Hope è uno dei marchi aftermarket più conosciuti ed è specializzato in mozzi, attacchi manubrio, corone, luci e freni, per dirne solo alcuni. L’obiettivo di Hope è produrre componenti di alta qualità affidabili nel tempo che durano nel tempo, rigorosamente prodotti nel Regno Unito. Ha una storia che ha le proprie radici all’inizio degli anni 90 e fin da allora ha cercato di restare coerente coi propri principi e produrre nel Regno Unito ogni piccolo componente.
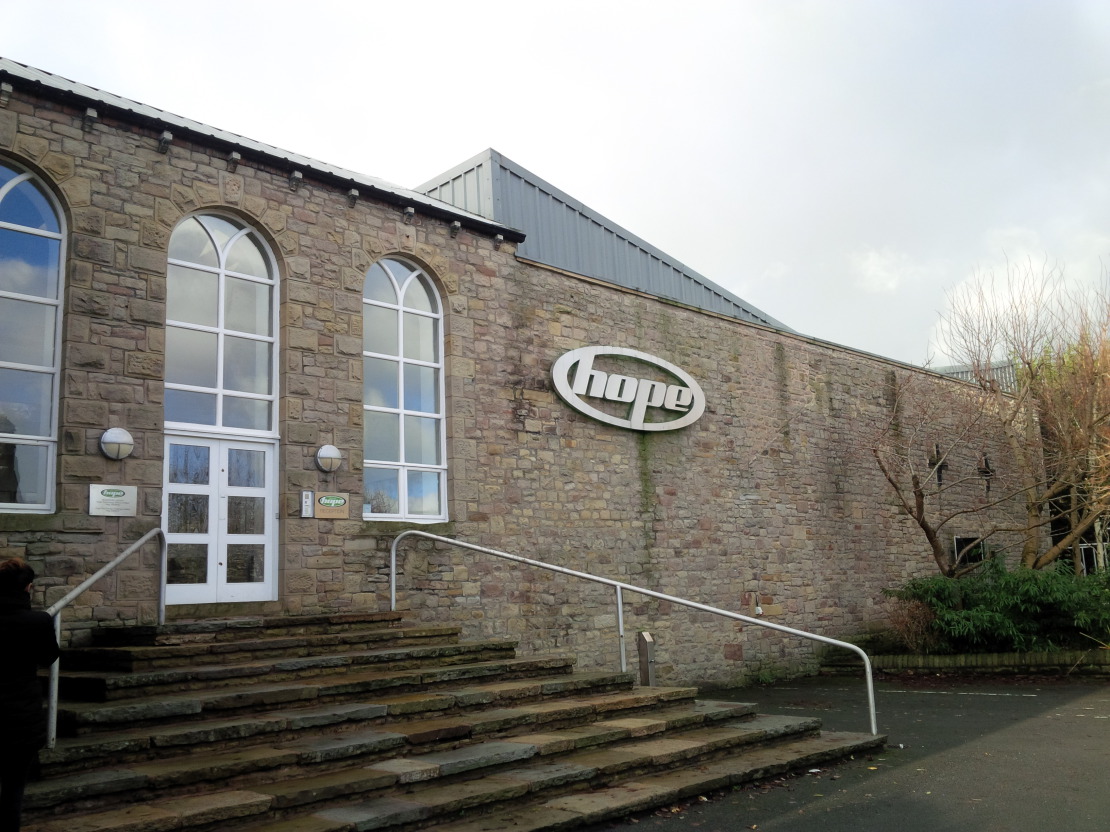
La fabbrica si trova a Barnoldswick, vicino a Manchester, tra le colline dello Yorkshire. Lì vicino si trovano anche Rolls Royce ed altri produttori di alto livello ingegneristico. Abbiamo visitato Hope per vedere come i prodotti vengono fatti e come funziona