Orange Bikes è un’azienda di Halifax, West Yorkshire nel nord del Regno Unito e costruisce biciclette dal 1988.
La casa è nata come un’attività collaterale di un’altra azienda, anch’essa operante nella lavorazione del metallo. Col passare del tempo però Orange è diventato un marchio autonomo tutto focalizzato nella produzione di biciclette.
Negli anni, Orange ha legato il proprio nome a quello di rider importanti, primo fra tutti quello di Steve Peat, che su bici Orange ha corso in coppa del mondo vincendo diverse gare. Più avanti Steve ha lasciato Orange che, pur restando una piccola casa, si era ormai guadagnata l’affetto di un buon gruppo di appassionati, amanti dello stile unico di queste biciclette.
Orange è anche un marchio più unico che raro se si considera che produce tutte le bici nel Regno Unito, ed imparticolare produce da sola i telai. E’ per questo che abbiamo deciso di organizzarci e di andare a visitarla, per vedere come sono fatti i telai e come nasce la nuova Five 2015.
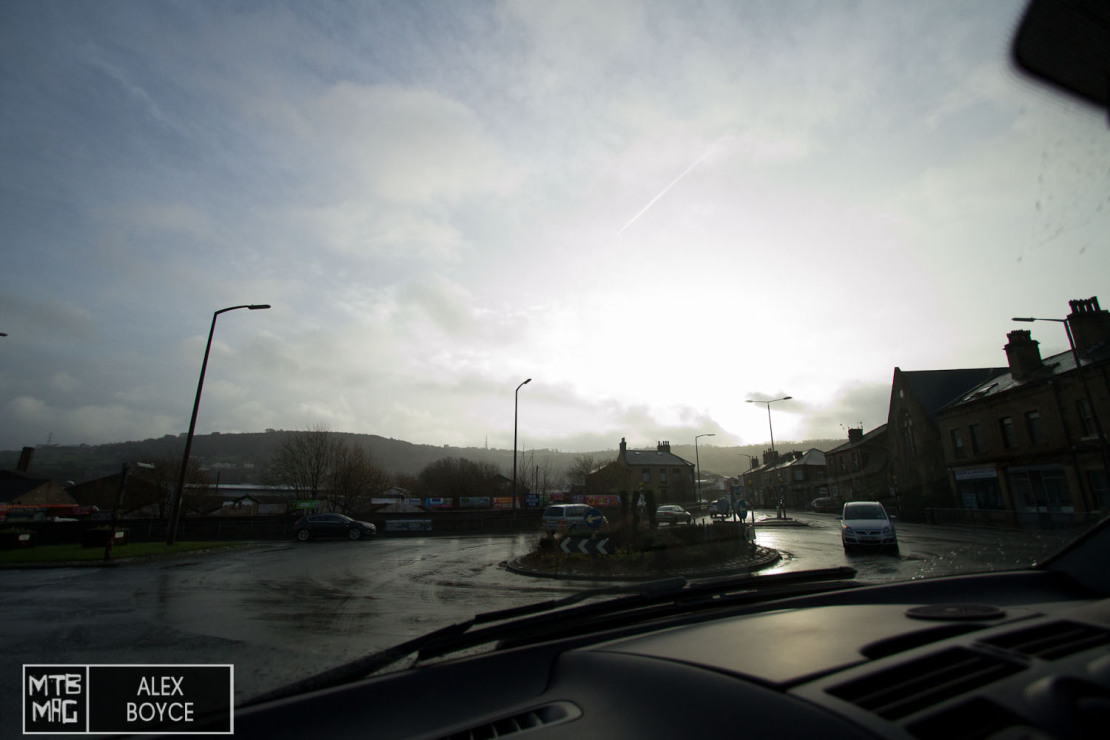
La storia
Appese ai muri ci sono un sacco di cose, comprese le bici usate dallo staff. Ma ciò che ha attirato la nostra attenzione è stata questa bici, usata da Steve Peat agli inizi della propria carriera.
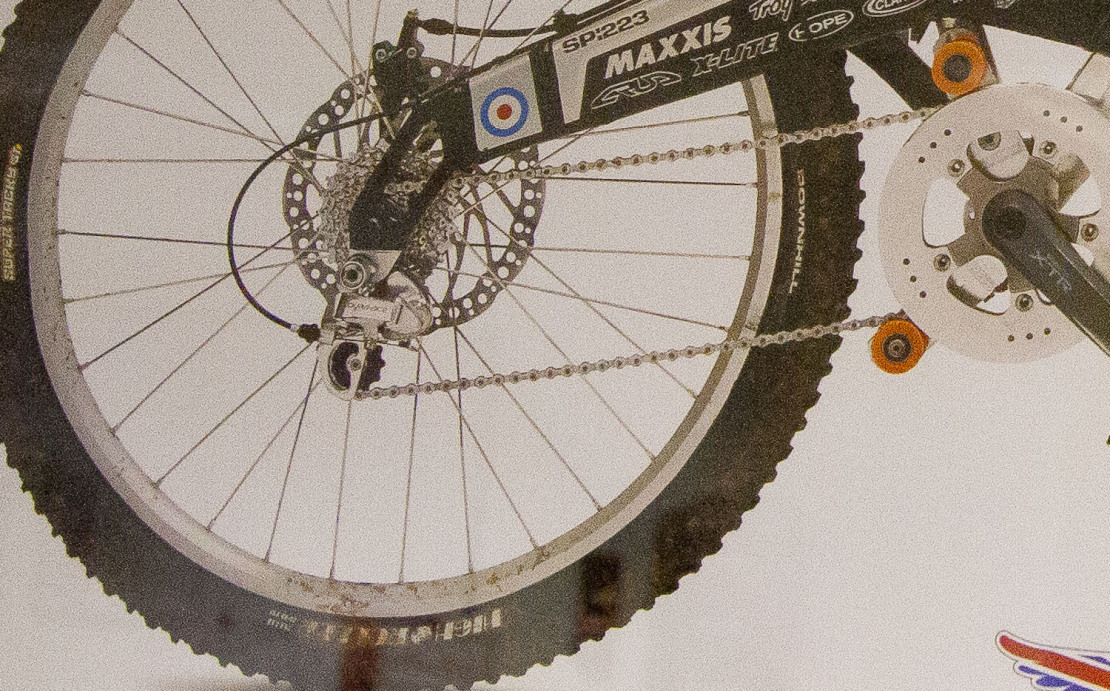
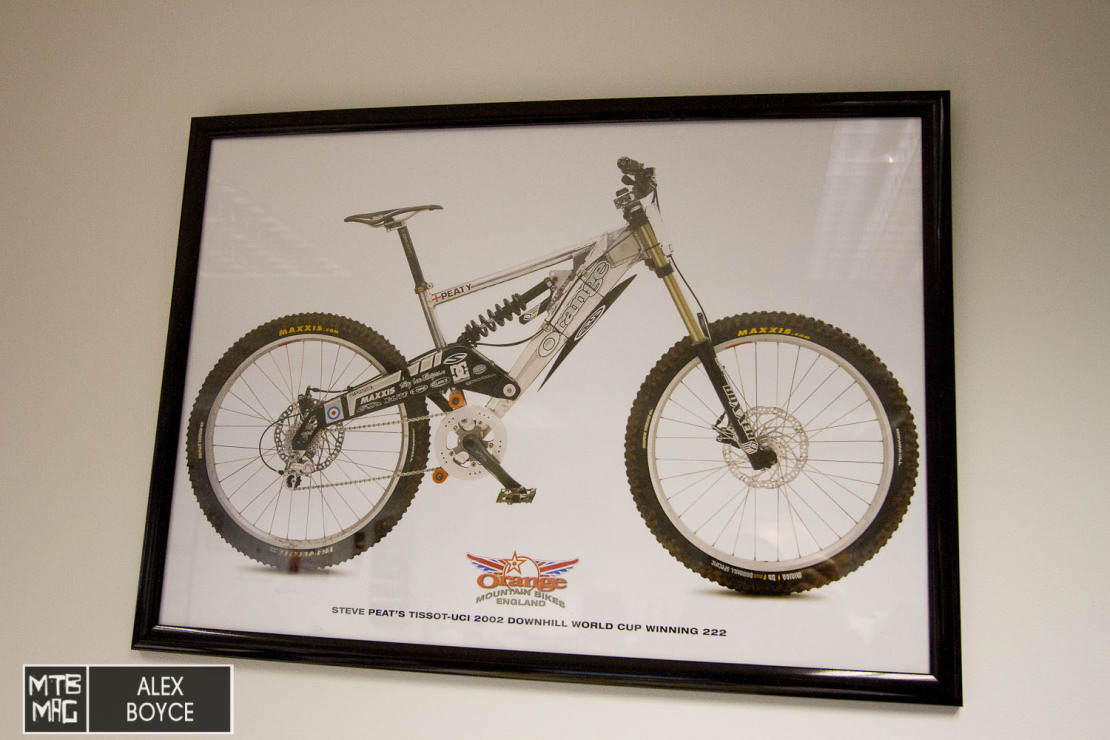
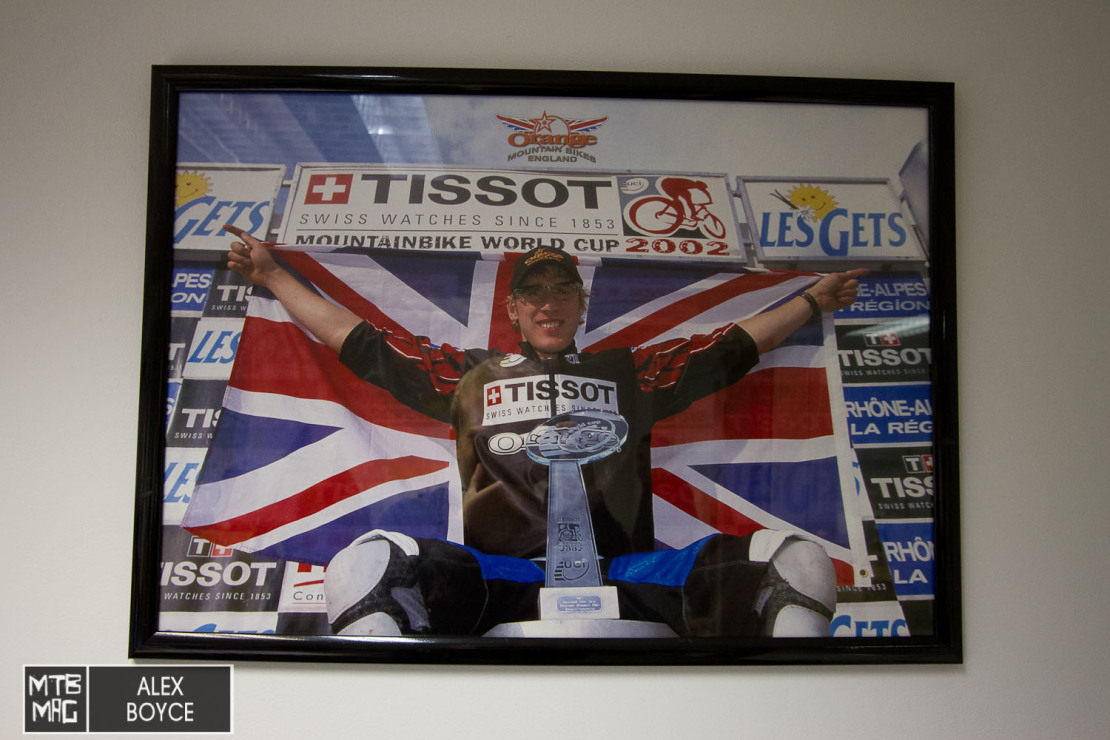
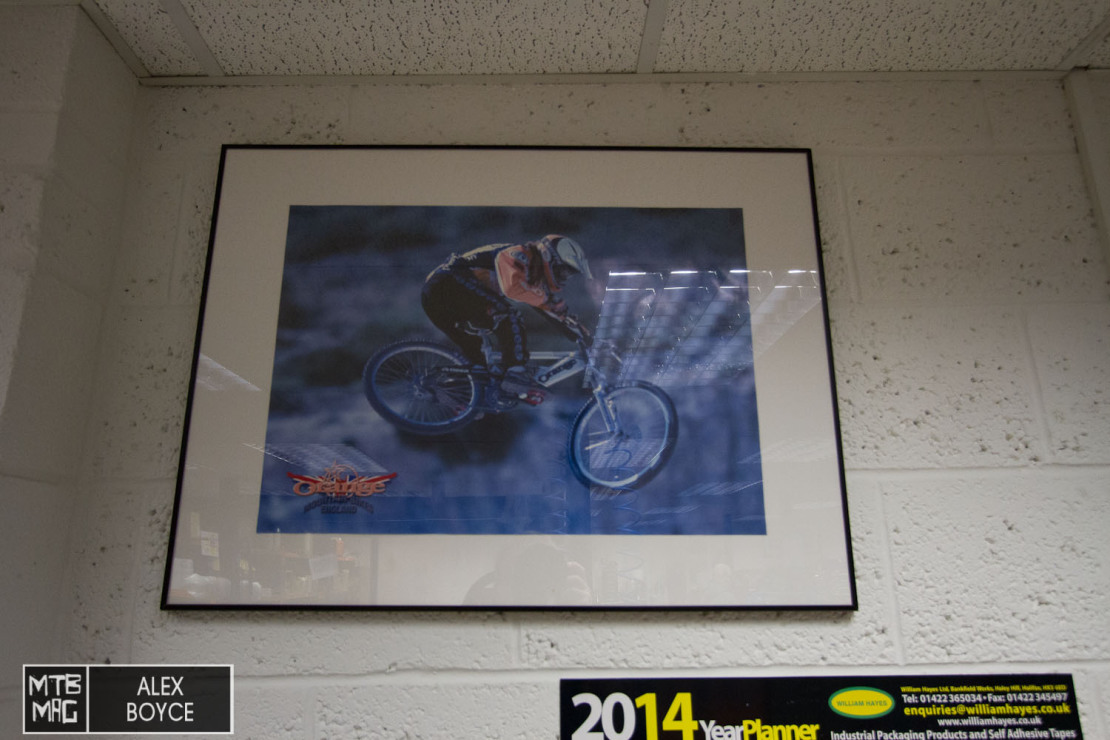
Design
Le bici Orange sono uniche, costruite saldando tubi fatti di alluminio di livello aerospaziale, che poi subisce trattamento termico per migliorarne la solidità e viene rifinito sempre nella fabbrica Orange. Sono biciclette con sospensione single pivot, a tutto vantaggio di semplicità ed affidabilità.
