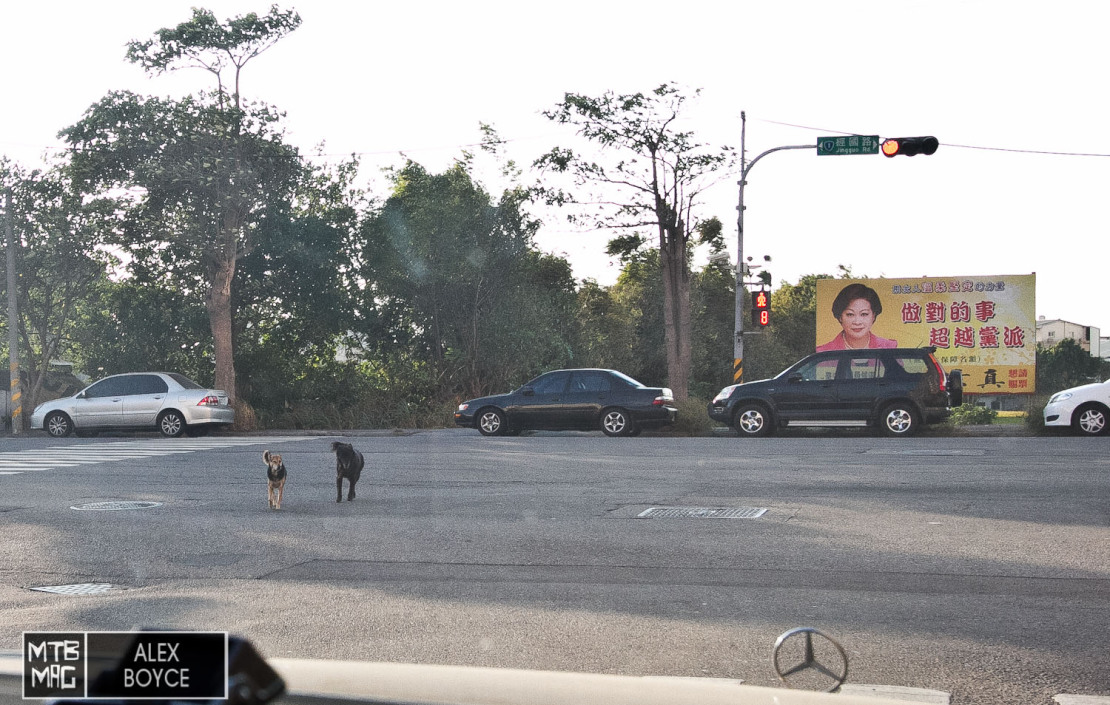
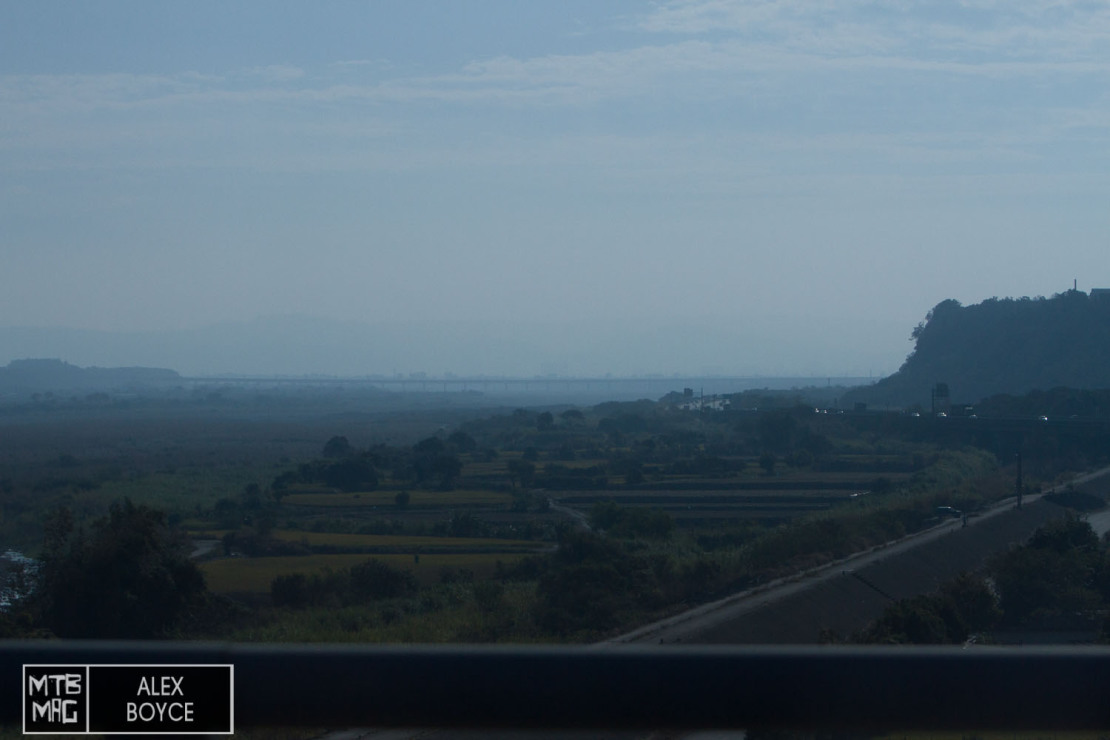
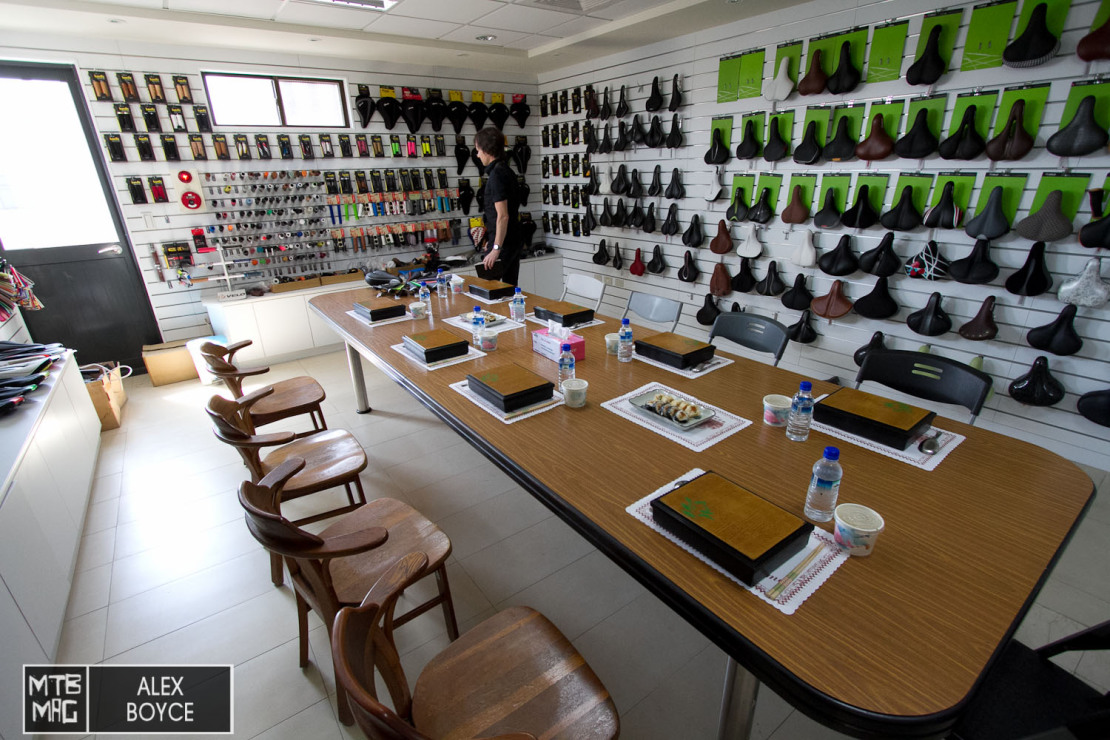
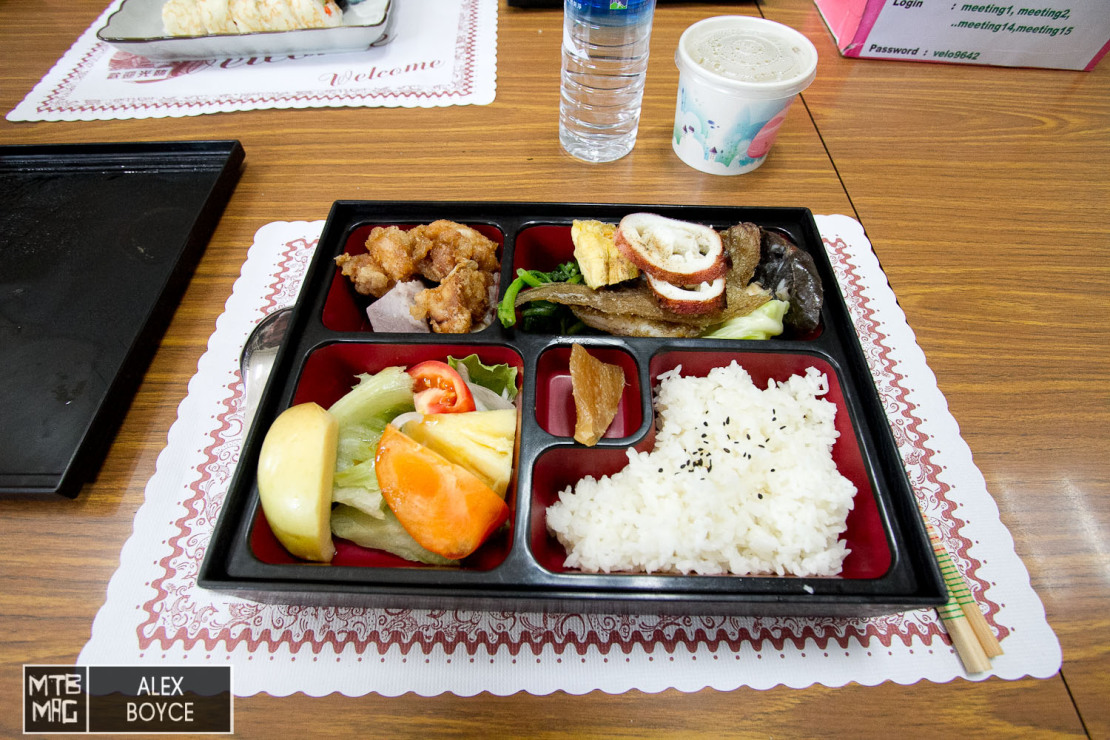
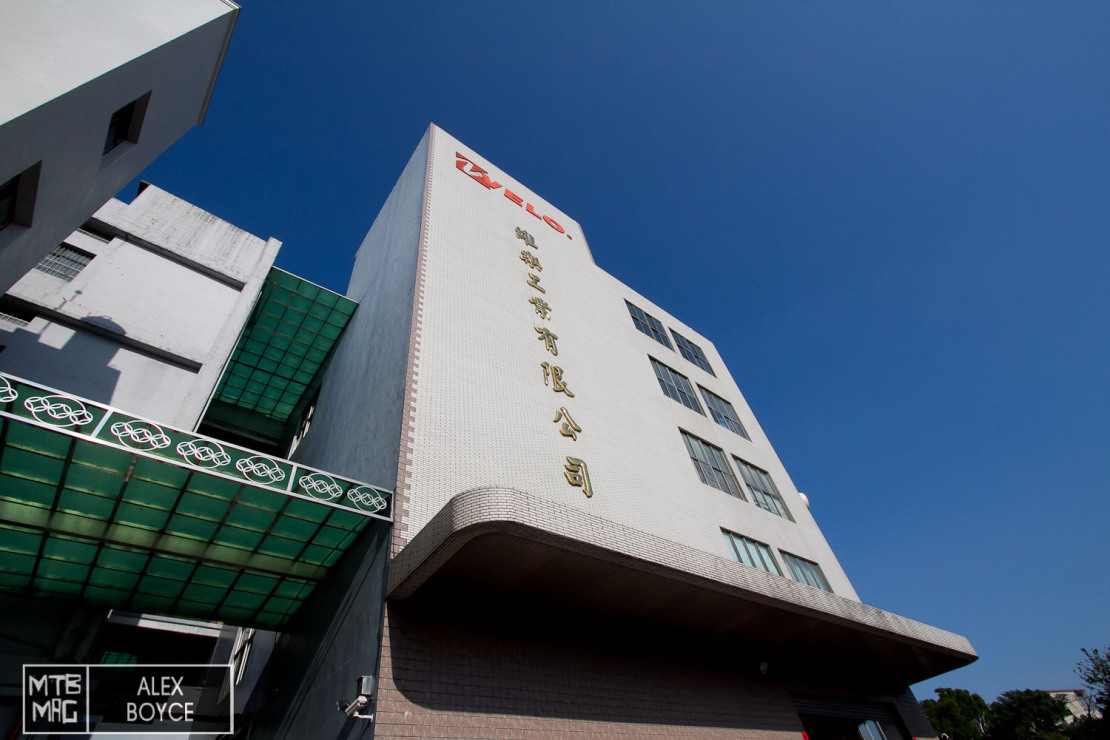
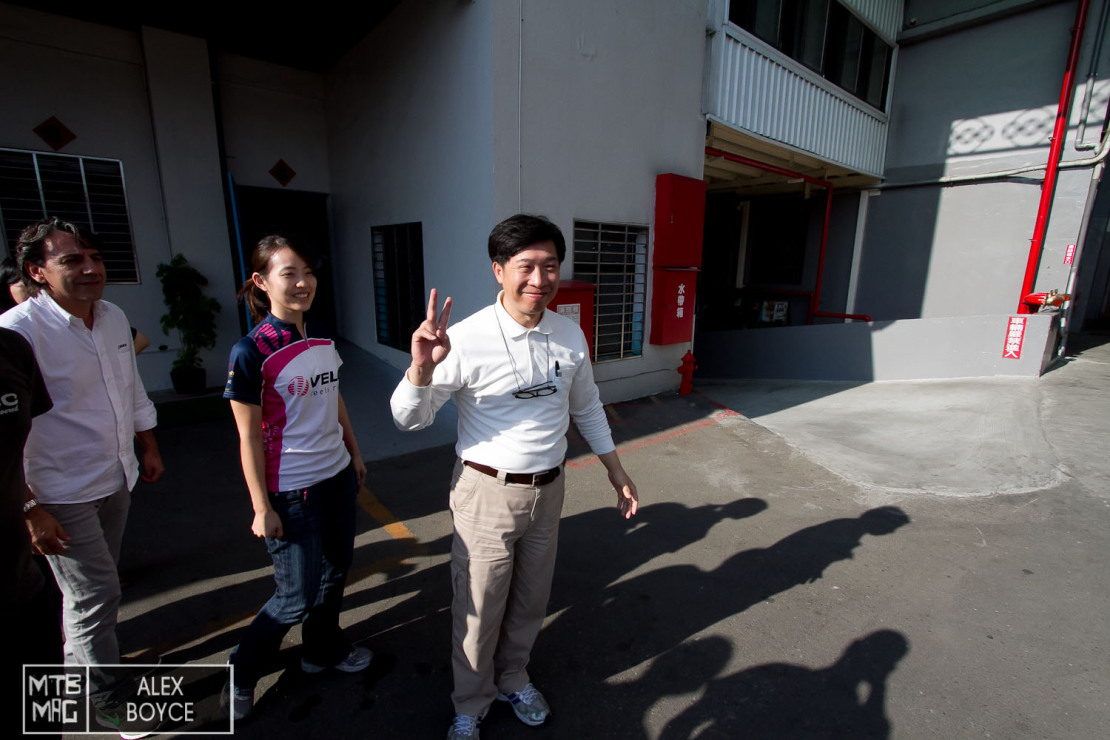
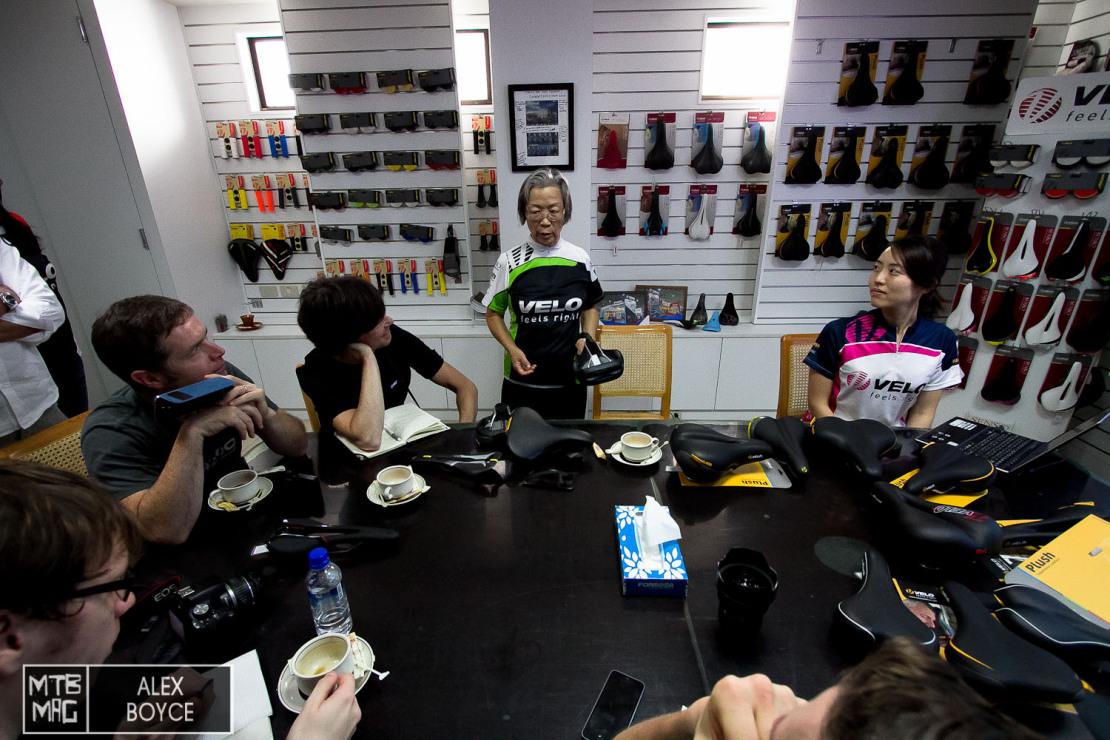
Production Line
We visited the production line facility for the saddles and saw how the materials and components were used and created and put together to become the final products.