la linea di produzione. I ragazzi di Hope ci hanno permesso di capire quali siano il loro stile di vita e la dedizione per la mountain bike. L’impressione che abbiamo avuto è che Hope faccia ciò in cui crede e che sia una gran bella azienda in cui lavorare.
Introduzione
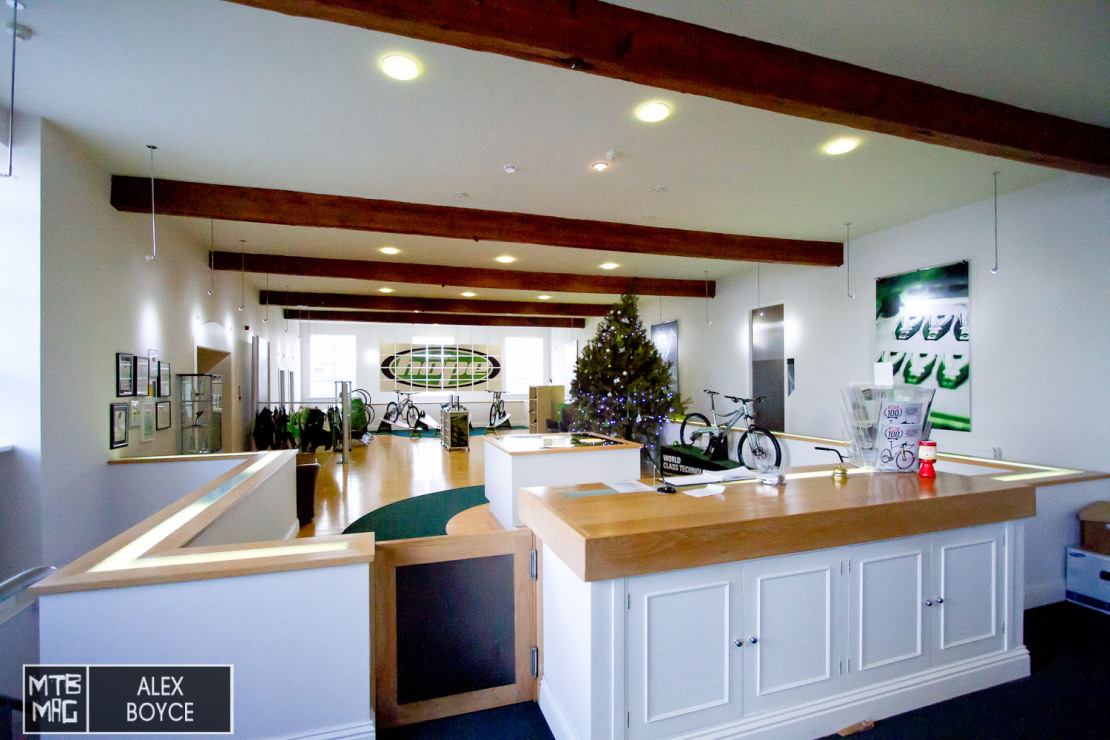
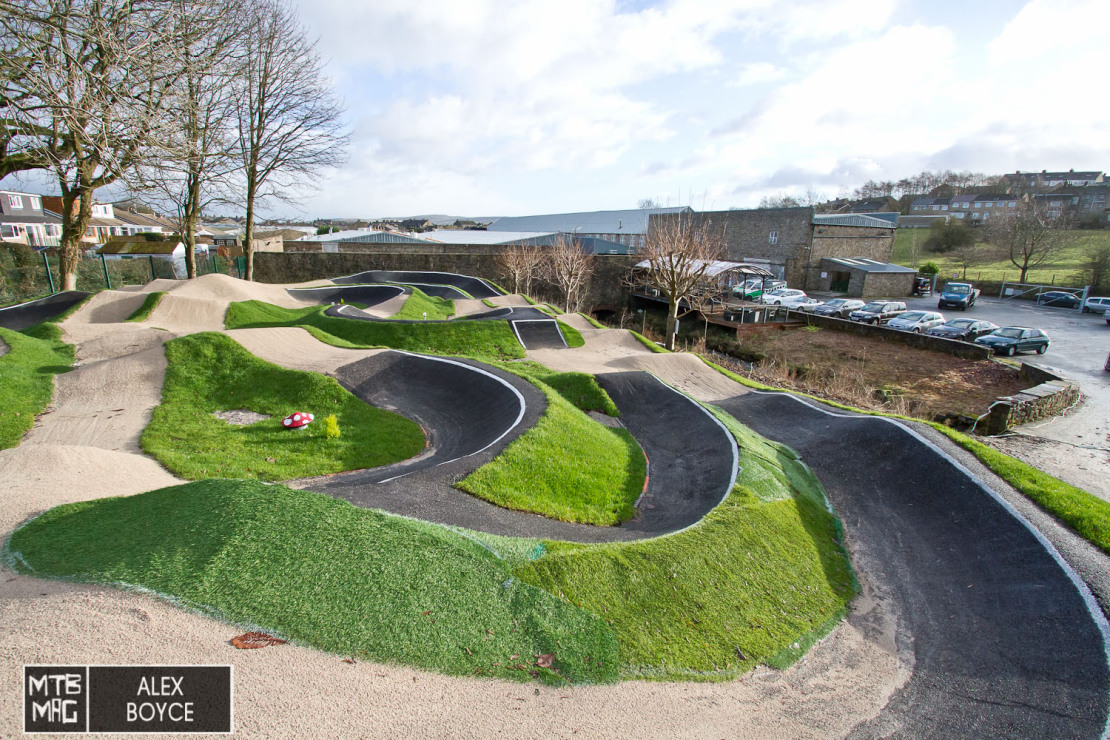
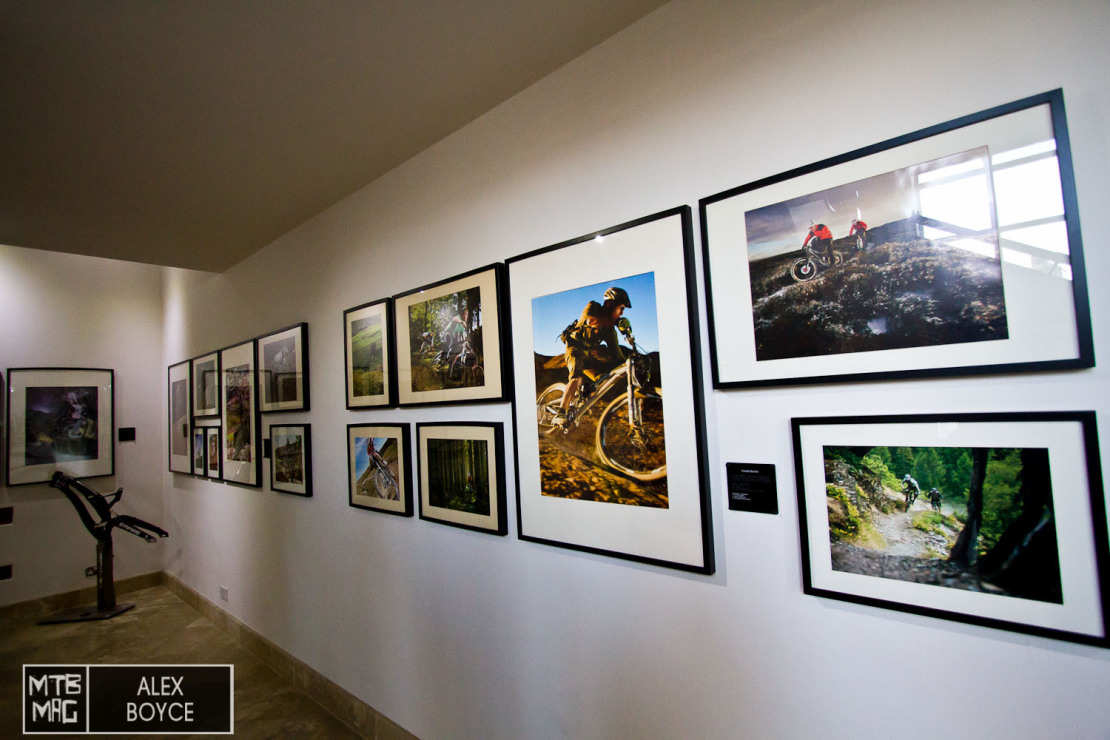
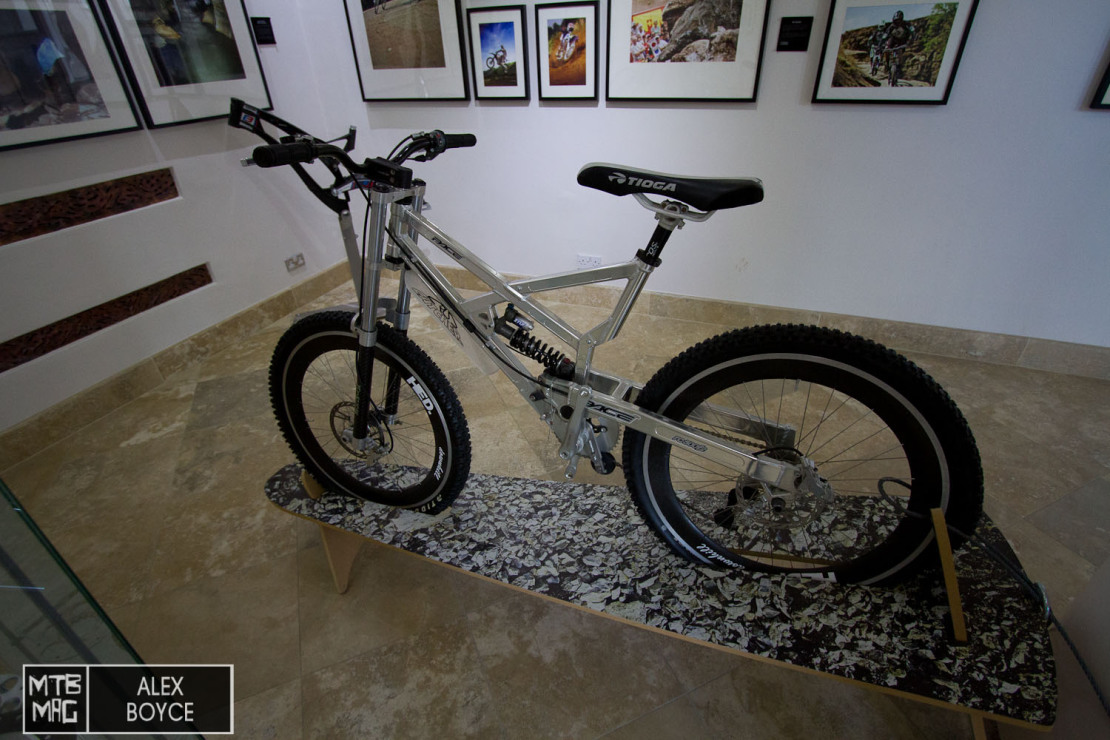
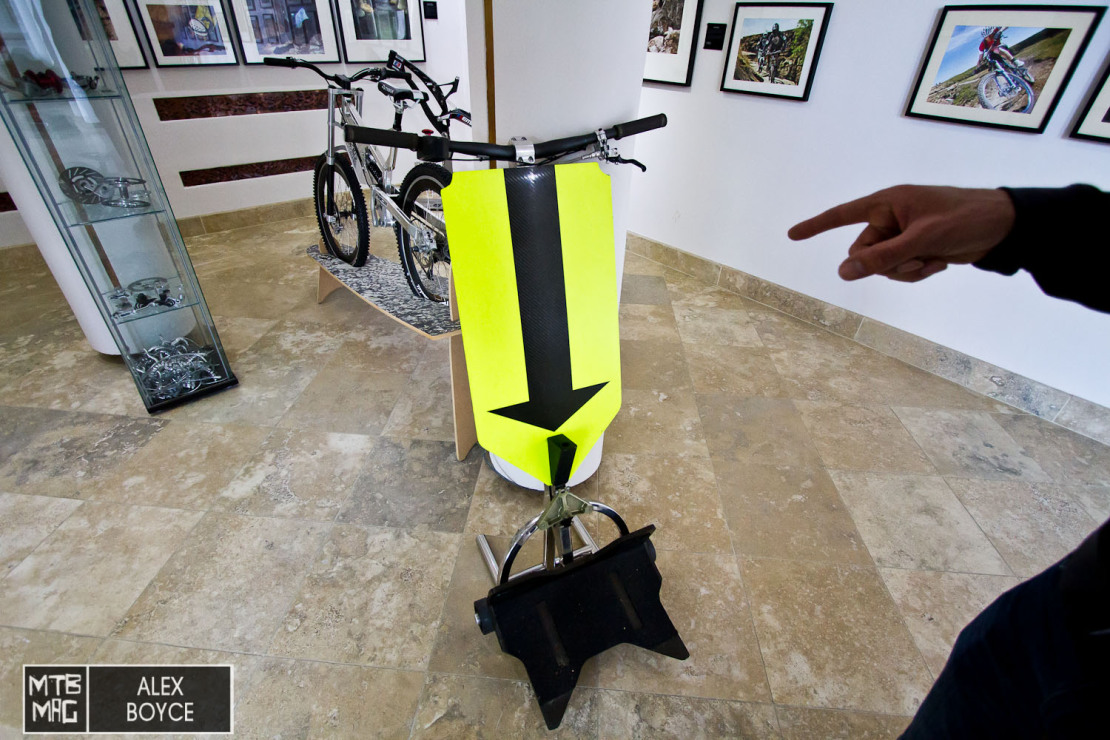
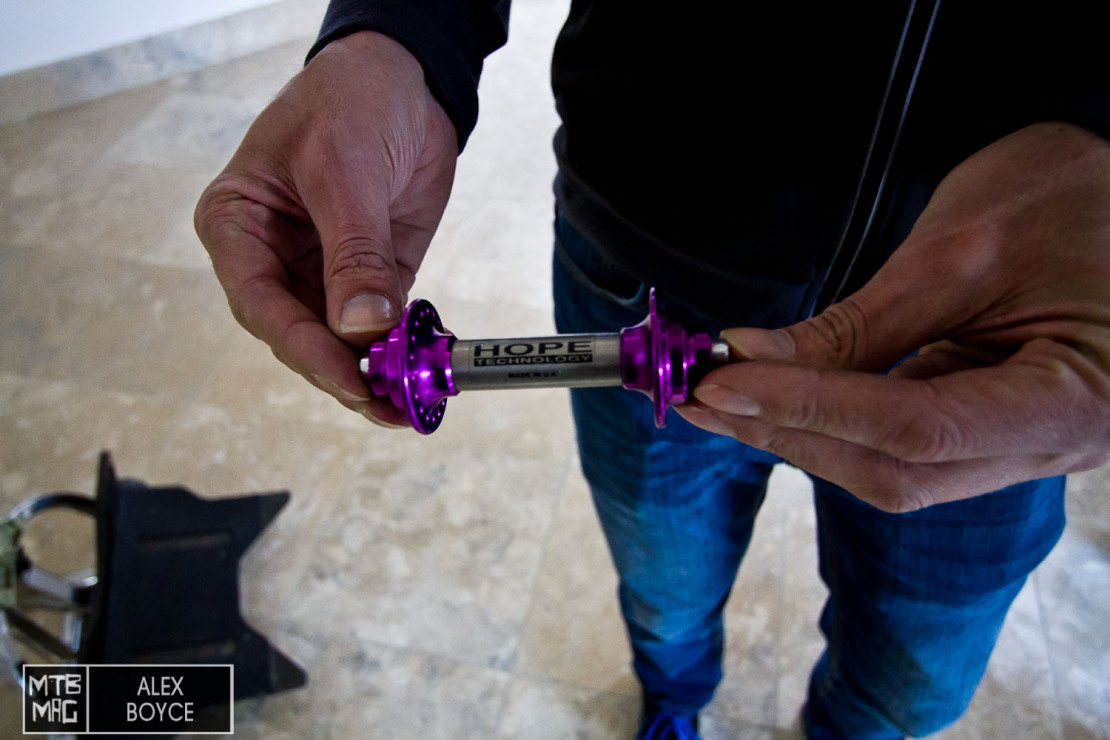
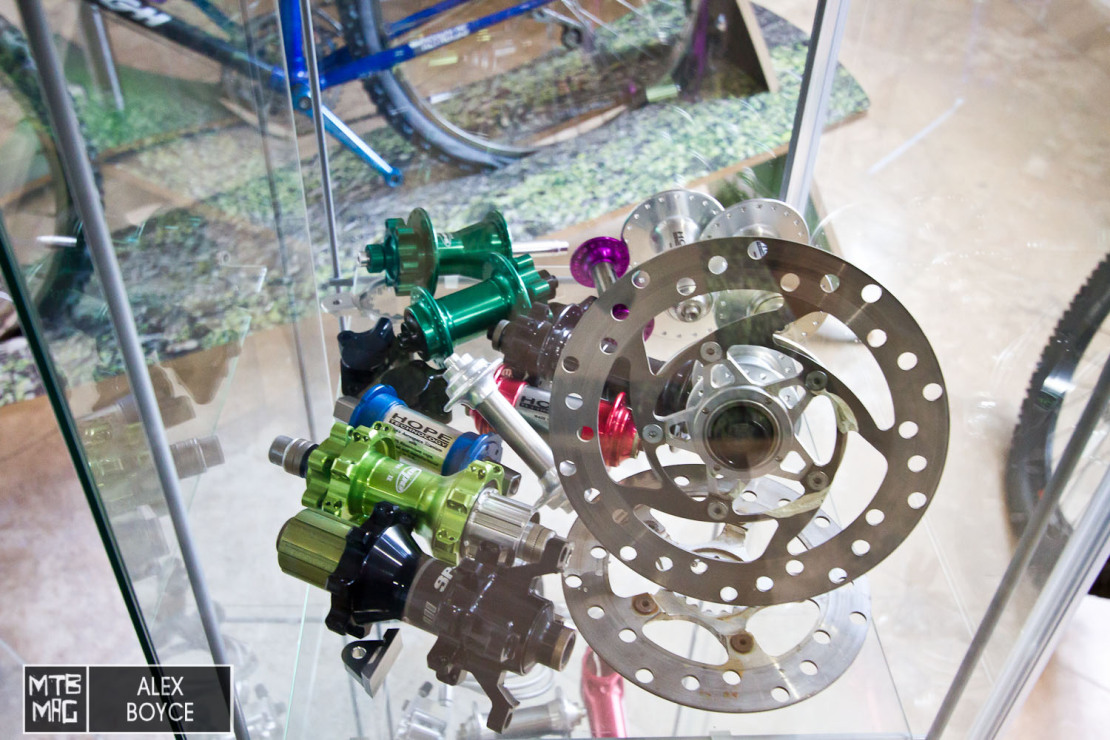
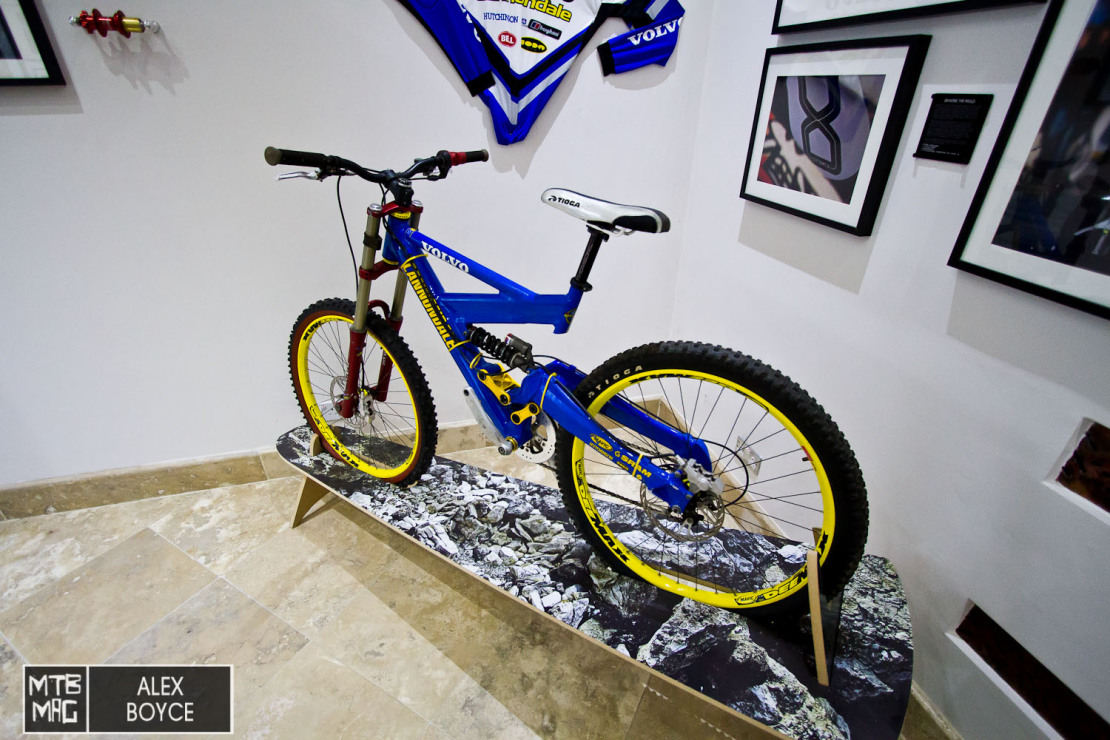
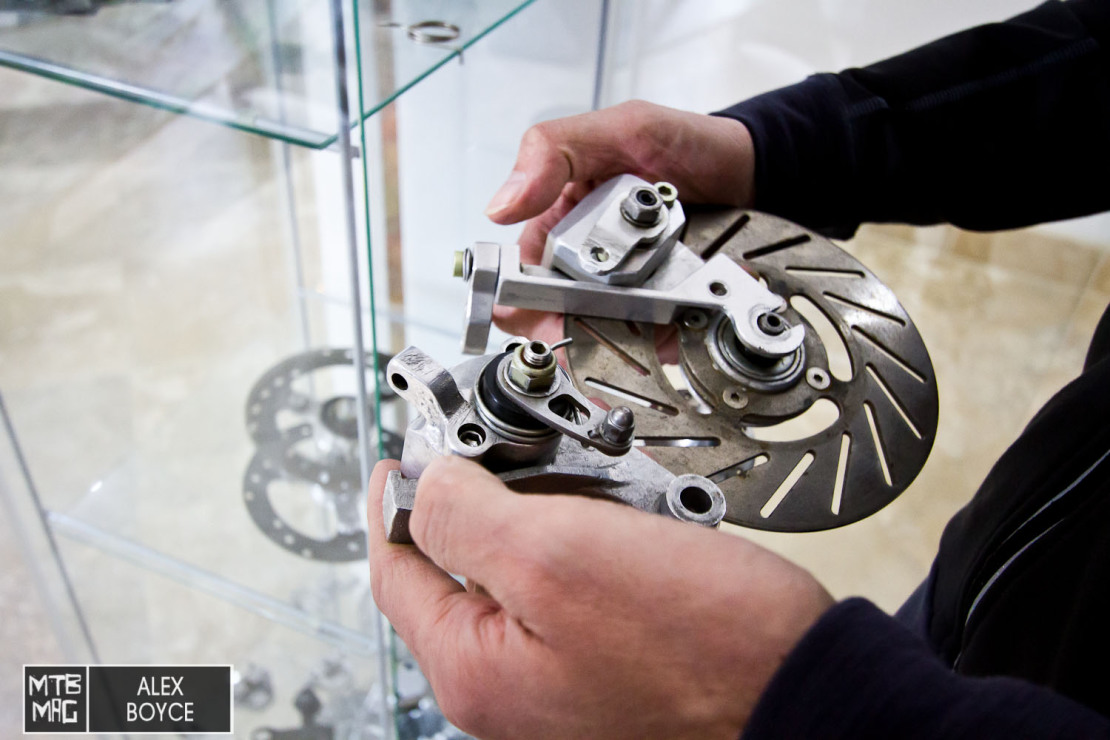
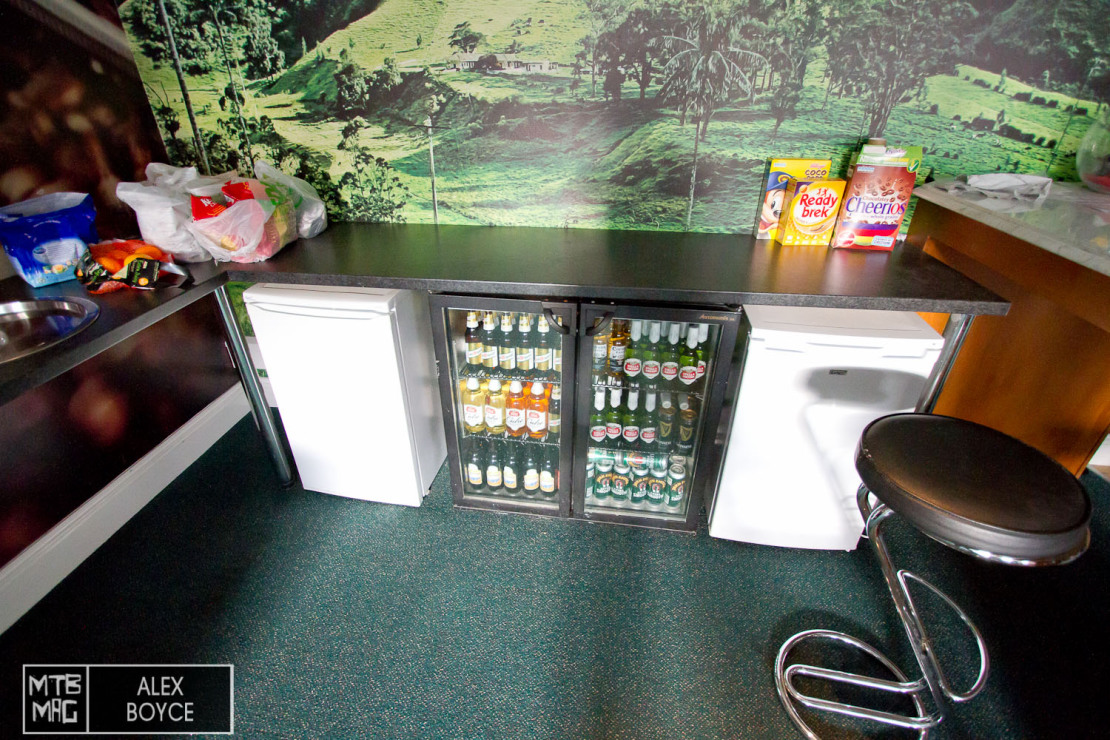
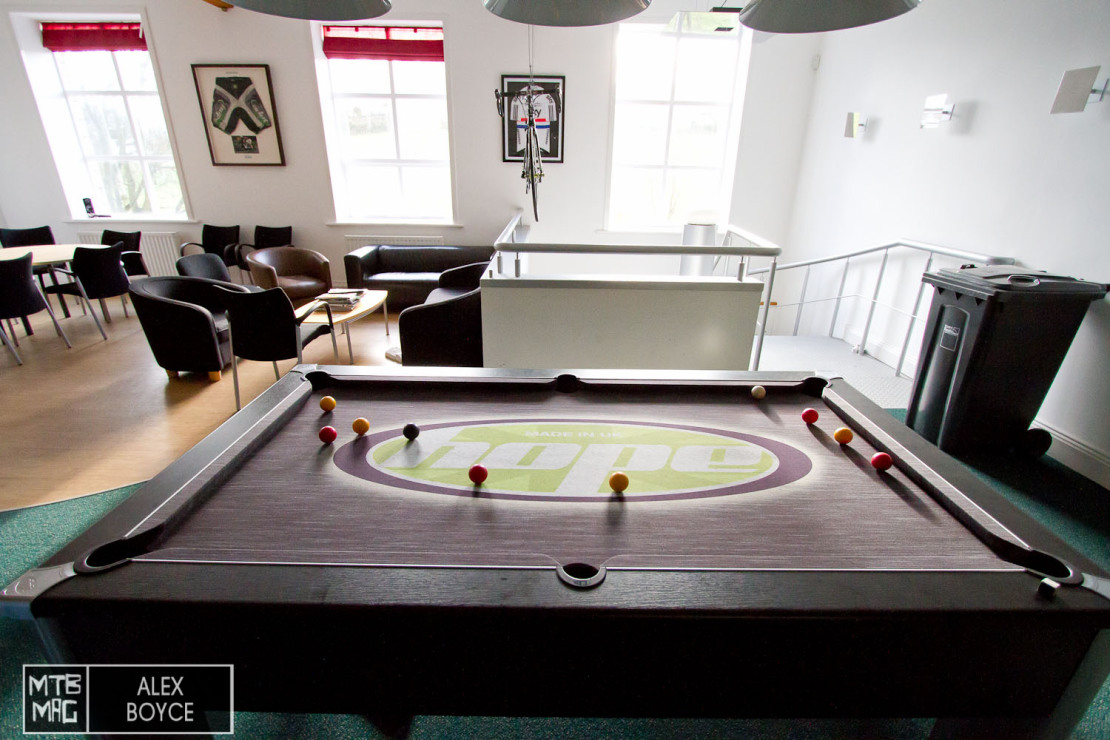
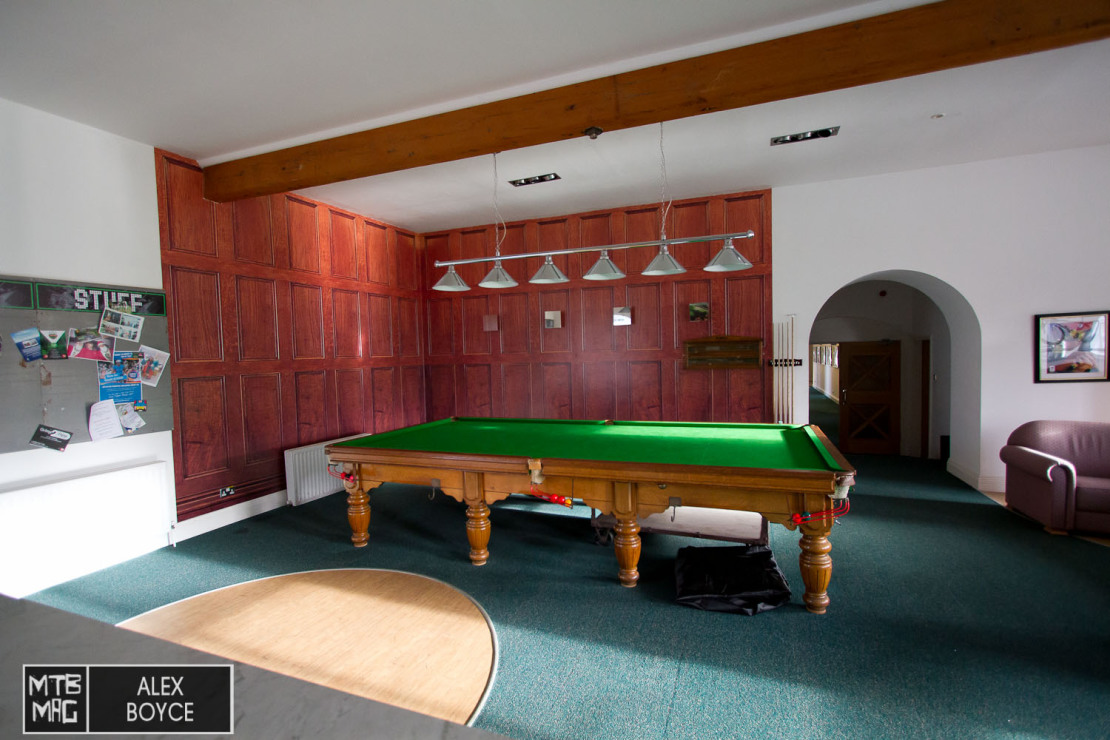