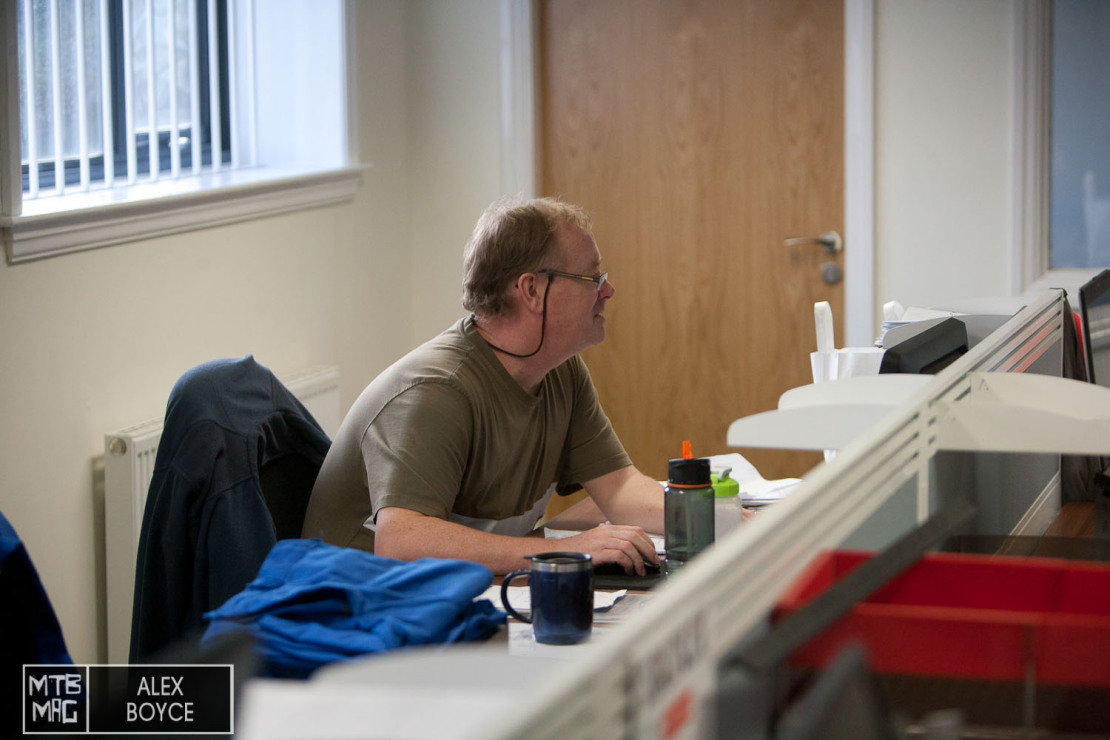
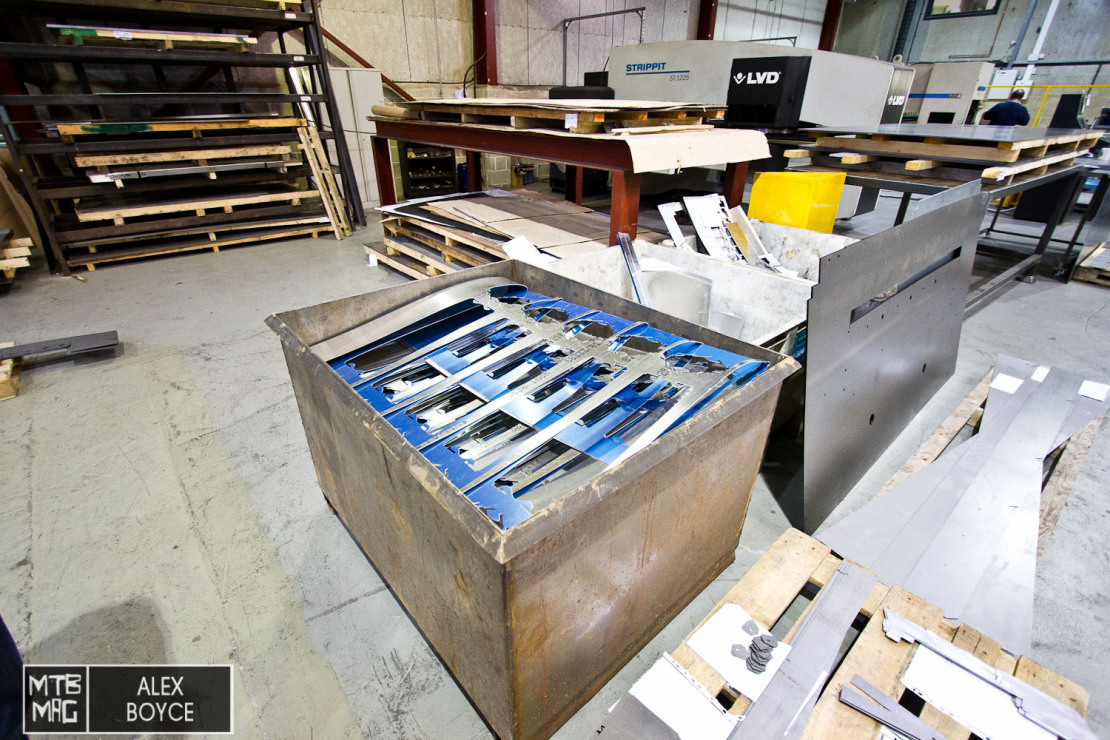
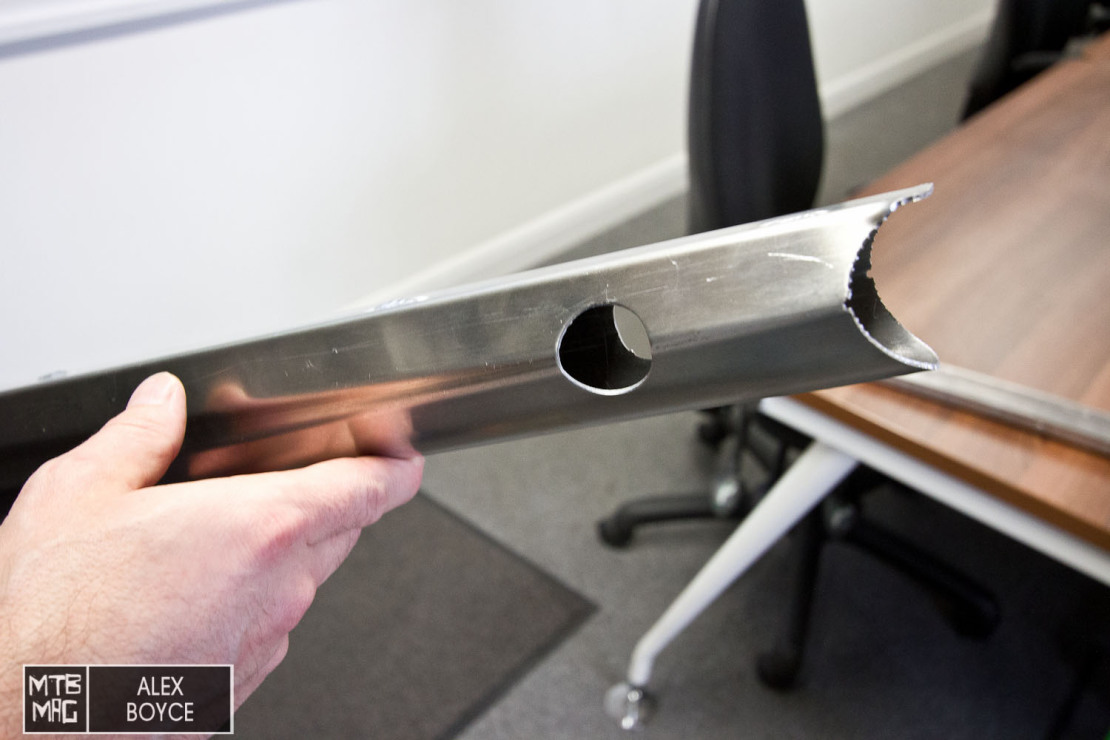
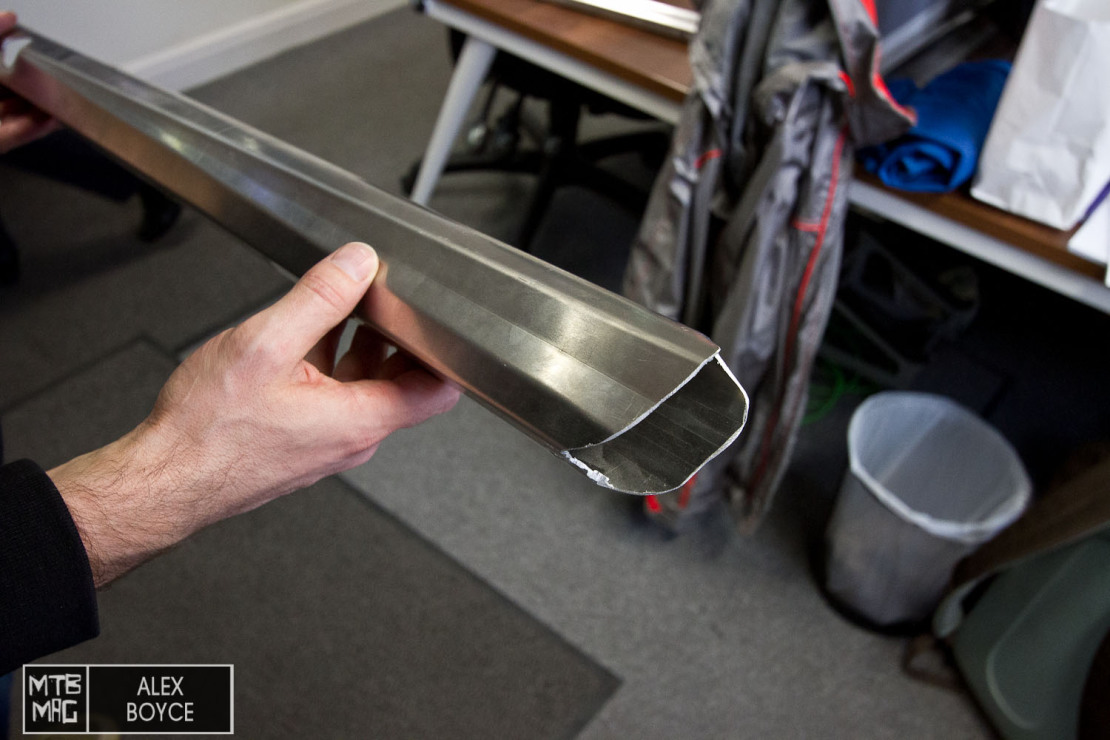
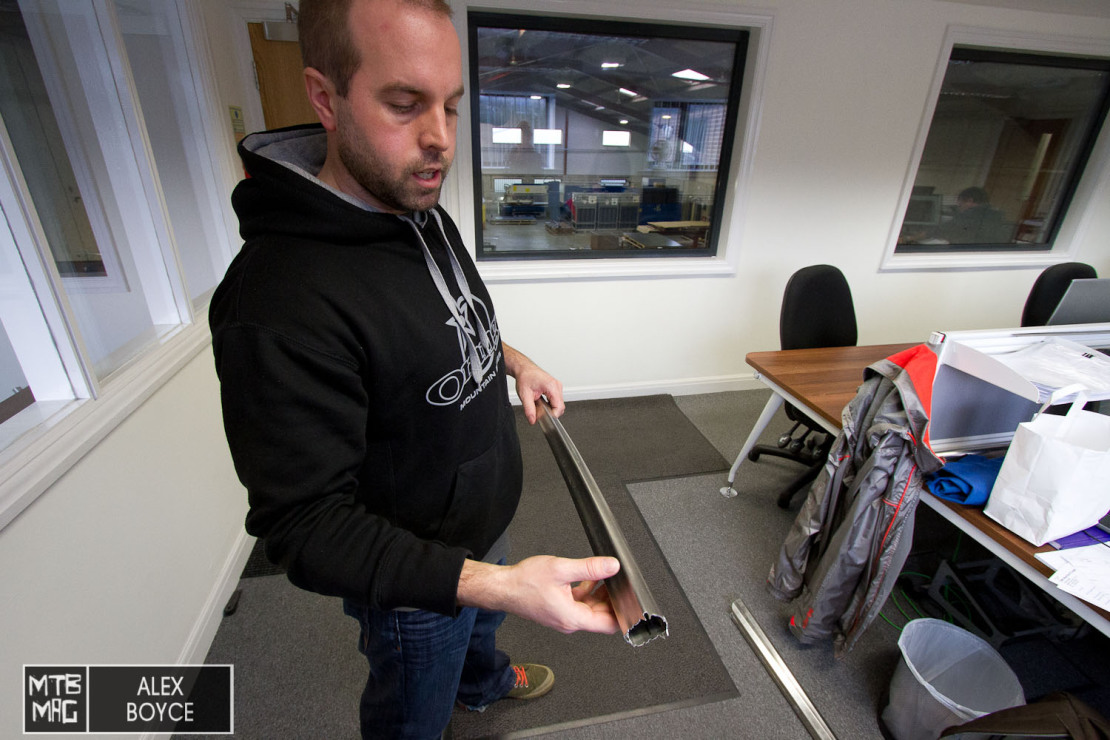
Il taglio del materiale
I tubi sono tagliati da lastre piane di metallo tramite laser. Tutto l’alluminio usato è della massima qualità: per telai solidi sono necessarie buone materie prime.