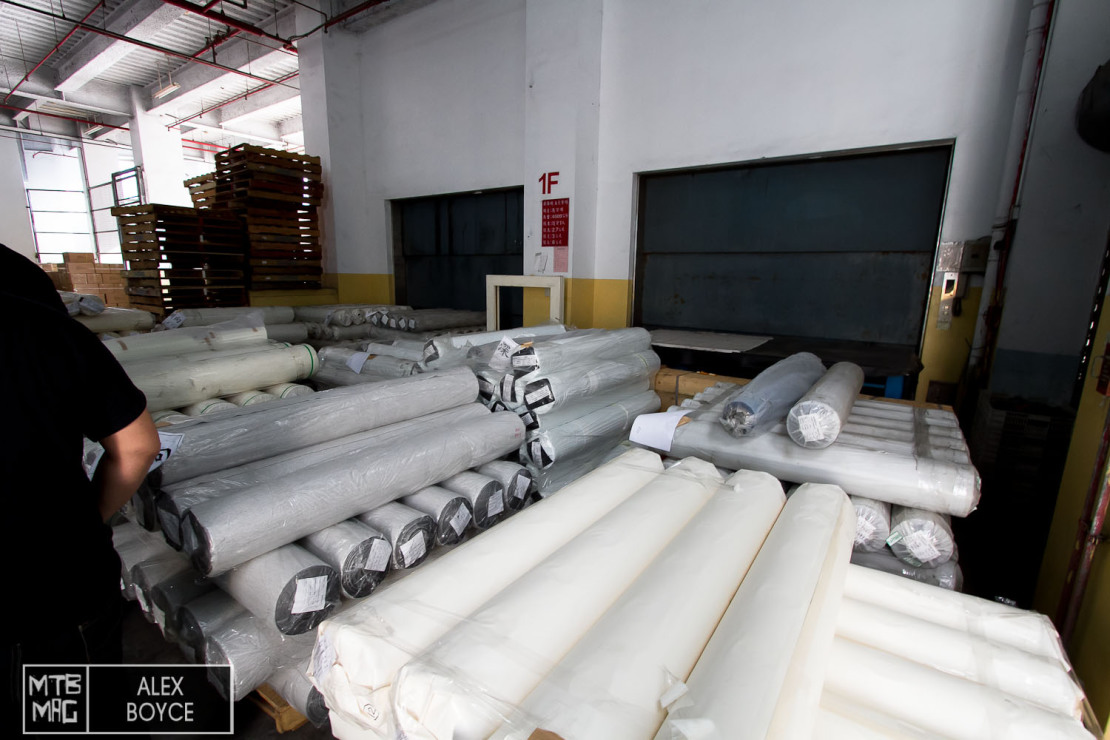
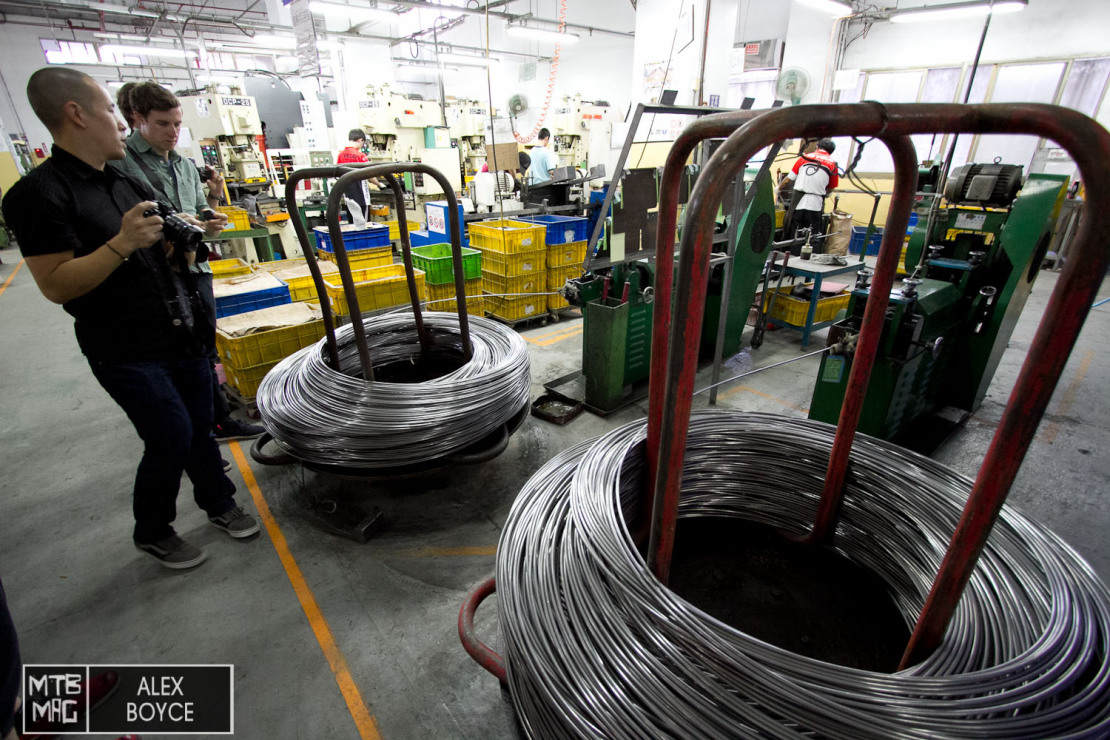
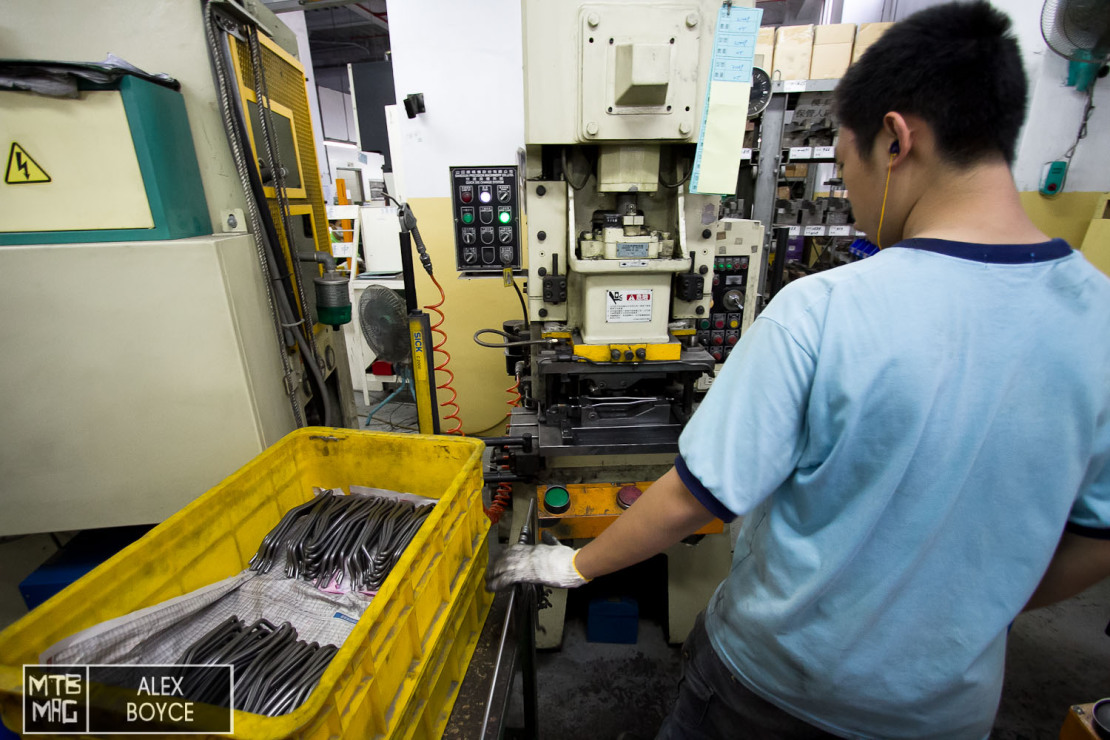
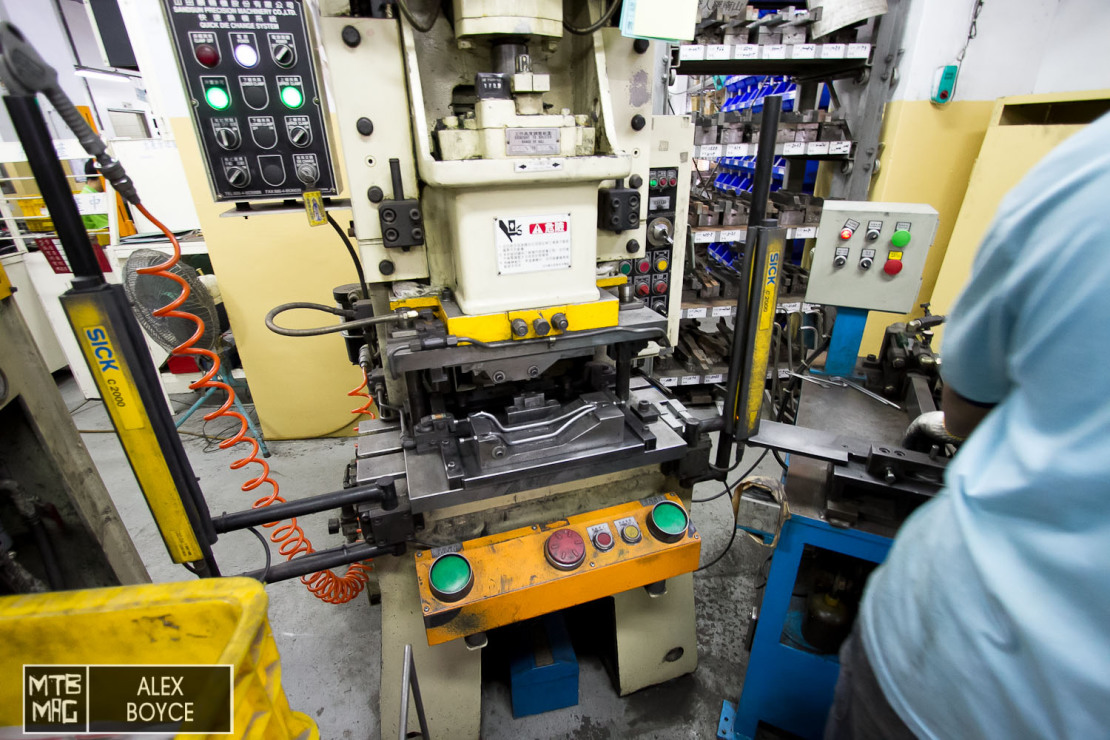
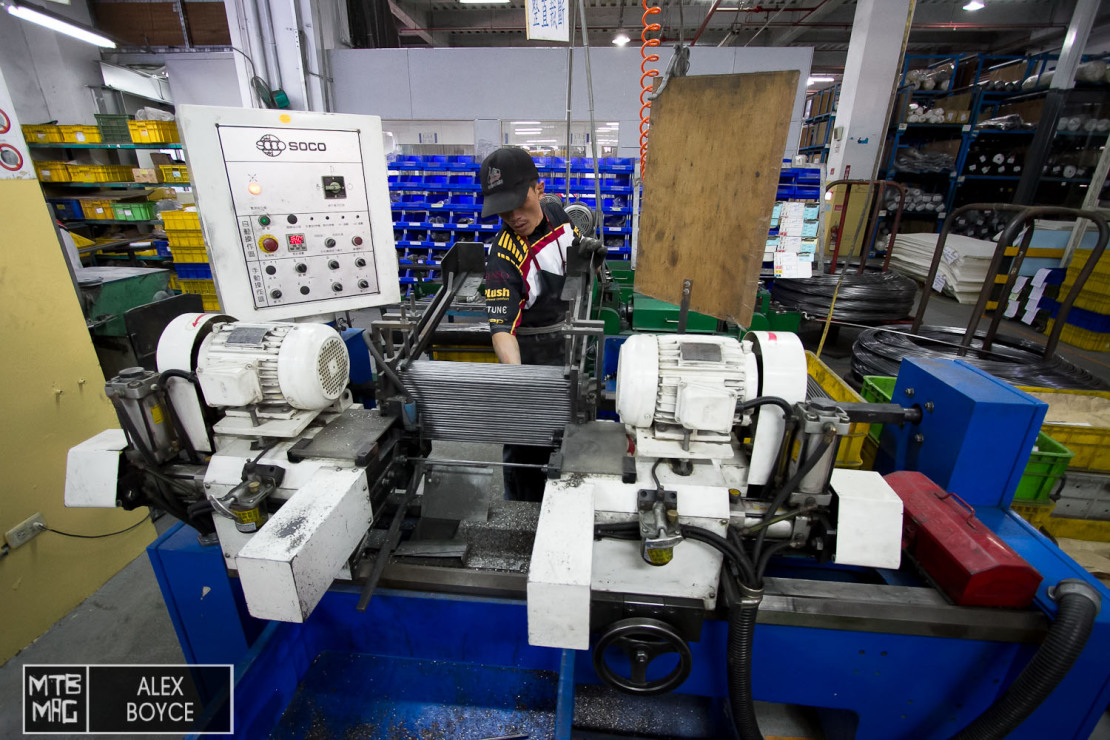
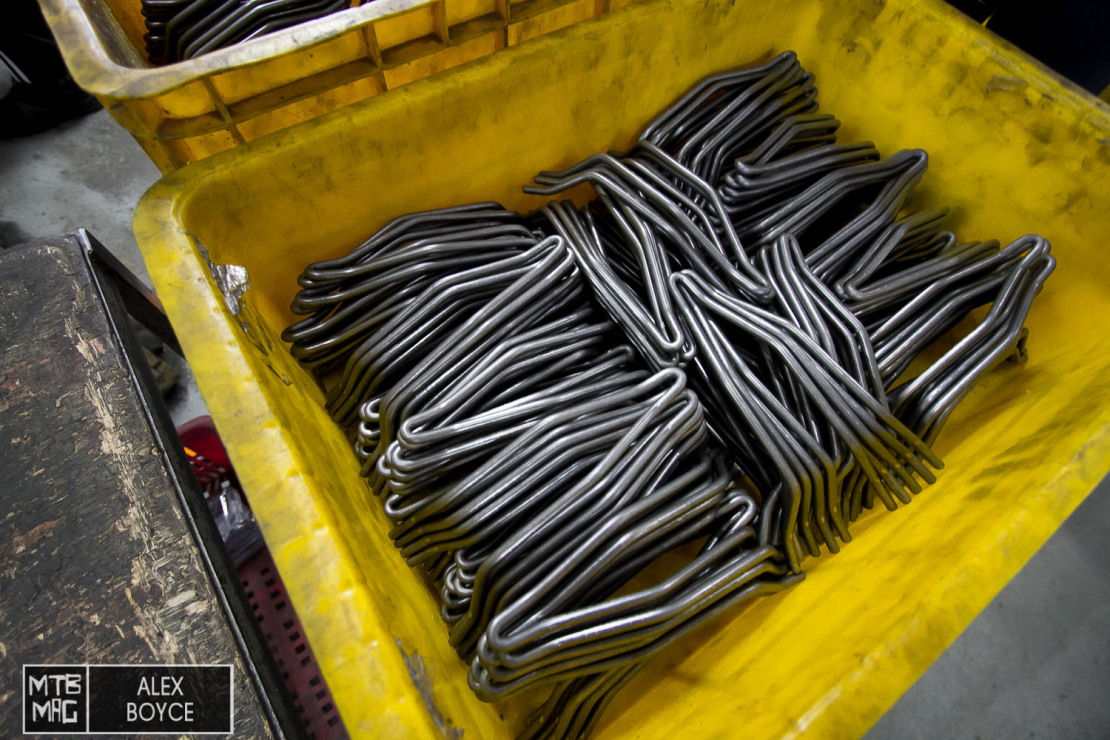
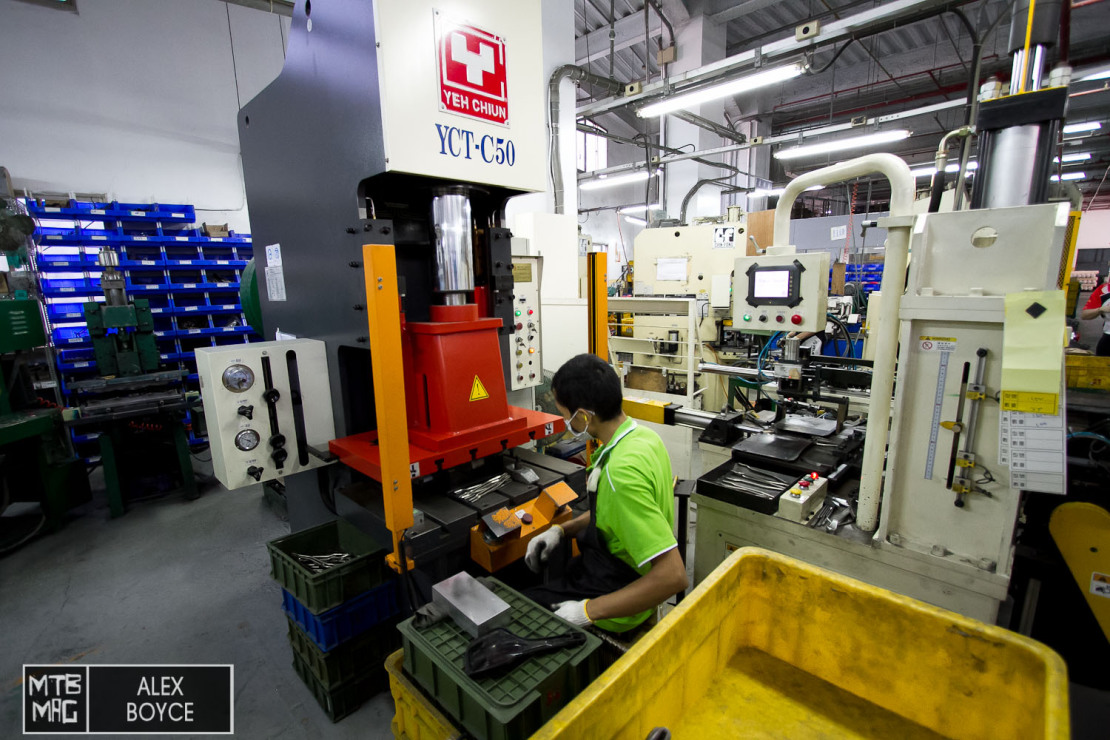
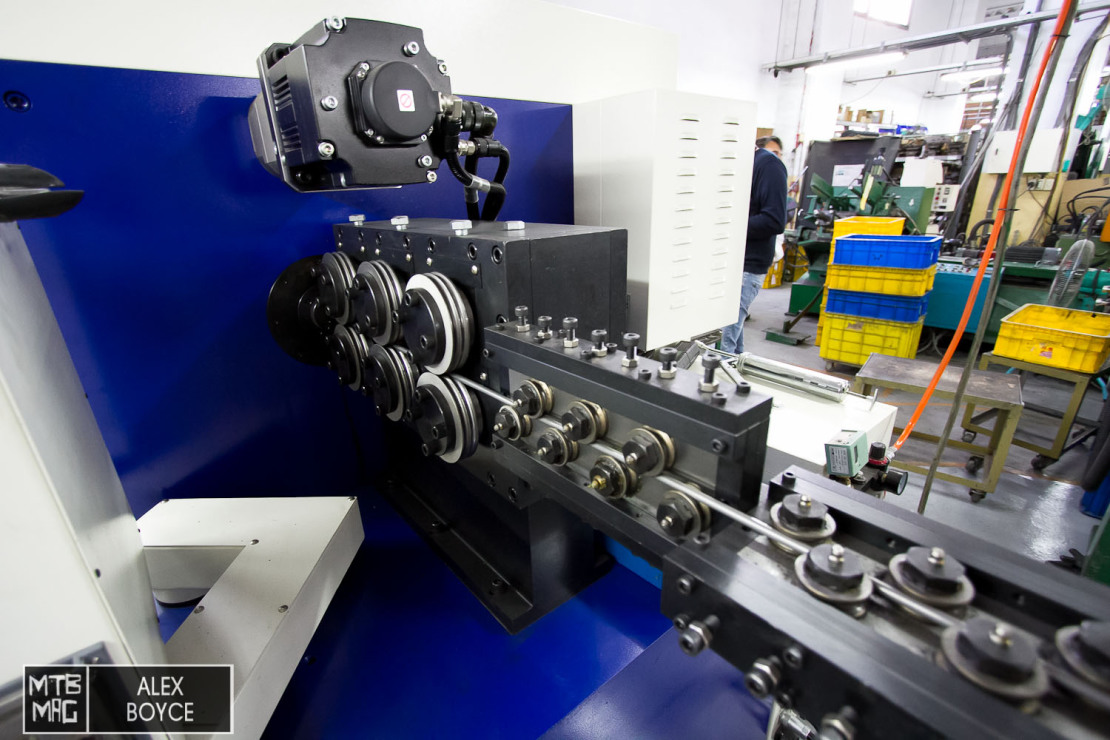
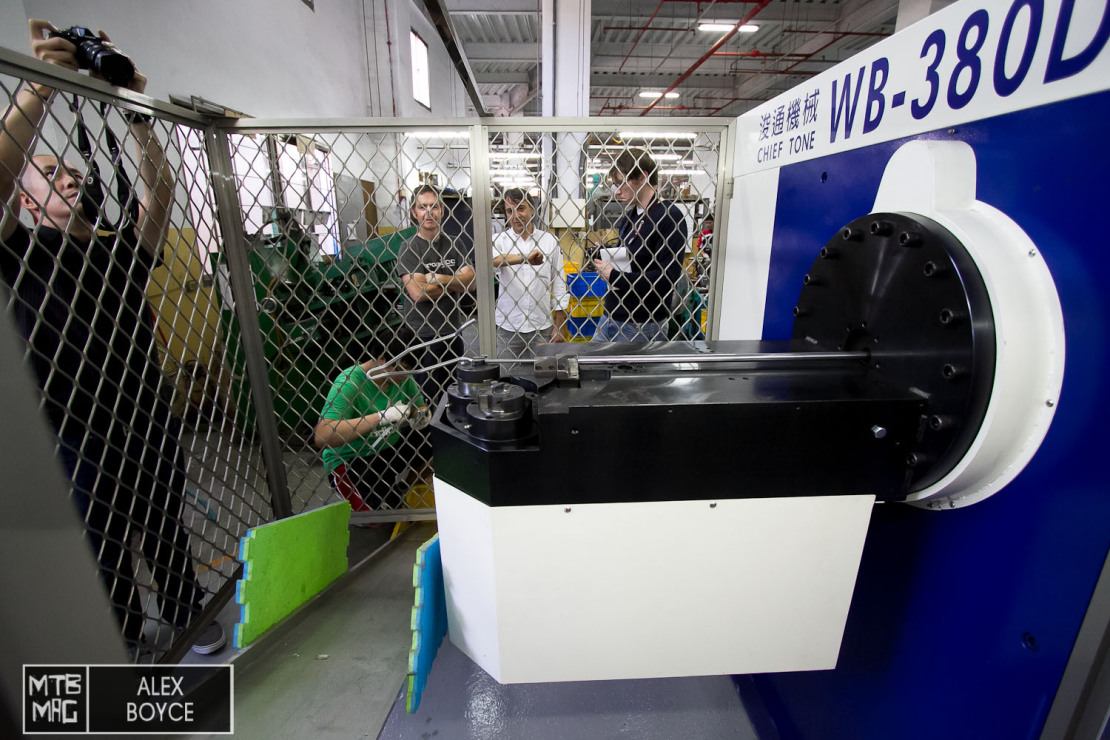