Ricerca e Sviluppo
Hope non riesce a fare un prodotto nuovo senza provare qualche idea nuova per scoprire cosa funziona e cosa no nell’uso di tutti i giorni. Abbiamo dato un’occhiata alle loro “idee”, che gironzolavano per gli uffici, ed alle macchine che usano per produrle.
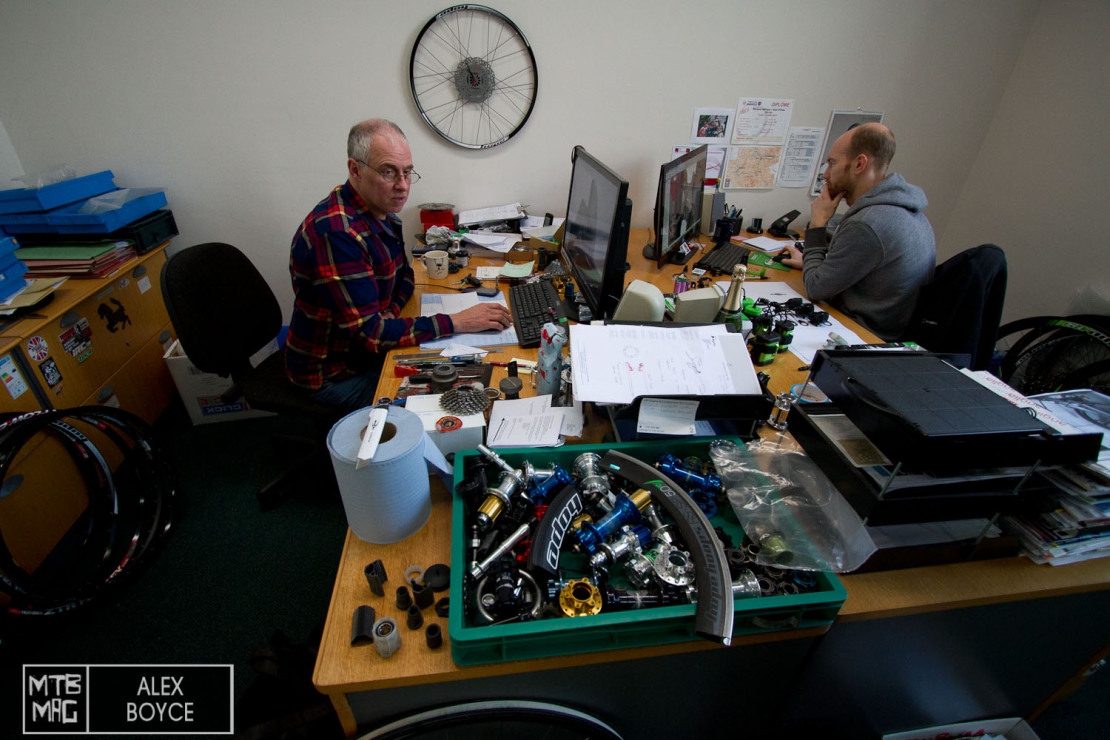
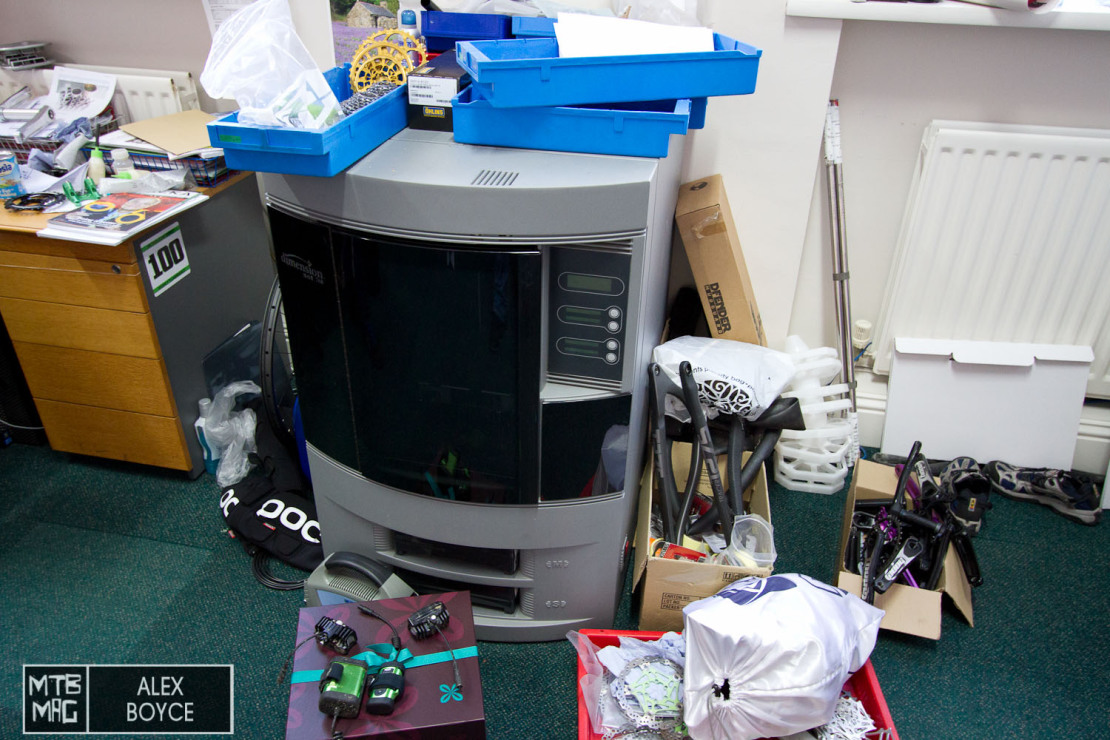
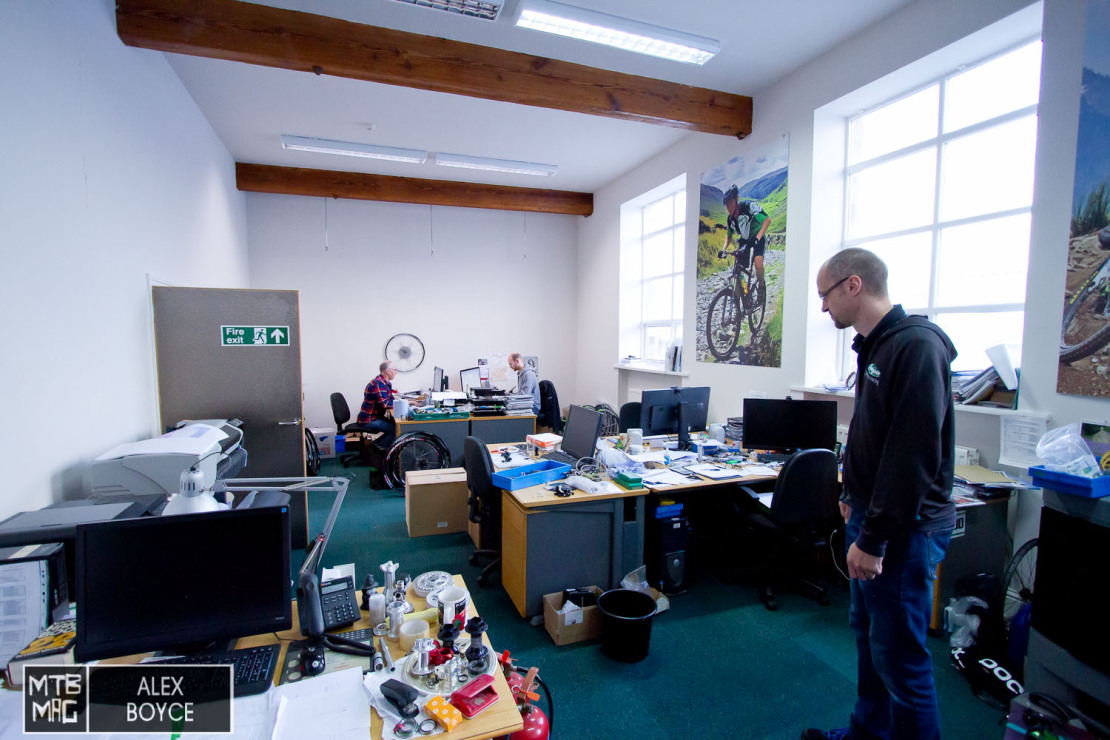
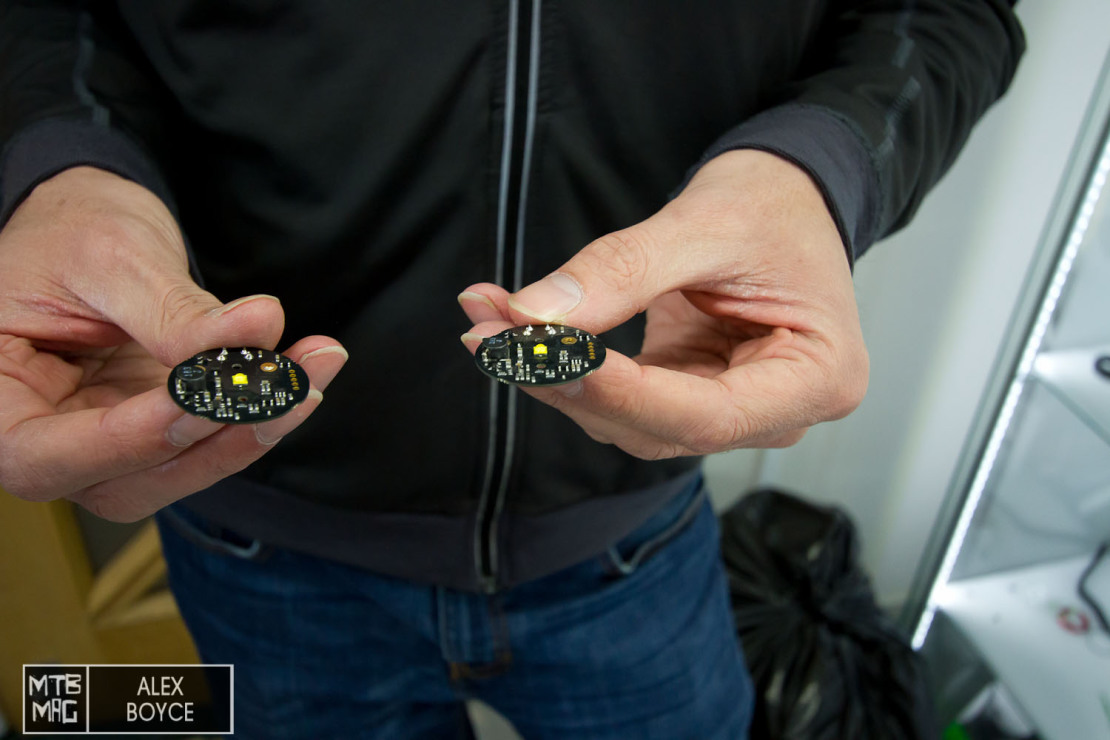
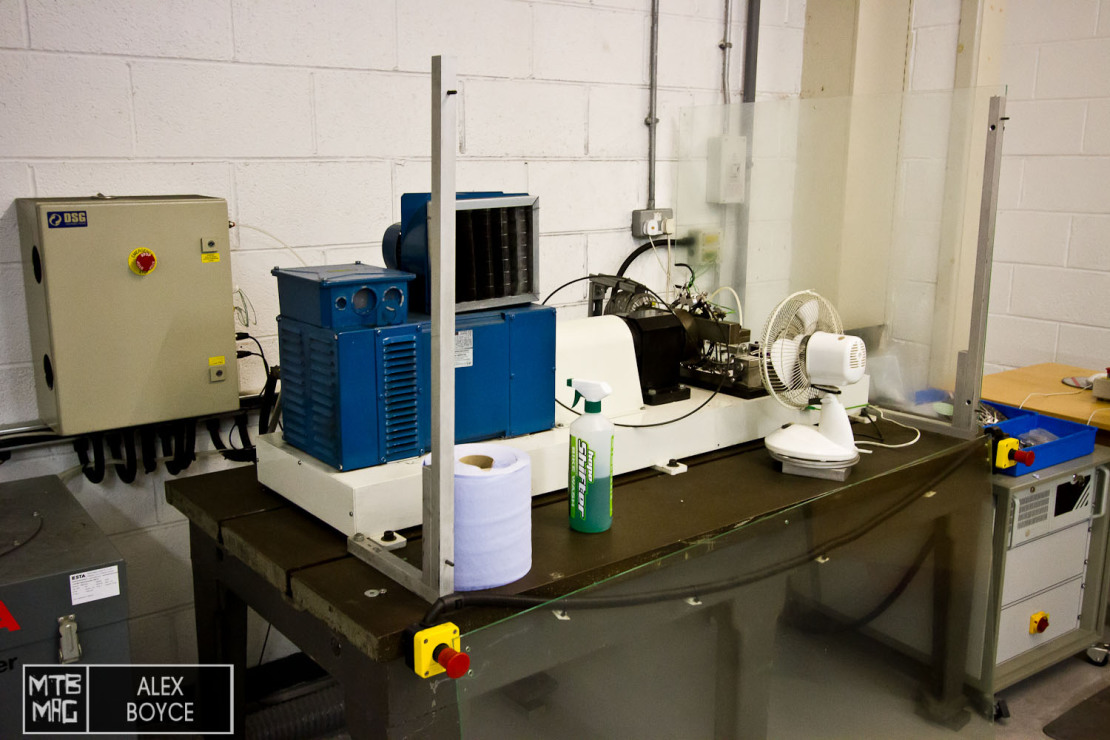
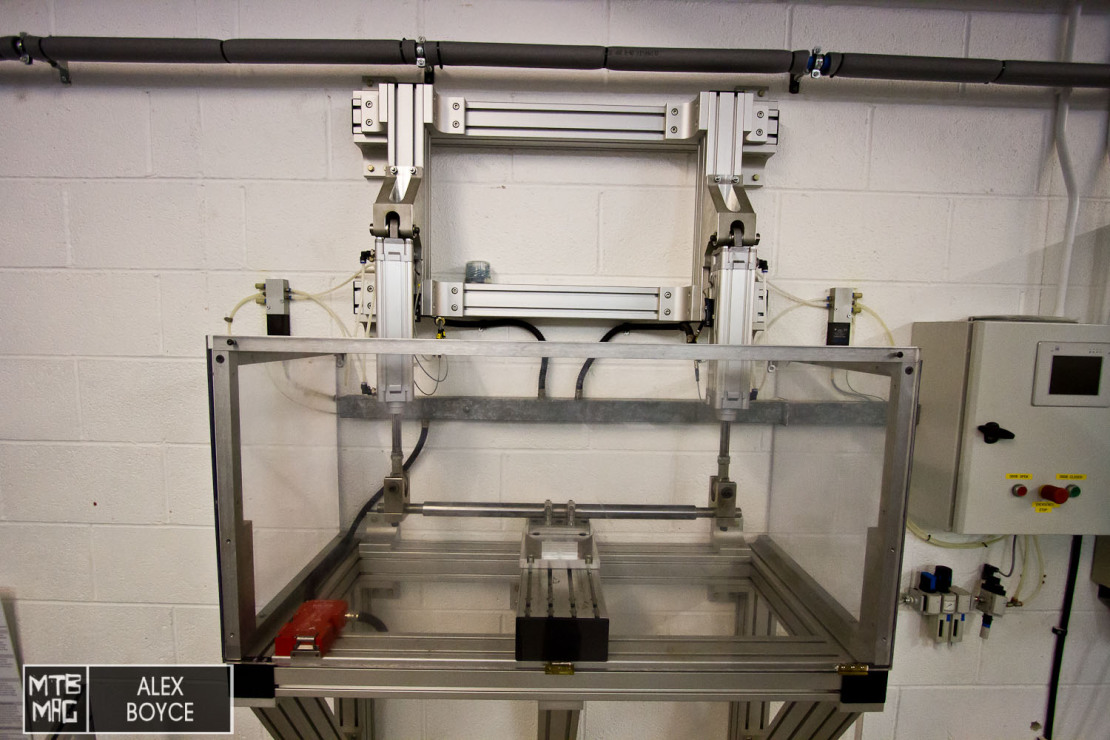
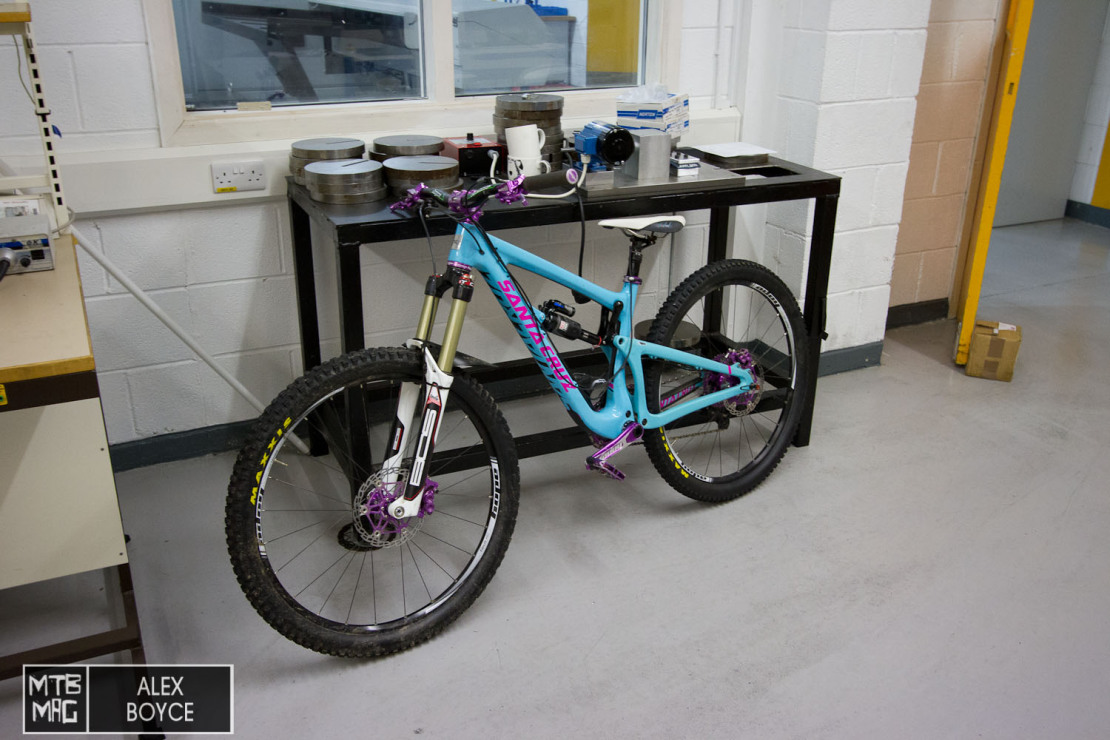
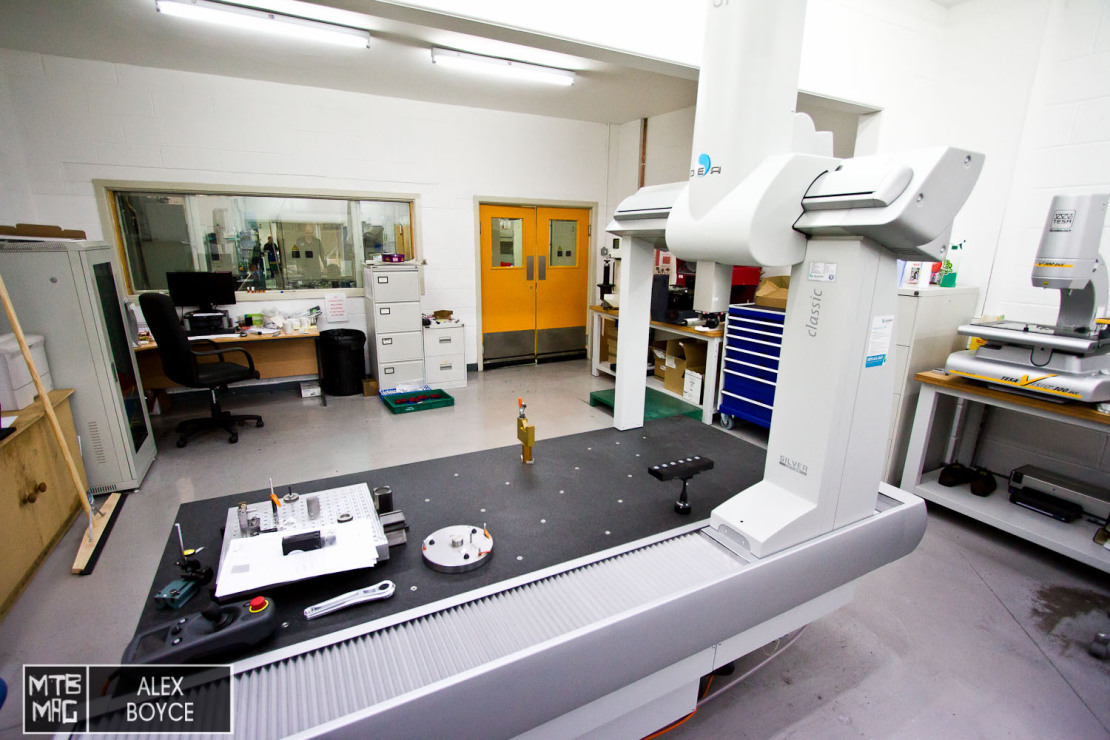
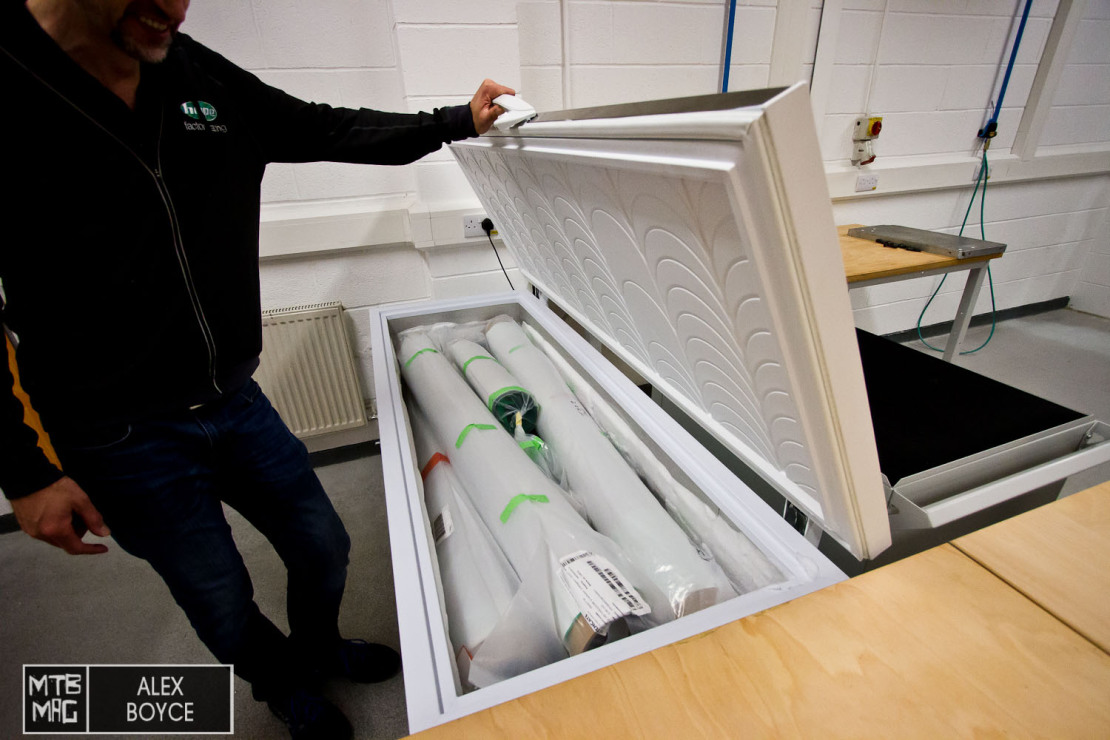
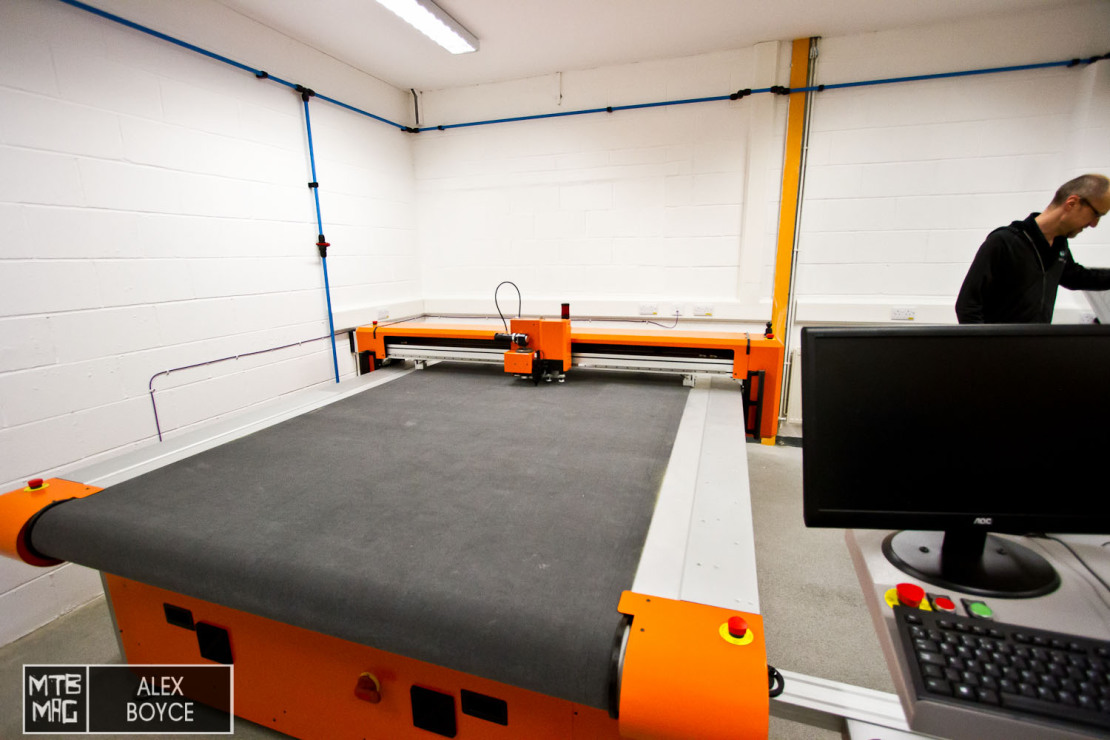
Produzione