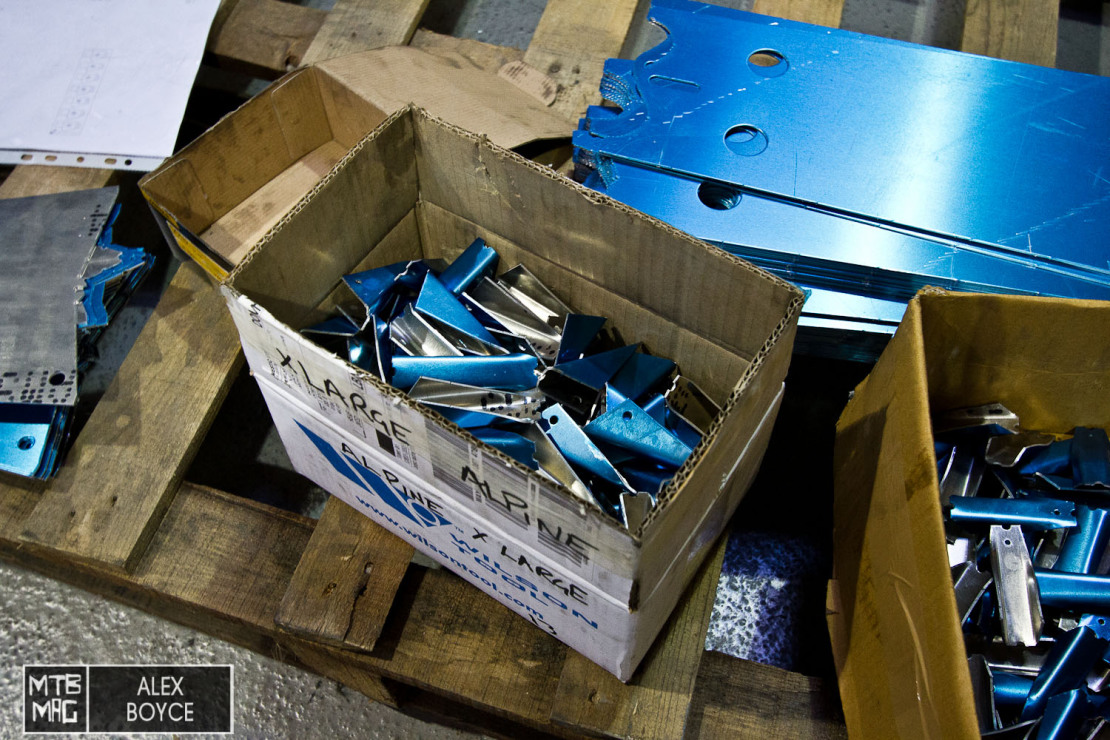


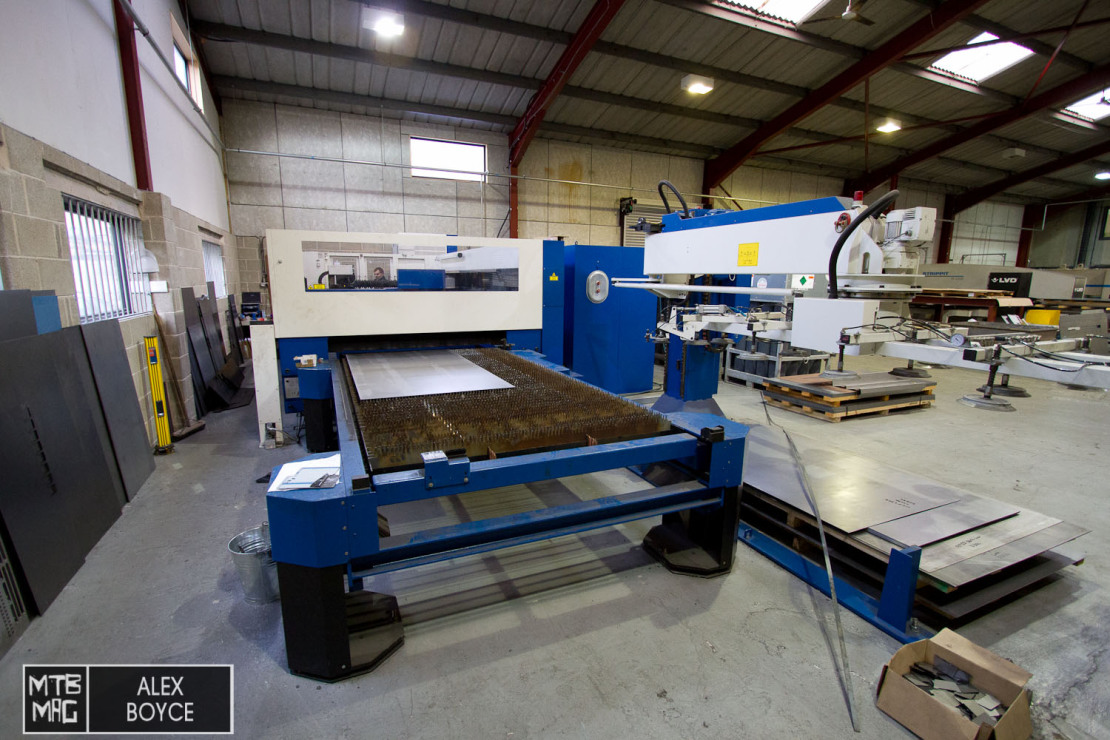
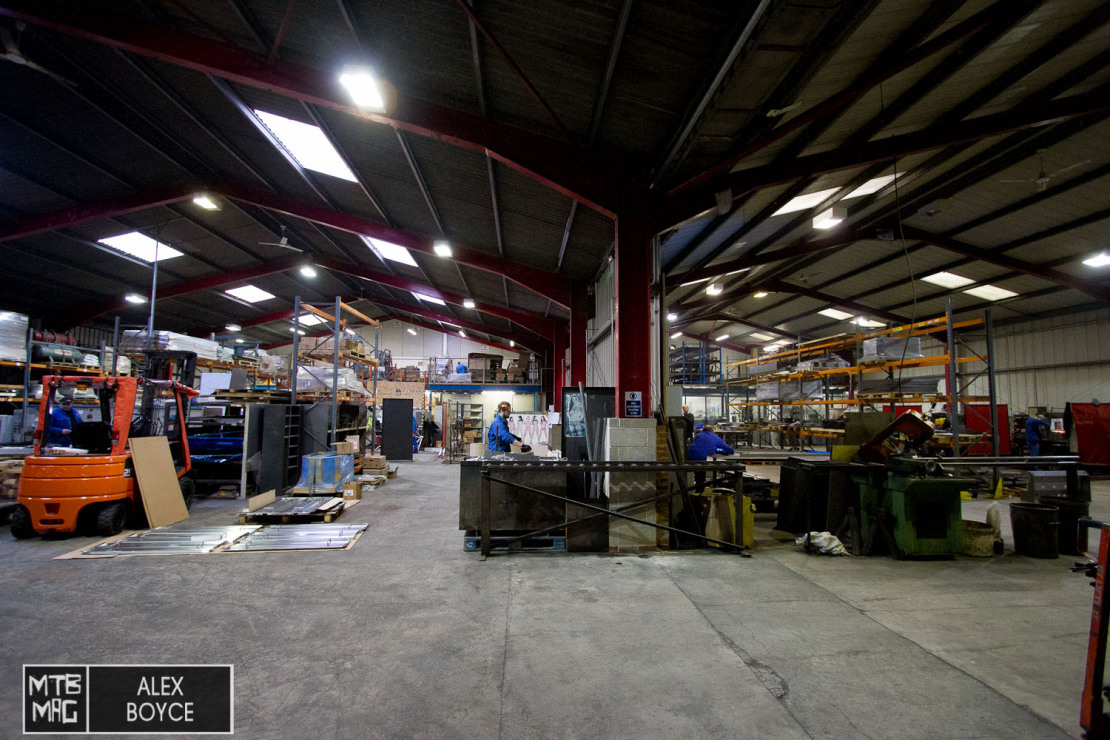
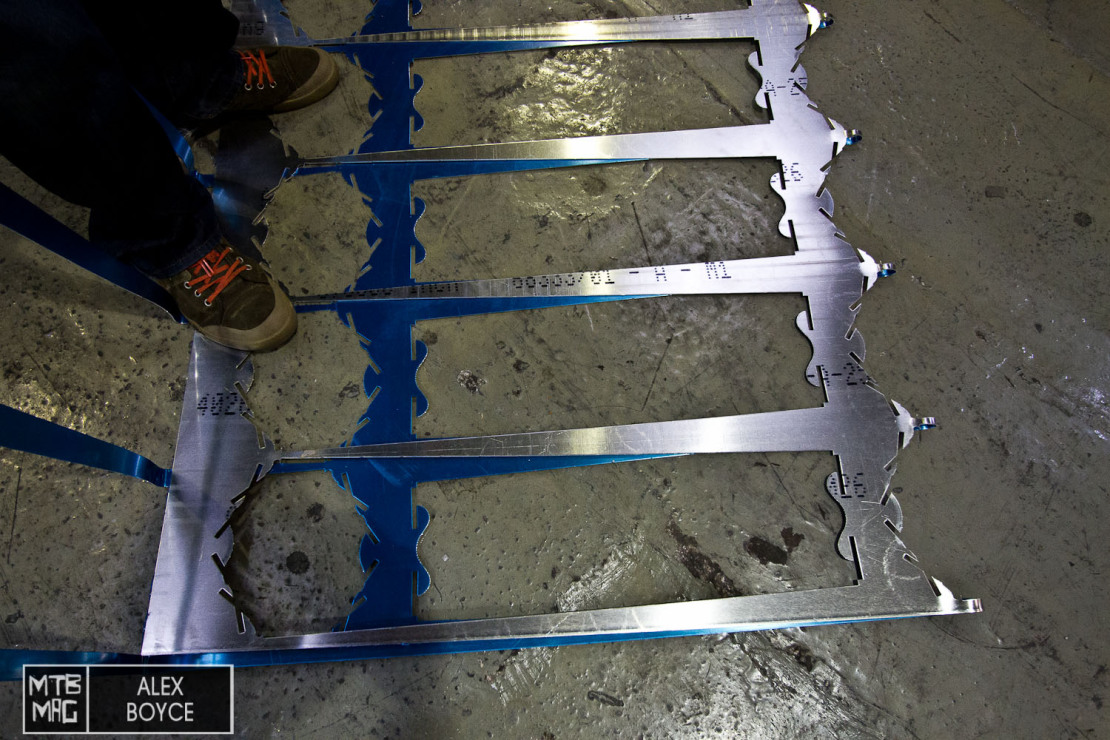
Fabbricazione dei telai
Per fare i tubi, ogni parte del telaio è piegata per dargli la forma e viene tagliata nel punto giusto per fare sì che tutti i tubi combacino bene. Più sono le pieghe nei tubi, più questi sono rigidi. Il processo richiede molto lavoro manuale, ed ogni passo richiede un operaio che curi la produzione delle parti.