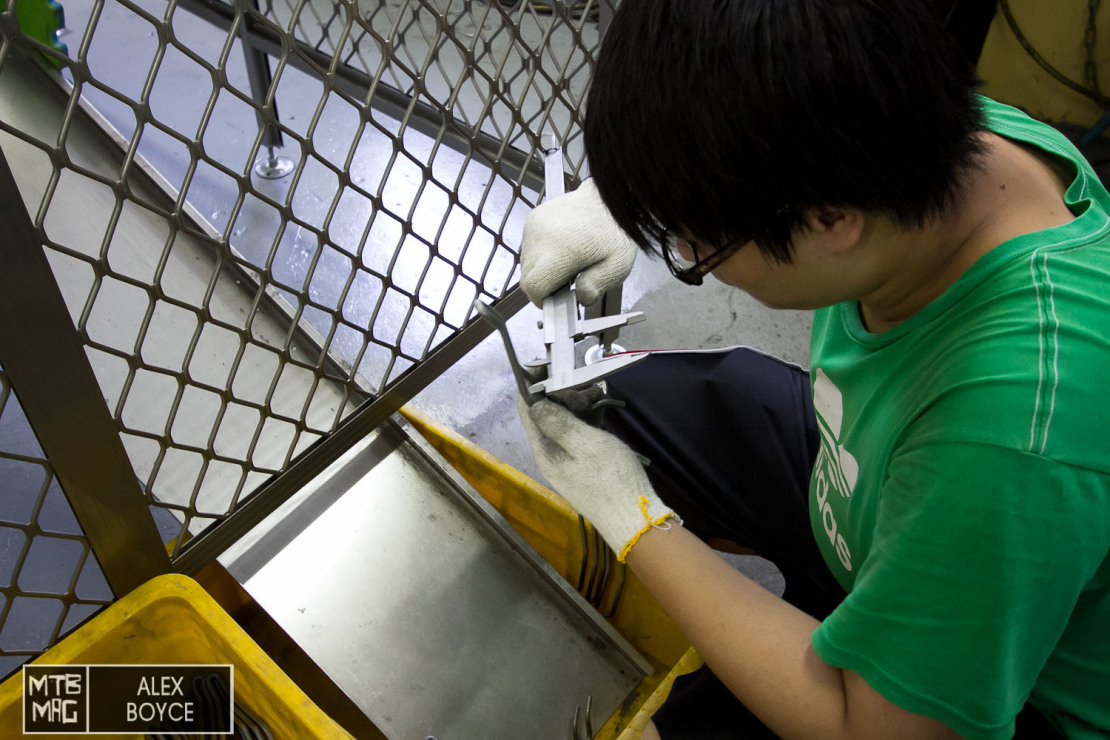
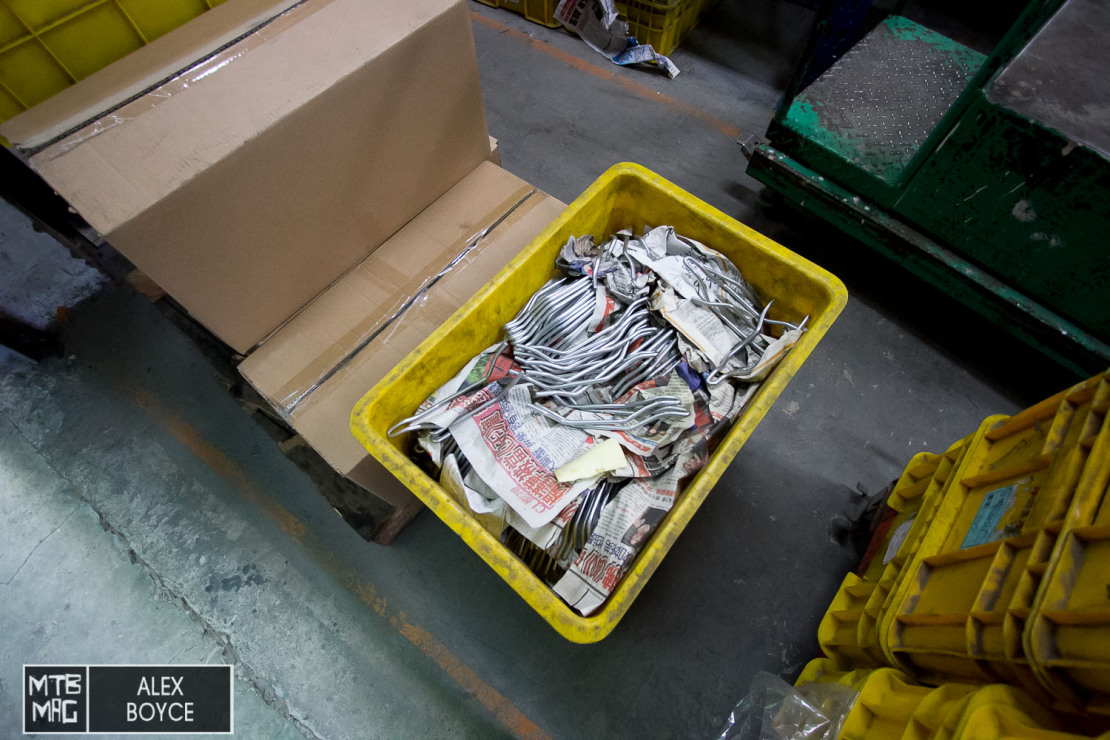
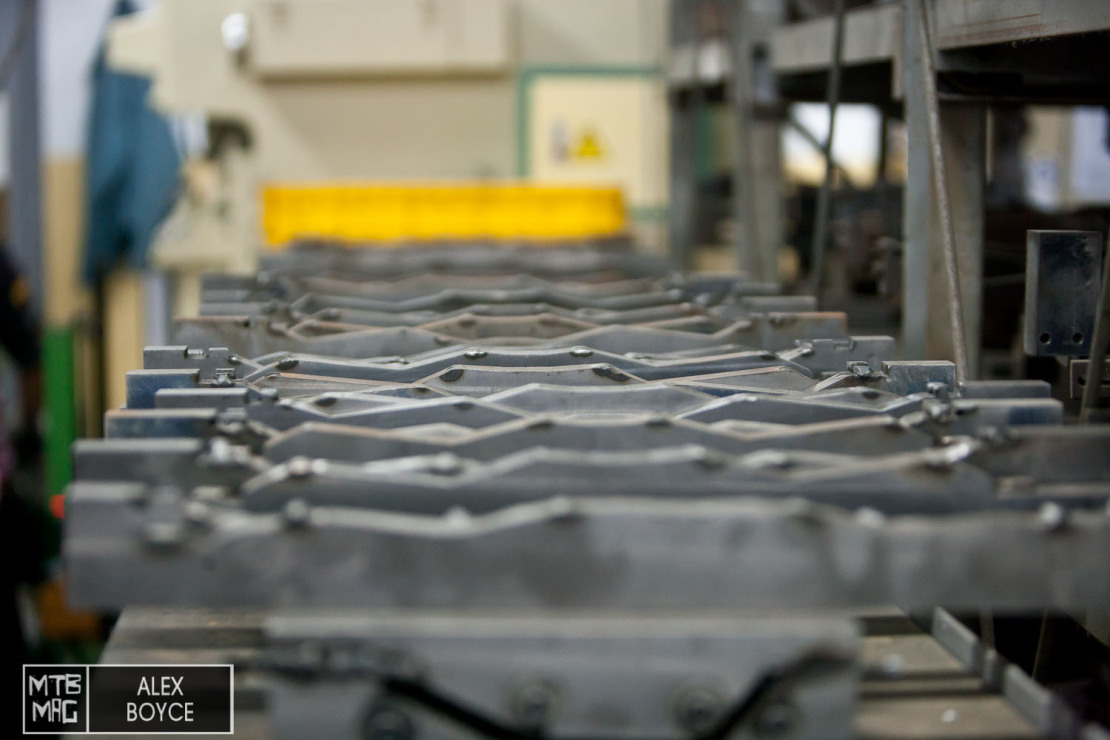
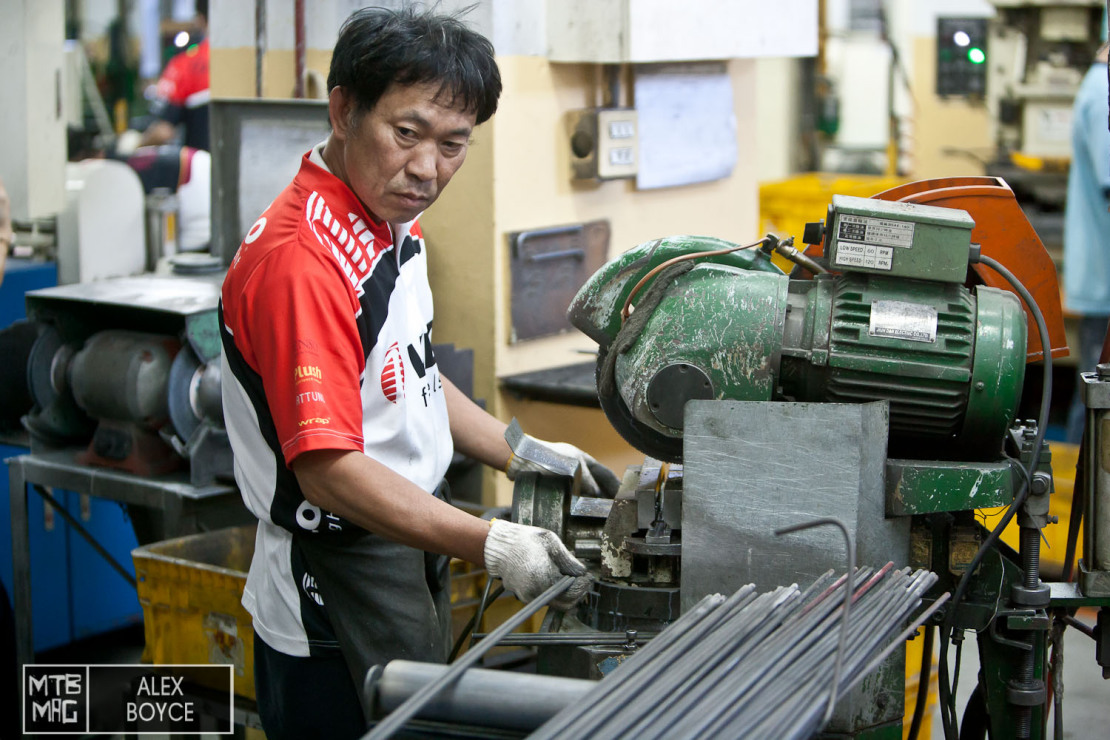
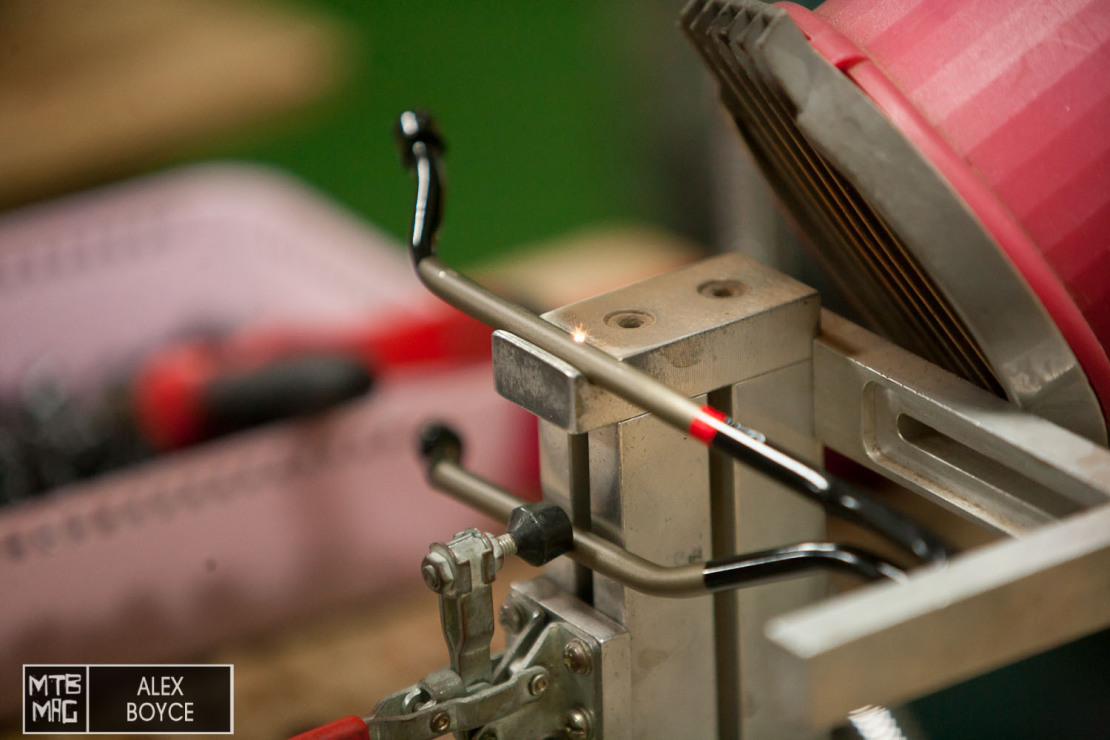

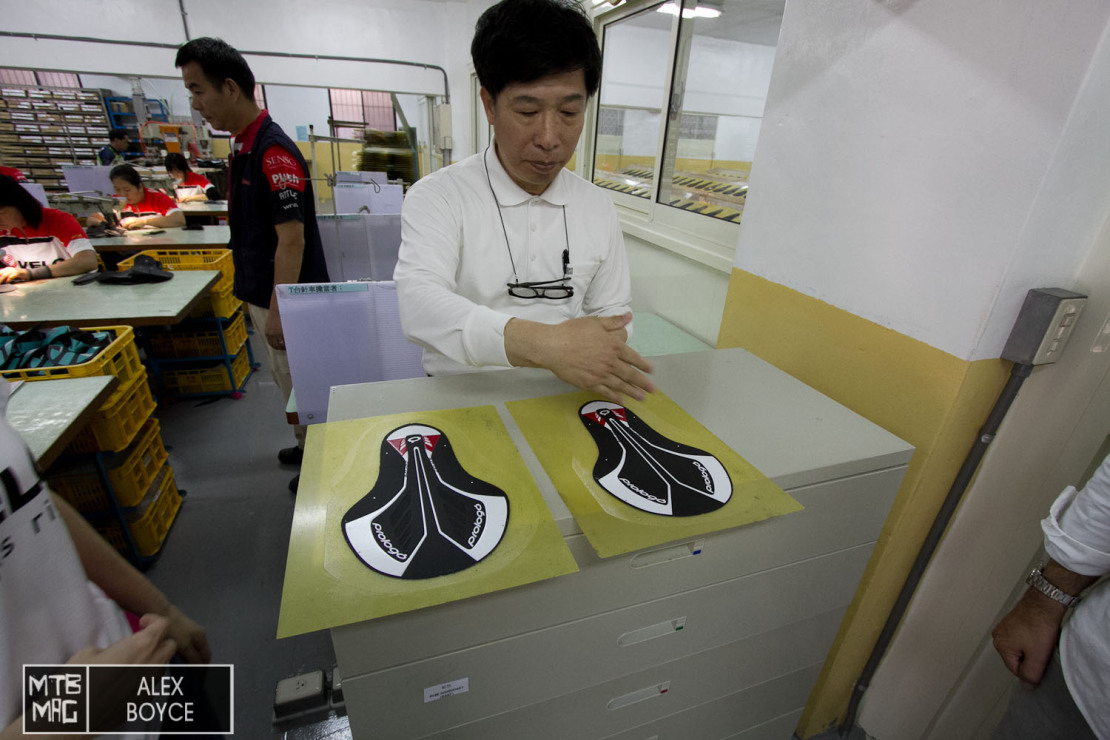
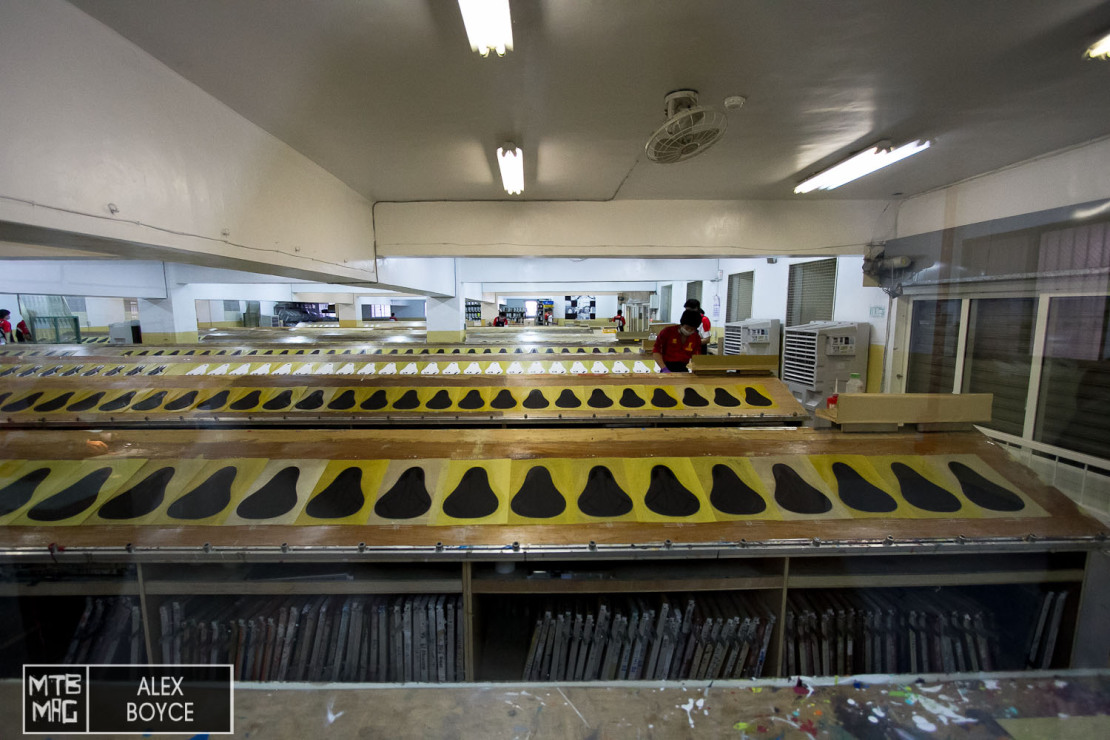
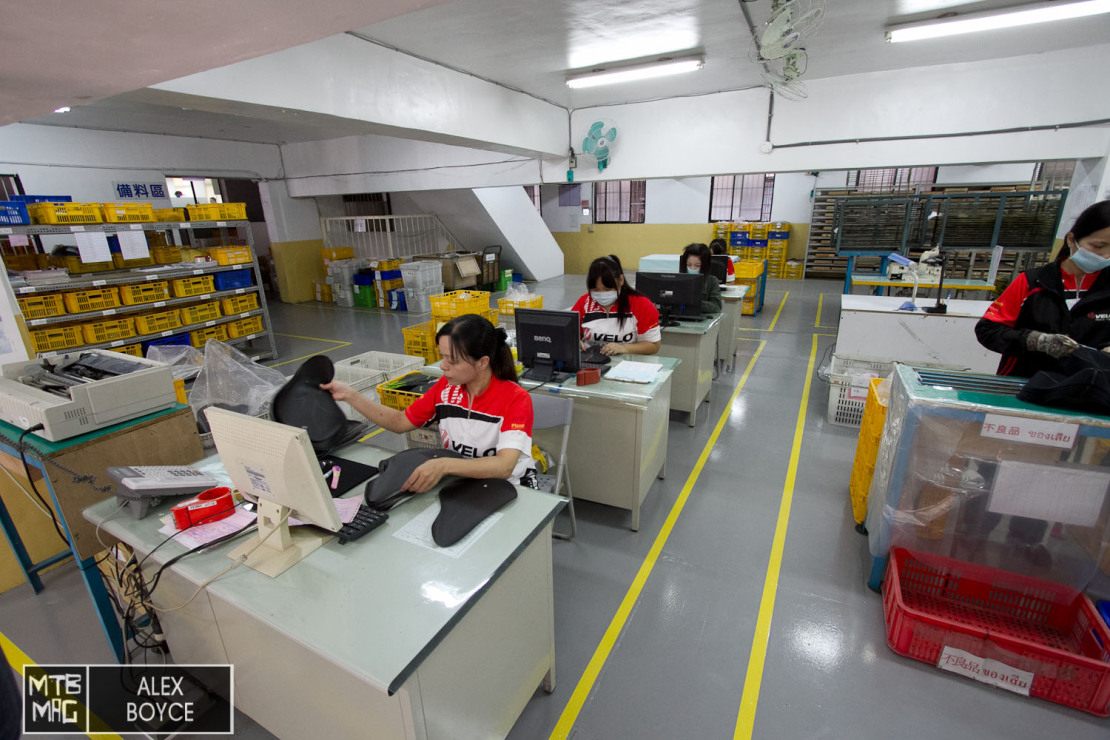