Hope ha molto a cuore l’efficienza della propria produzione. Fa in casa quasi ogni singolo elemento che produce, esclusi i cavi delle luci ed alcuni cerchi che monta sui mozzi. Anche le più piccole viti sono fatte con le macchine CNC. Hanno un sacco di macchine che operano 24 ore al giorno per tagliare, fresare e lucidare componenti della massima qualità. Le tolleranze arrivano in alcuni casi ai 2 micron per ridurre al minimo l’usura e si trovano essere tra le più basse di tutta l’industria ciclistica.
Ci siamo guardati intorno per bene chiedendoci come gli sia venuto in mente di fare tutto. Sembra che ci sia un motto che suoni circa così: “quanto potrà mai essere difficile farci tutto da noi?”. Nella fabbrica non c’è una chiara linea di produzione, semplicemente le macchine sono raggruppate in posti diversi e svolgono mansioni diverse.
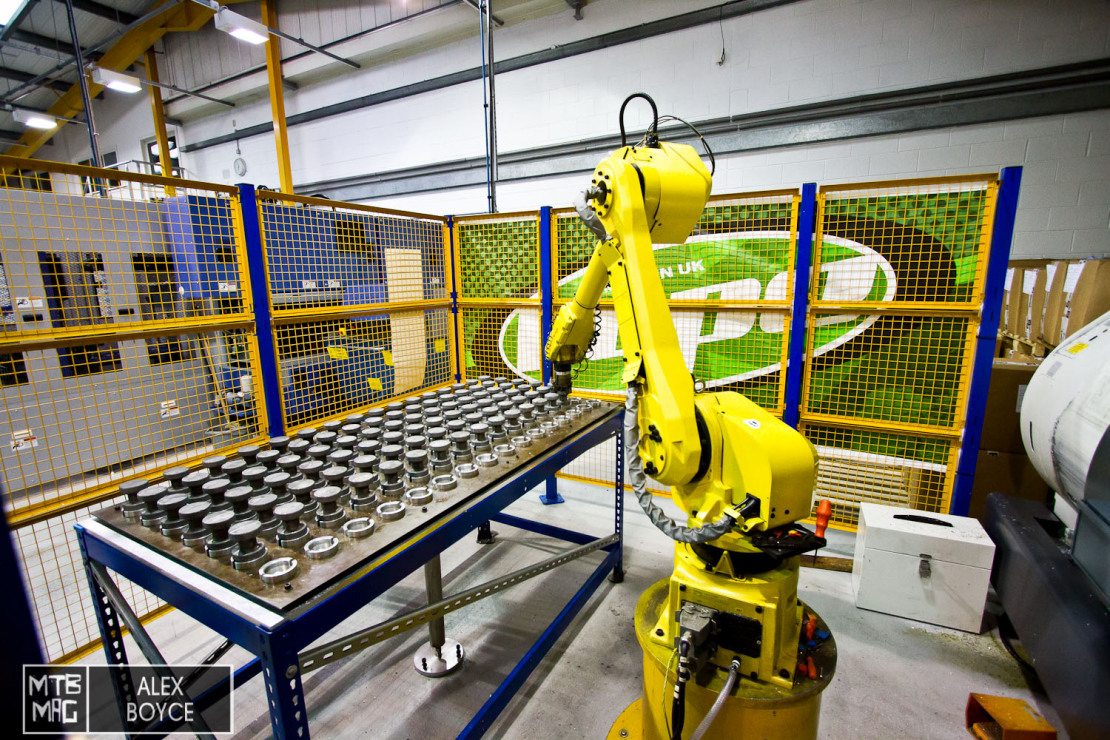
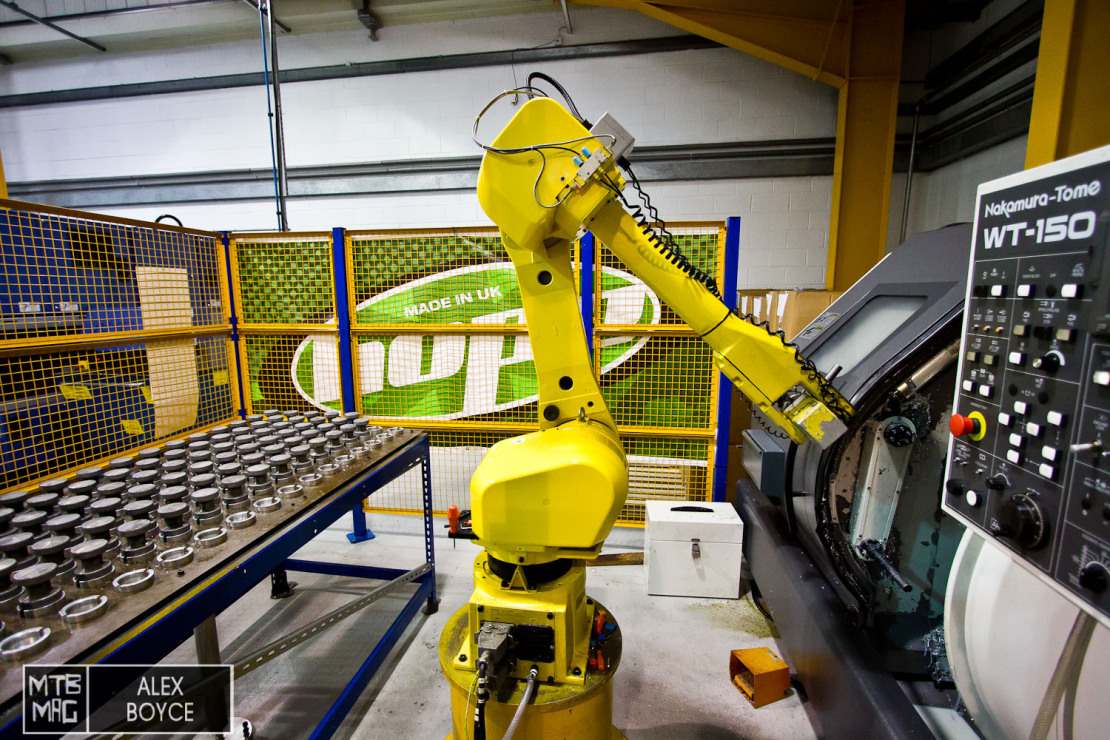
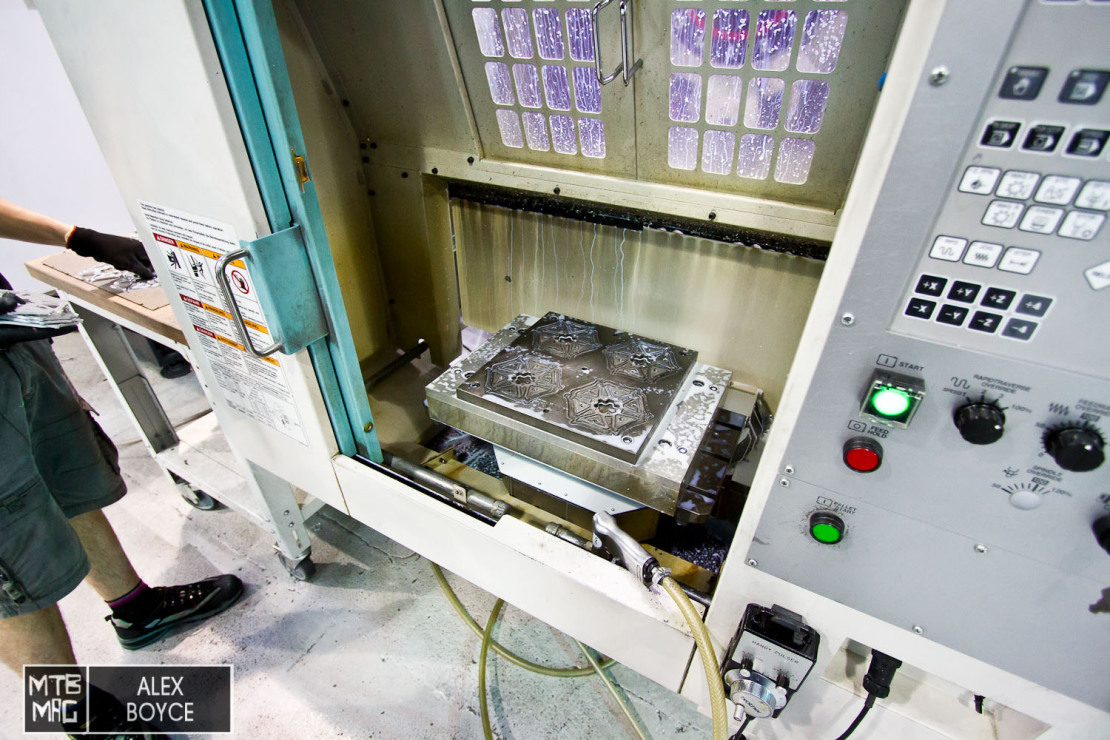
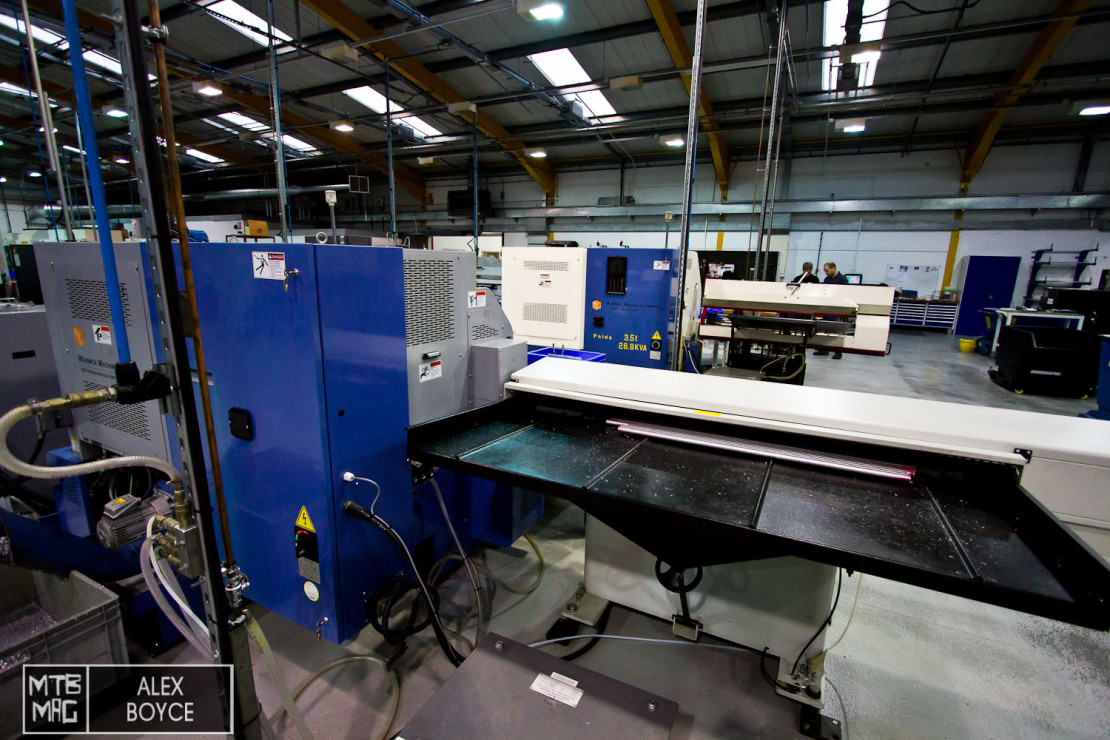
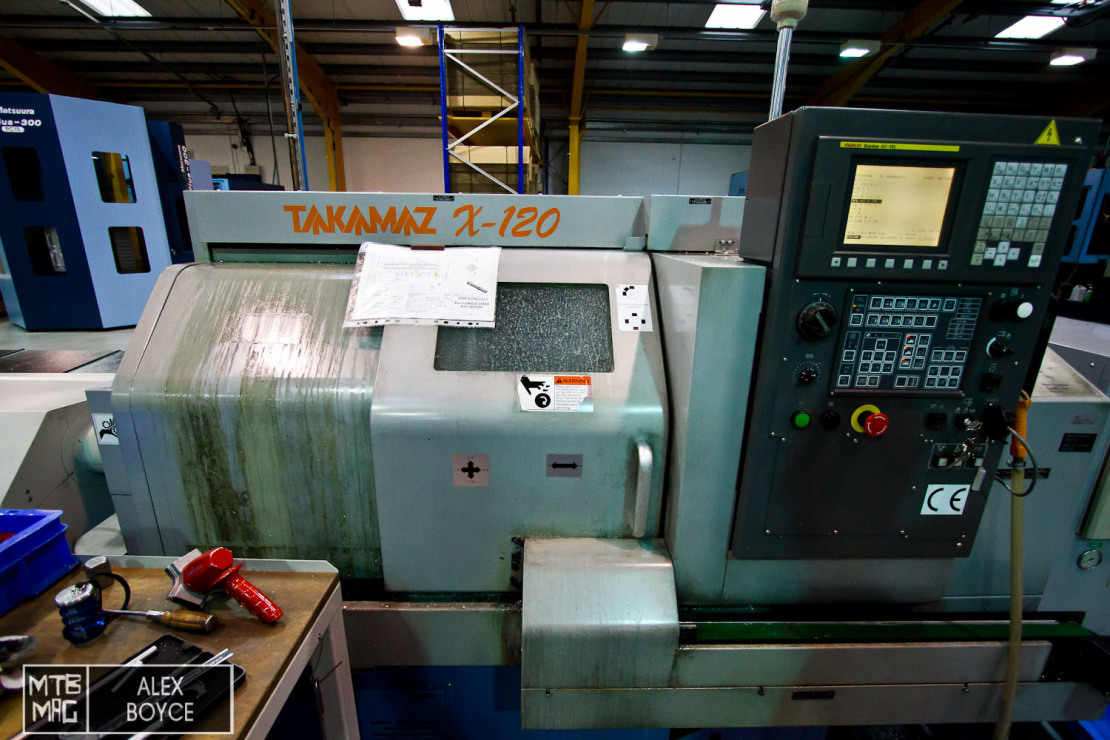
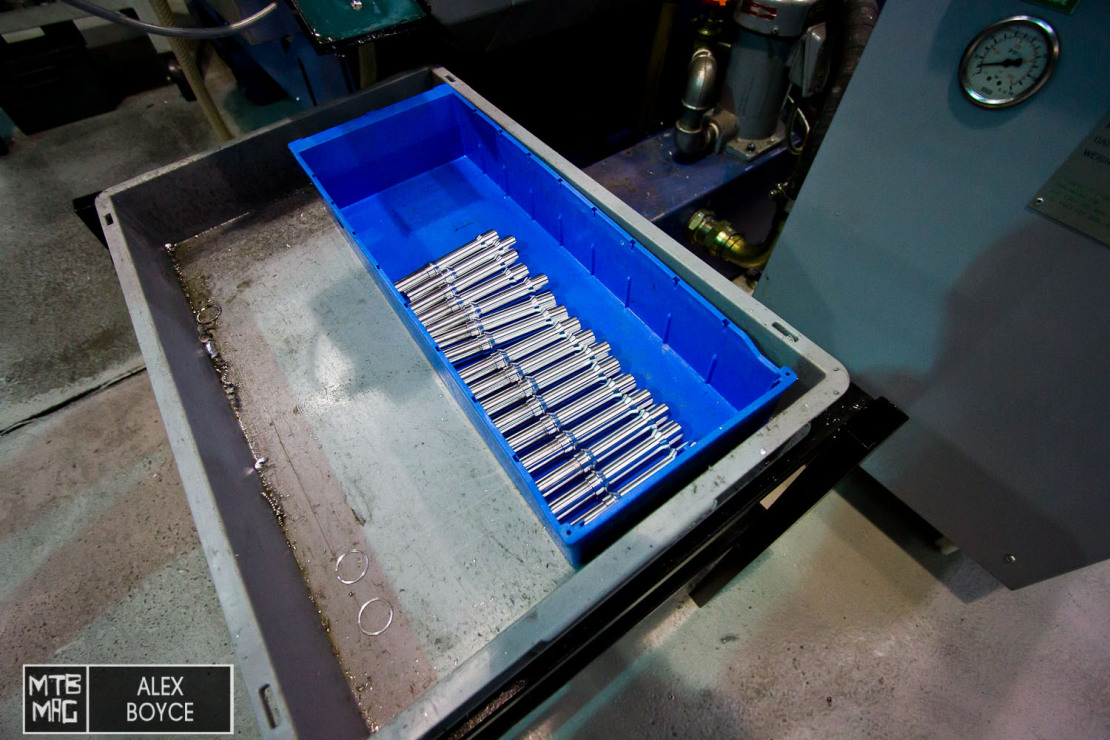
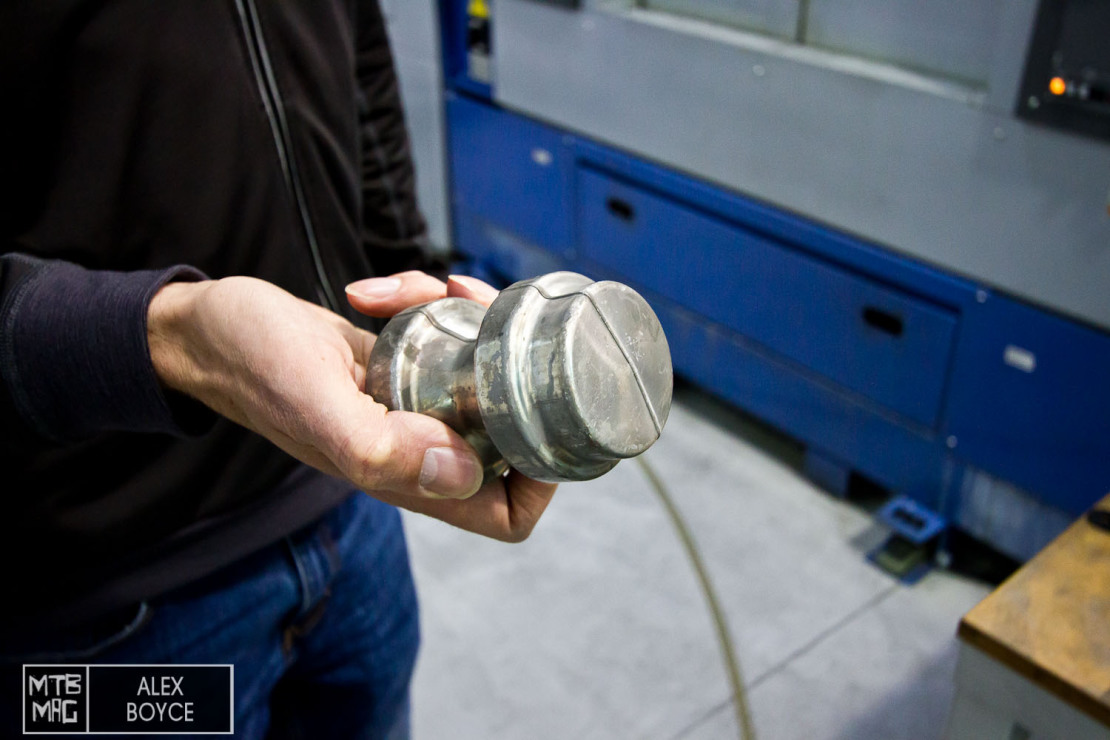
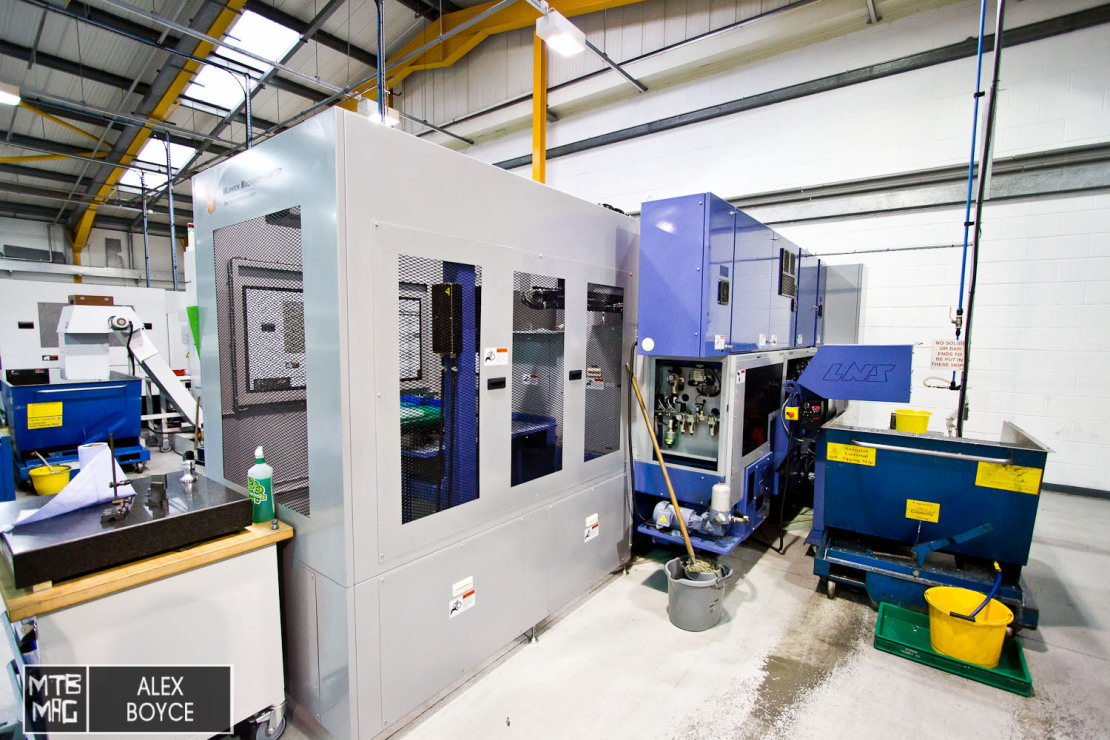
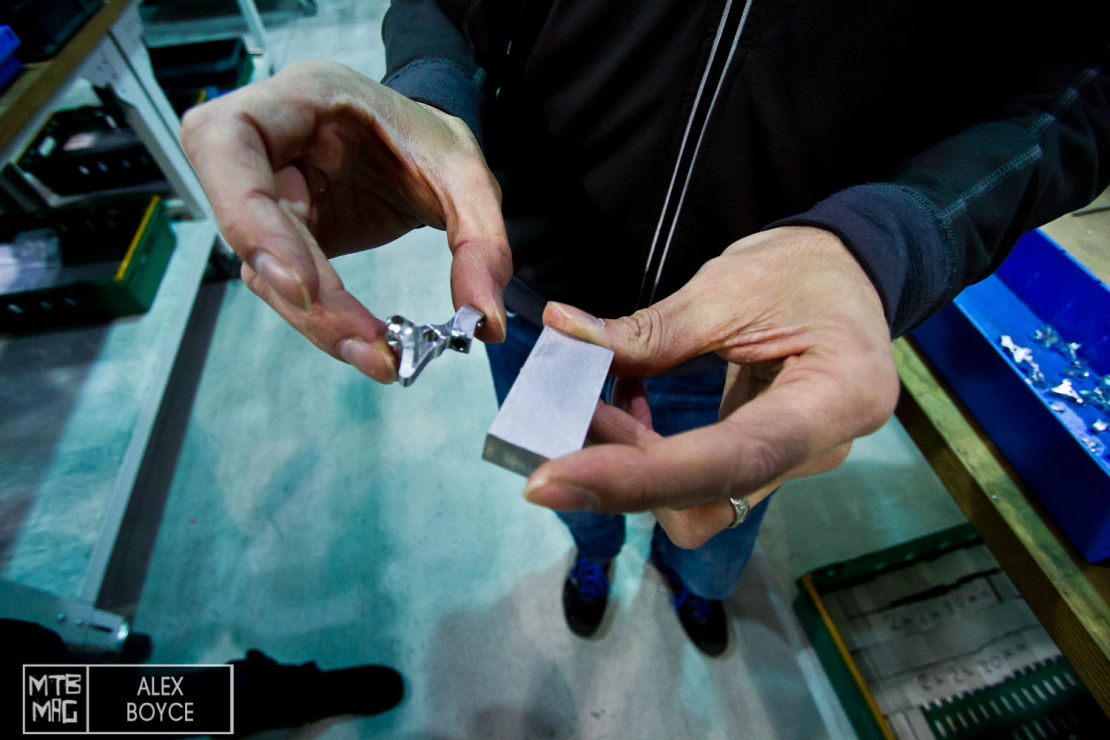
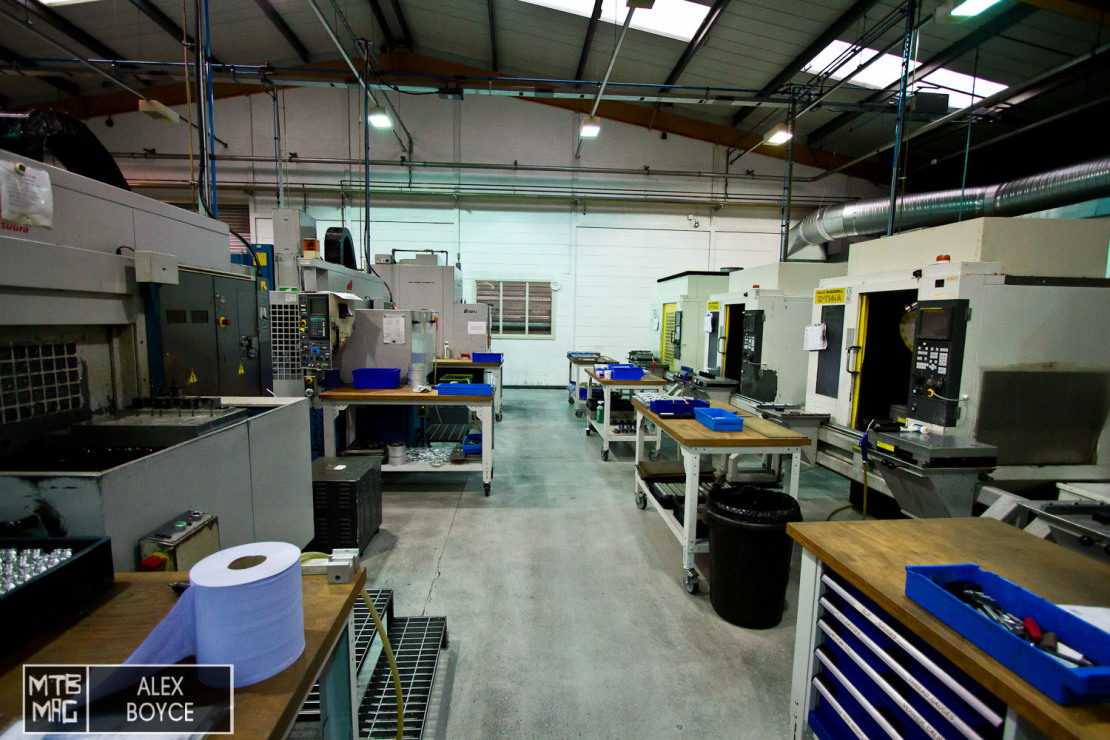
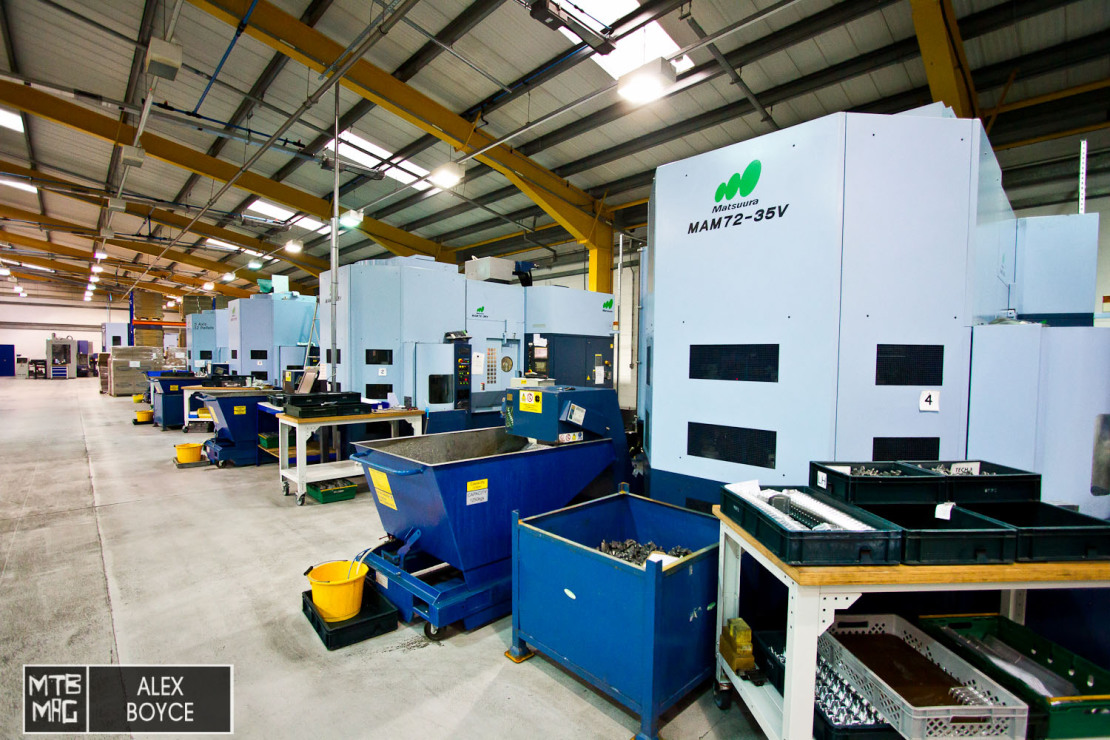
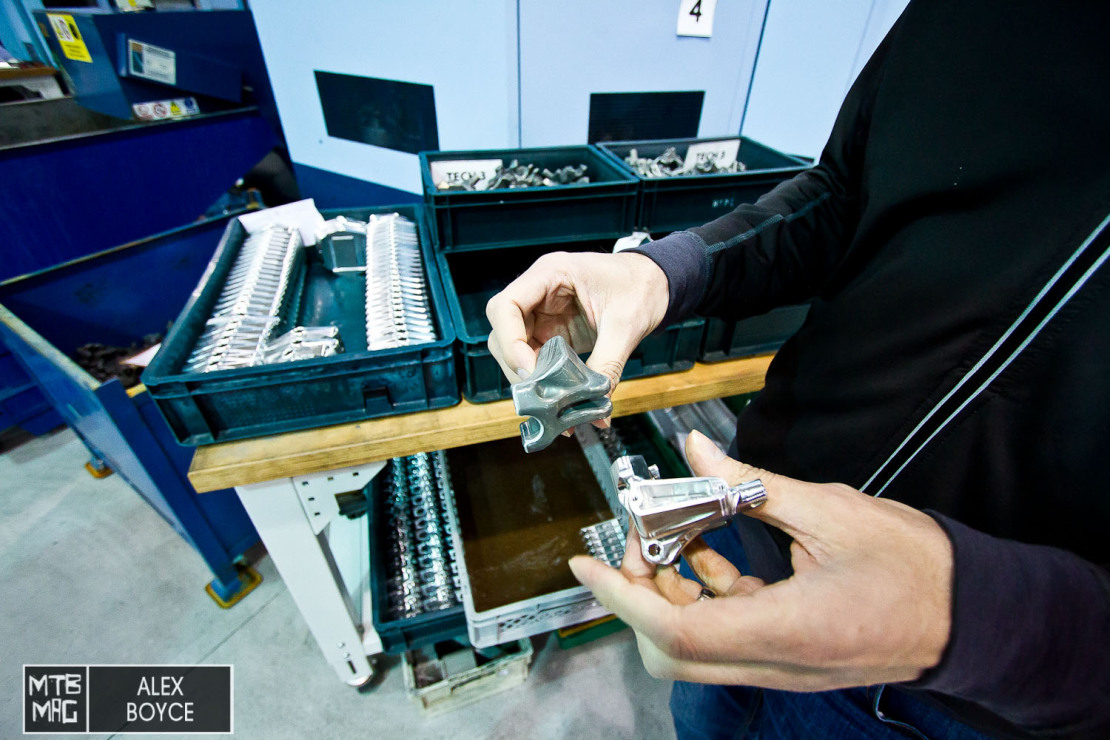
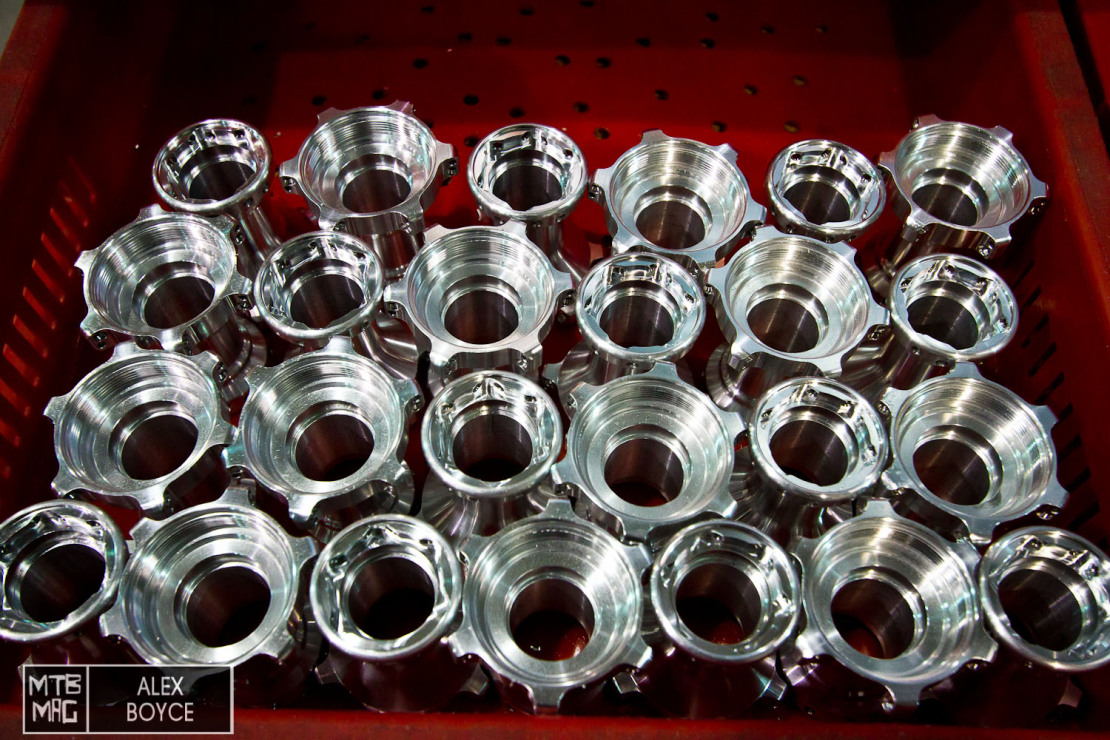
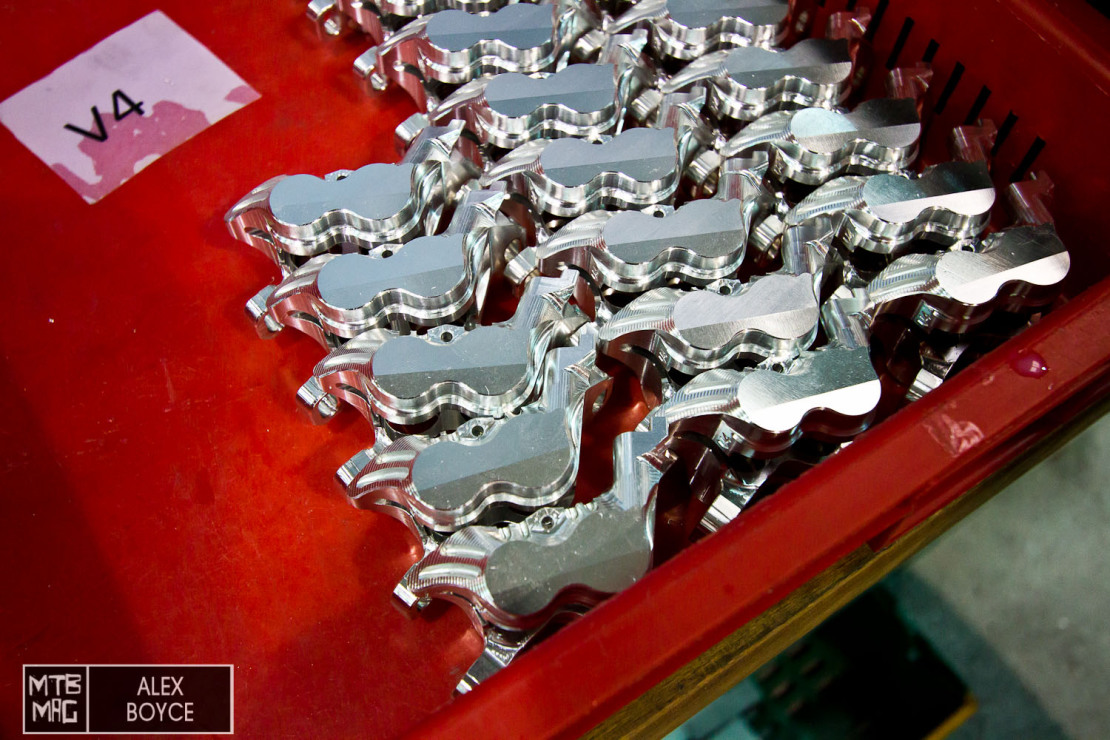
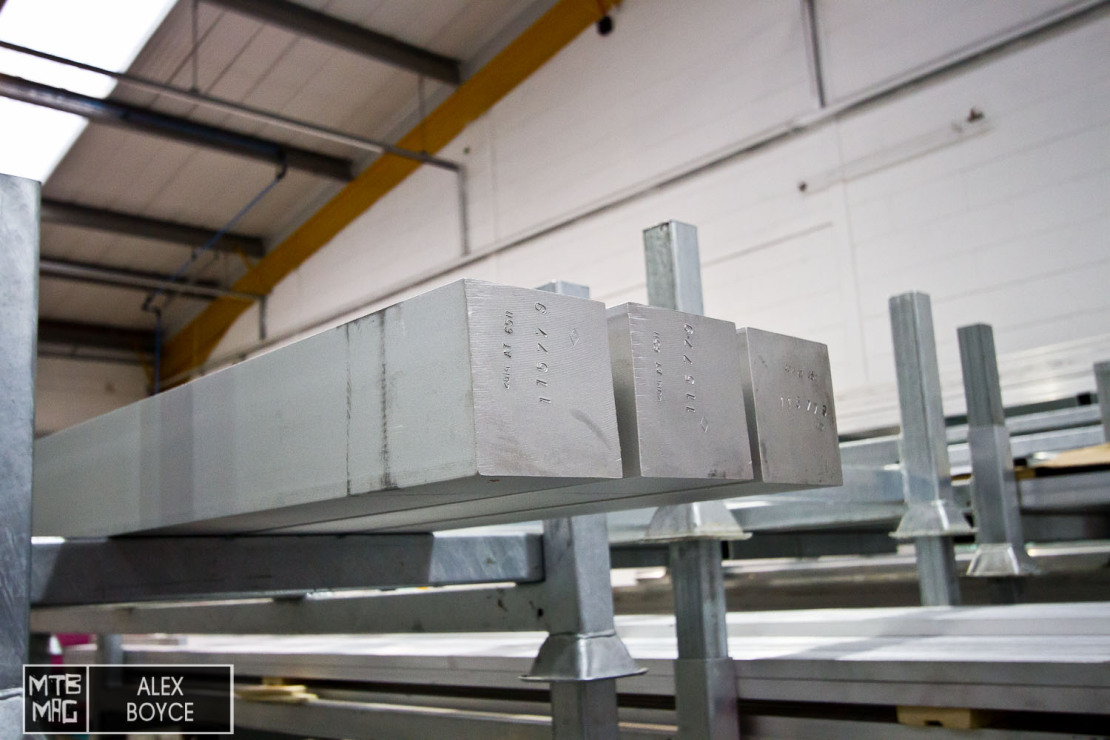
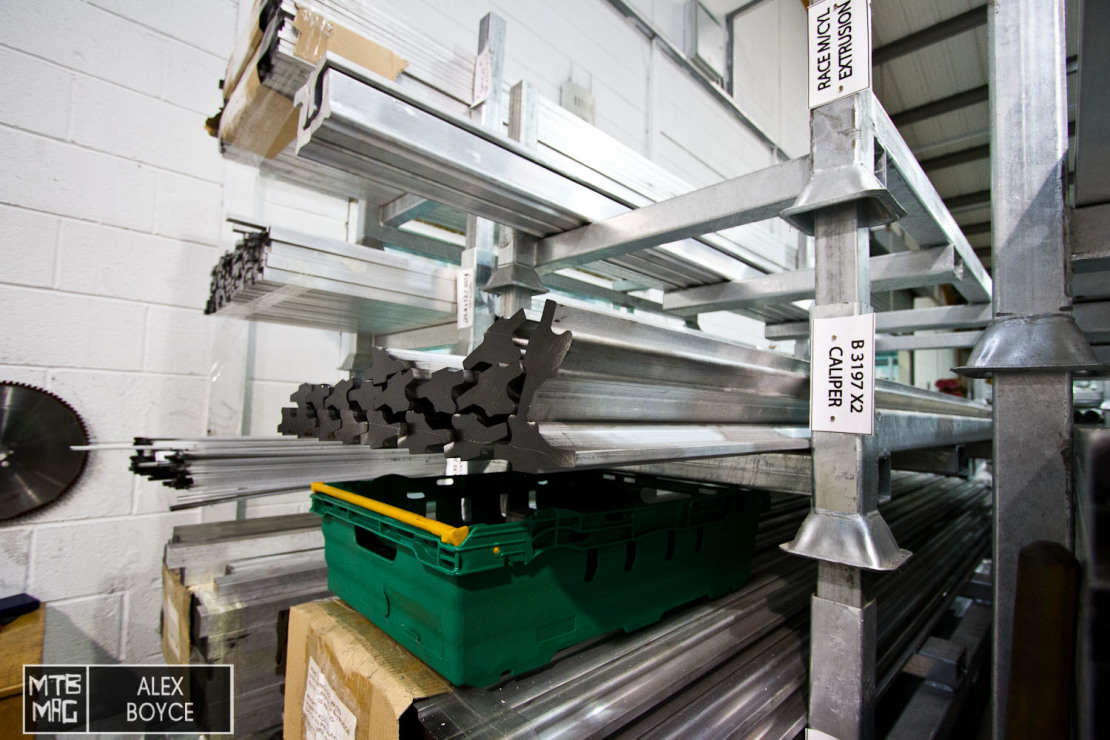
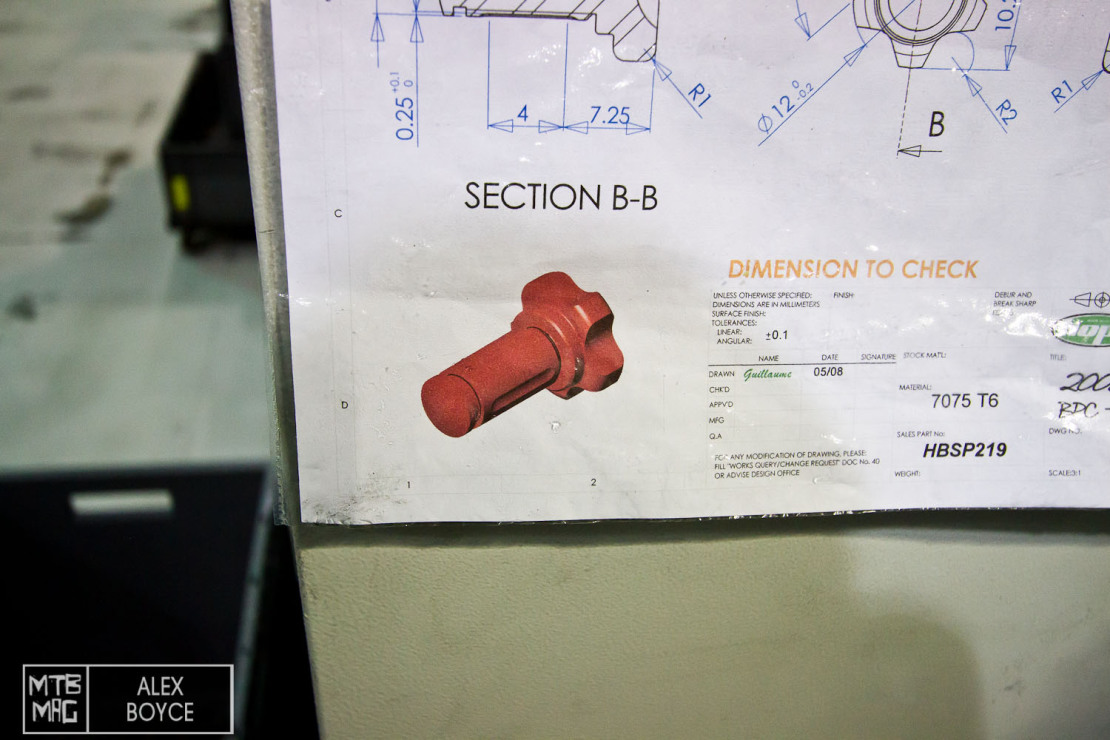
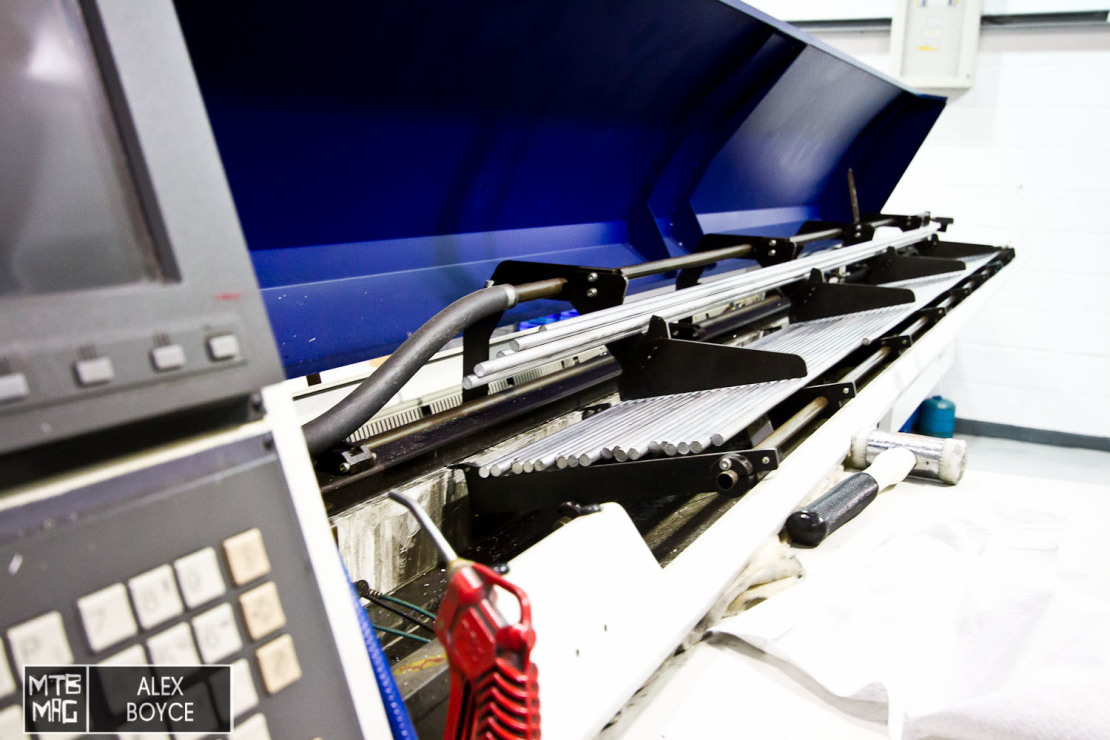