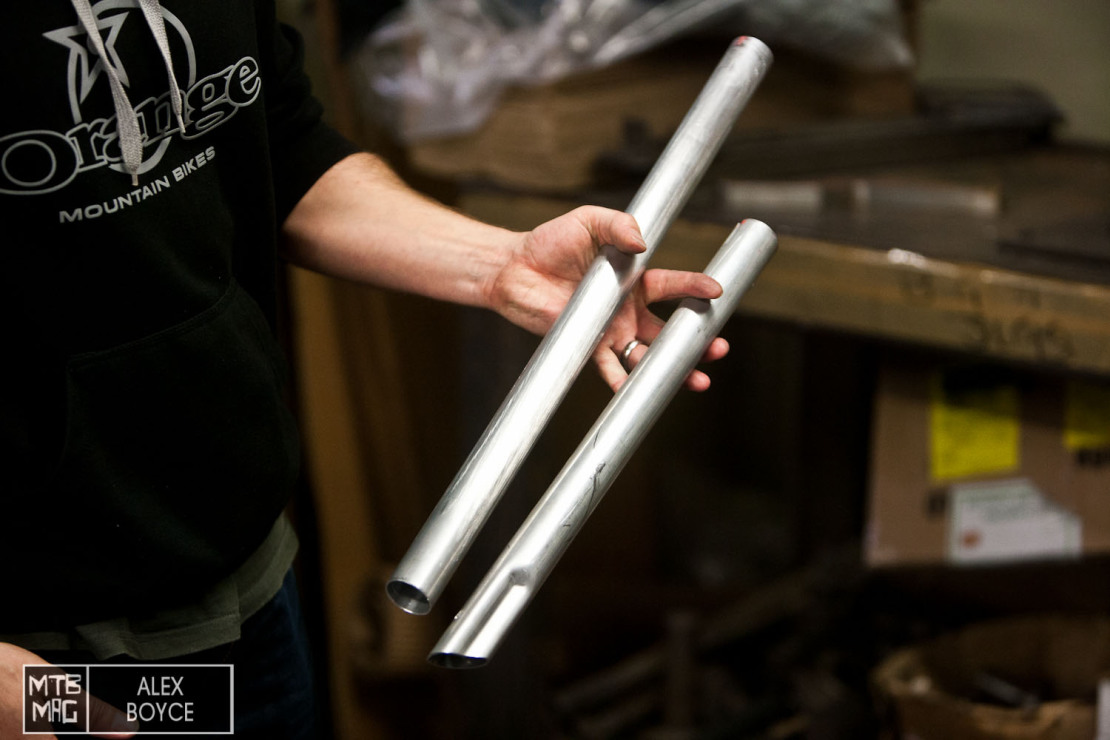
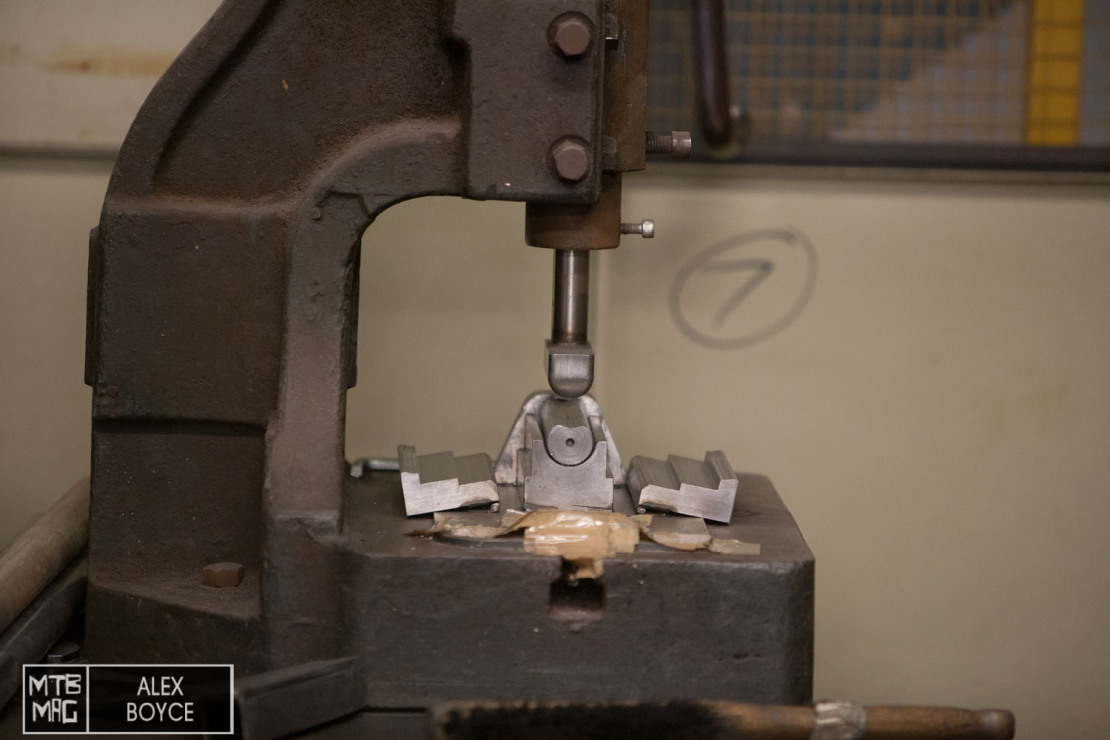
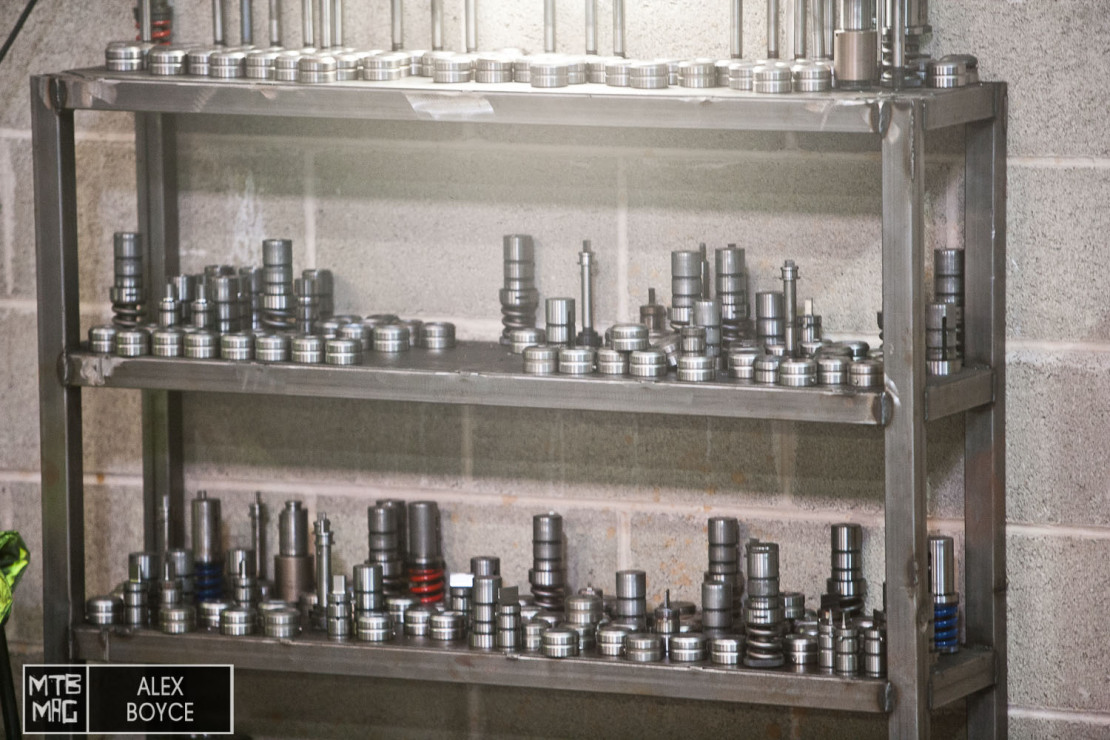

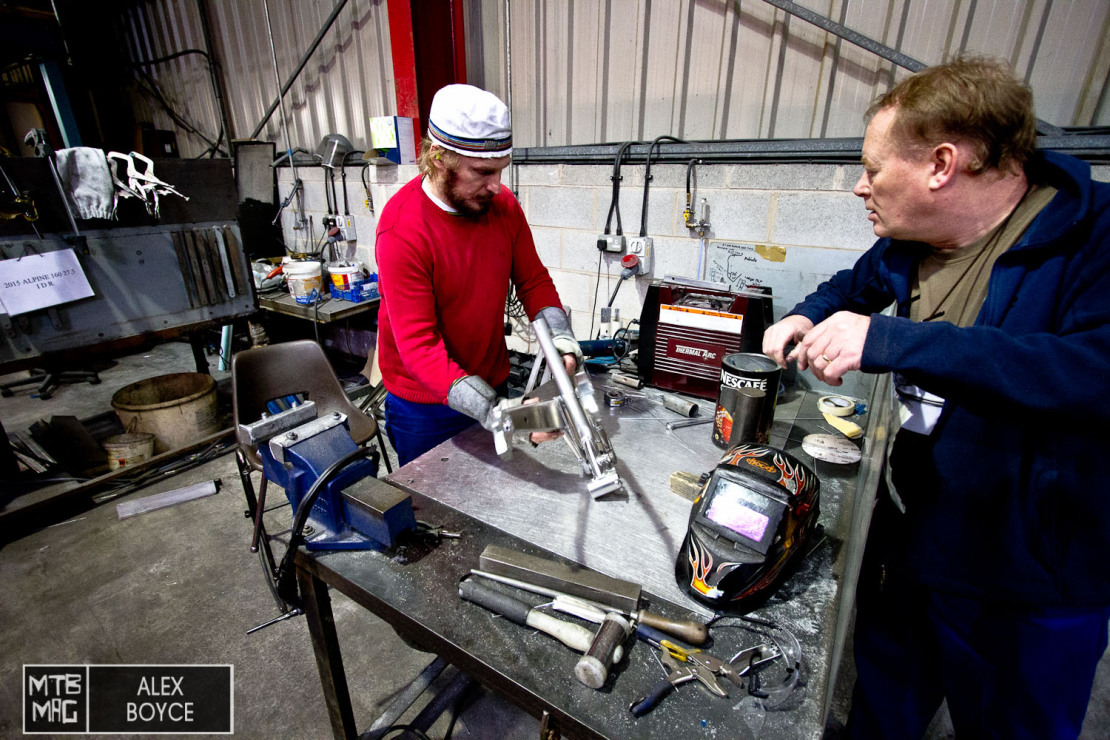
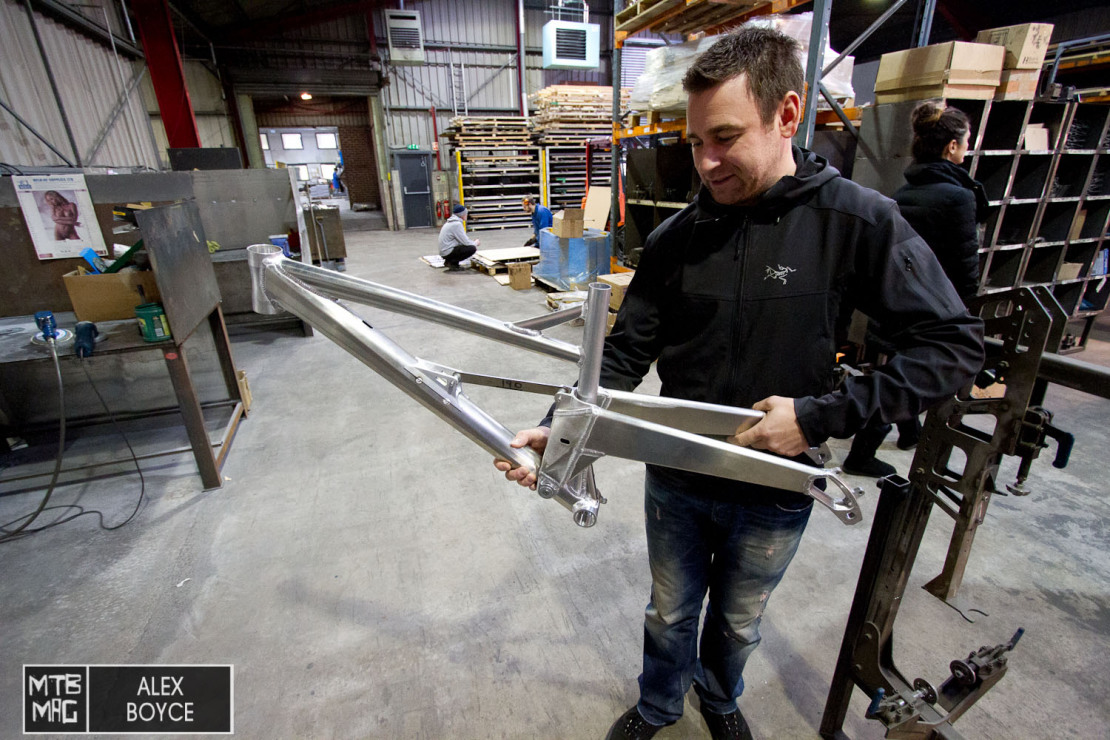
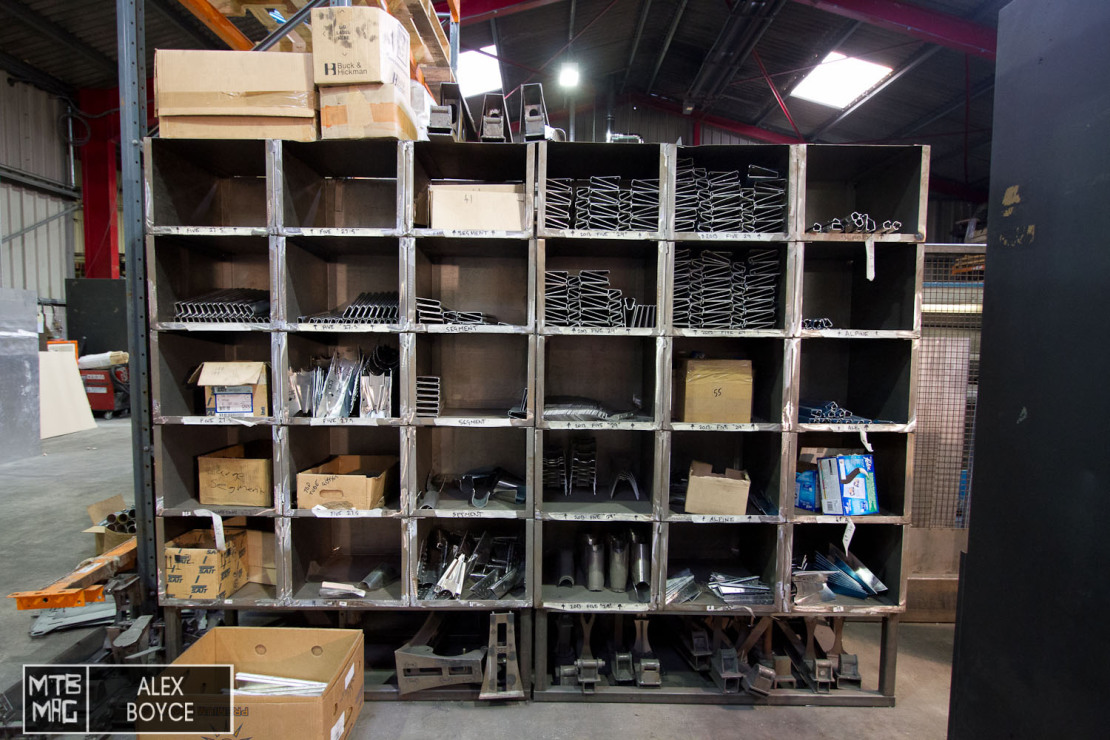

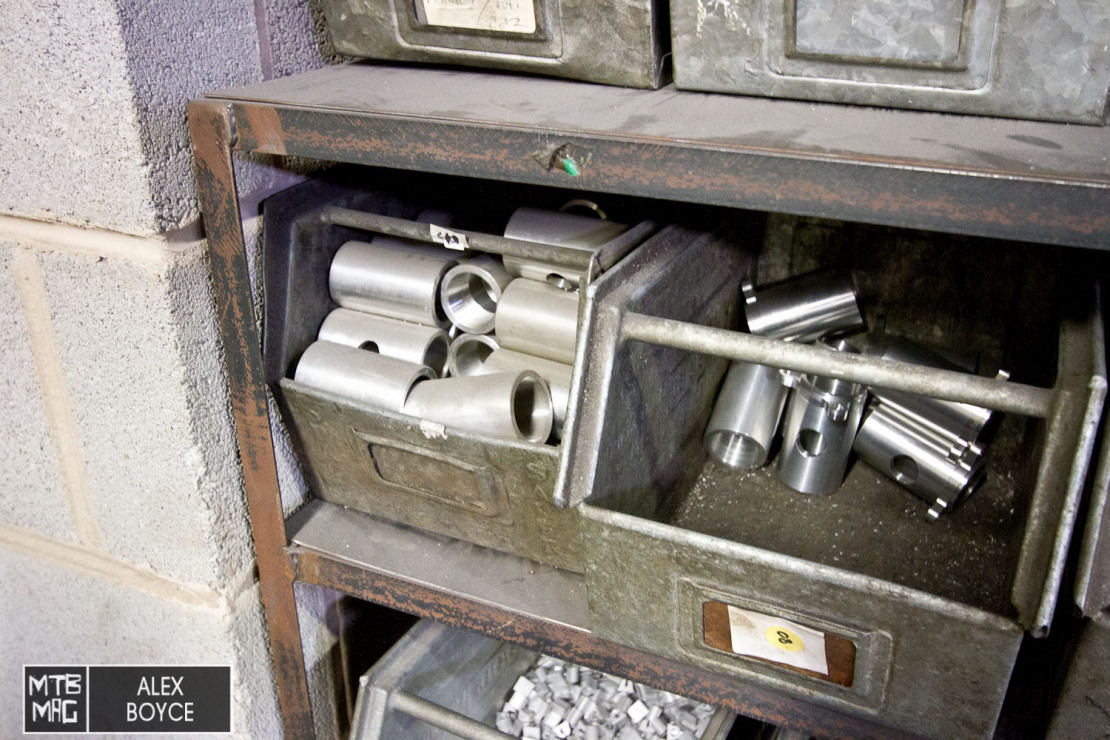
Saldatura dei telai
Le parti di metallo vengono saldate assieme, poi i telai sono sottoposti a trattamento termico per riallineare le giunzioni e consolidare il telaio. I