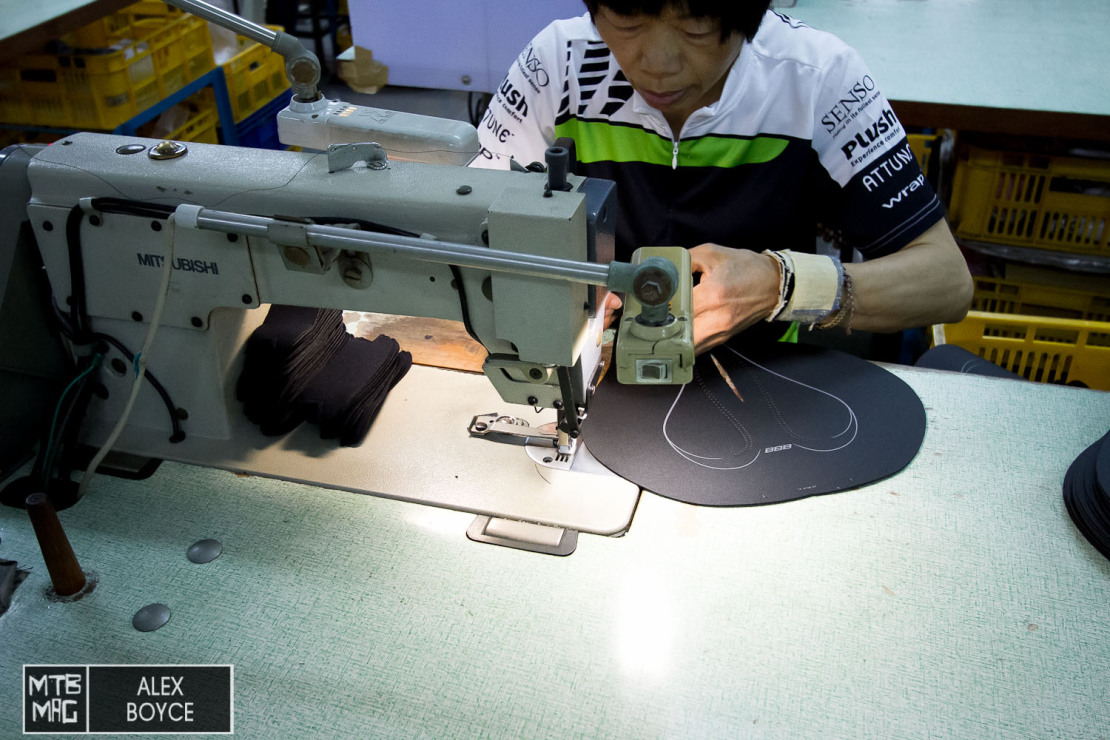
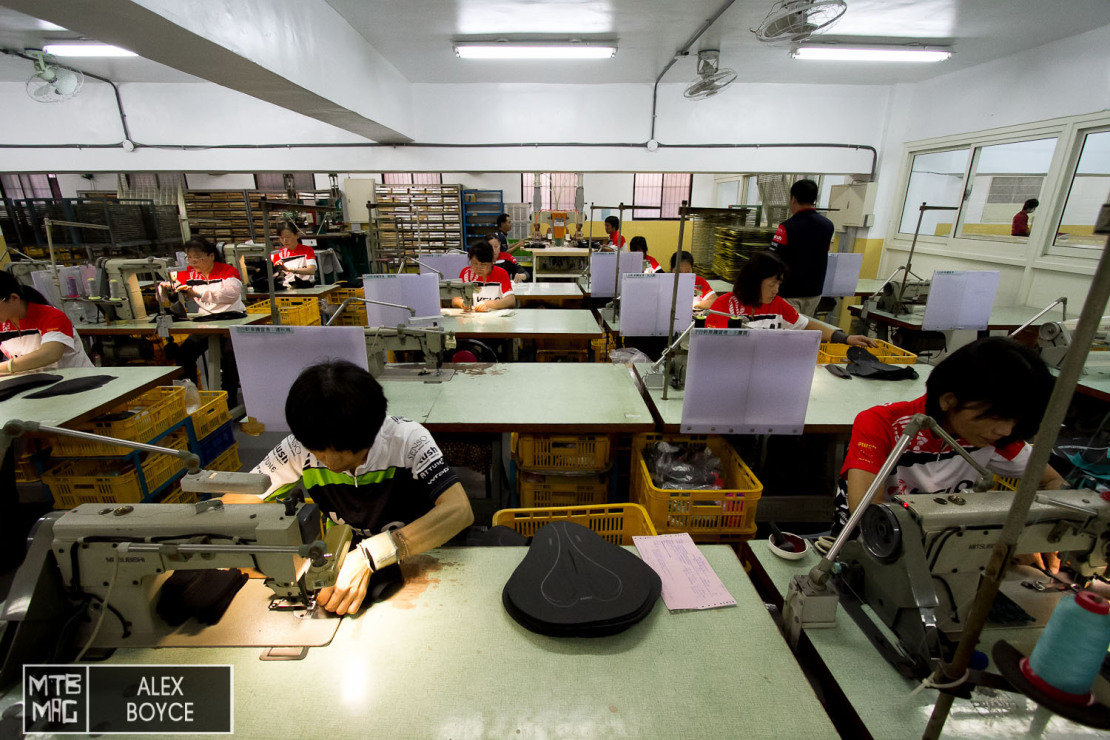
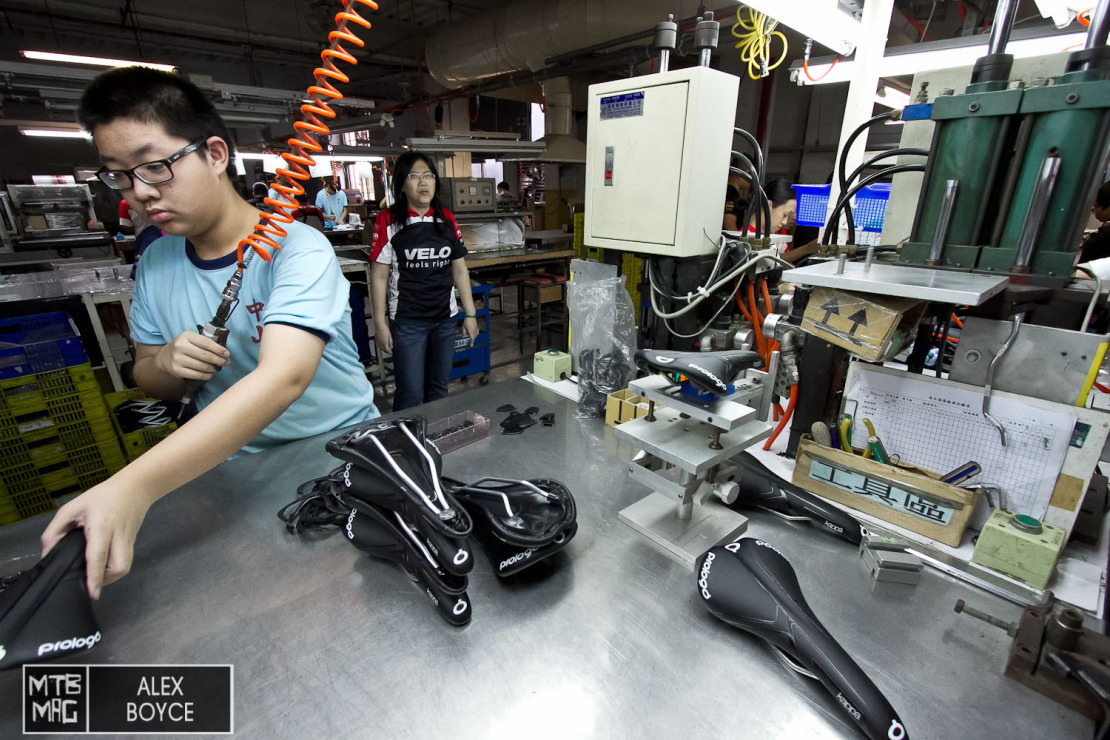
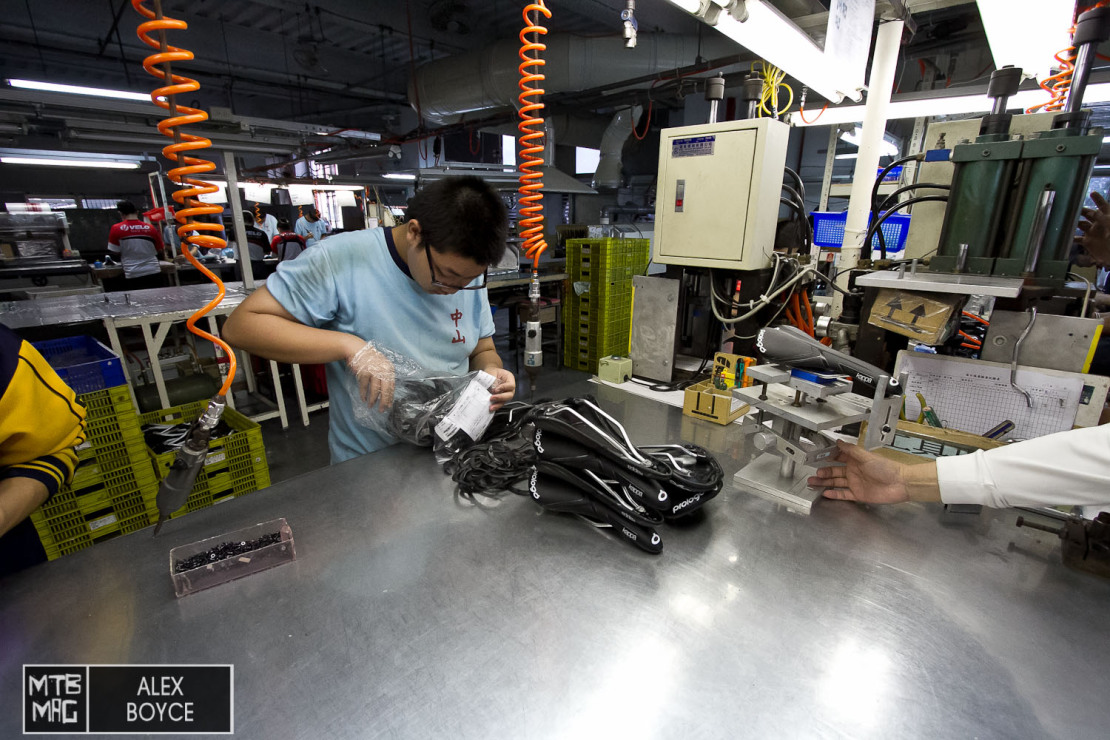
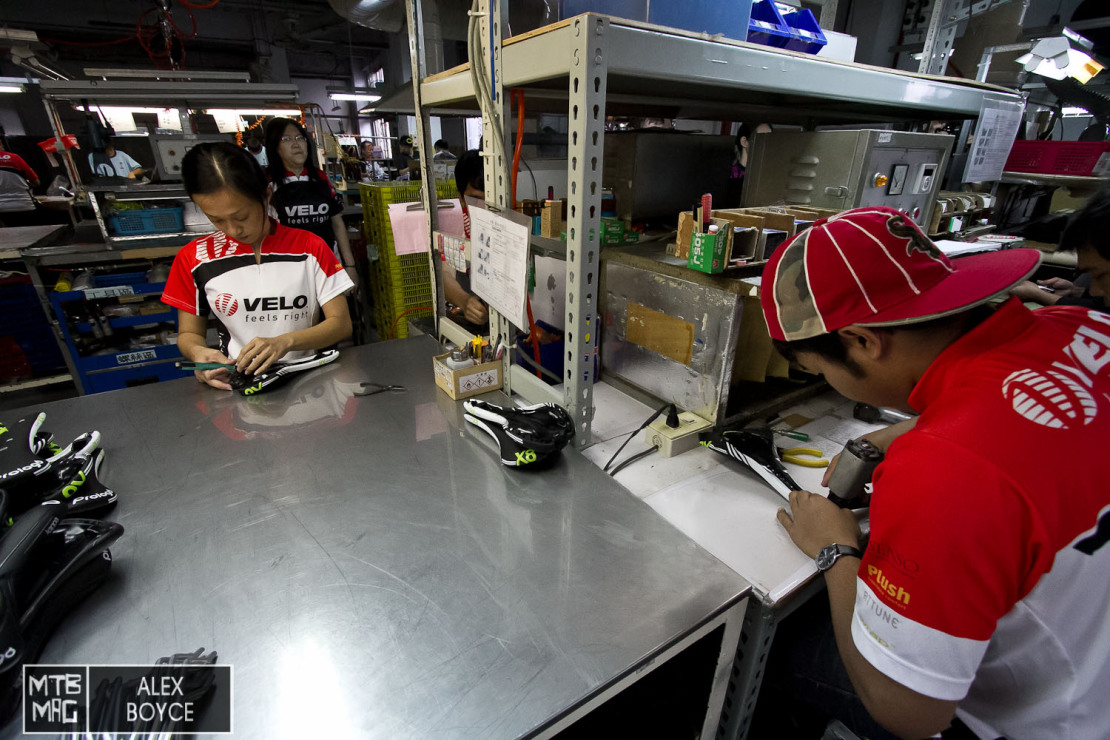
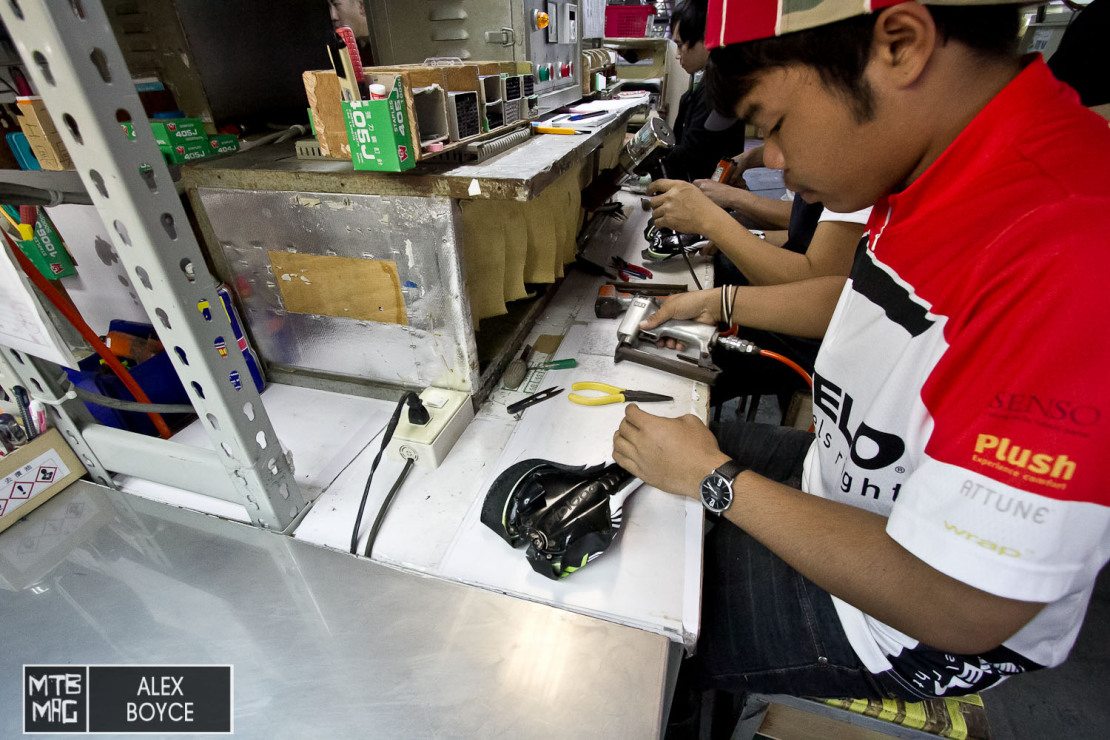
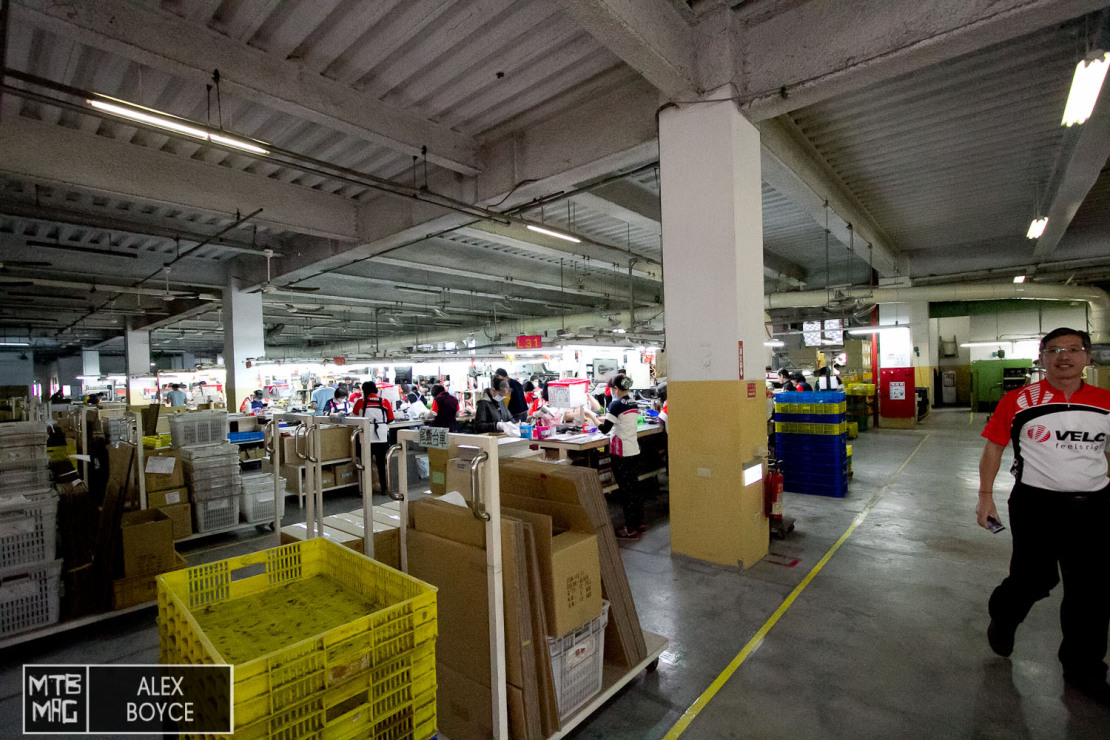
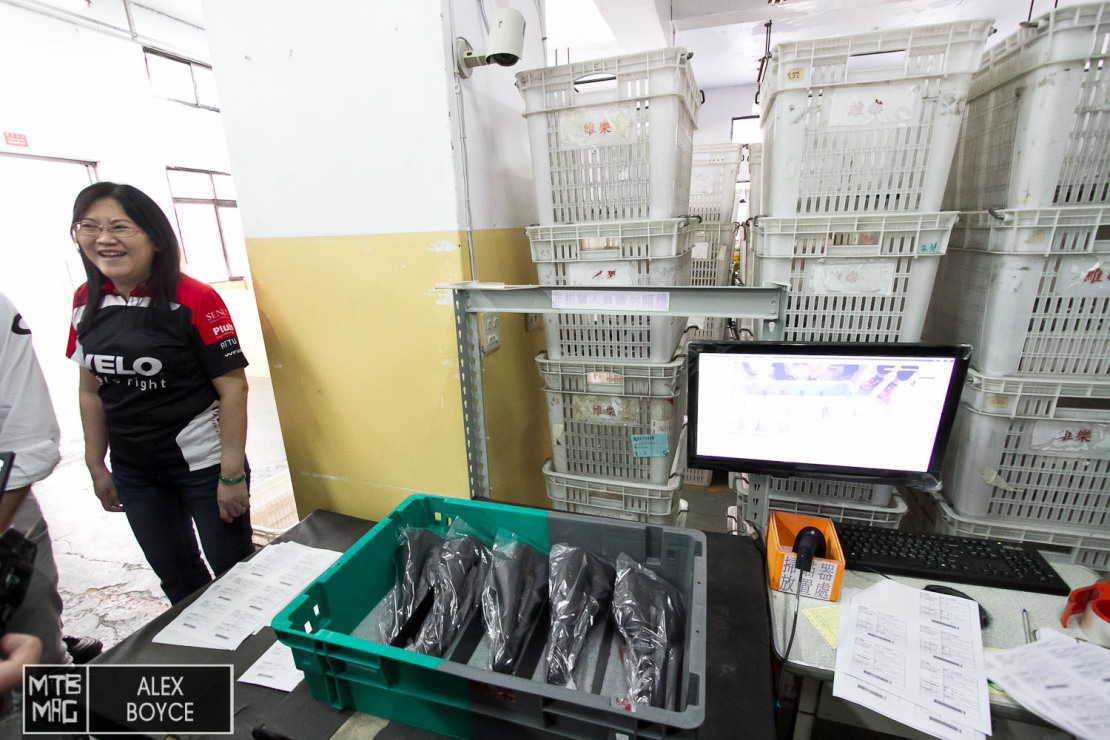
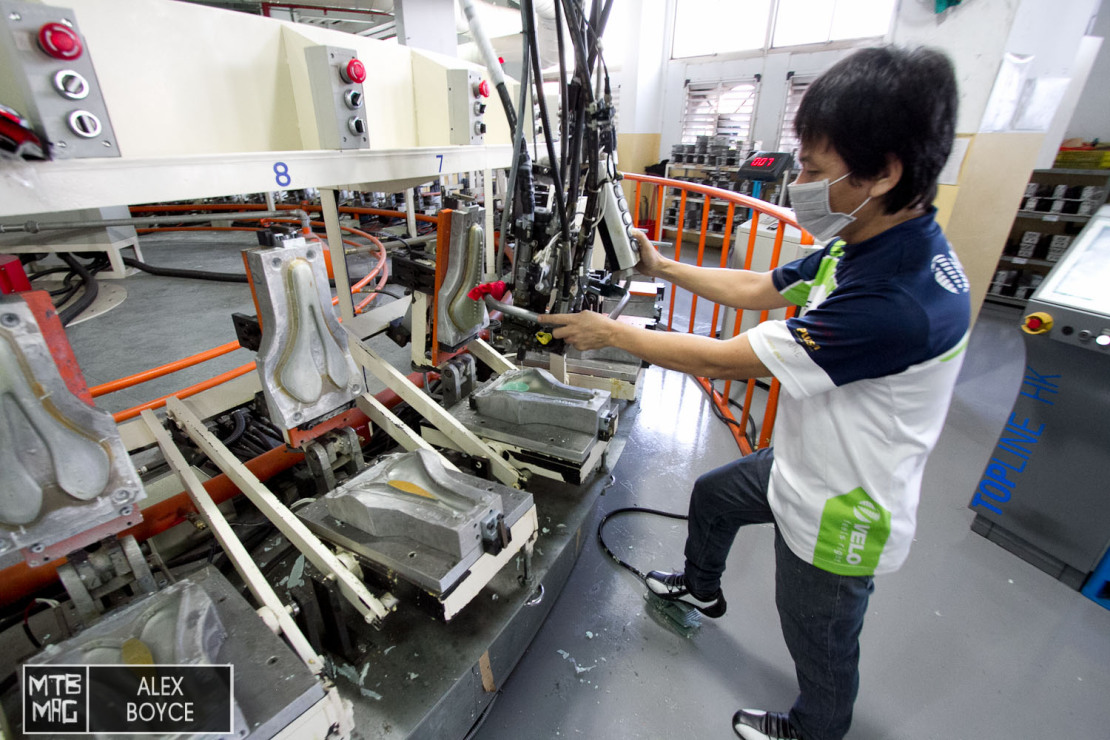