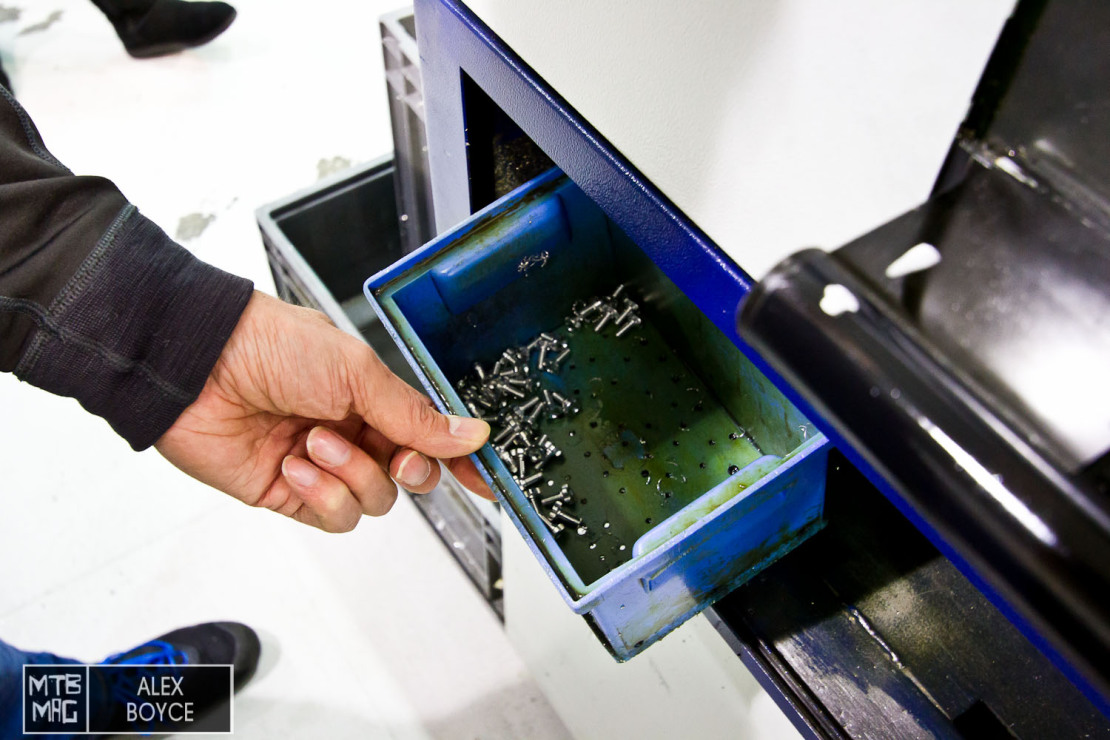
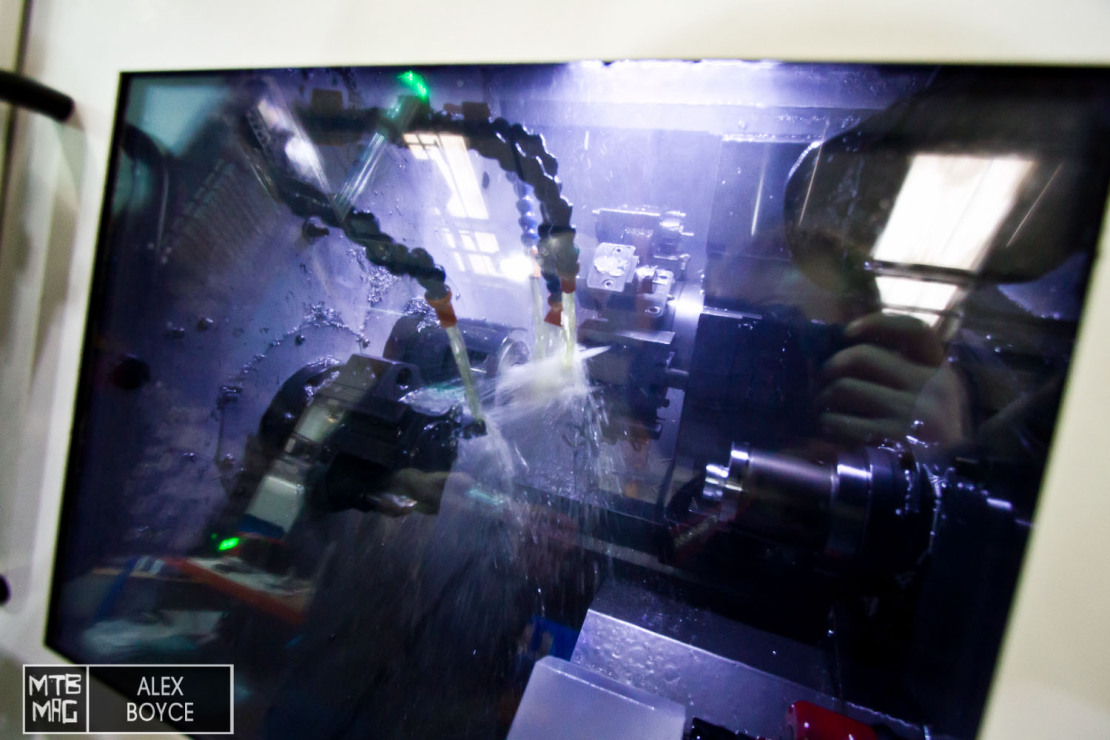
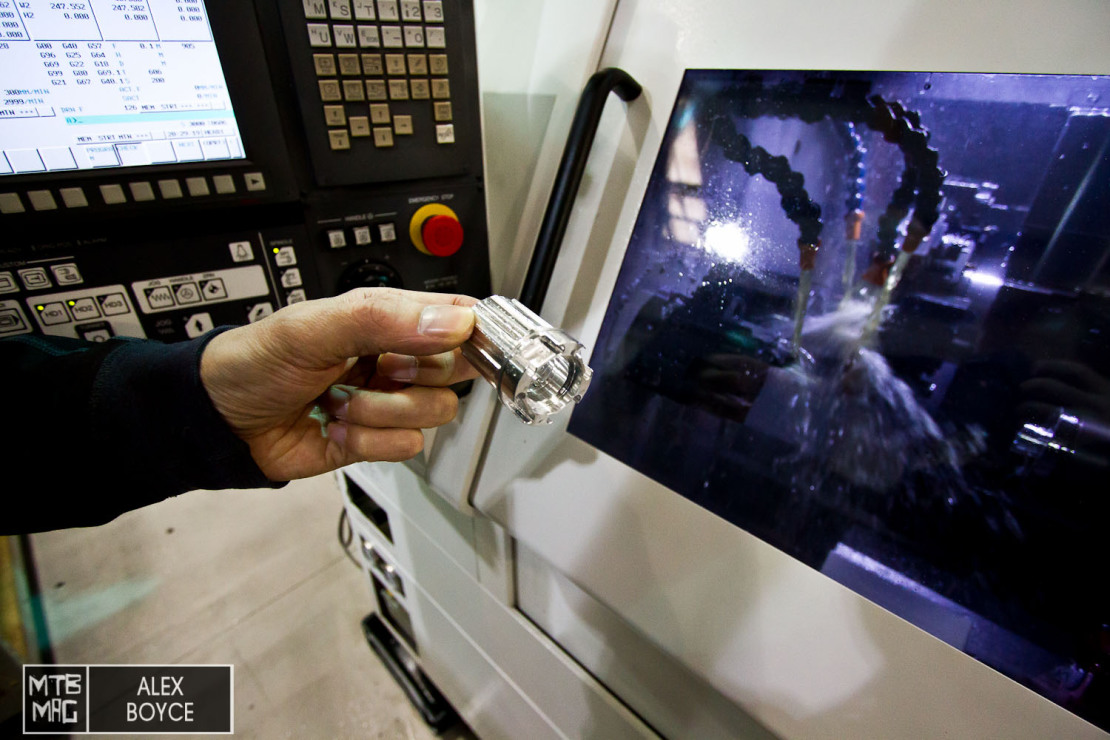
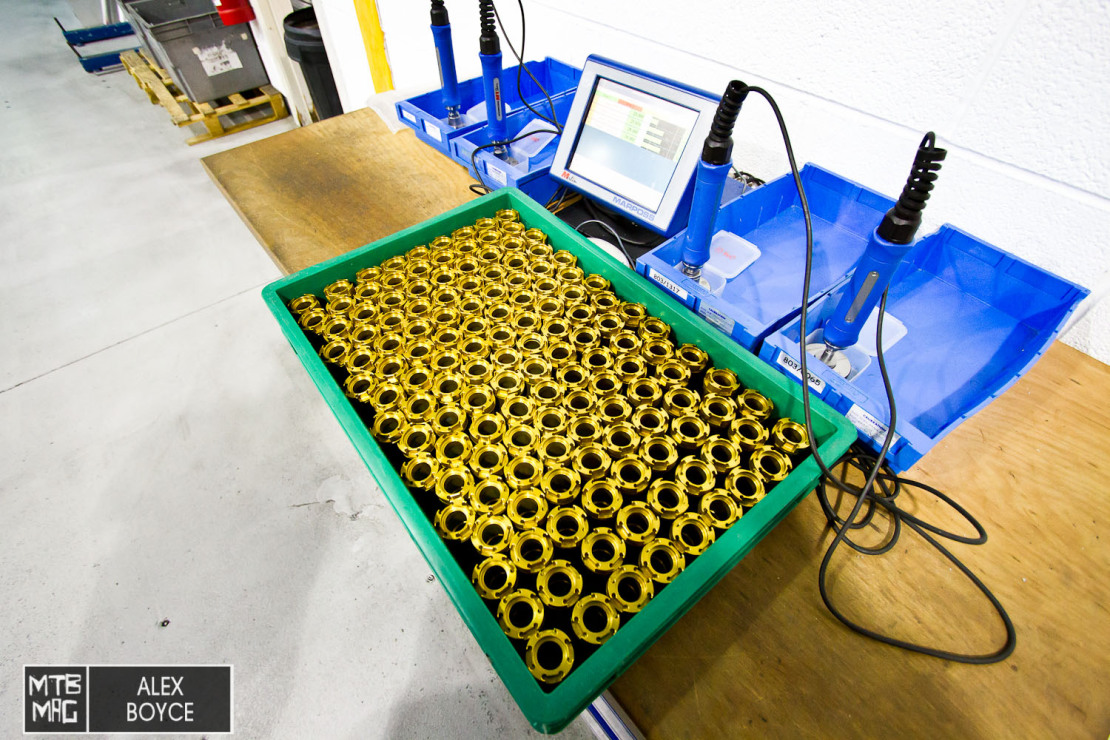
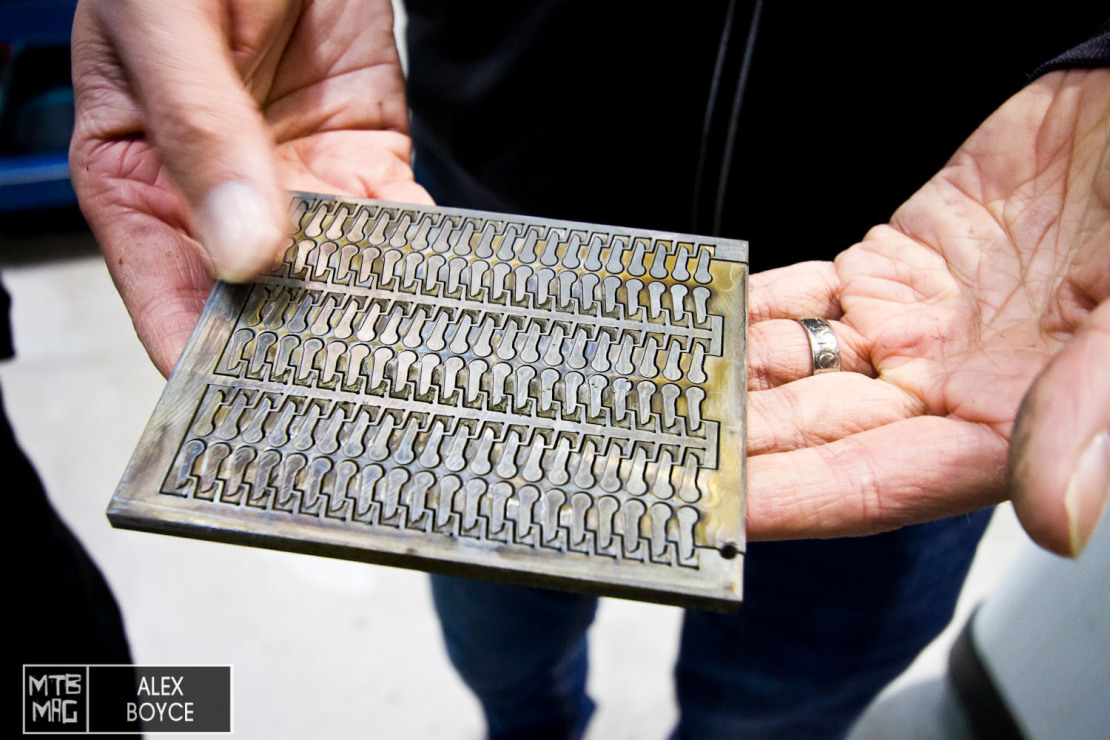
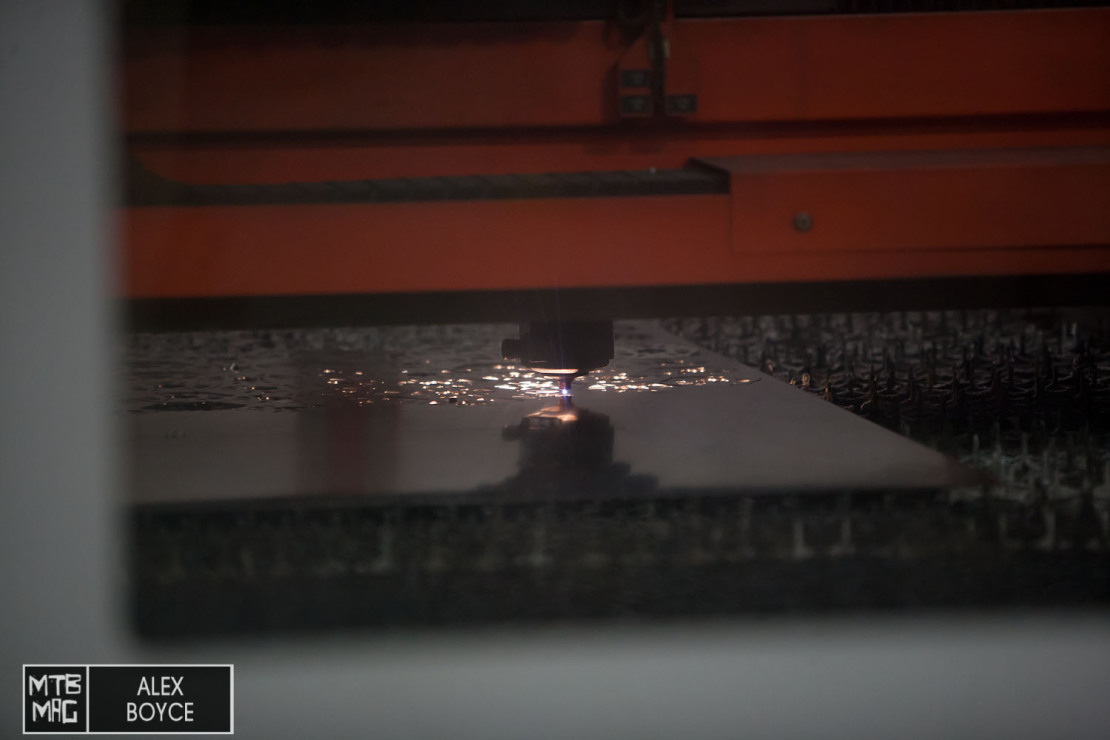
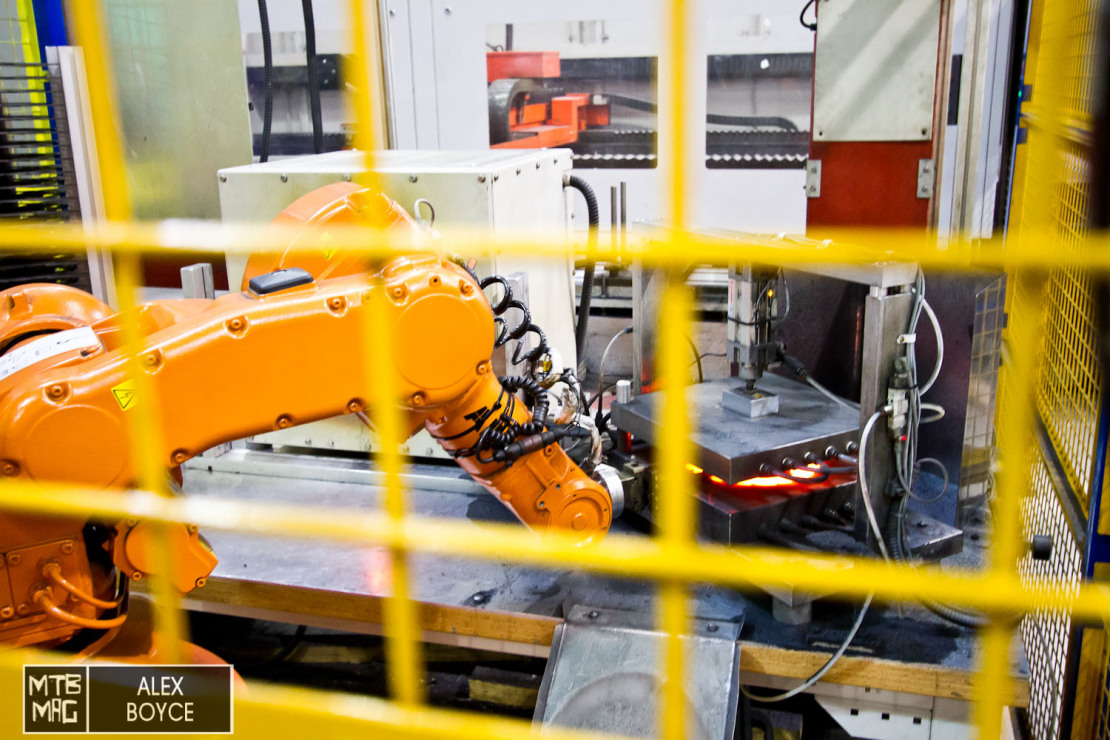
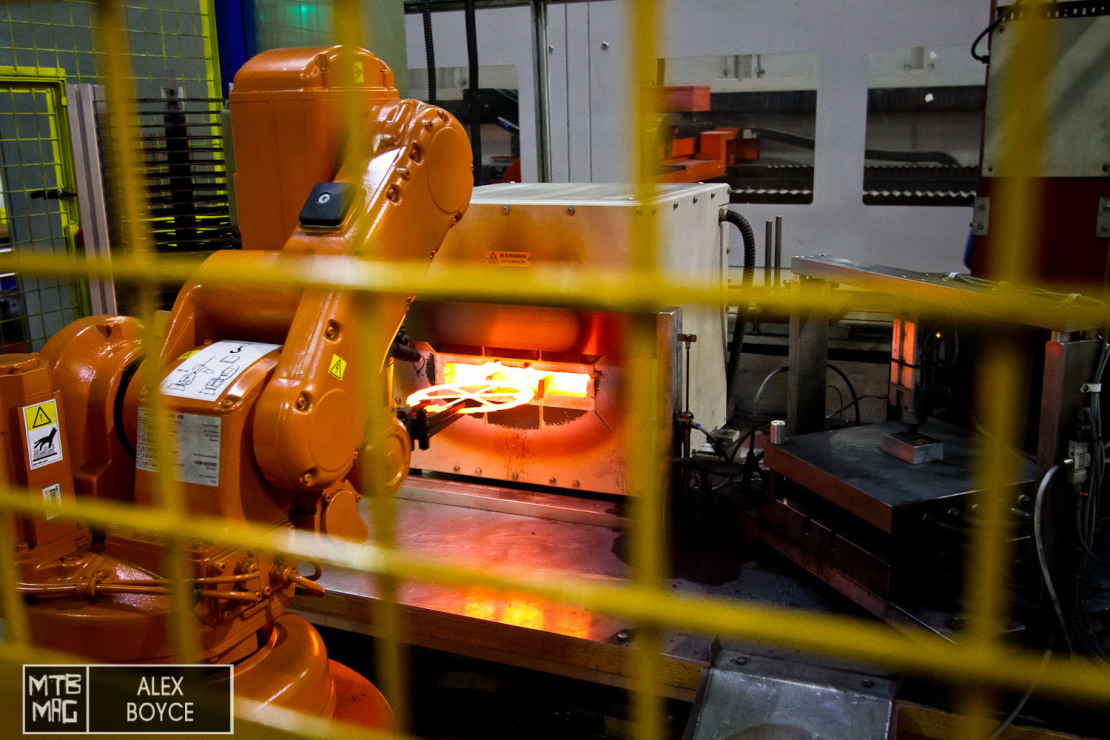
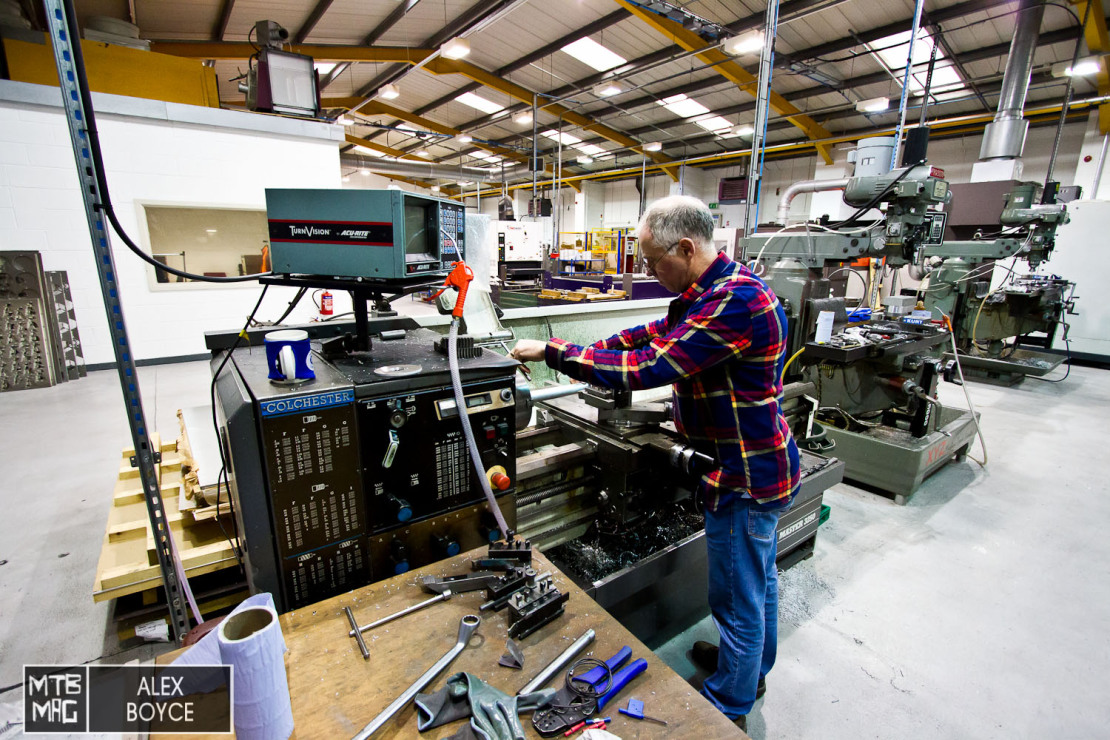
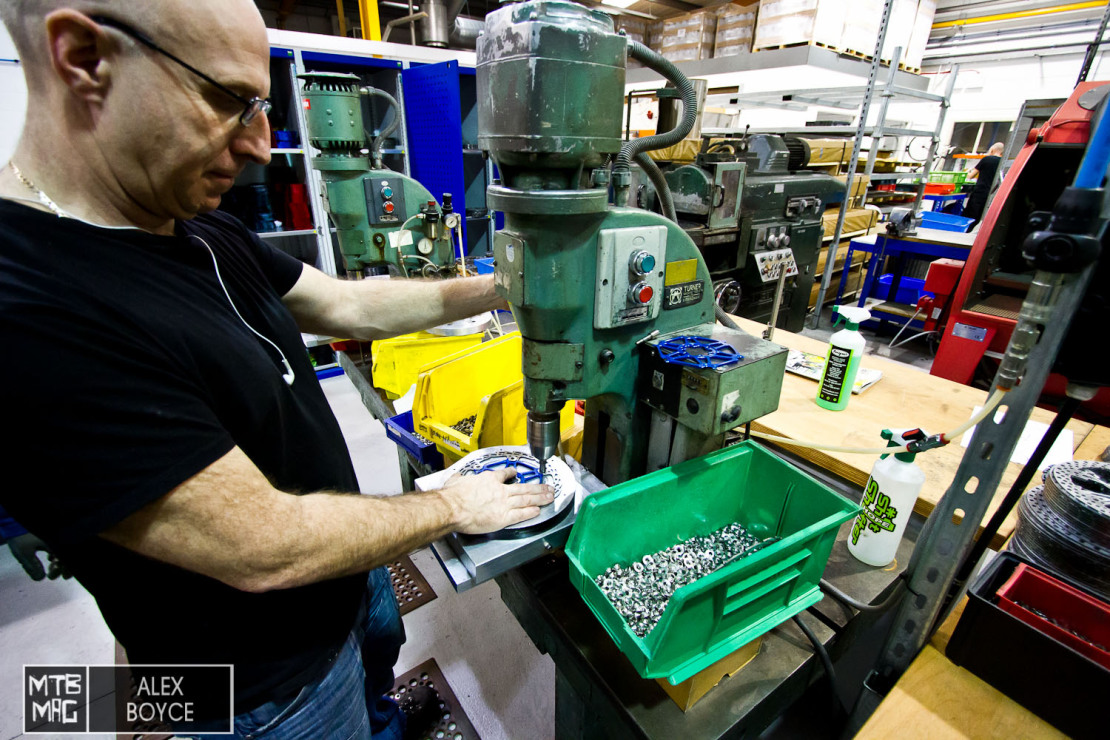
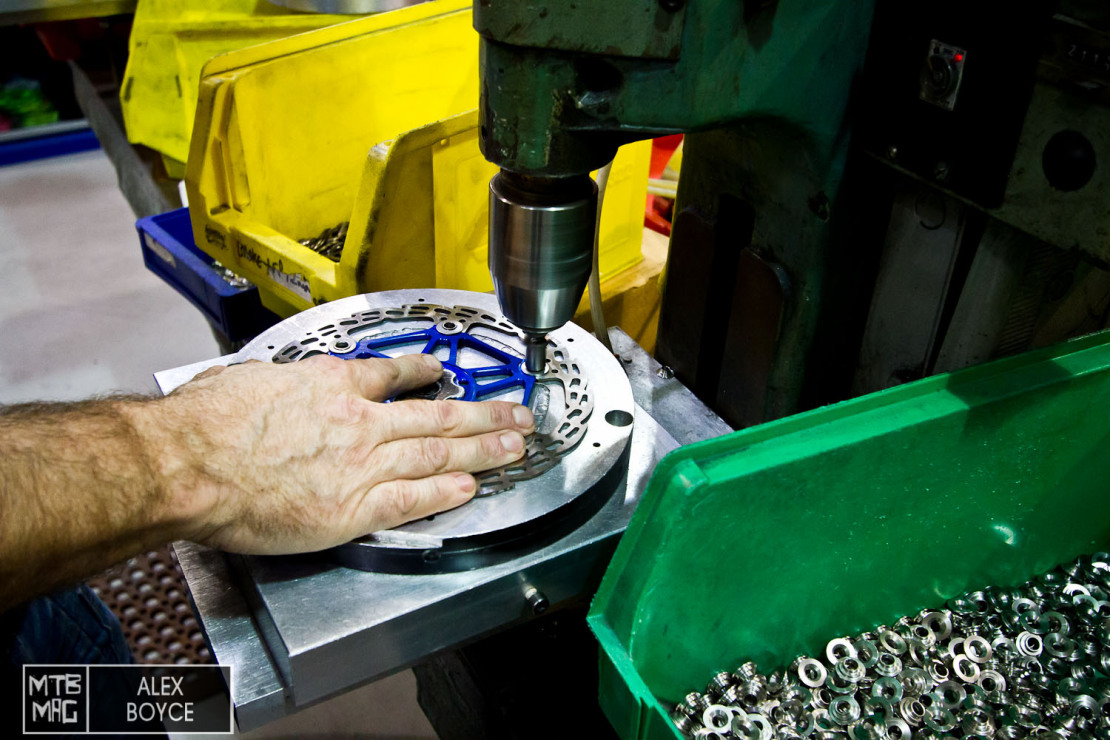
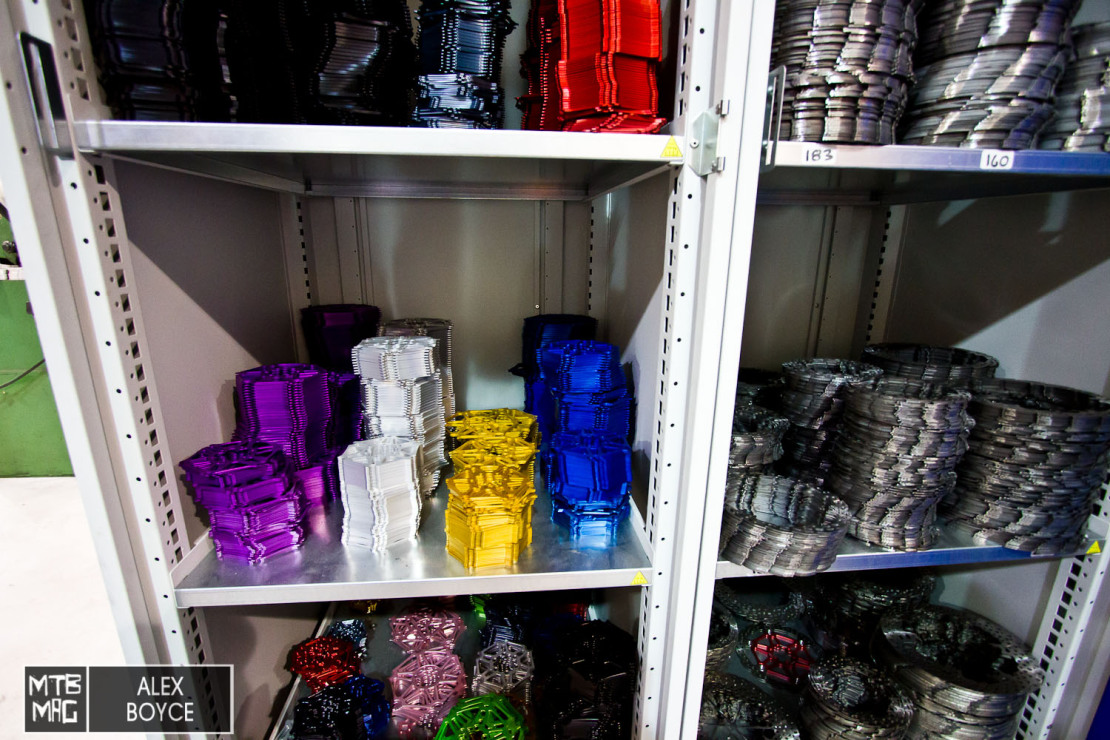
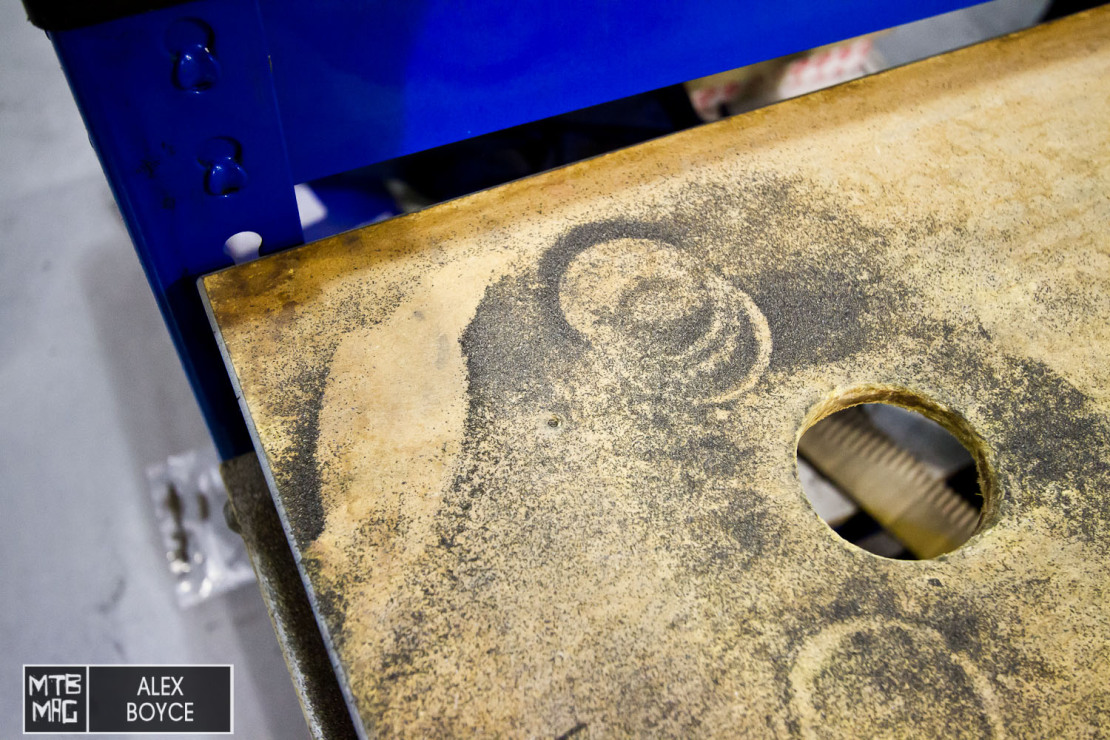
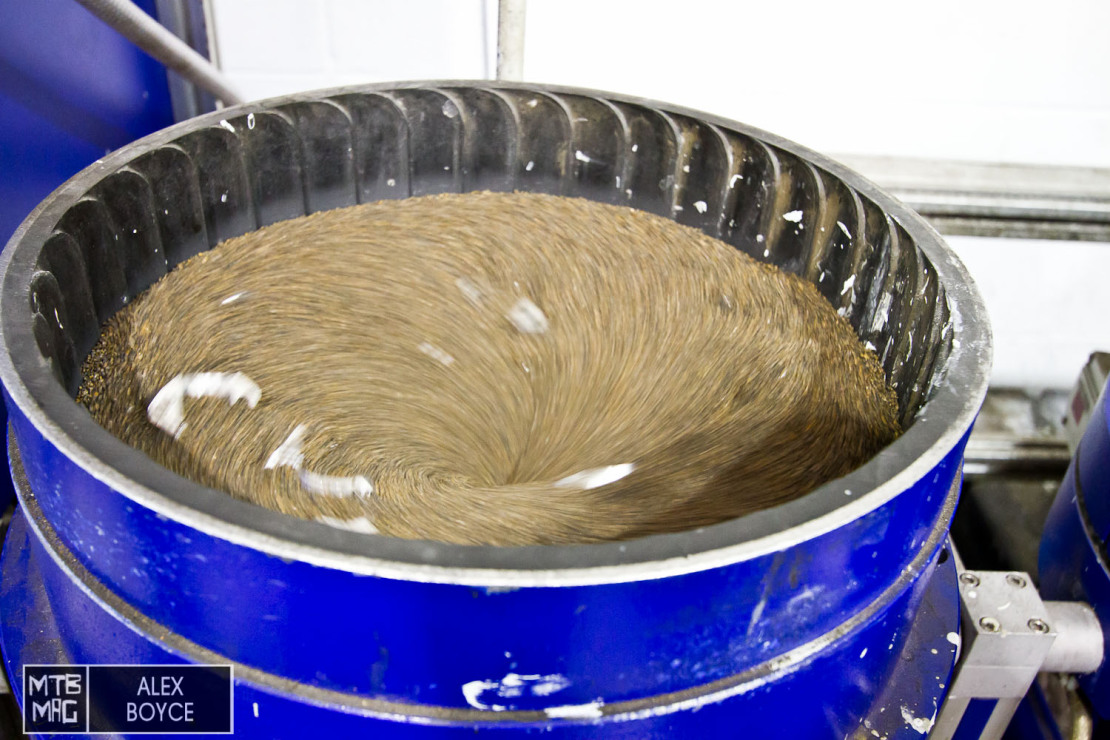
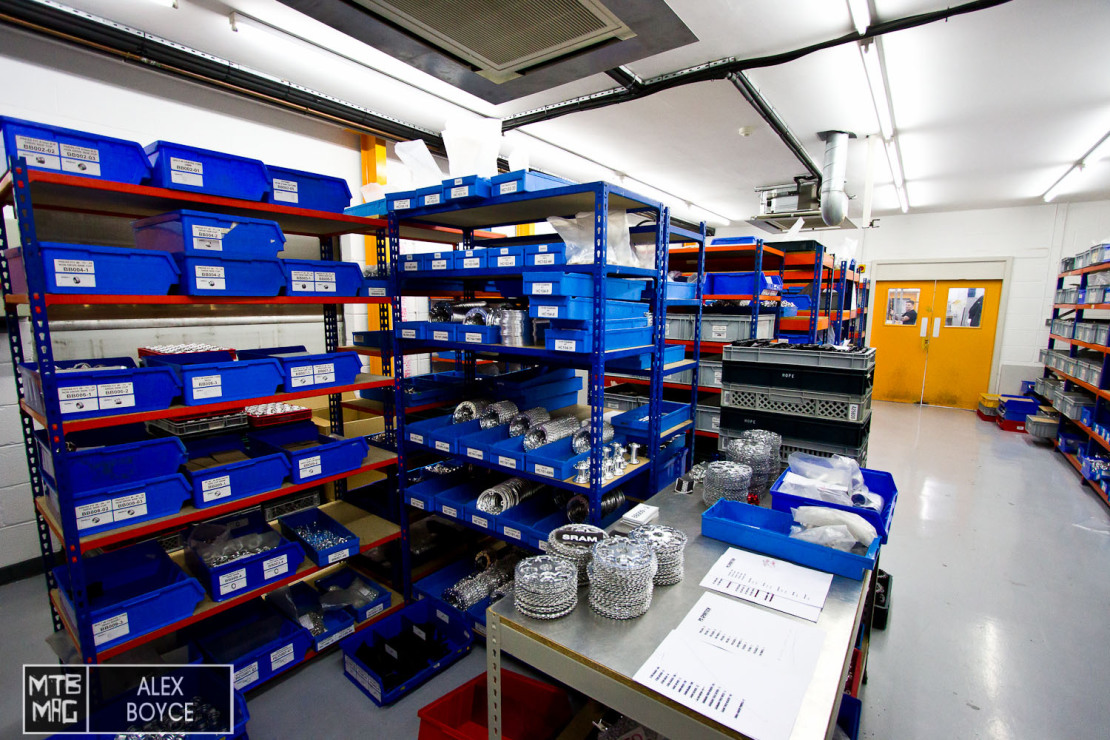
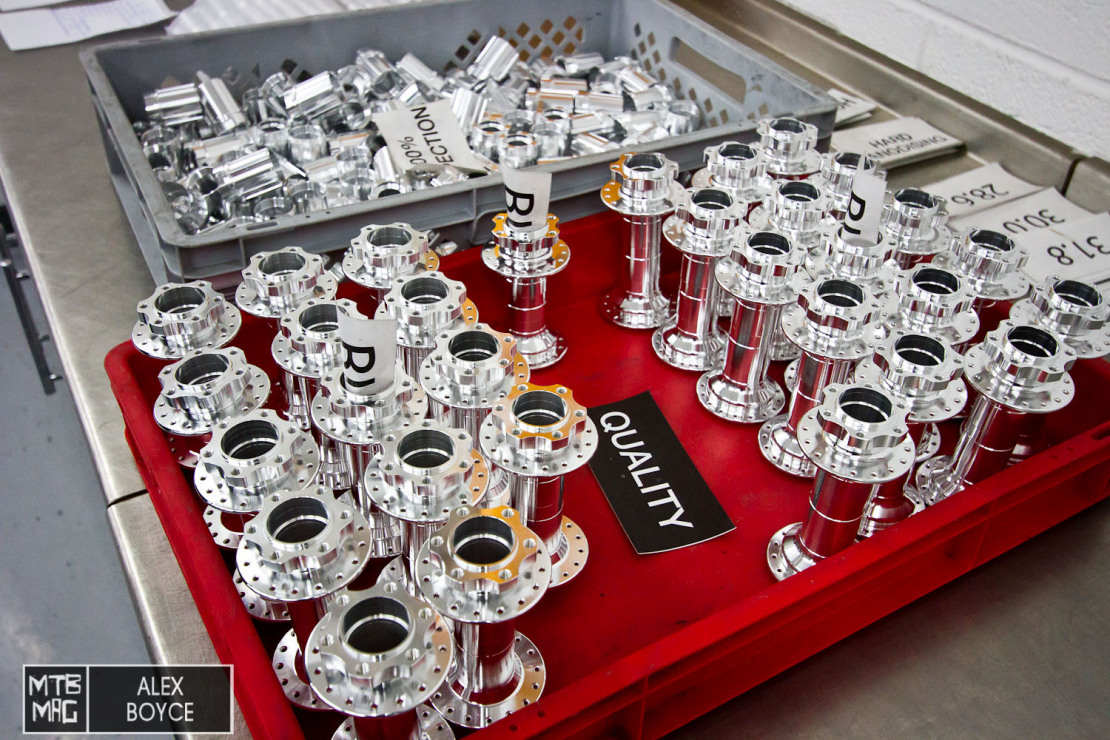
TIl processo di anodizzazione
Hope colora in casa i componenti e fa da 2.000 a 80.000 parti alla settimana.