telai vengono fatti saldando prima diverse parti che poi vengono messe assieme con l’aiuto di dime. Ogni telaio viene preso in carico da un particolare saldatore: tutti sono abilissimi e vantano anni di esperienza.

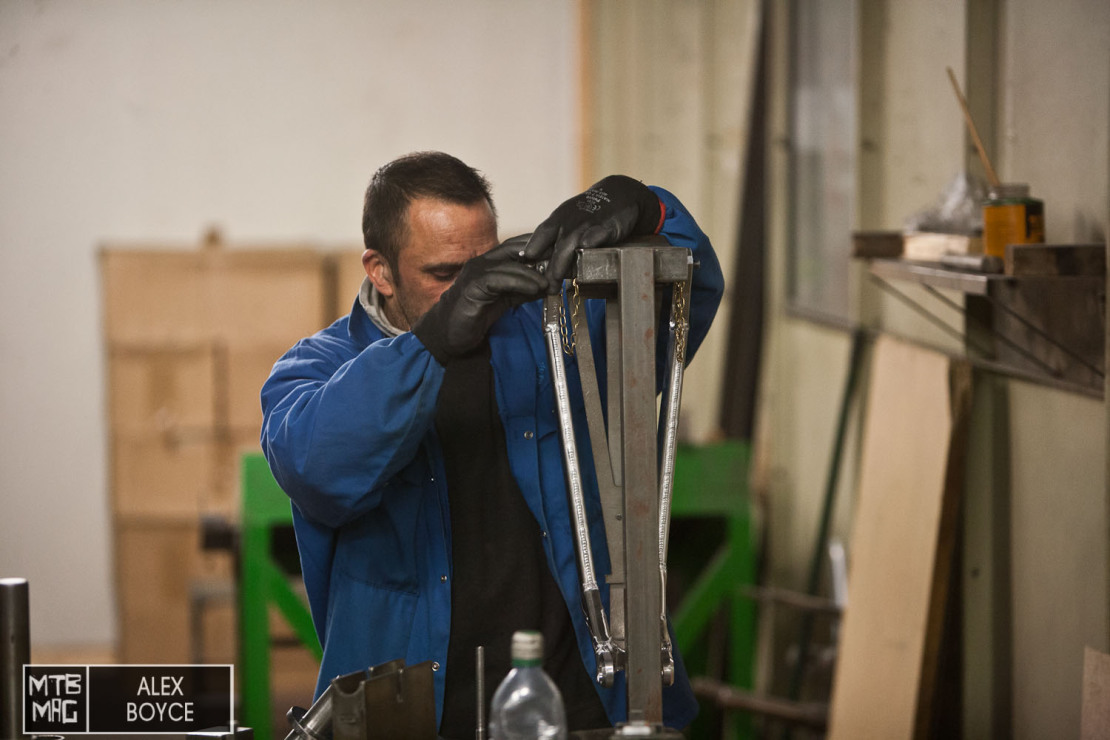
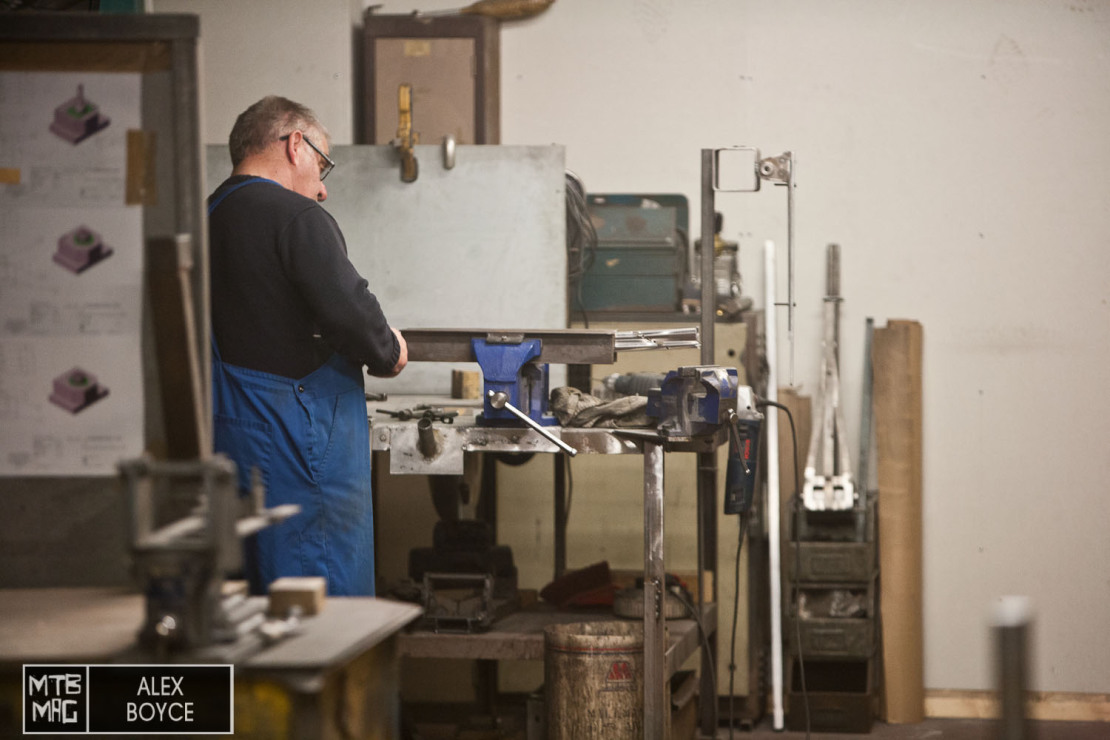
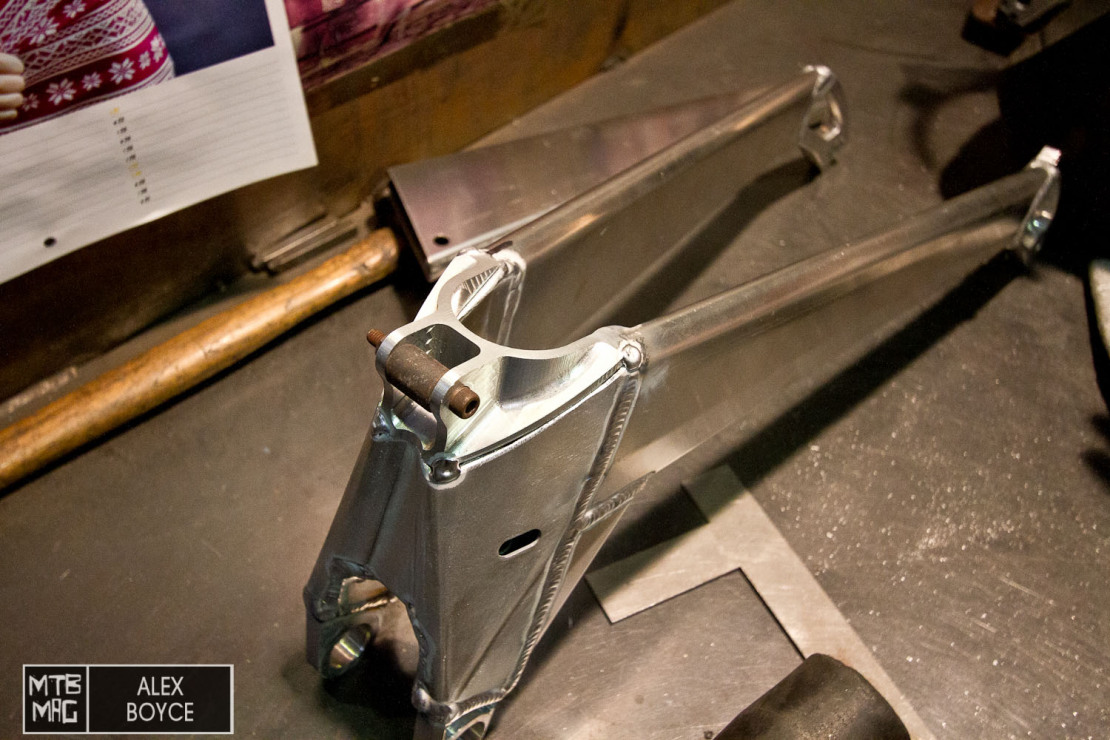
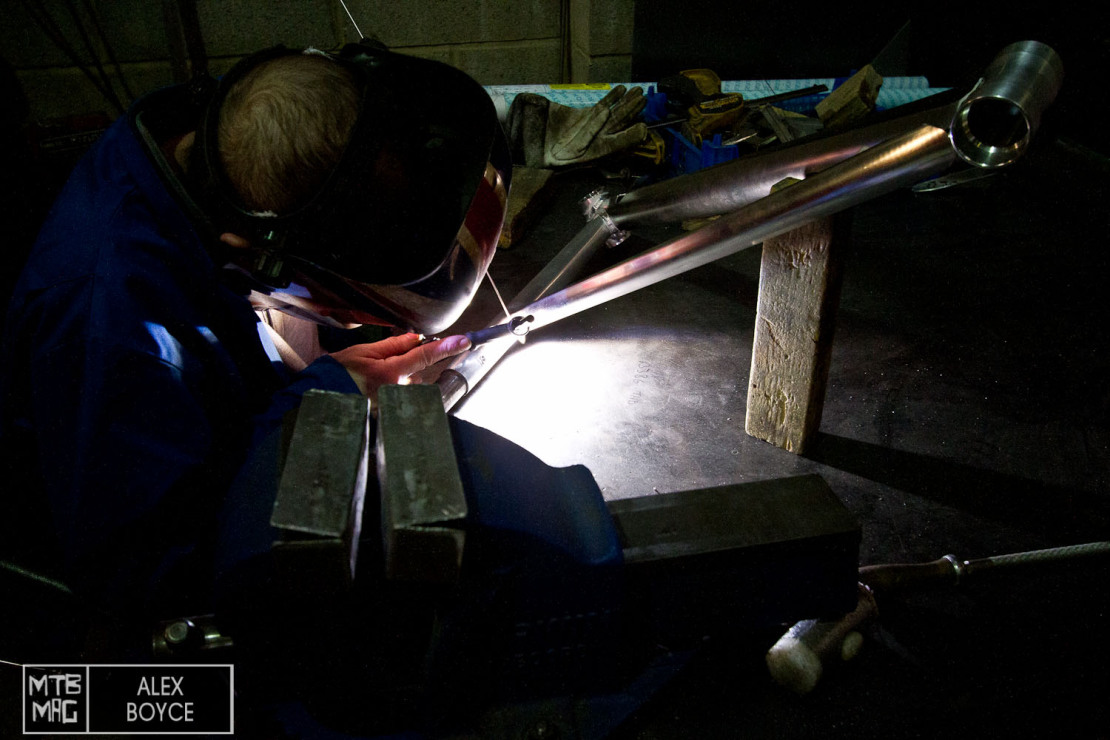

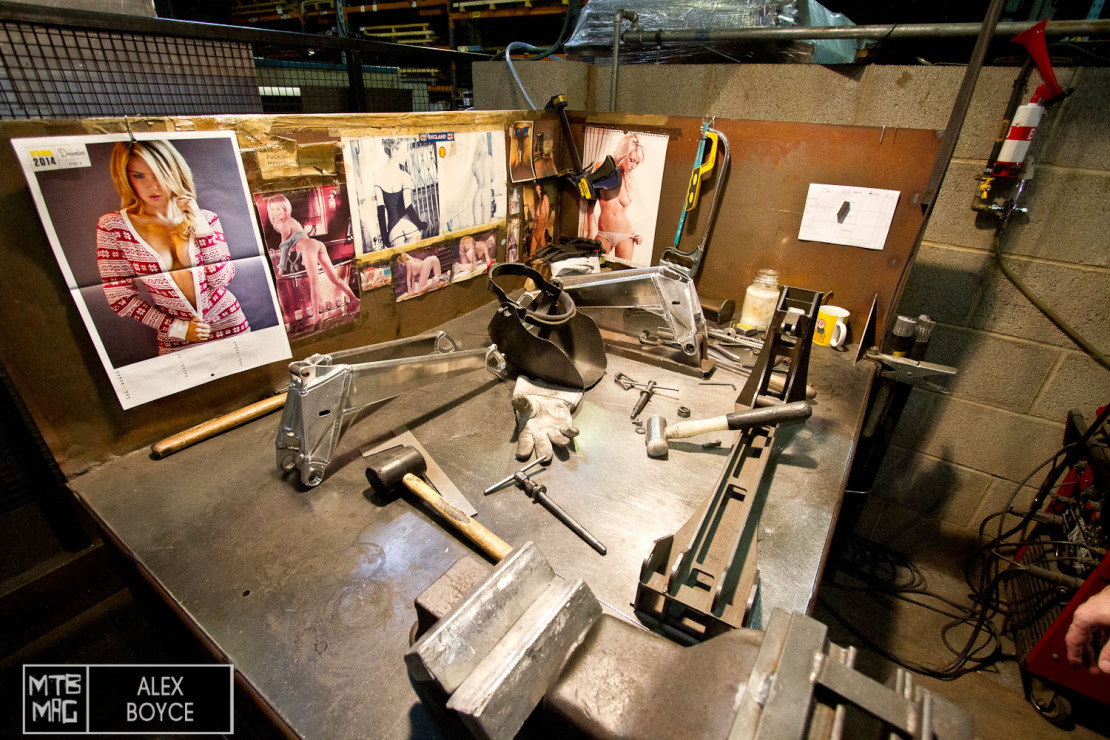
Verniciatura