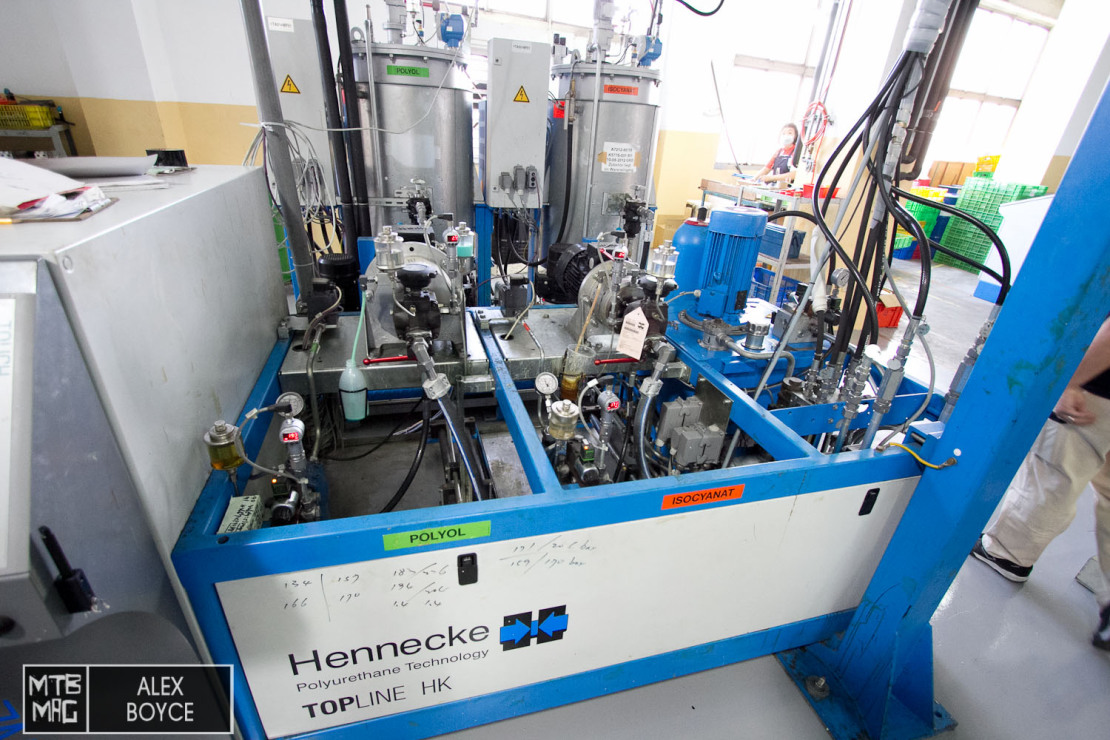
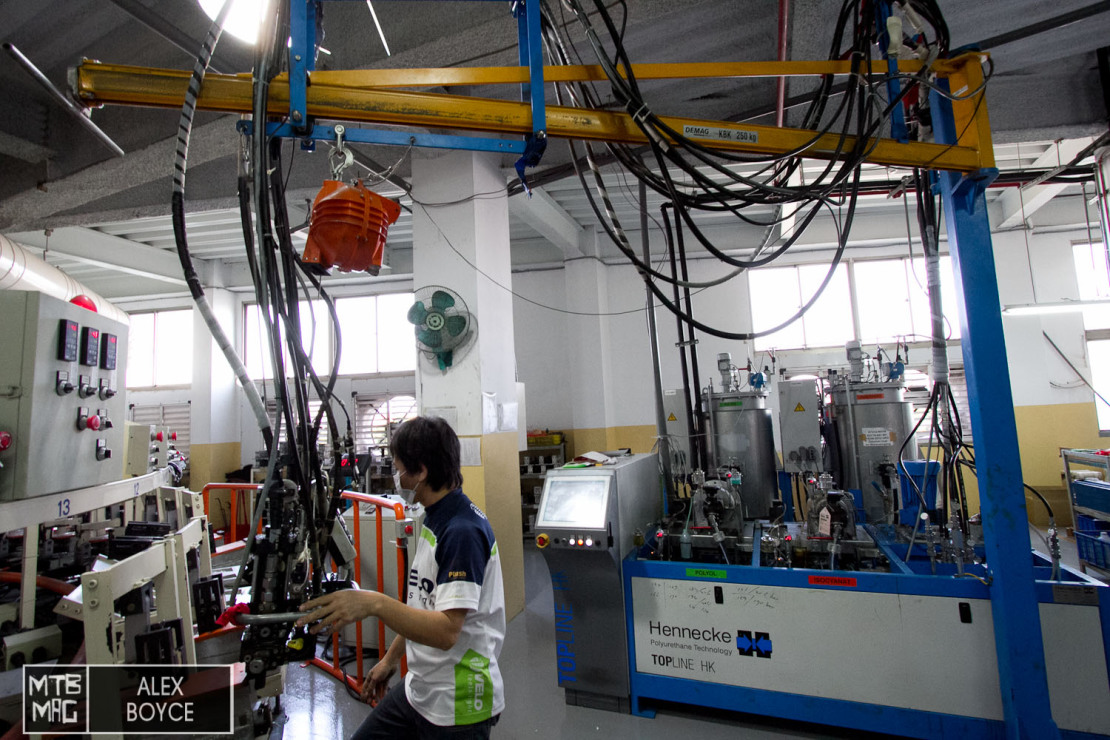
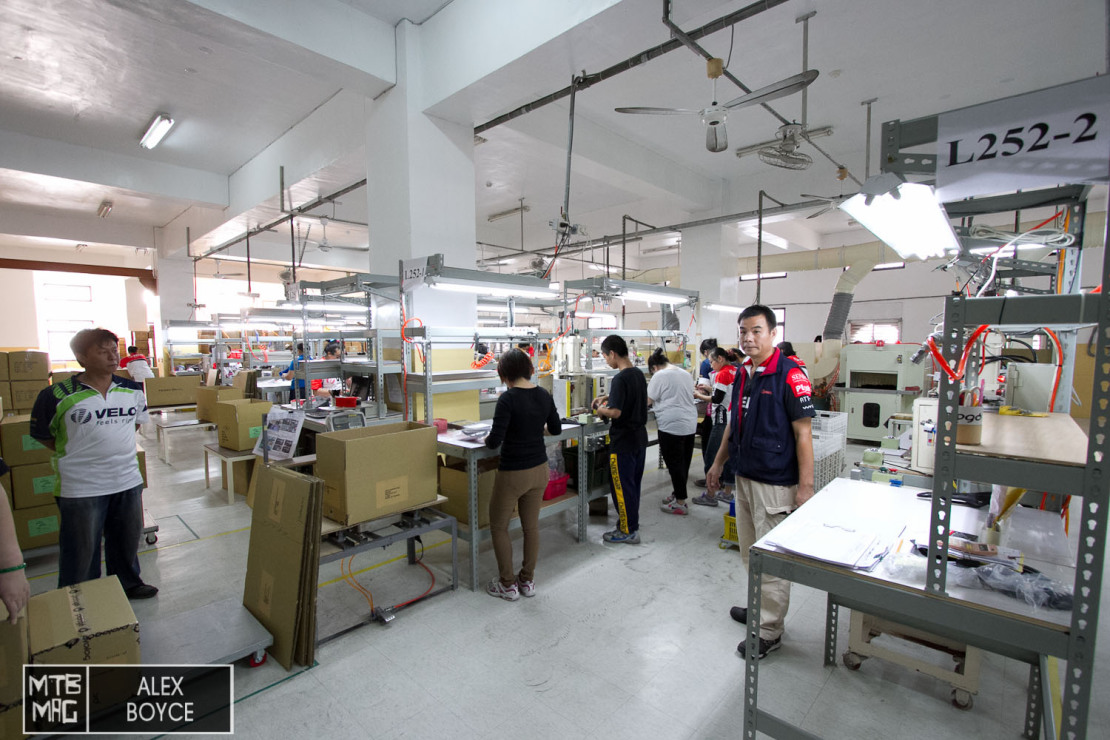
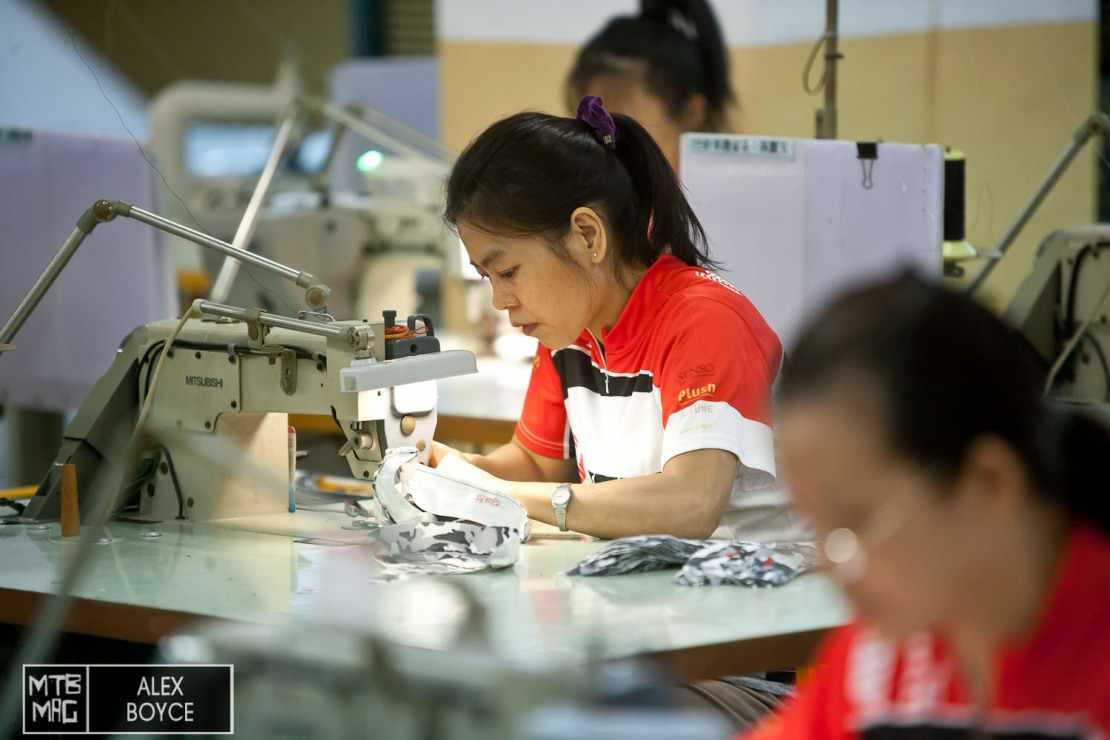
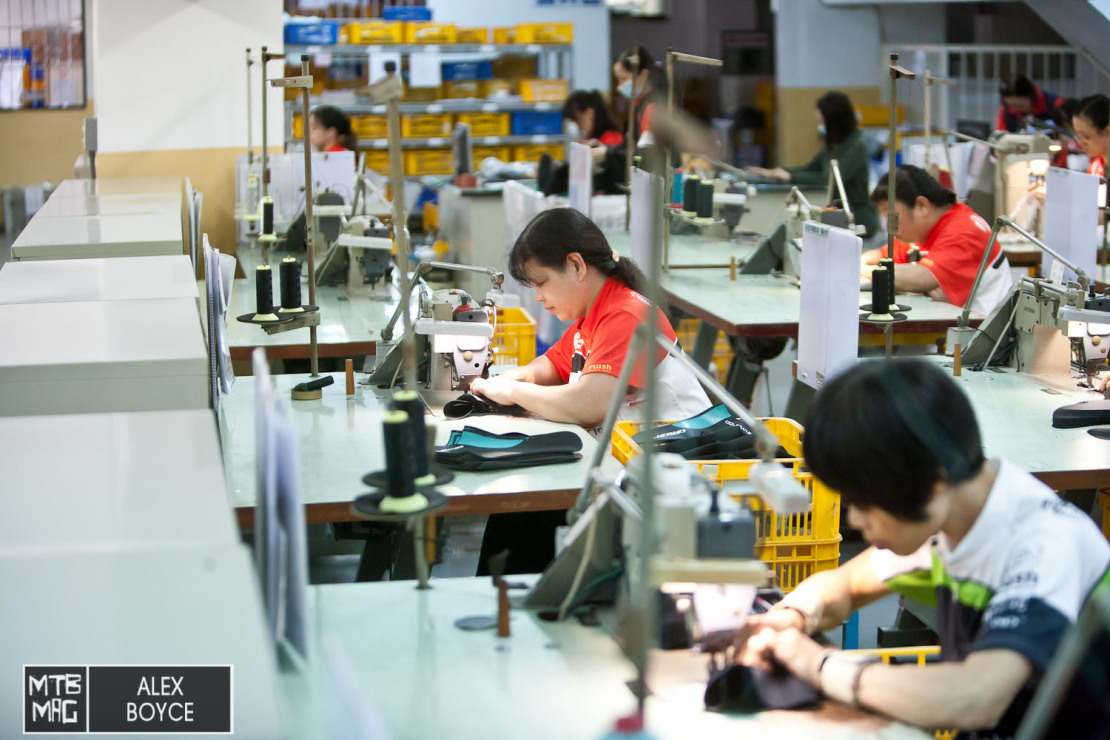
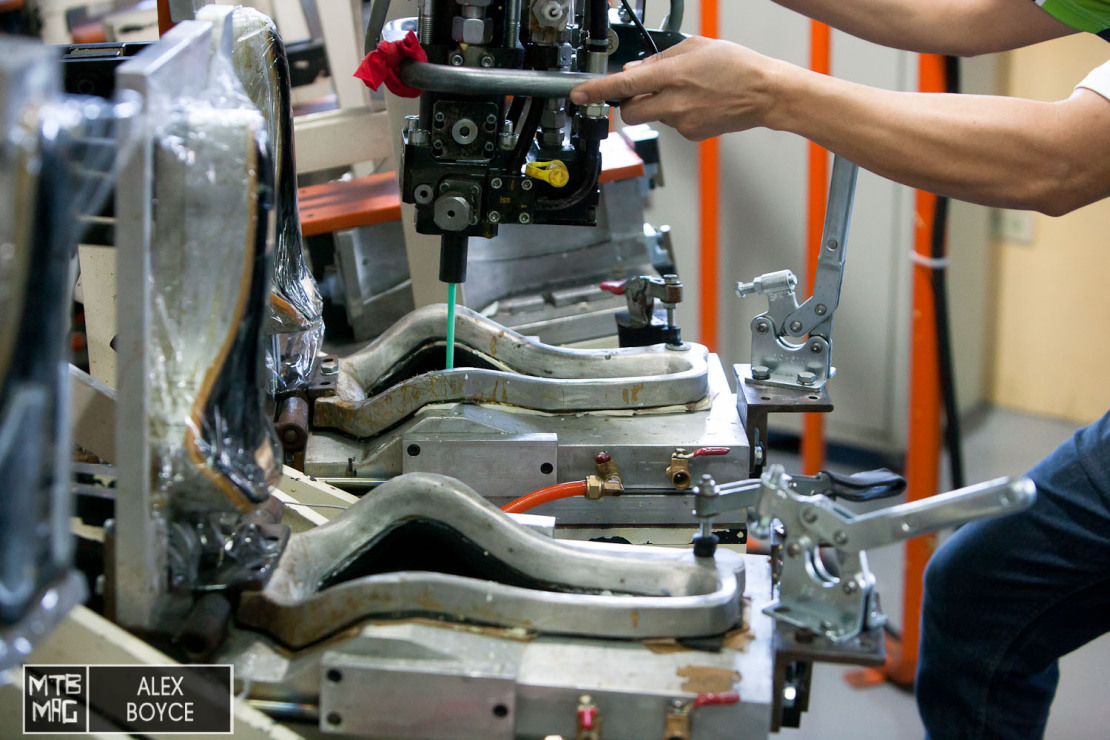
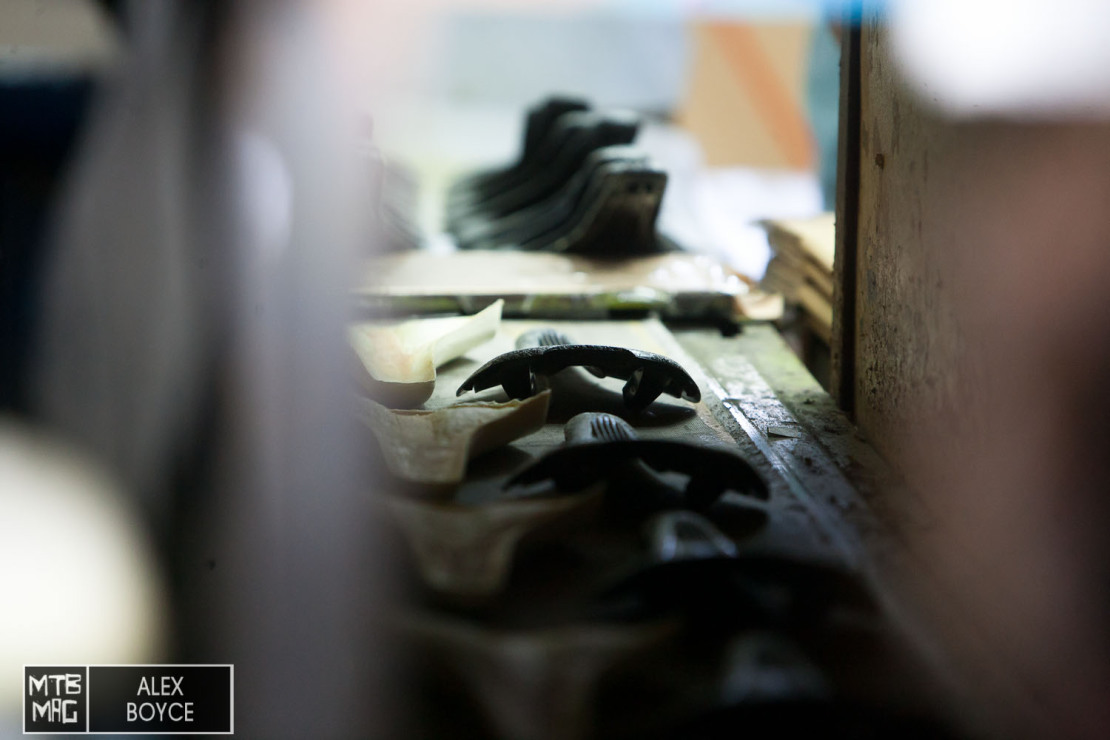
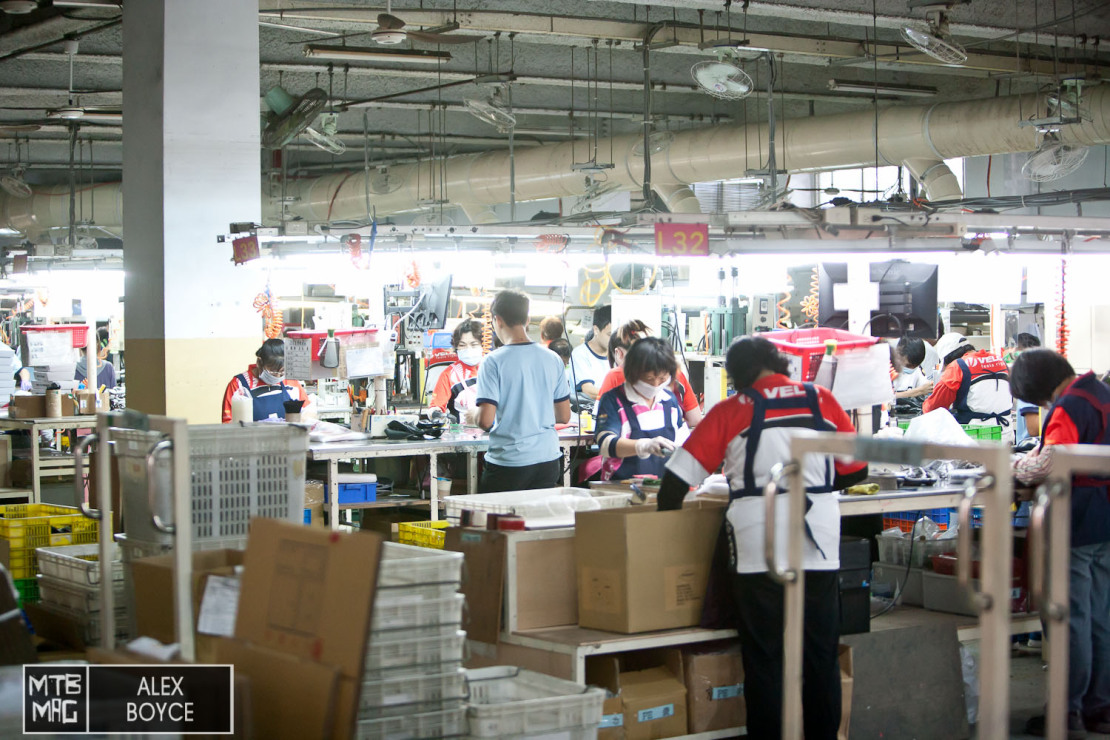
Research and Development
Velo carries out it’s own research and testing to make sure that all of the components work as they intend and designed them to. With many processes automated saddles can be put through repetitive tests to make sure they meet the standards of quality control, we were shown, rubbing tests, temperature tests and sitting tests.