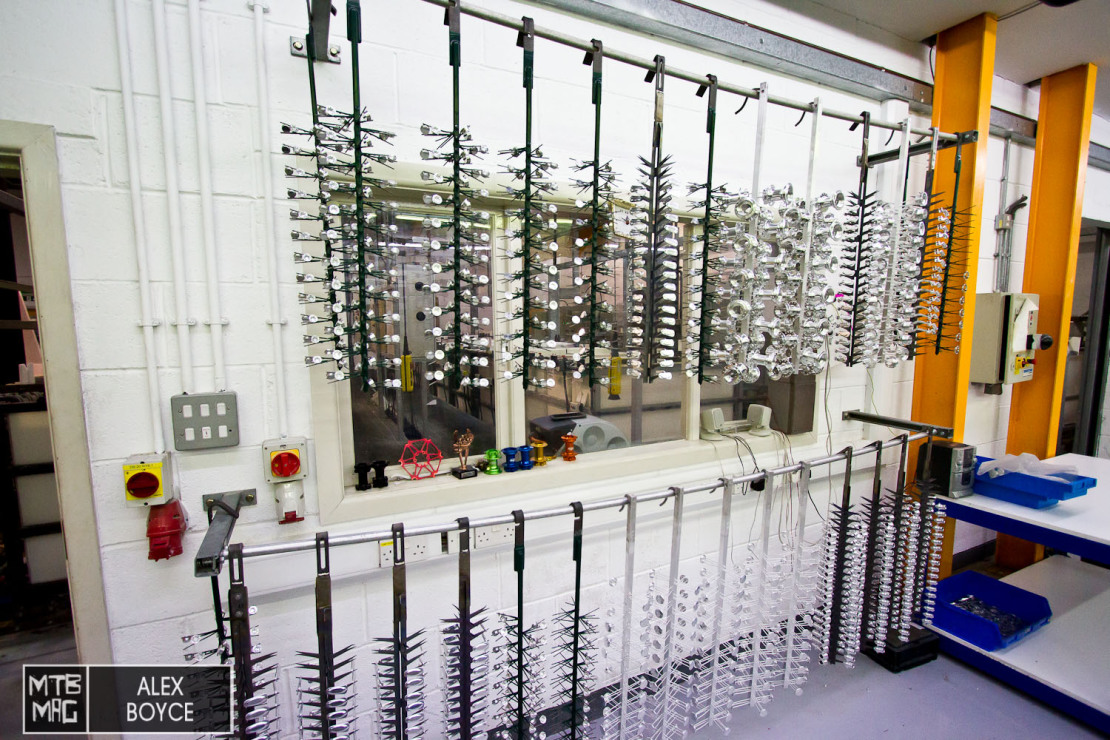
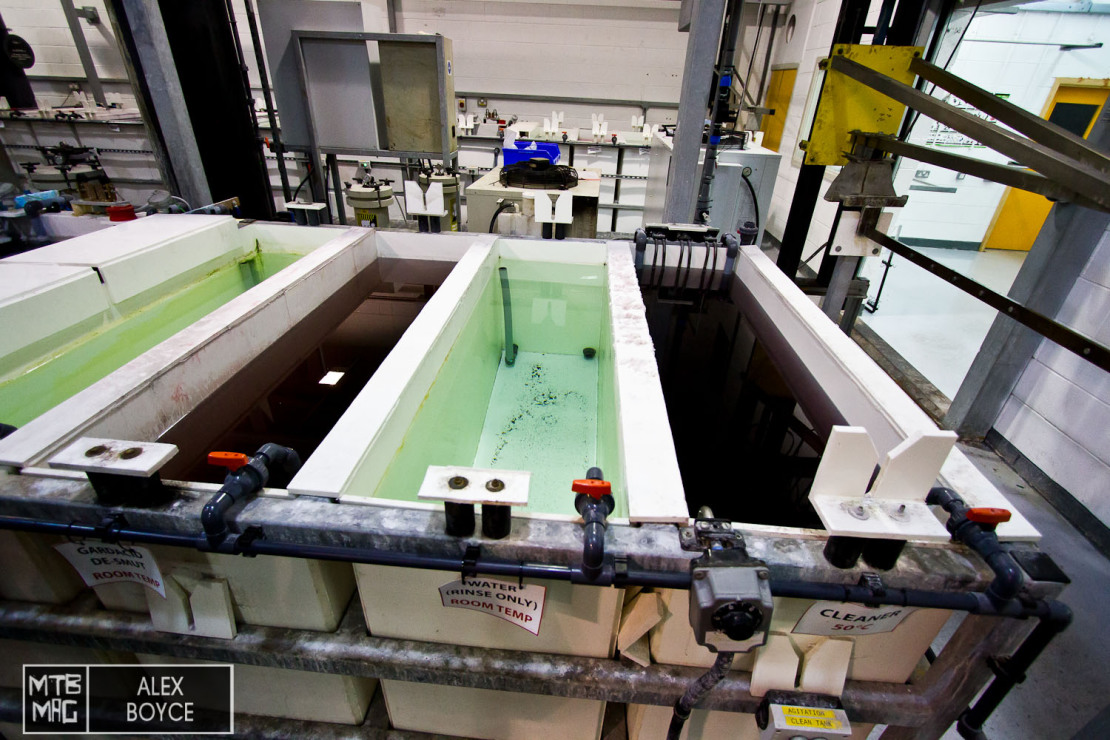
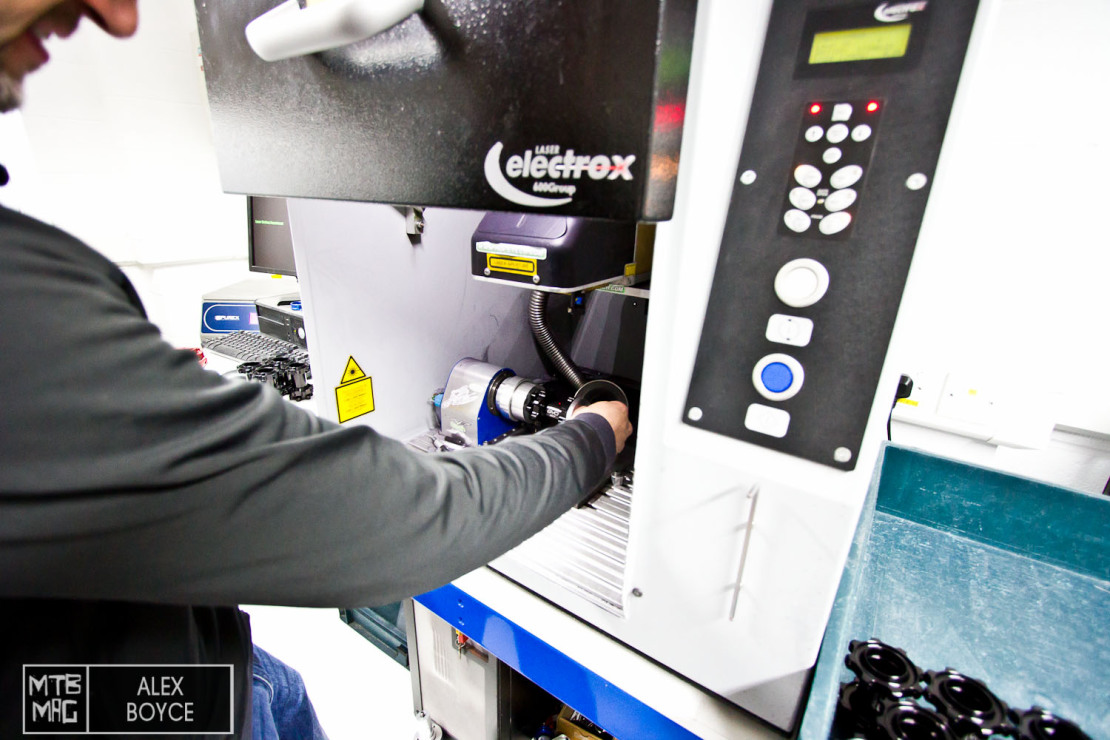
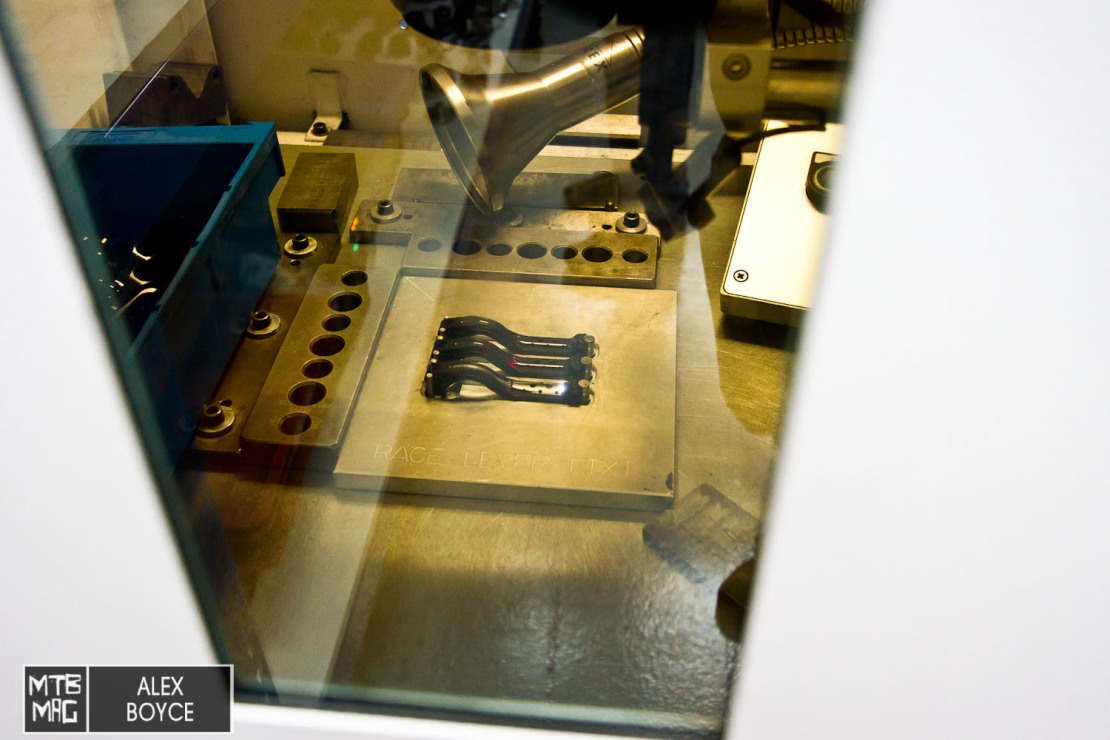
Componenti ed assemblaggio
Le parti sono messe assieme nella zona dell’assemblaggio finale, dove avviene anche un ultimo controllo qualità.
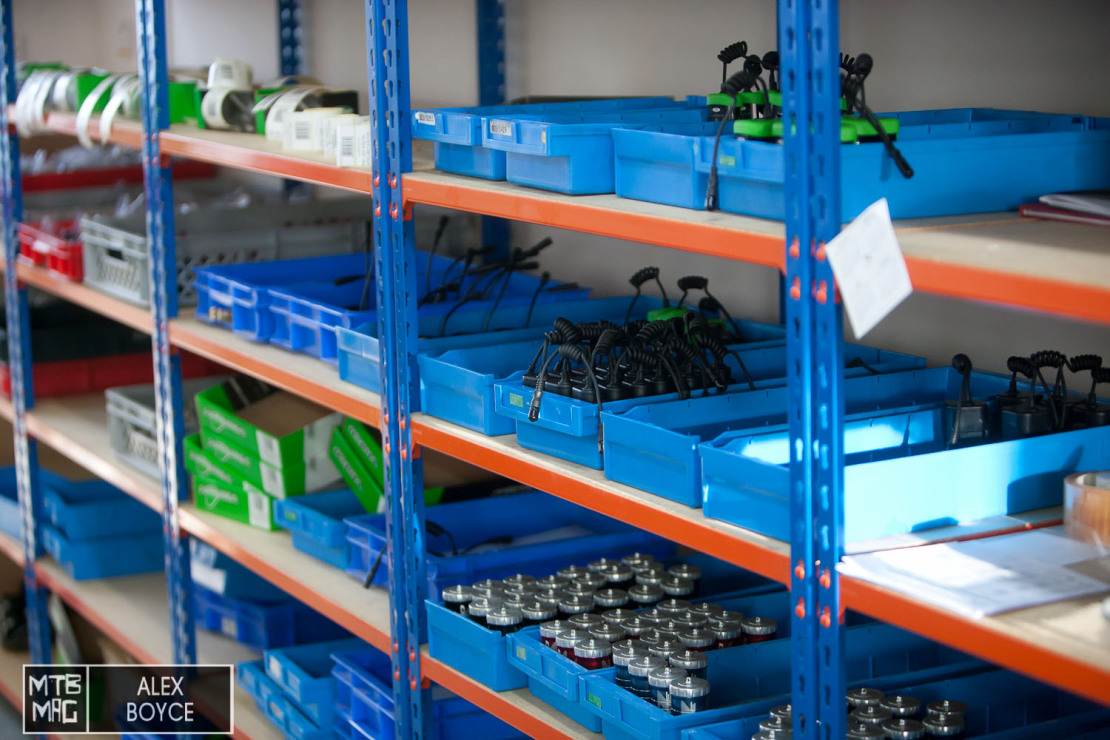
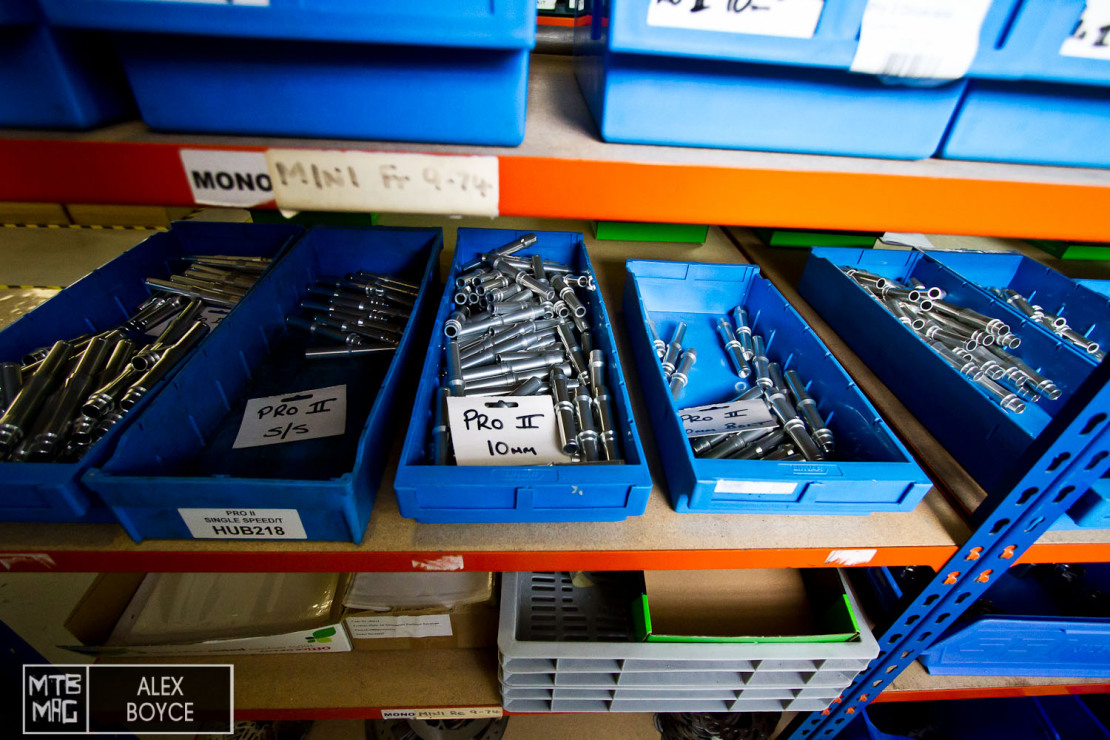
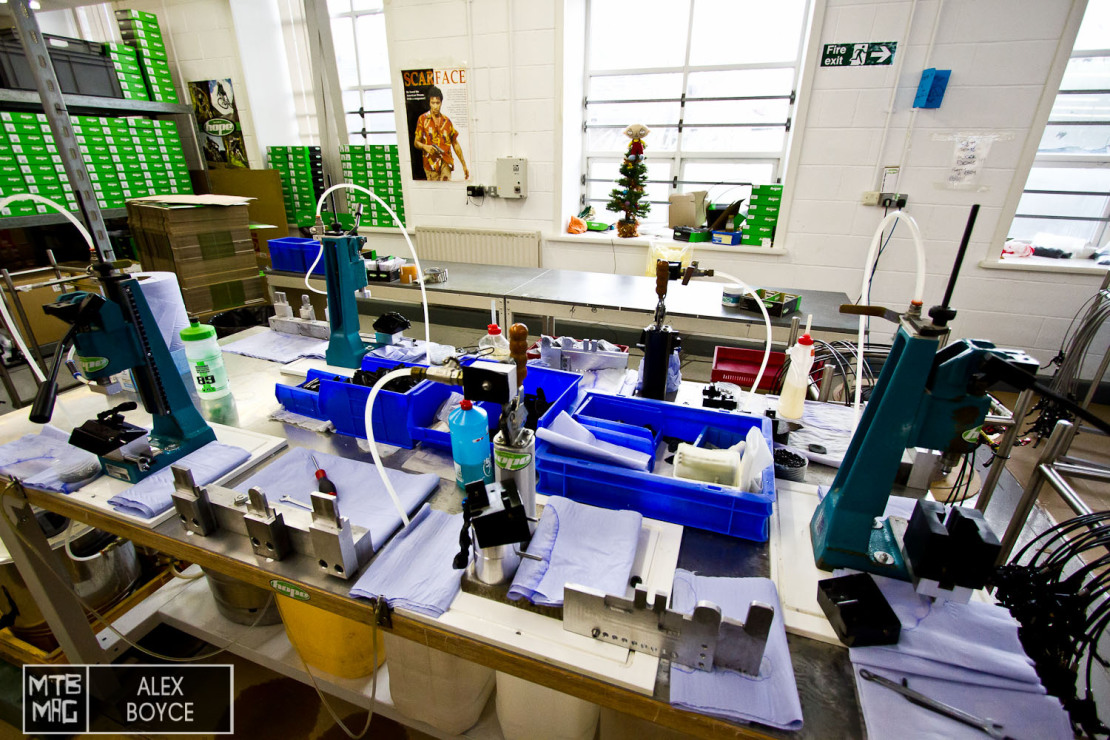
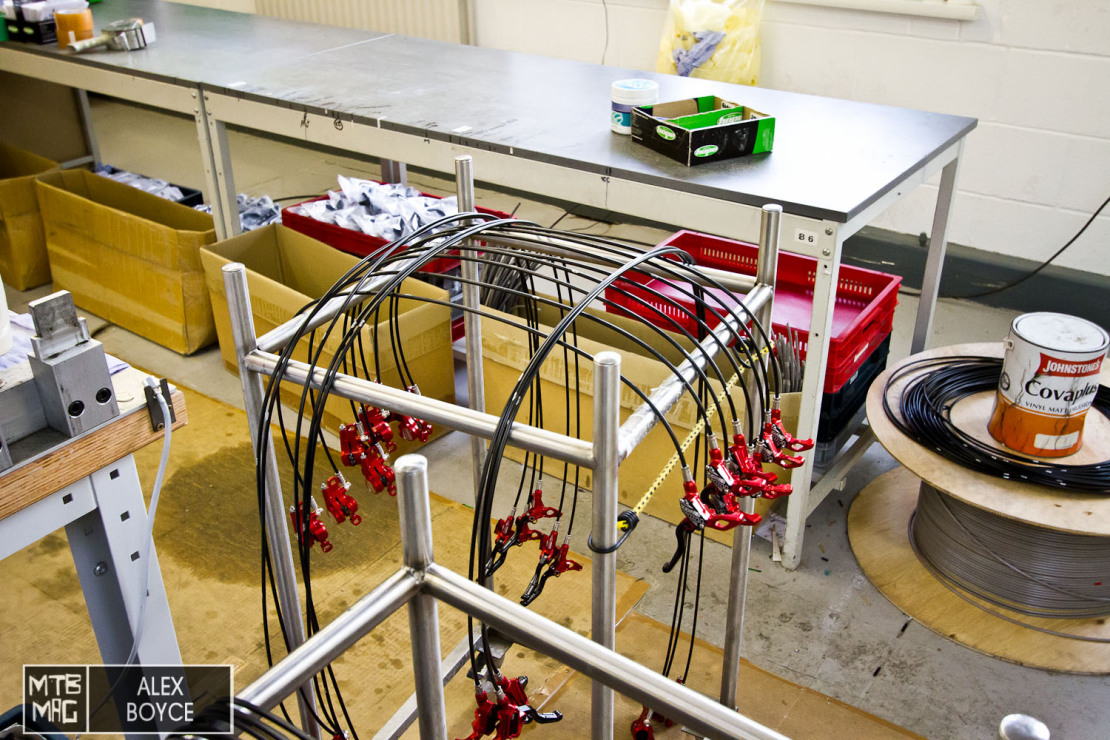
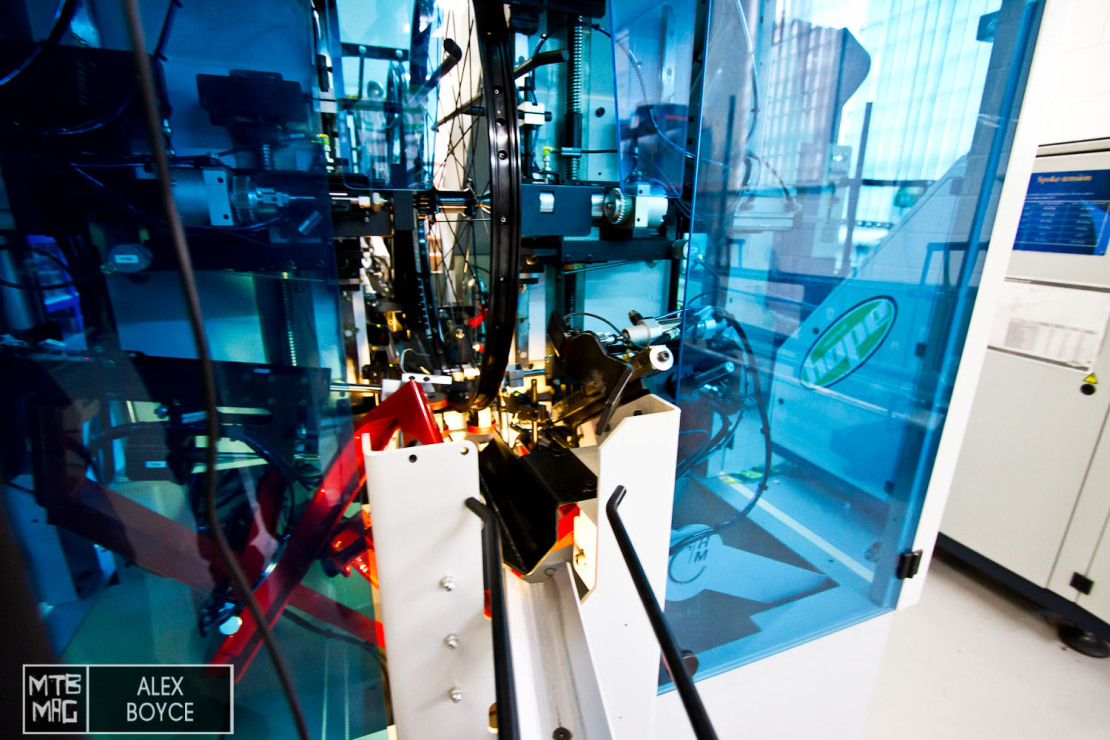
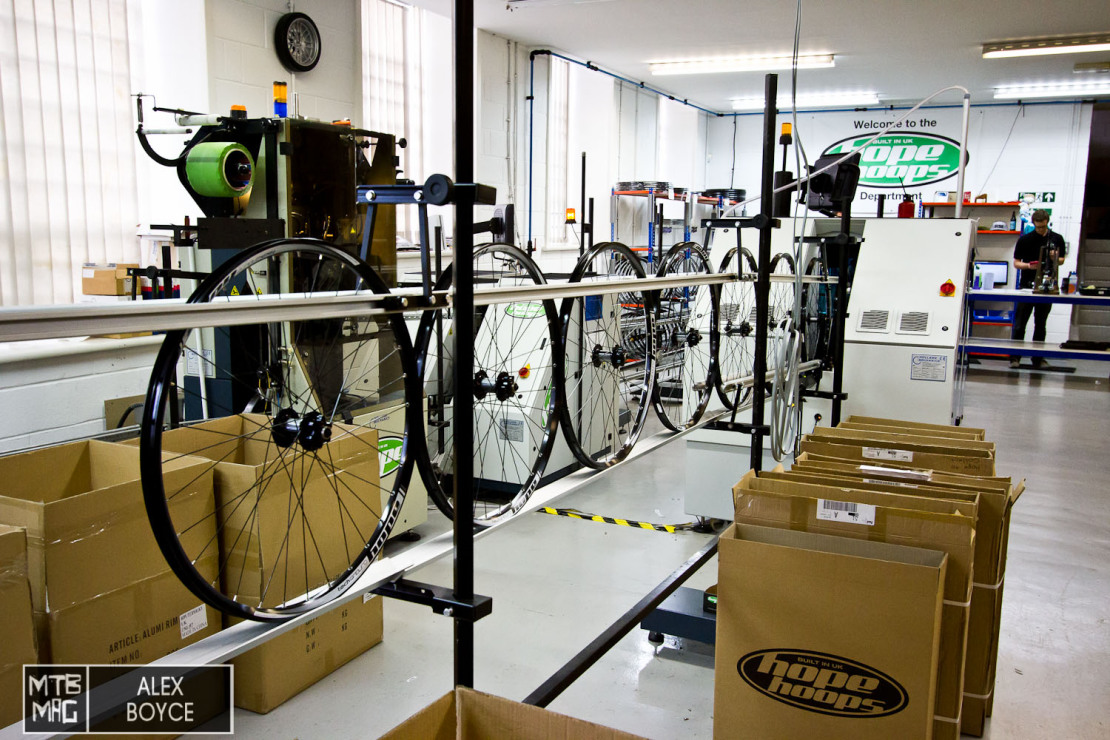
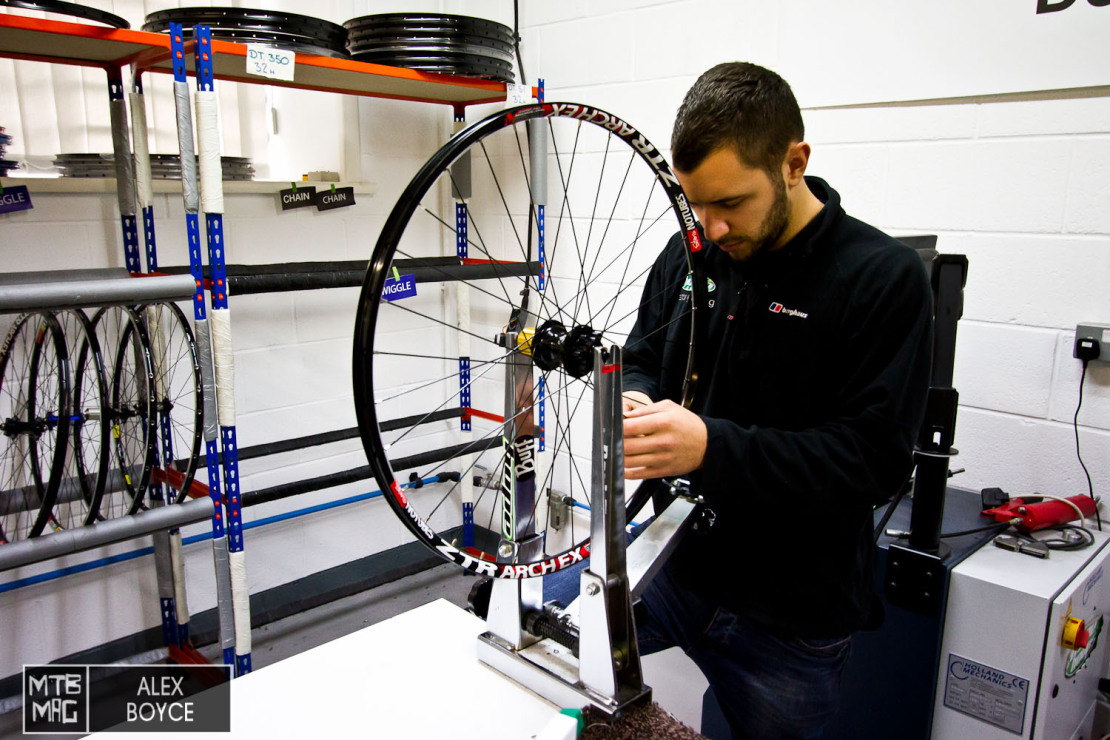
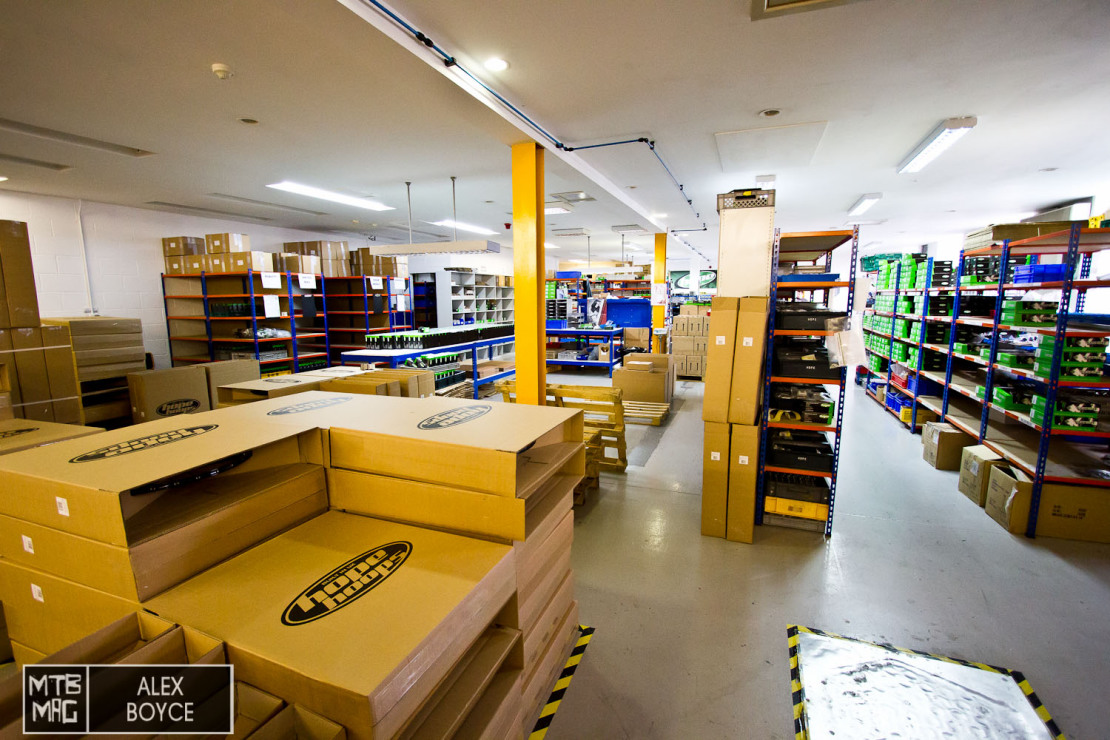
Altre curiosità
Un po’ di scatti vari in giro per la fabbrica