Una volta saldati, i telai sono verniciati a polvere. Le verniciatura viene poi fissata in forno.
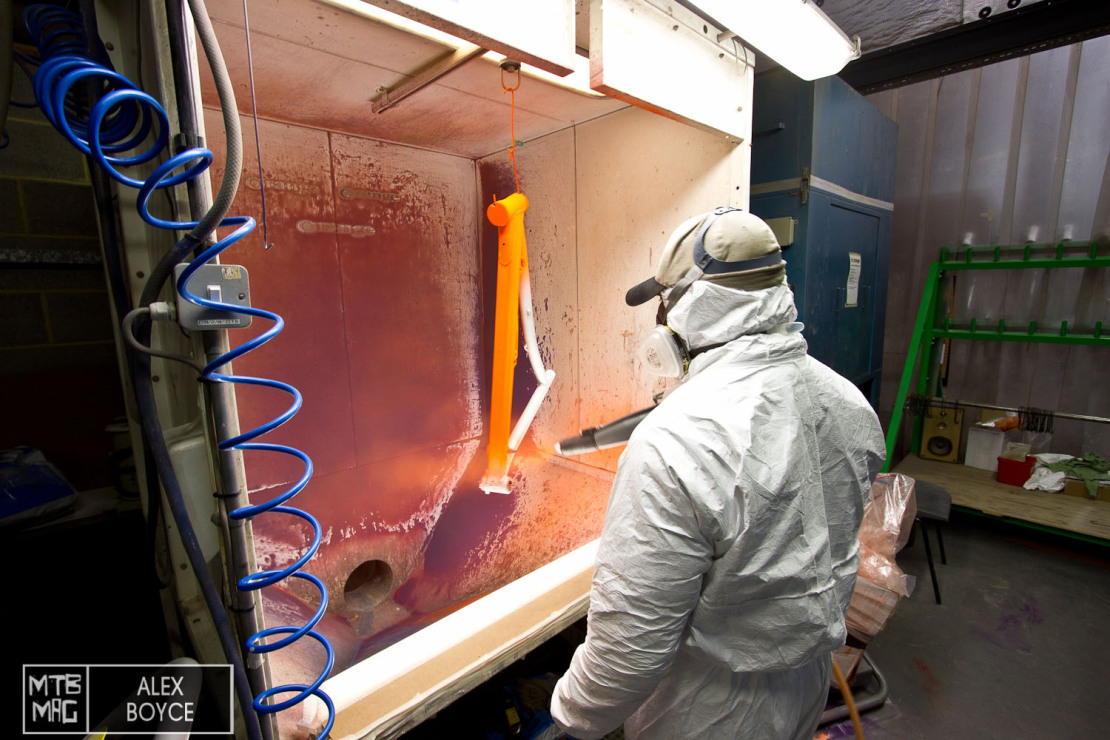
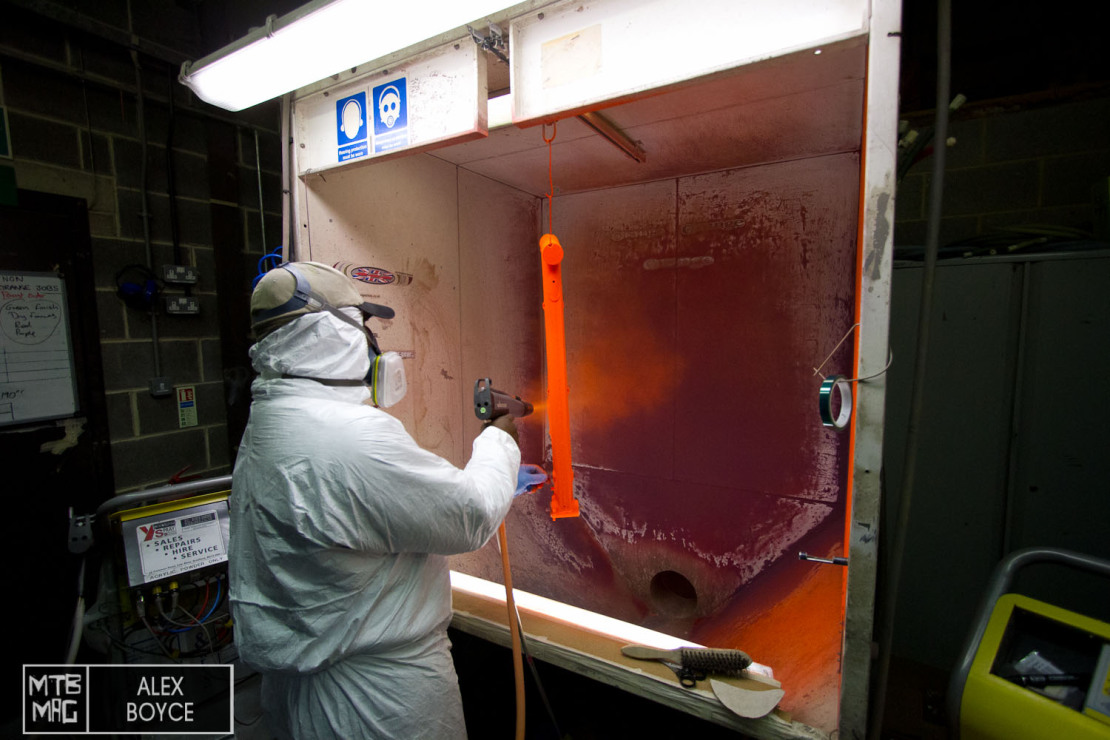

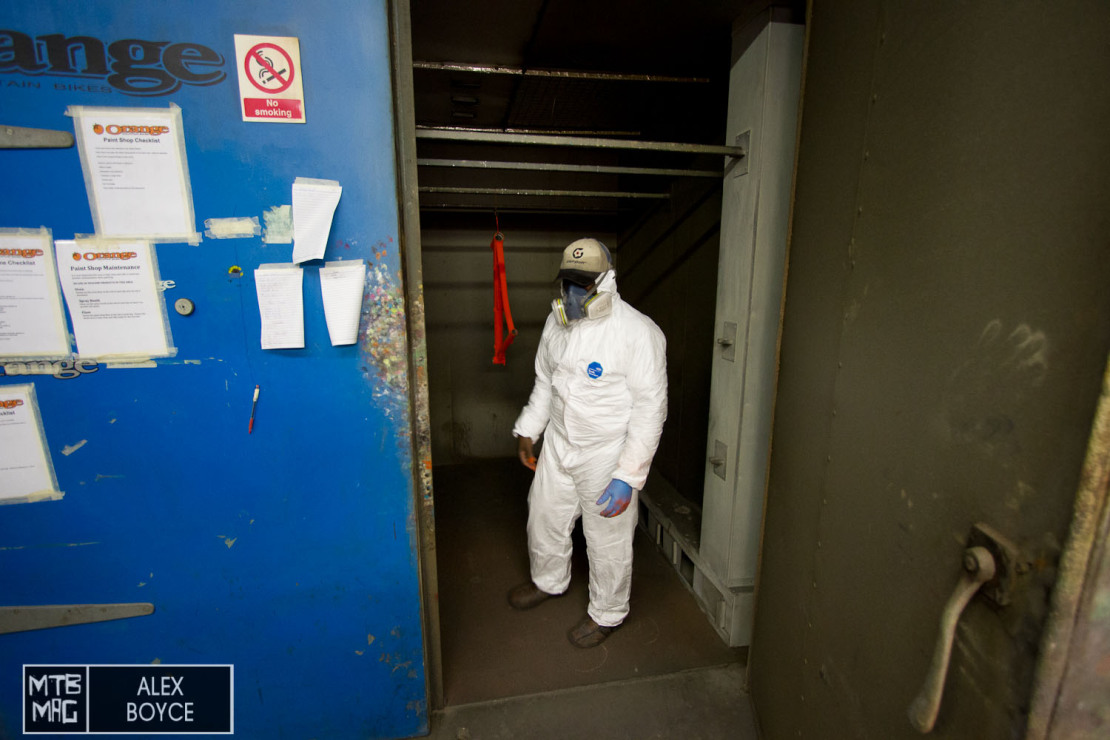
Montaggio della bici
Grazie al grande controllo che Orange ha sulla produzione, può offrire ai clienti un’enorme scelta di assemblaggi: praticamente ad ognuno viene fatta la sua bici personalizzata. Anche durante il montaggio la bici viene controllata più volte.