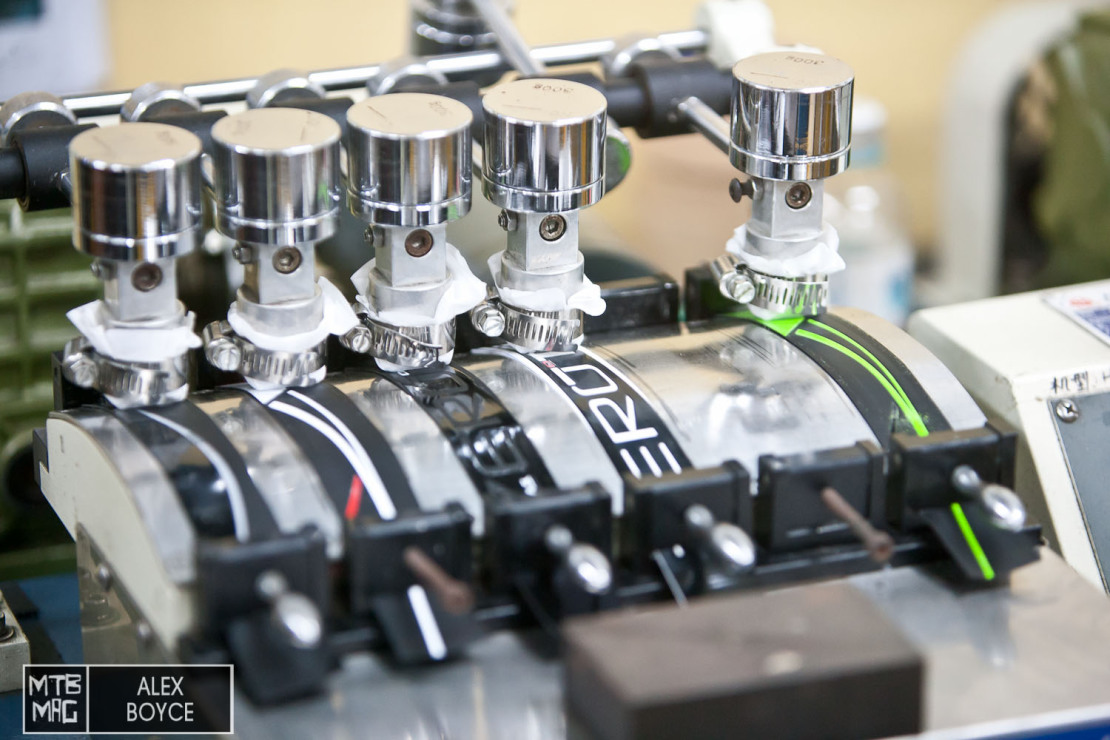
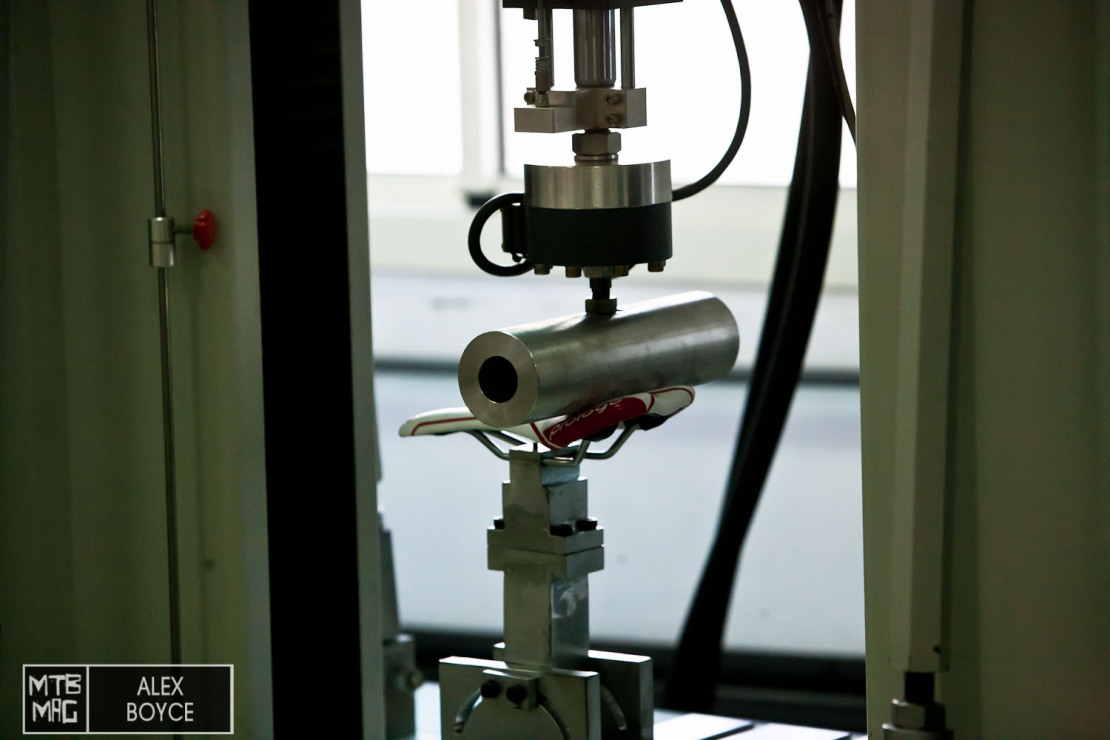
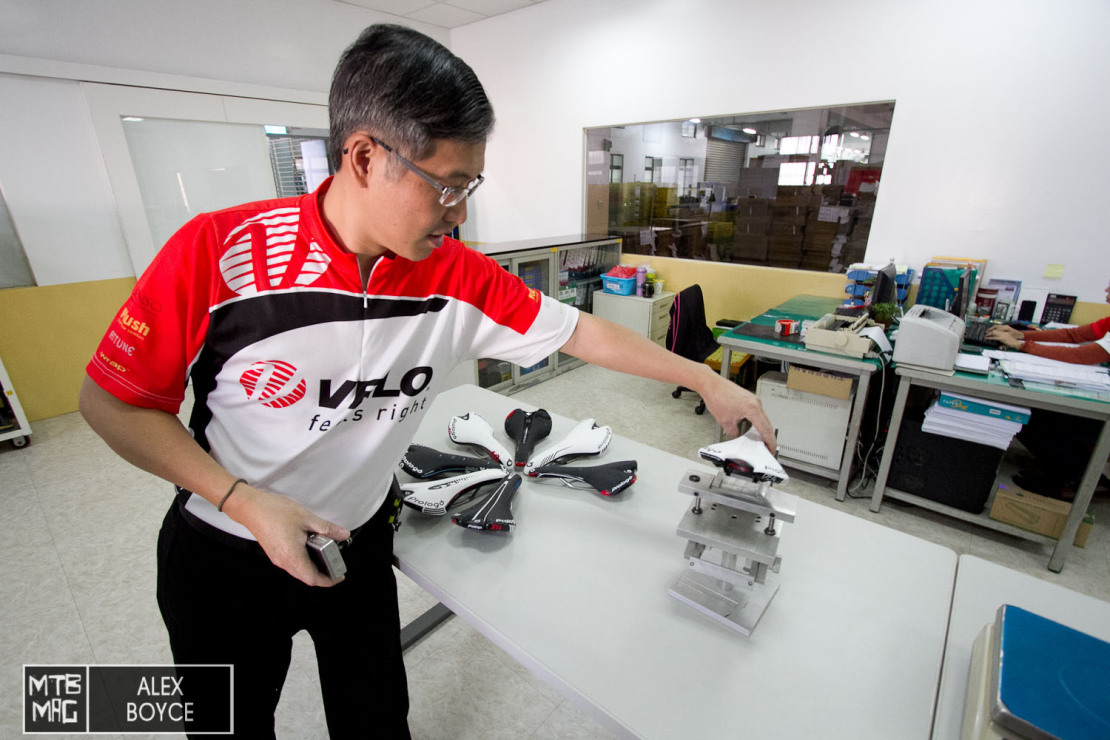
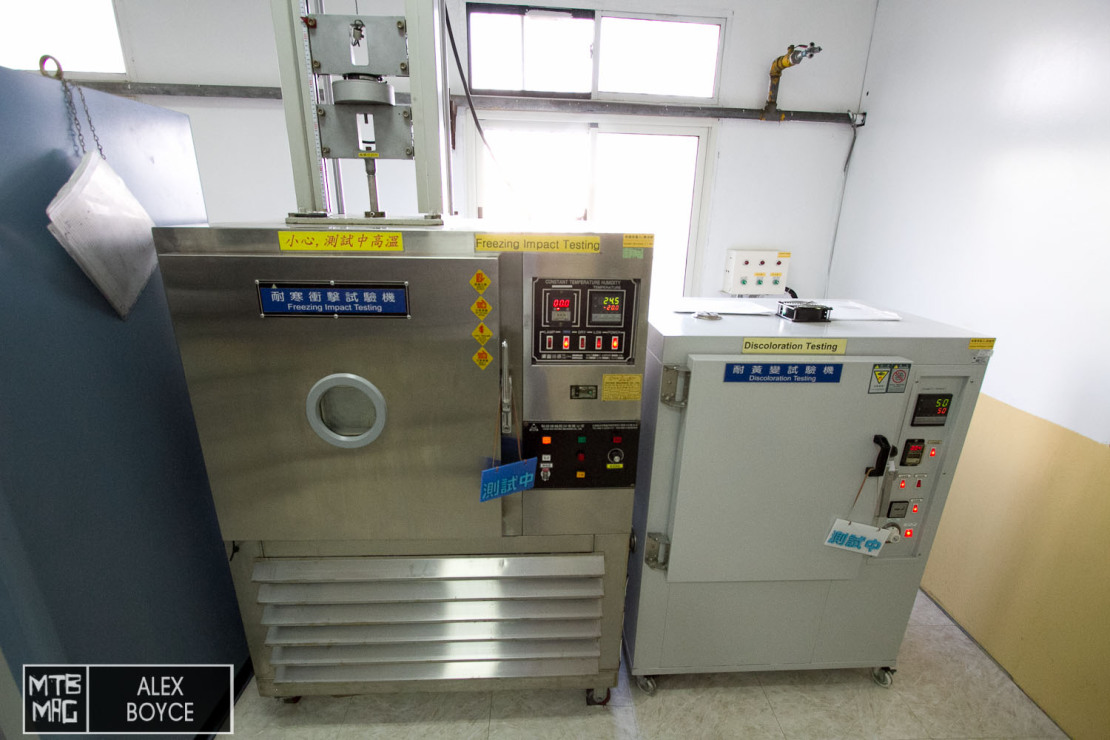
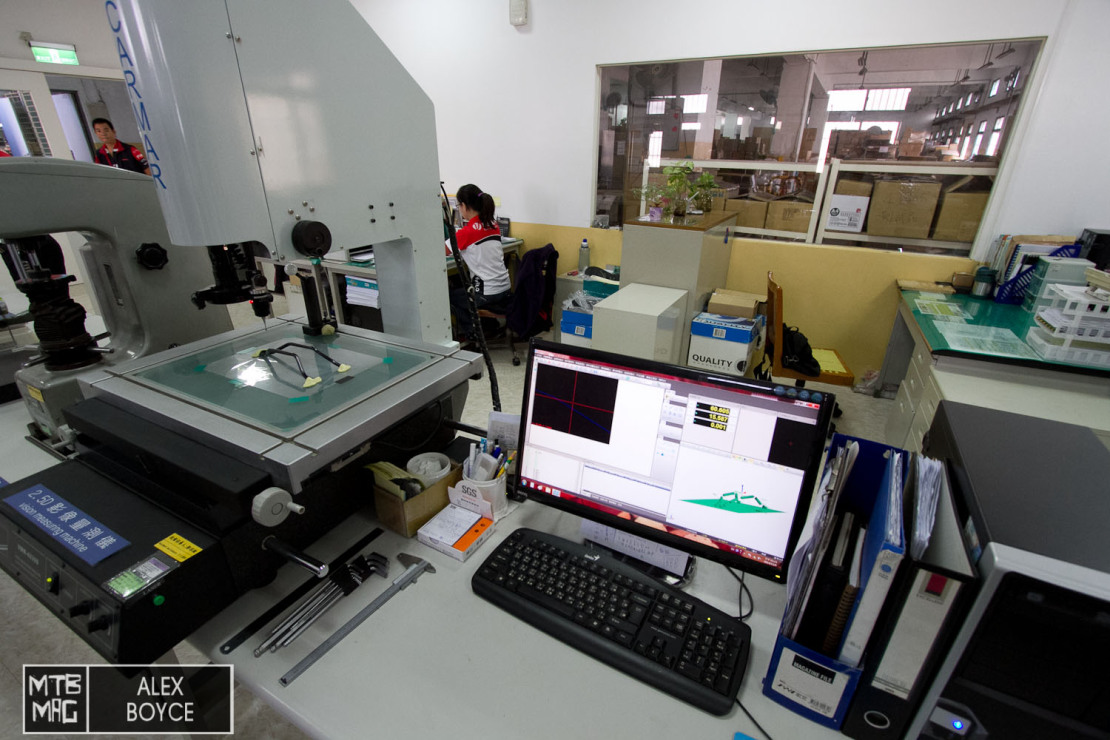
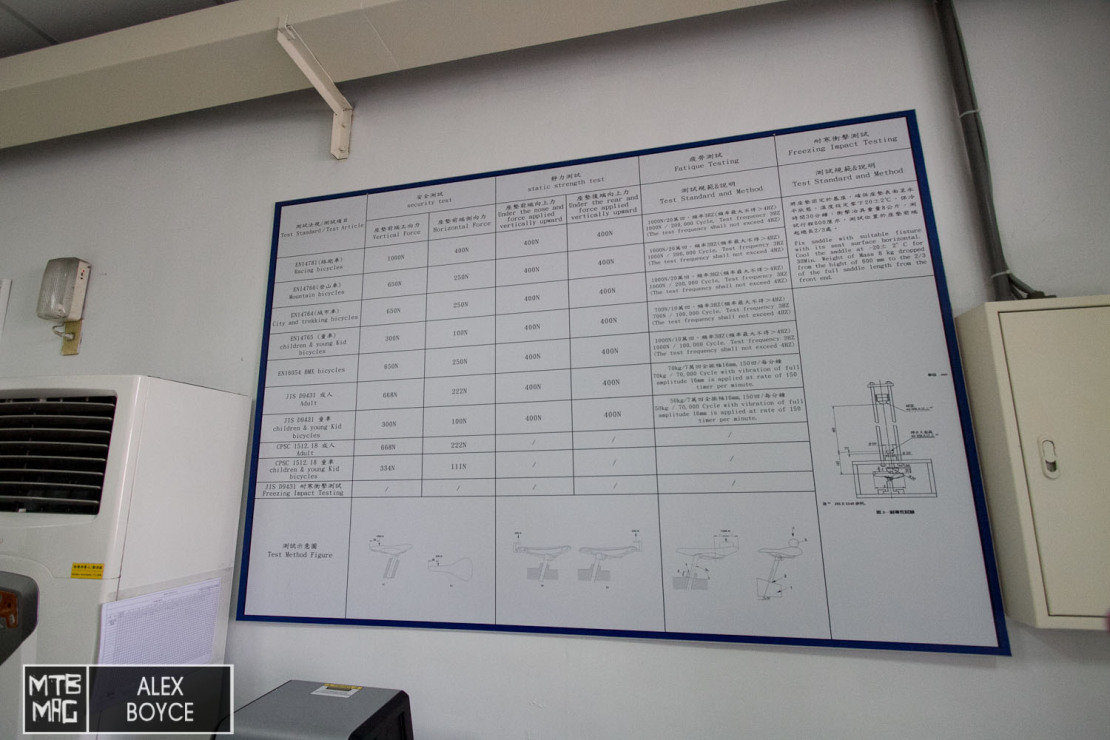
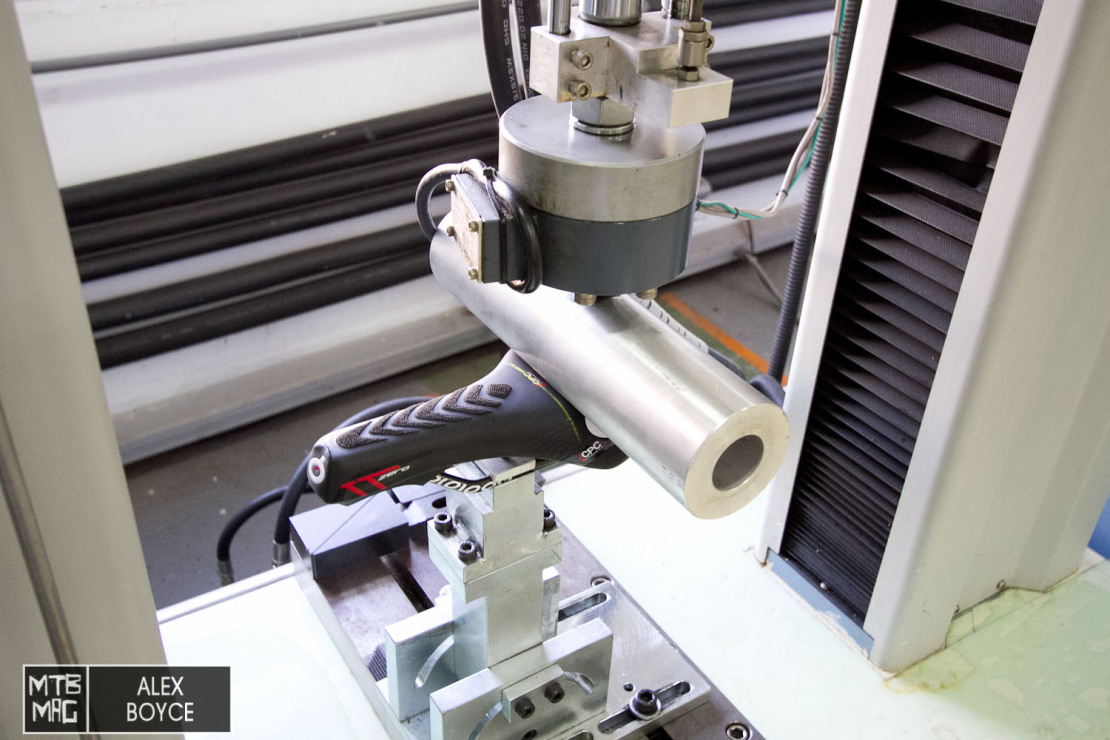
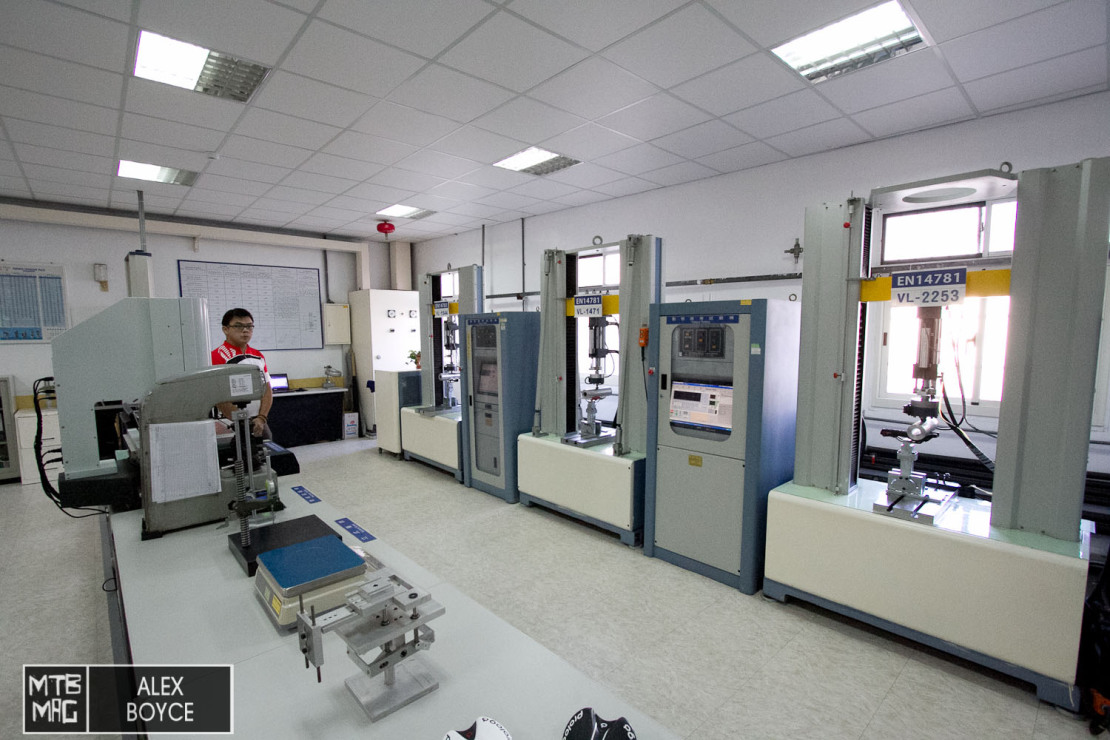
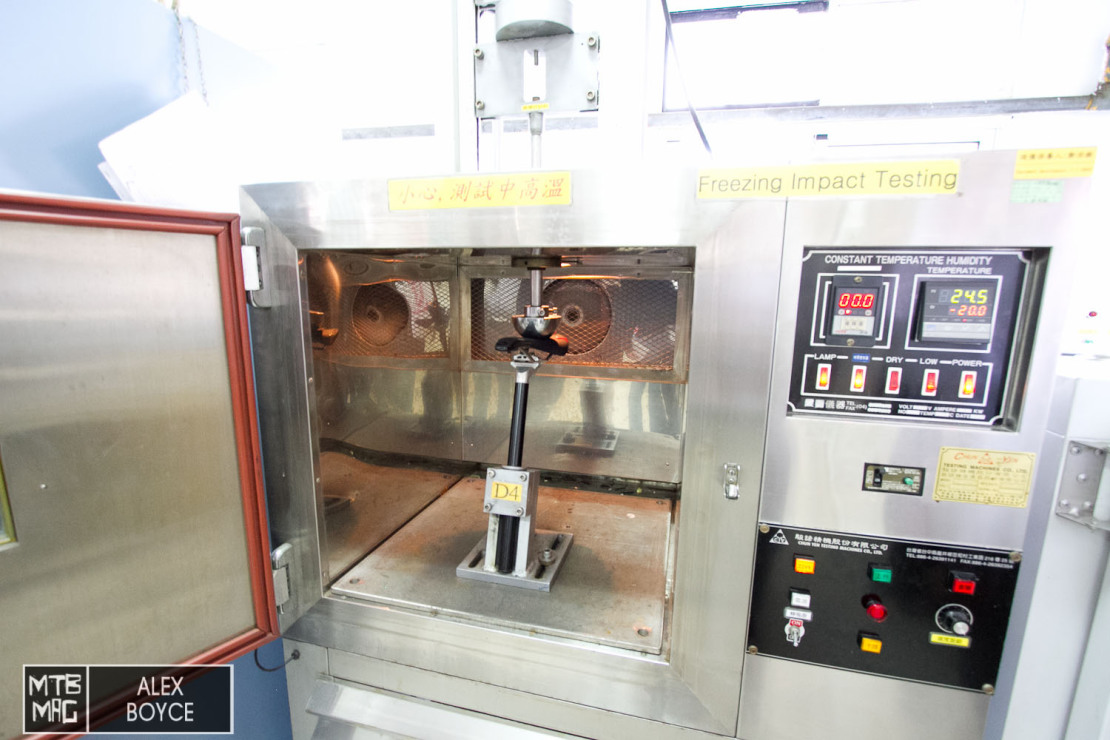
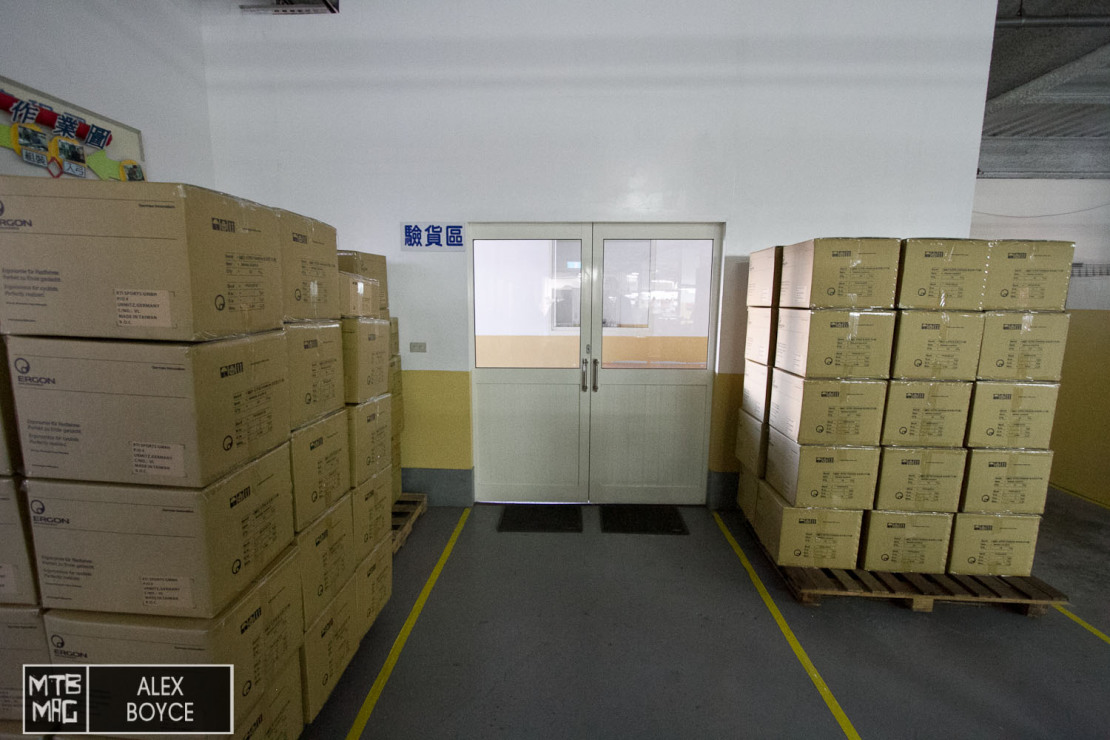
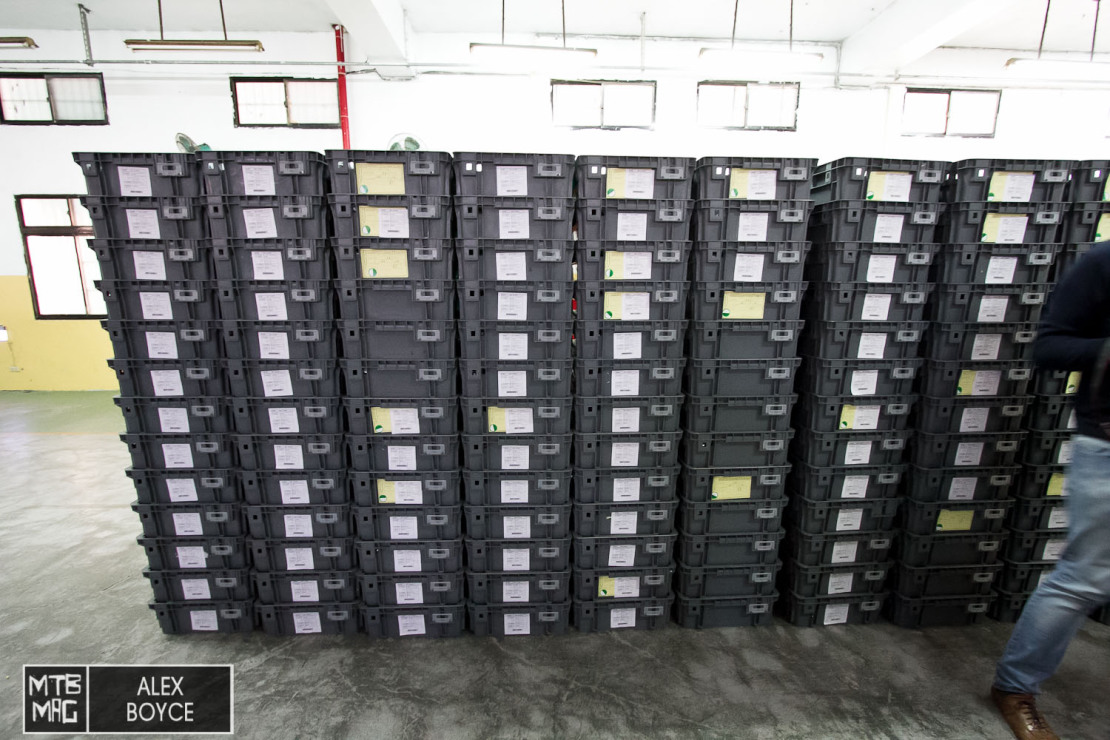
Products
Velo showed us a range of features they have been developing for various markets in their product room after we finished the tour. We saw a few interesting features that will find their way onto production bikes soon.
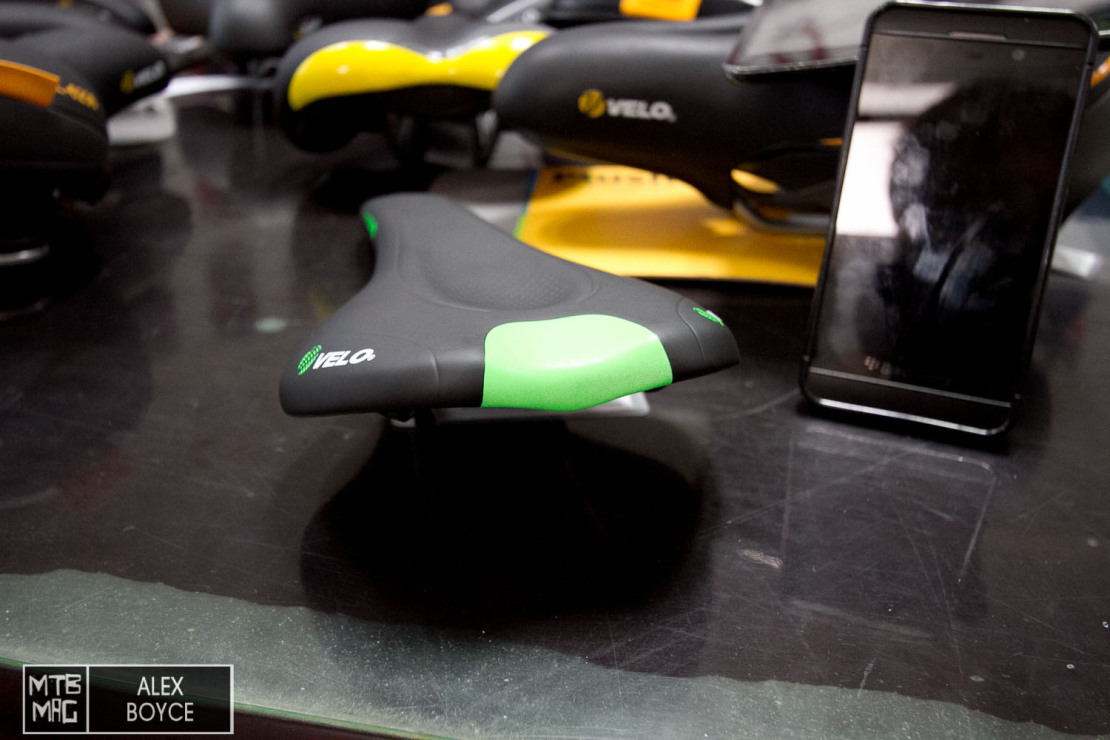
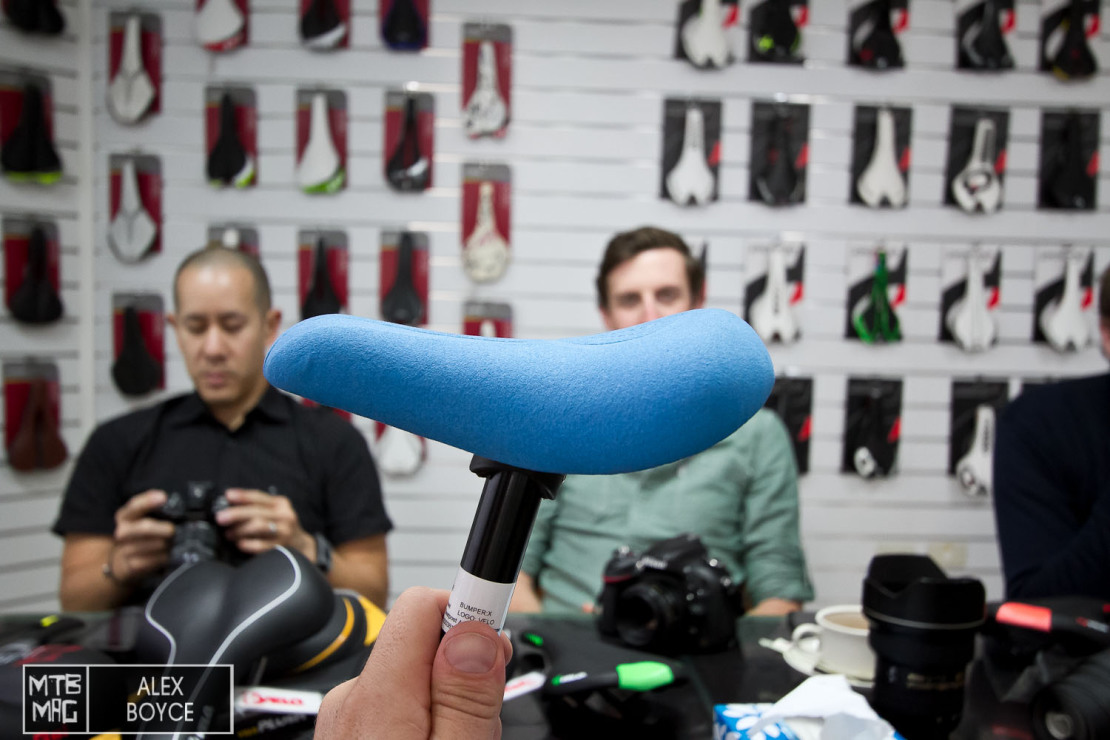
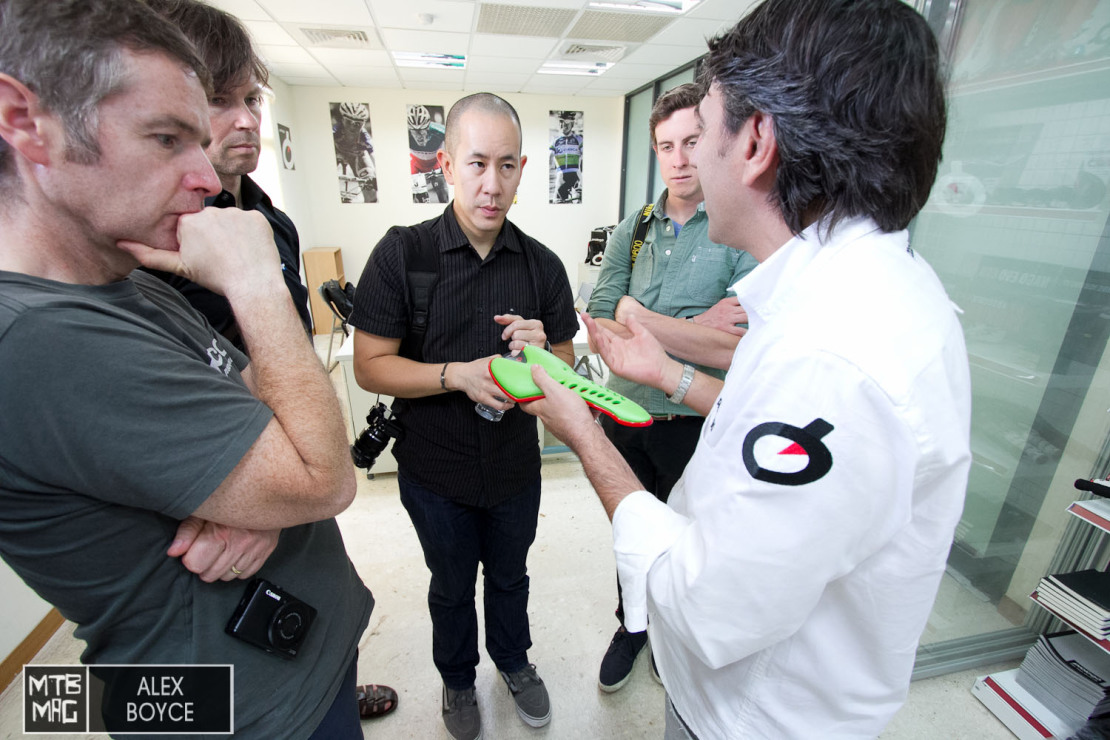