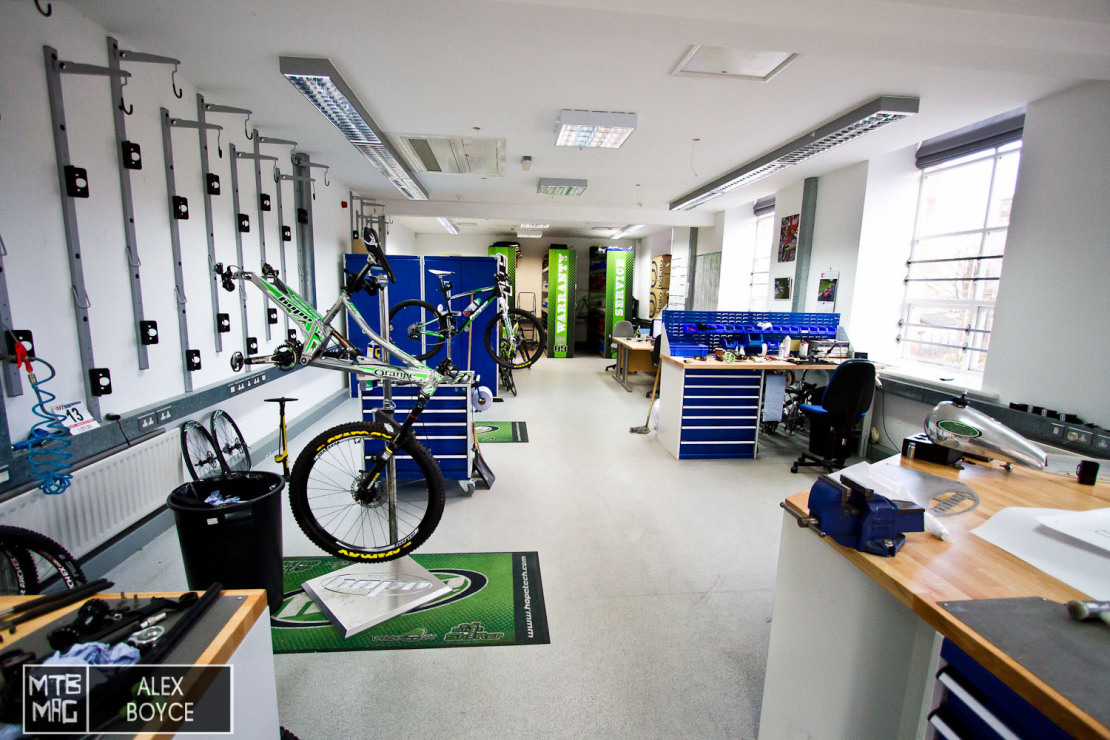
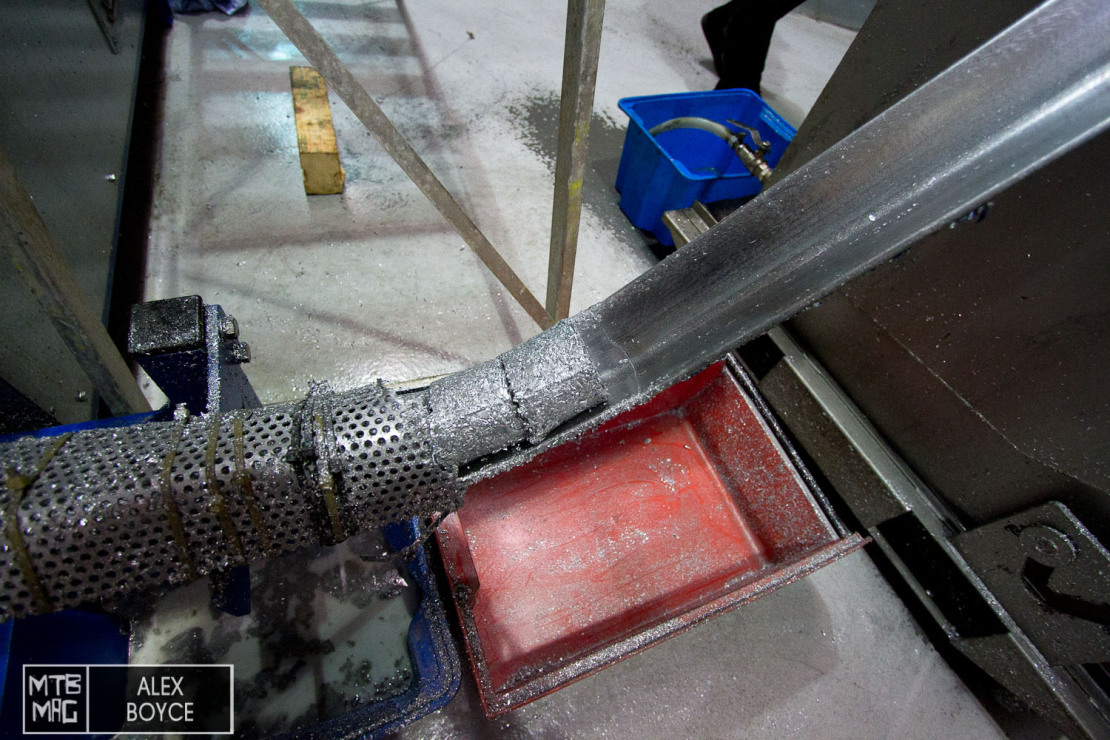
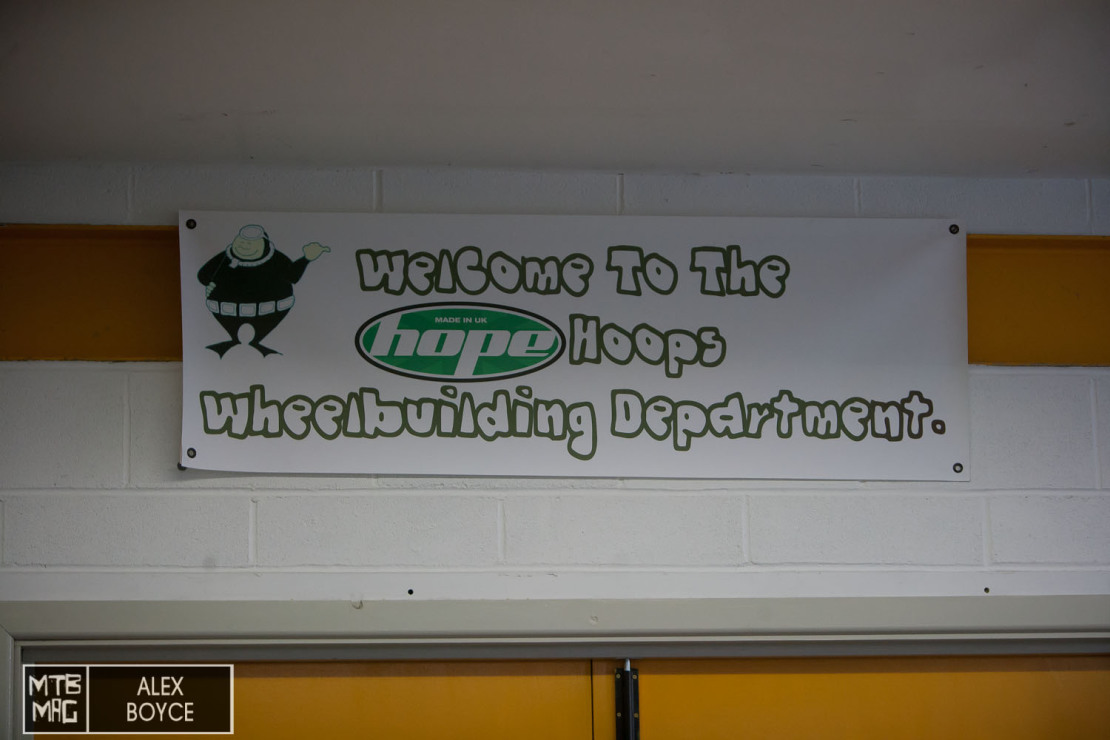
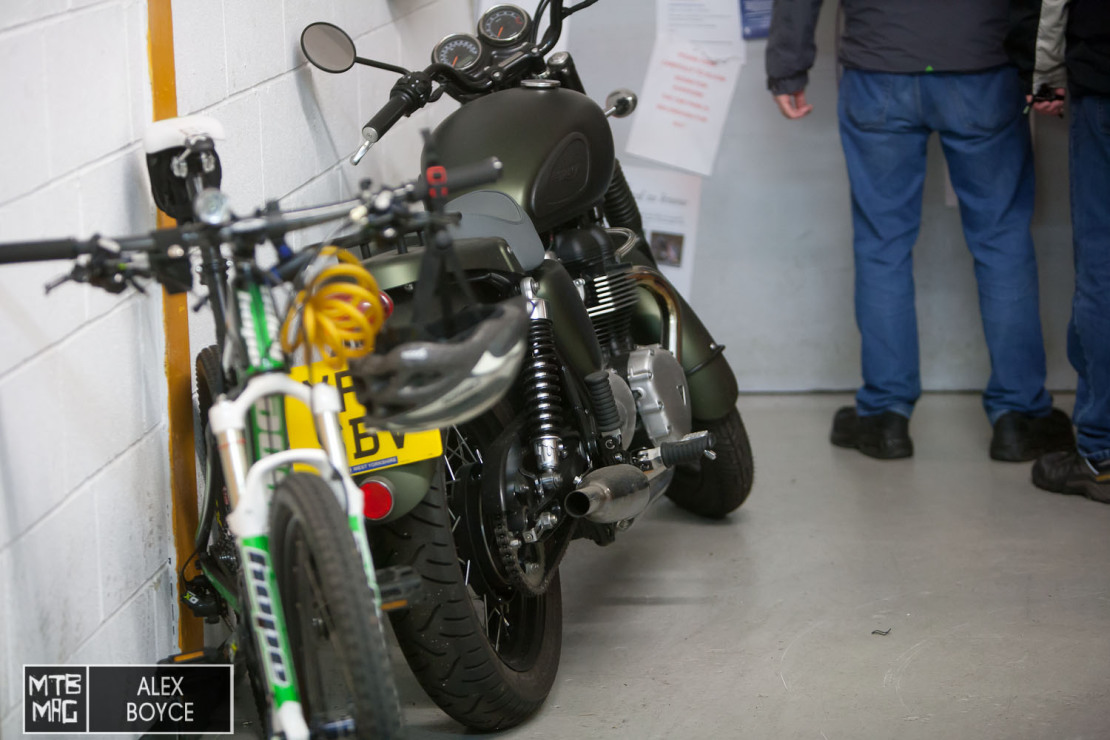
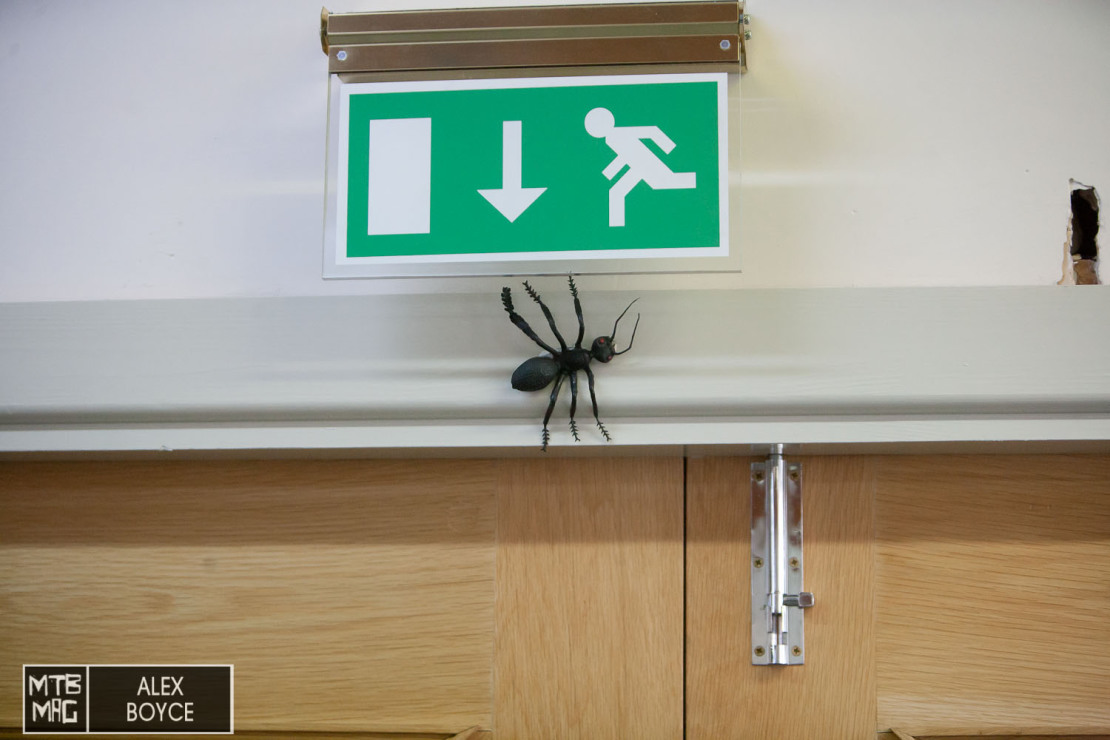
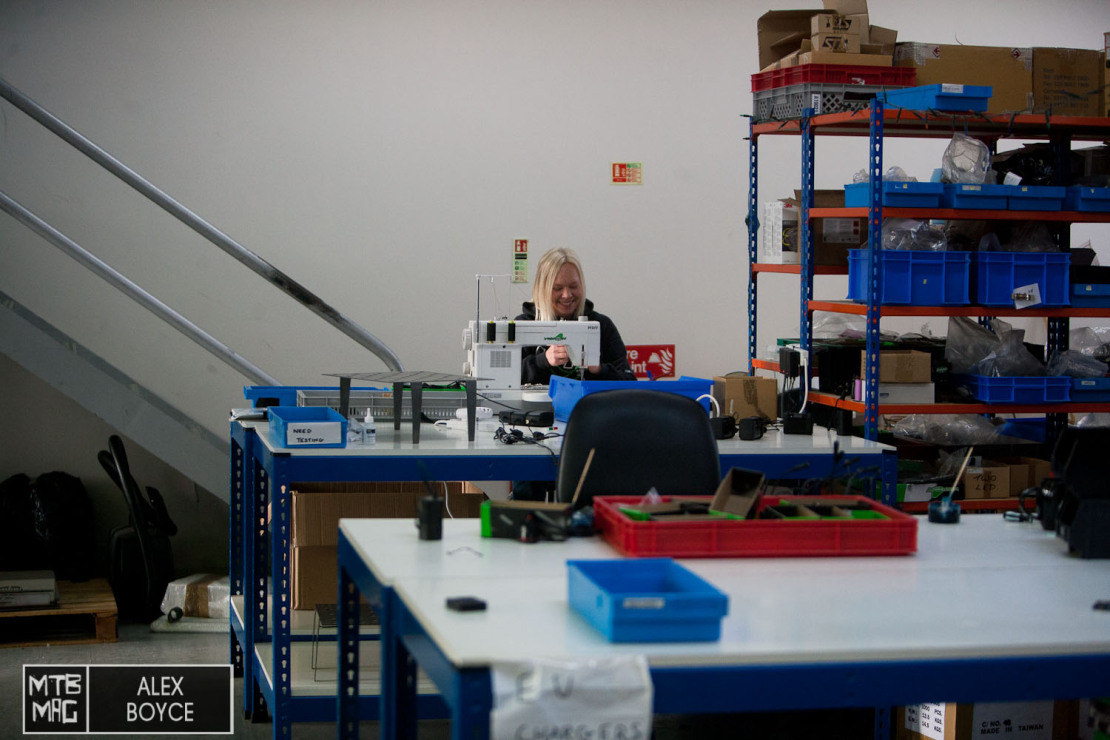

Hope è probabilmente uno dei migliori posti di tutta l’industra ciclistica dove lavorare. Ci sono divertimento, lavoro serio ed innovazione, il tutto in un bell’ambiente. Inoltre la produzione è fatta in casa, tenuta sotto controllo e con continuo sviluppo e nuovi investimenti, compreso lo sviluppo di un nuovo pumptrack in aggiunta a quello che c’è già. Hope sta anche lavorando ad un velodromo, che cominceranno presto a costruire, quindi torneremo presto per un’altra visita!