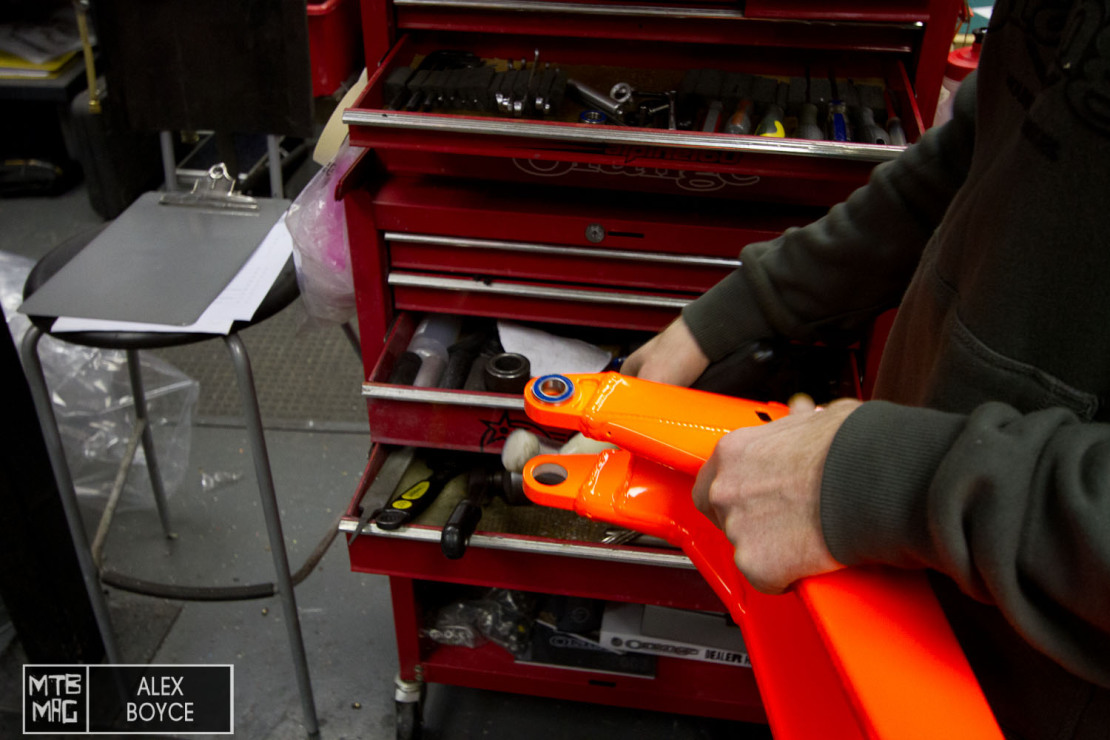
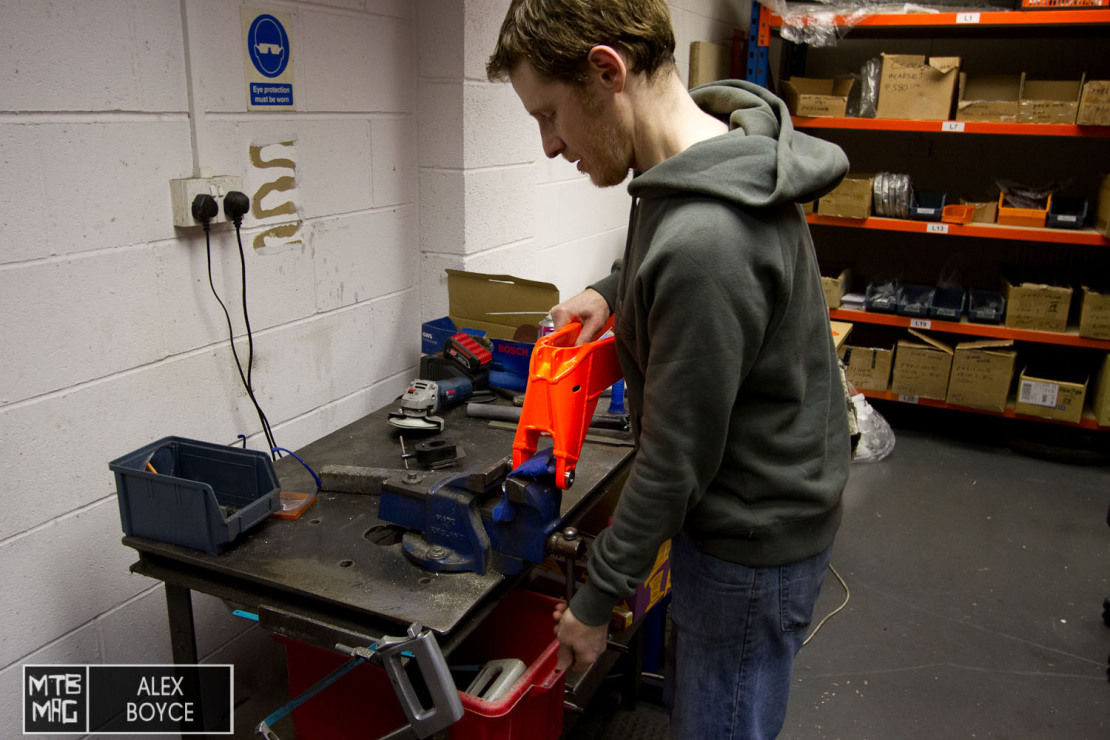
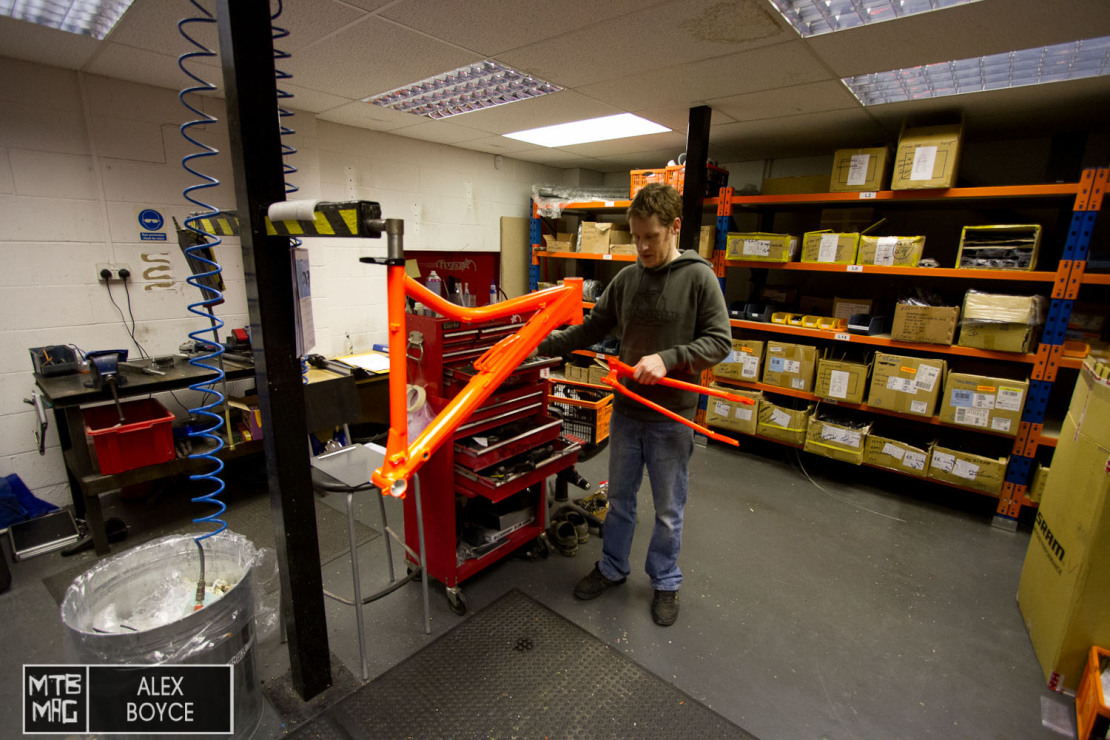
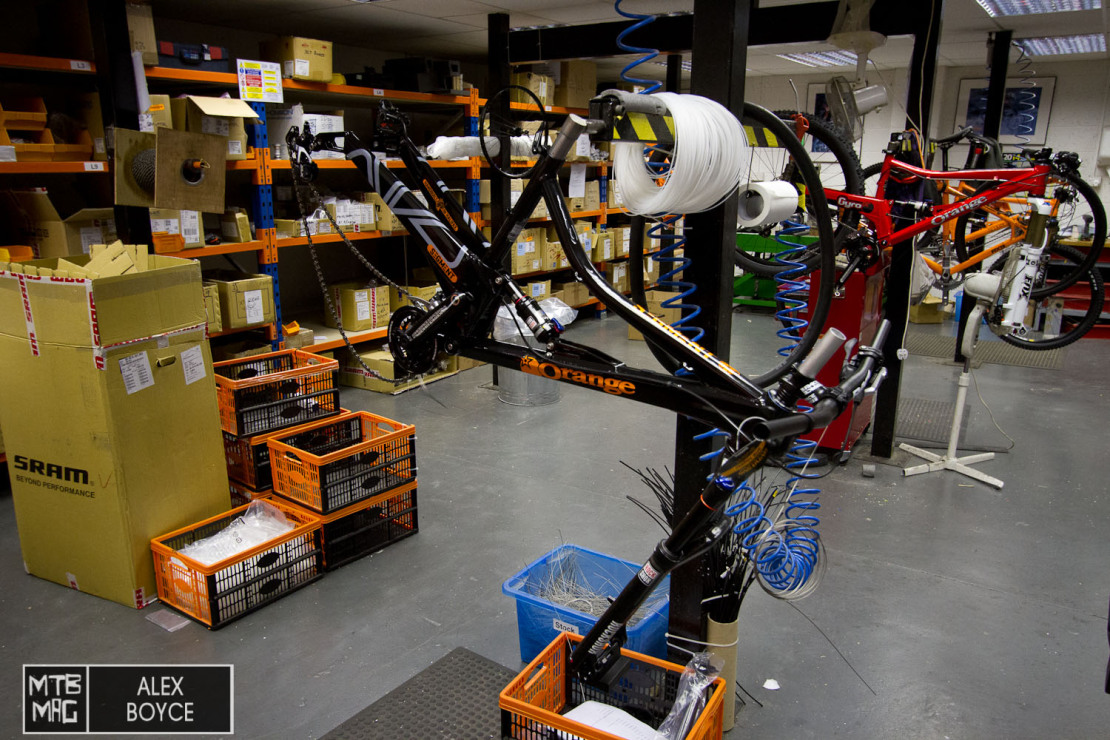
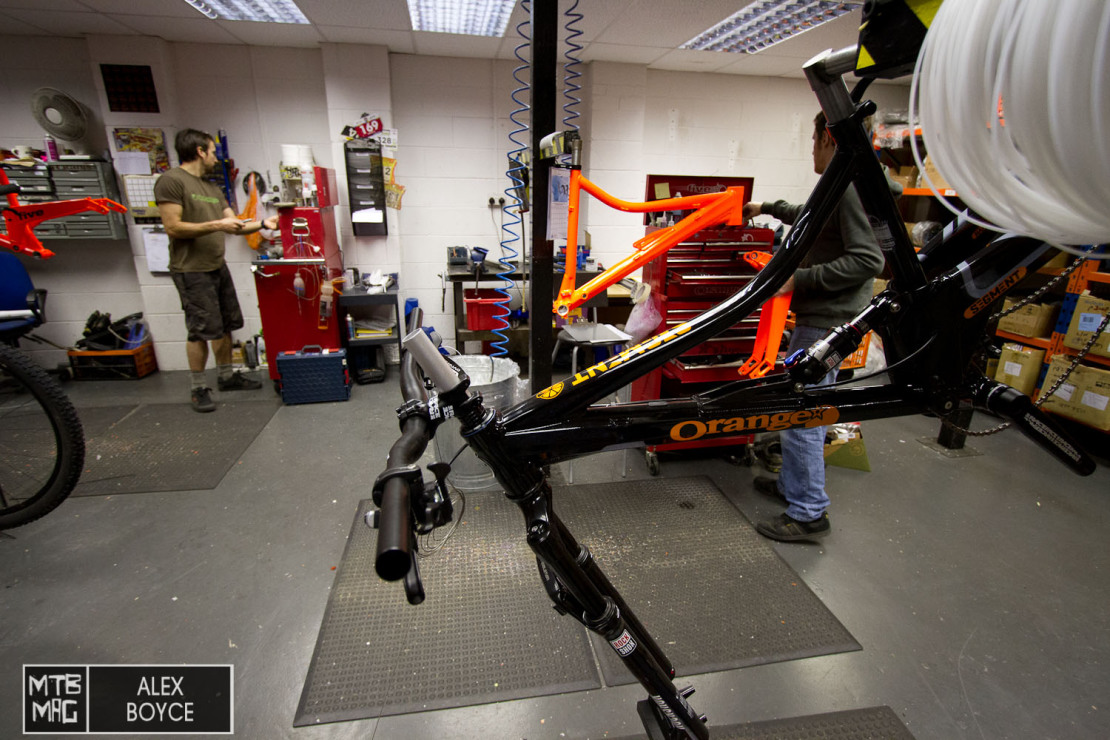
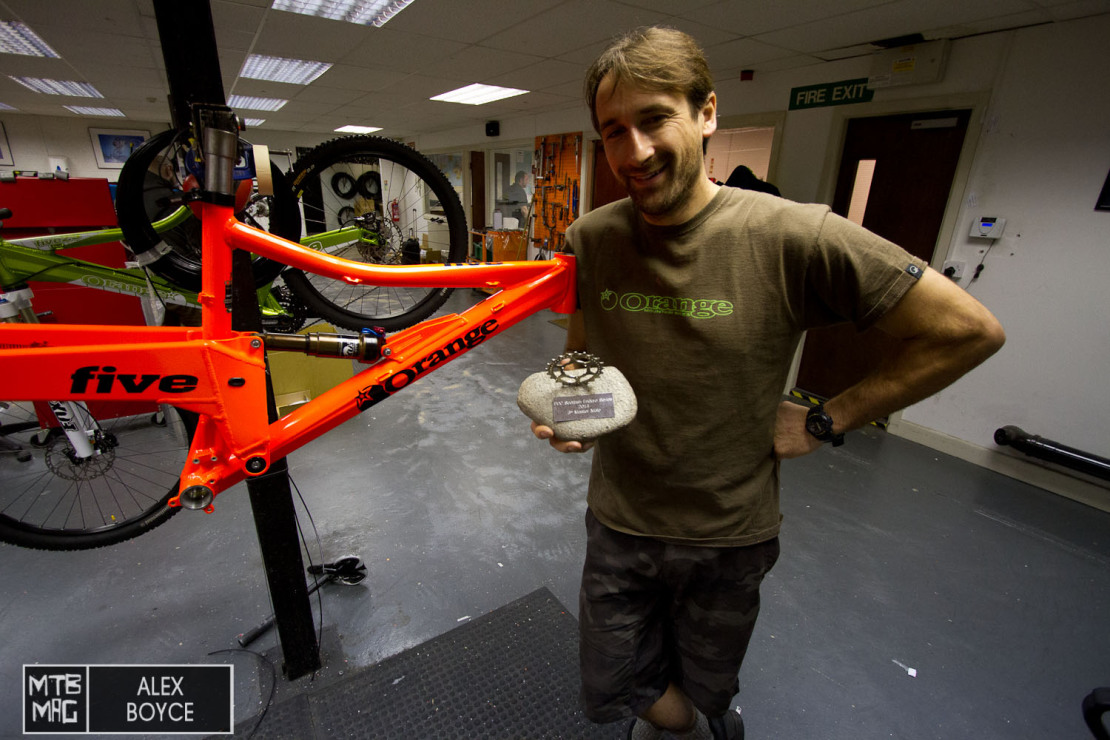
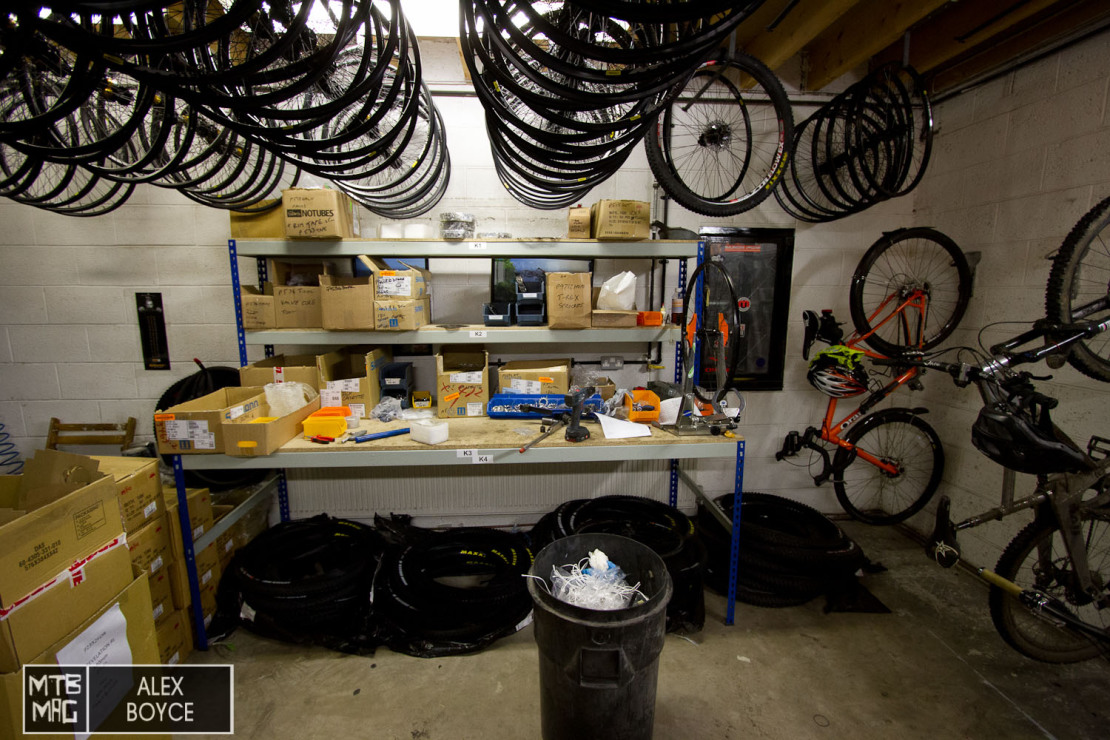