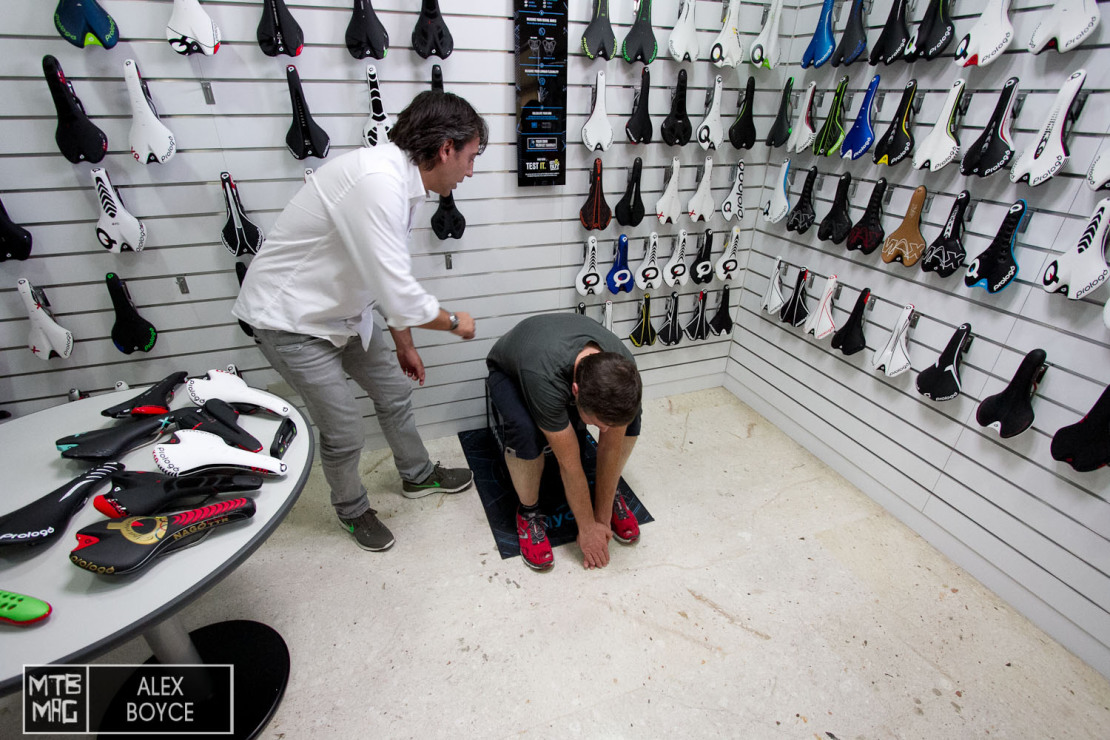
A Few Facts
The tours that day also allowed us to speak to the workers and we were able to ask about working condition’s and pay. Apparently workers work an average of 5 1/2 days a week depending on their role and are paid between 1200 up 2000 US dollars a month gross. The average time workers have been with the company is 5 to 10 years. The jobs are very sort after. All workers get lunch breaks and their lunch is included as part of their benefits, some have the option to live on site. Workers are from Taiwan and many other Asian countries. Velo produces about 80 percent of the high end saddle market, although numbers weren’t that specific about 1.5 million saddles are made every month.
Thanks kindly to the Staff at Velo for showing us around.