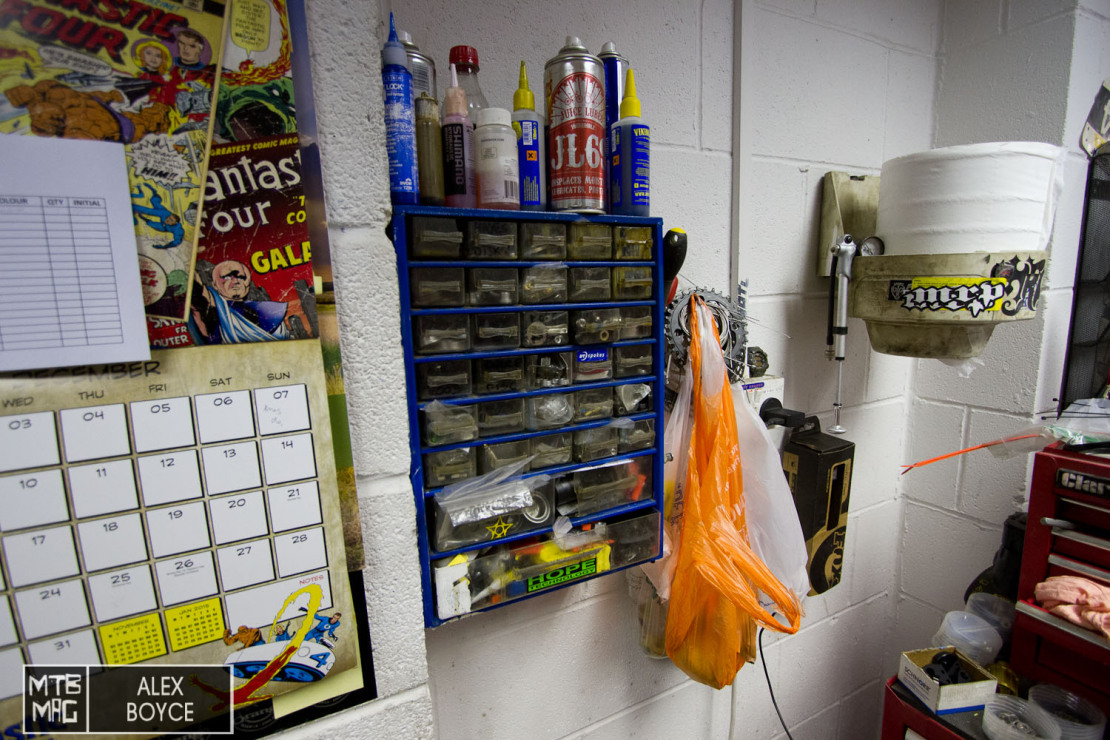
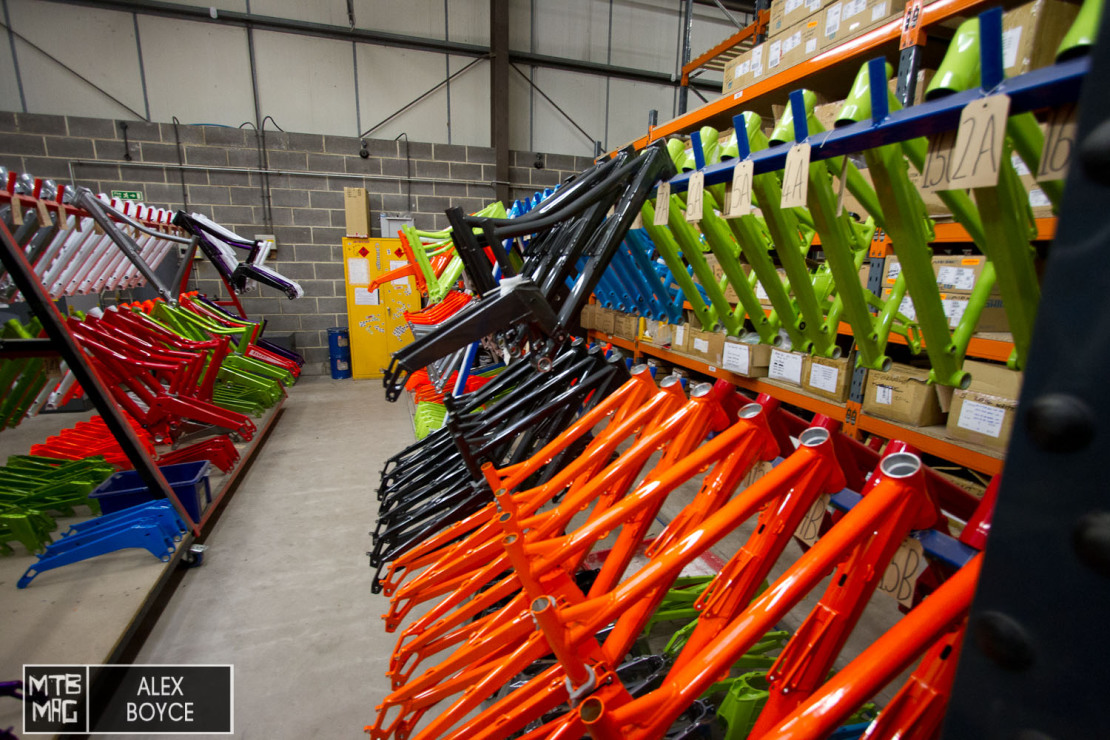
Ogni passo della produzione è seguito con attenzione e nel lungo periodo questo ha portato a solo lo 0.4% di difetti coperti dalla garanzia.
Presto avremo tra le mani una Orange Five per un test di durata, rimanete collegati!